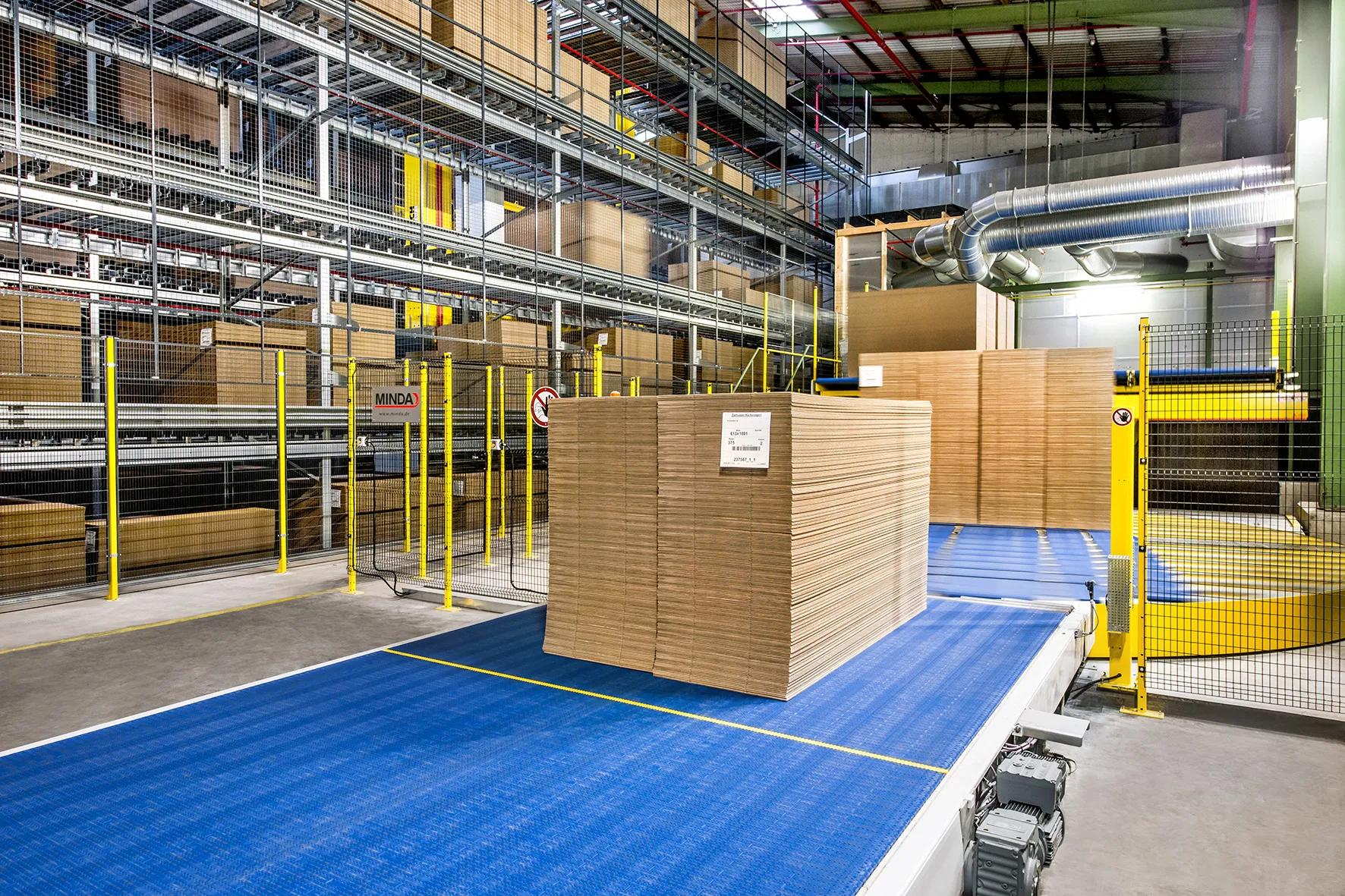
Highly flexible warehouse concept with finished goods and format goods high-bay warehouse at Zerhusen
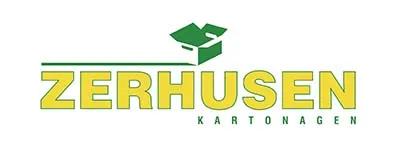
Zerhusen Kartonagen GmbH specializes in the production of corrugated board packaging as well as customer-specific special packaging. At the Damme site, approximately 440 employees process around 200 million square meters of corrugated board per year, which are manufactured from 100,000 tons of paper on the company's own corrugator. Folding boxes, erecting boxes, blanks or multi-component packaging are produced. The strong growth in production at Zerhusen made it necessary to increase storage capacity. HÖRMANN Logistik developed a highly flexible logistics concept and, as general contractor, implemented the three-aisle high-bay warehouse (HRL 1), its extension and expansion (HRL 2), a two-aisle format goods warehouse, and in each case the connecting conveyor technology.
Concept
All components at Zerhusen are based on the HÖRMANN logistics warehouse concept, which was specially developed for the specific properties of corrugated board. This is tailor-made for the low weight and high volume of corrugated board. The relatively low weight allows the simultaneous transport of several load units during storage and retrieval. With one storage or retrieval cycle of a storage and retrieval machine (SRM), up to three identical pallets can be stored or retrieved. The number of load units transported simultaneously depends on the size of the packages. For this purpose, each load unit is measured to the millimeter after the contour check at the end of production.
Innovative sorter concept
The largest packages are stored and retrieved individually, medium sizes as pairs and small load units as triples. An innovative sorter almost merges the same pallet types into pairs or triples to enable highly efficient use of the line capacity. The load units are buffered in several buffer lanes of the sorter until the pair or triple can be completed. At the storage spur of the high-bay warehouse, the load units are precisely aligned using a sophisticated technique and then transferred to the SRMs. These control the storage compartment with pinpoint accuracy by means of compartment fine positioning. Depending on their size, the pallets are stored 1 to 3 deep. All SRMs operate with the HiLIS Eco power management system, which saves up to 25% of energy consumption through intelligent energy balancing.
Highlights
Construction and extension of three-aisle high-bay warehouse HRL 1 for the storage of finished goods
- First construction phase of three-aisle high-bay warehouse: 125 m x 30 m x 38 m (L x W x H)
- 15,435 pallet spaces
- High-bay warehouse after extension: 155 m x 30 m x 38 m (L x W x H)
- 20,600 pallet spaces
- 3 stacker cranes in single-mast design with telescopic forks and chain conveyors
- Pallet storage 1 to 3 deep
- Single, pair or triple pallet transportation
- Flexible load unit size up to 3.1 x 1.7 x 1.95 m (L x W x H)
- Direct connection to production and shipping
- Expansion without interfering with day-to-day operations
Doubling of the three-aisle high-bay warehouse for the storage of finished goods HRL 2
The new high-bay warehouse 2 is connected to the north of the existing three-aisle high-bay warehouse 1 and is linked to production in terms of conveyor technology. A second distribution car enables the increased material flow in the direction of dispatch. The WMS HiLIS was also reconfigured.
- Three-aisle high-bay warehouse: 155 x 31 x 38 m (L x W x H)
- 22,000 pallet spaces
- 3 stacker cranes in single-mast design with telescopic forks and chain conveyors
- Pallet storage 1 to 3 deep
- Single, pair or triple pallet transport
- Gentle handling
- Flexible load unit size as in HRL 1
- Direct connection to production and shipping
Two-aisle format goods warehouse - transport and storage without bottom pallet
The two-aisle format warehouse was built in an existing hall to temporarily store format stacks with a wide range of dimensions until they are needed in processing. The stacks are transported and stored without load securing and without a bottom pallet.
- Two-aisle format warehouse: 59.5 x 18 x 10.8 m (L x W x H)
- Up to 752 stacking locations
- 2 two-mast stacker cranes with 11-tine telescopic forks
- 1 - 4 stacks per compartment, single-deep
- Maximum stacking weight: 3,000 kg
- Flexible handling of various dimensions, max. 3.73 x 2.62 x 1.85 m (L x W x H)
- Just-in-time supply of processing
"I was particularly impressed by the short start-up phase of the new HRL. After less than 6 weeks, the system was already running at full load in 3-shift operation. The assumed calculated storage and retrieval values were even exceeded. Detailed planning and a trouble-free construction phase were decisive for this. I am happy that we decided in favor of HÖRMANN Logistik."
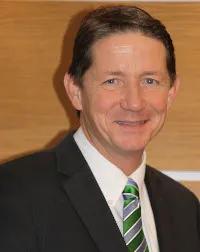
Roland Zerhusen
Managing Director
Zerhusen Kartonagen GmbH
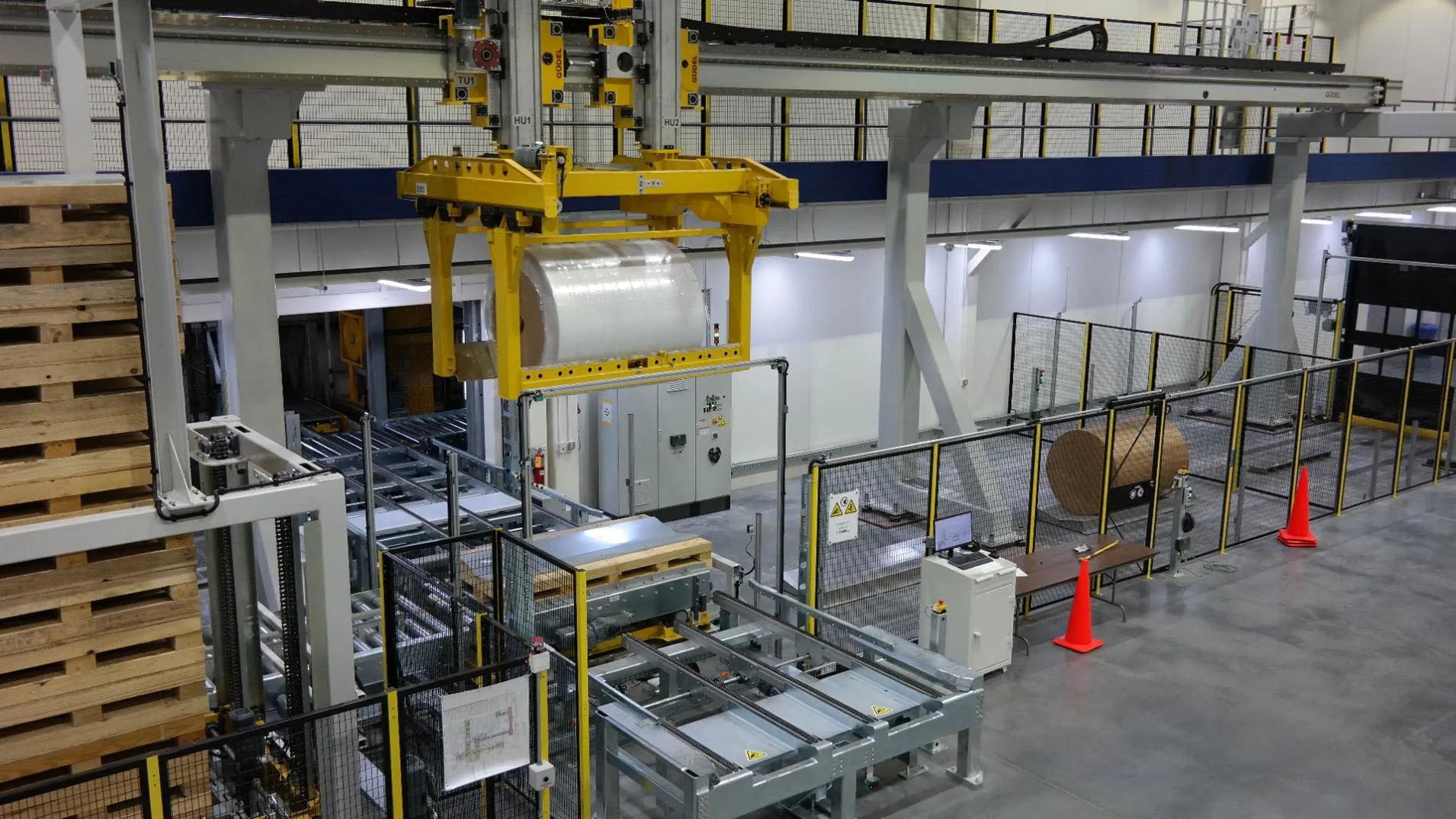
Referencje Green Bay
Magazyn wysokiego składowania rolek papieru w Green Bay Packaging, USA
Green Bay Packaging Inc. specjalizuje się w niestandardowych opakowaniach tekturowych, kartonach składanych i etykietach samoprzylepnych. Dzięki filozofii tworzenia kreatywnych rozwiązań dostosowanych do wymagań klienta, firma z Green Bay Wisconsin jest dostawcą premium w USA. Ponad 3 000 pracowników pracuje w lokalizacjach w 15 stanach USA oraz w Meksyku. W ramach rozbudowy zakładu w Green Bay's Labelstock Division w Wisconsin powstał nowy magazyn wysokiego składowania dla rolek papieru i towarów wysyłanych na paletach. Jest on bezpośrednio połączony z istniejącymi liniami powlekania i cięcia, jak również z nowo utworzonymi obszarami produkcyjnymi za pomocą automatycznych pojazdów kierowanych (AGV). HÖRMANN Logistik zrealizował jako generalny wykonawca nowy, imponujący magazyn wysokiego składowania wraz z łączącymi go przenośnikami i techniką przeładunkową oraz dwoma różnymi systemami AGV.
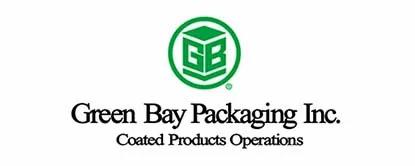
Koncepcja
Szczególnym wyzwaniem w dwunawowym magazynie kanałowym był transport i obsługa różnorodnych jednostek ładunkowych o masie do 5 ton. Dzięki kilku innowacyjnym rozwiązaniom, takim jak różne manipulatory rolkowe, urządzenia do opuszczania płyt podrzędnych, specjalne pojazdy AGV z odbiorem trzpieni i wagony do dystrybucji krzyżowej z technologią Powercap, firma HÖRMANN Logistik spełniła wszystkie wymagania projektu. Dotyczy to również w pełni elastycznych strategii składowania i pobierania z trzema układnicami. W każdym kanale magazynowym mogą być składowane zarówno rolki papieru, jak i różne rodzaje palet z wyrobami gotowymi. W tym kontekście jeden korytarz magazynu wysokiego składowania (HRL) jest wyposażony w dwie maszyny do składowania i pobierania (SRM) na jednym torze, a jeden korytarz w jedną SRM.
Kasety układające wyposażone są każda w dwa wózki kanałowe, które mogą wysuwać się pojedynczo (dla mniejszych palet) lub razem (dla palet systemowych dla ciężkich rolek). Środkowa jednostka regałowa może być obsługiwana z obu korytarzy, co zapewnia redundantne dostawy rolek na produkcję. Regały mają 2 głębokości, 4 głębokości lub 6 głębokości, aby elastycznie reagować na różne ilości artykułów. Szerokości
Kanały magazynowe mają szerokość od 1.000 mm do 2.200 mm dla lepszego wykorzystania przestrzeni. Wszystkie maszyny do magazynowania i pobierania są wyposażone w samouczące się precyzyjne pozycjonowanie przedziałów, co pozwala na zbliżenie się do kanałów z milimetrową precyzją.
W odbiorze towarów, rolki surowca są umieszczane na palecie systemowej za pomocą bramy liniowej. W procesie tym rolka jest mierzona, dopasowywana do zgłoszonych danych, transportowana do HRL i przechowywana. Gdy produkcja potrzebuje surowca, żąda wyboru rolek poprzez system logistyki wewnętrznej HiLIS firmy HÖRMANN, z którego HiLIS wybiera tę, która jest najłatwiej i najszybciej dostępna dla SRM. W ten sposób można uniknąć przesunięć magazynowych. Po pobraniu przez SRM rolki wskazanej przez HiLIS, jest ona przenoszona do innego portalu za pomocą technologii przenośników.
To usuwa ją z palety systemowej i ustawia rolkę dla Automatycznego Pojazdu Prowadzącego (AGV). AGV transportuje rolkę bezpośrednio na łyżkę odwijarki w produkcji. Droga powrotna gotowych rolek powlekanych do magazynu odbywa się w odwrotnej kolejności. System HiLIS WMS zarządza i kontroluje wszystkie procesy przepływu materiałów i komunikuje się poprzez interfejs z Green Bay HOST. Wizualizacja HiLIS zapewnia stałą przejrzystość i szybką diagnozę błędów w przypadku awarii.
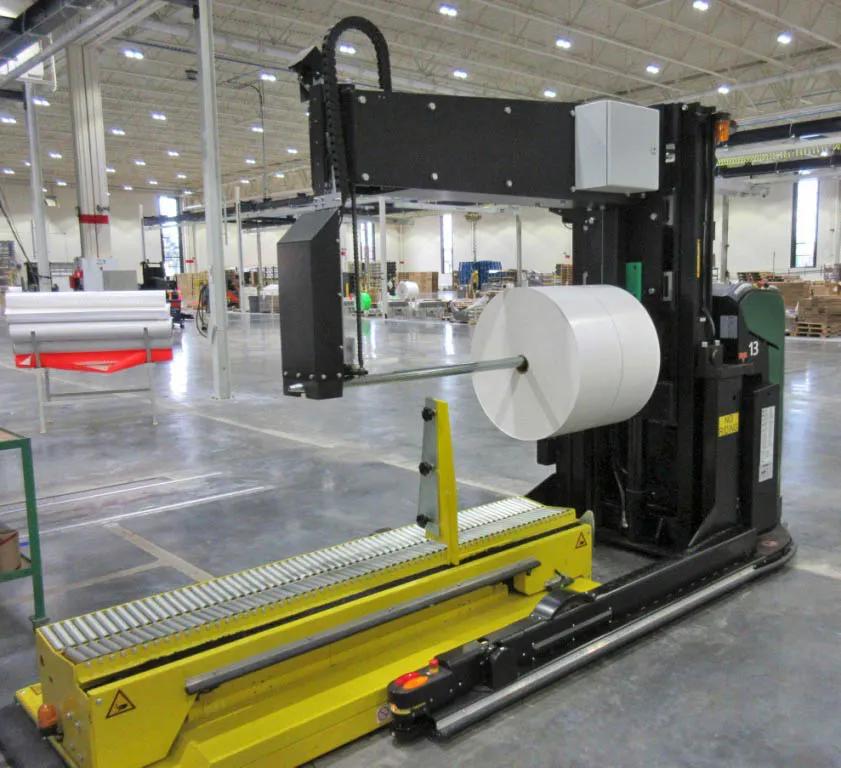
Elastyczne interfejsy i innowacyjne techniki
System zarządzania magazynem HiLIS nie tylko koordynuje ruchy materiałów pomiędzy magazynem a produkcją. Specjalny interfejs pomiędzy HiLIS, AGV, maszynami produkcyjnymi i technologią przenośników umożliwia przenoszenie rolek i innych danych produkcyjnych równolegle z transportem fizycznym.
Ponieważ urządzenie przeładunkowe wymagane do automatycznego transportu nie było dostępne na rynku, firma HÖRMANN Logistik we współpracy z producentem opracowała specjalne rozwiązanie. Ten innowacyjny AGV z trzpieniem jest w stanie odebrać zestaw pociętych rolek o szerokości 1.400 mm i wadze 2 ton bezpośrednio z przewijarki do cięcia wzdłużnego i dostarczyć je w pełni automatycznie do wielu różnych punktów odbioru w opakowaniu. W ten sposób cięcie i pakowanie są oddzielone pod względem czasu bez wielokrotnej obsługi.
Podczas łączenia obszaru pakowania z magazynem, transport na poziomie podłogi przecina główną trasę komunikacyjną. Specjalnie zaprojektowane wózki dystrybucyjne są sterowane poprzez łącze danych WLAN i otrzymują energię elektryczną z PowerCaps (kondensatorów). Ponieważ PowerCaps potrzebują tylko kilku sekund na naładowanie, mogą być ładowane w momencie przekazania palety bez konieczności oczekiwania. Ponadto bloki kondensatorów są bezobsługowe i mają długą żywotność.
Highlights
- 2-nawowy magazyn wysokiego składowania w konstrukcji silosowej: 176 x 26 x 25 m (dł. x szer. x wys.)
- Magazyn o podwójnej głębokości do 6 głębokości
- Mieszane składowanie rolek papieru i wyrobów gotowych na paletach
- Pojemność magazynowa: 12 800 palet lub 6 370 rolek
- 3 automatyczne układnice (korytarzowe) z dwoma wózkami kanałowymi każda
- 3 automatyczne suwnice do obsługi rolek, po dwie w pełni redundantne
- 4 wózki AGV do poziomej obsługi rolek
- 3 wózki AGV ze specjalnym odbierakiem (trzpieniem) dla pociętych rolek klienta
- Wózek dystrybucyjny do przekraczania tras ruchu wózków widłowych z technologią Powercap
- HiLIS WMS
- Zaopatrzenie produkcji w systemie Just-in-time
W celu utrzymania się na rynku szukaliśmy możliwości zwiększenia prędkości i przepustowości, obsługi większych ciężarów rolek, maksymalizacji jakości i minimalizacji ilości odpadów. Firma HÖRMANN Logistik zapewniła nam wiedzę wewnętrzną oraz sieć kompetentnych dostawców, dzięki czemu mogliśmy zrealizować bardzo indywidualny i wydajny system.
Green Bay
Zespół projektowy
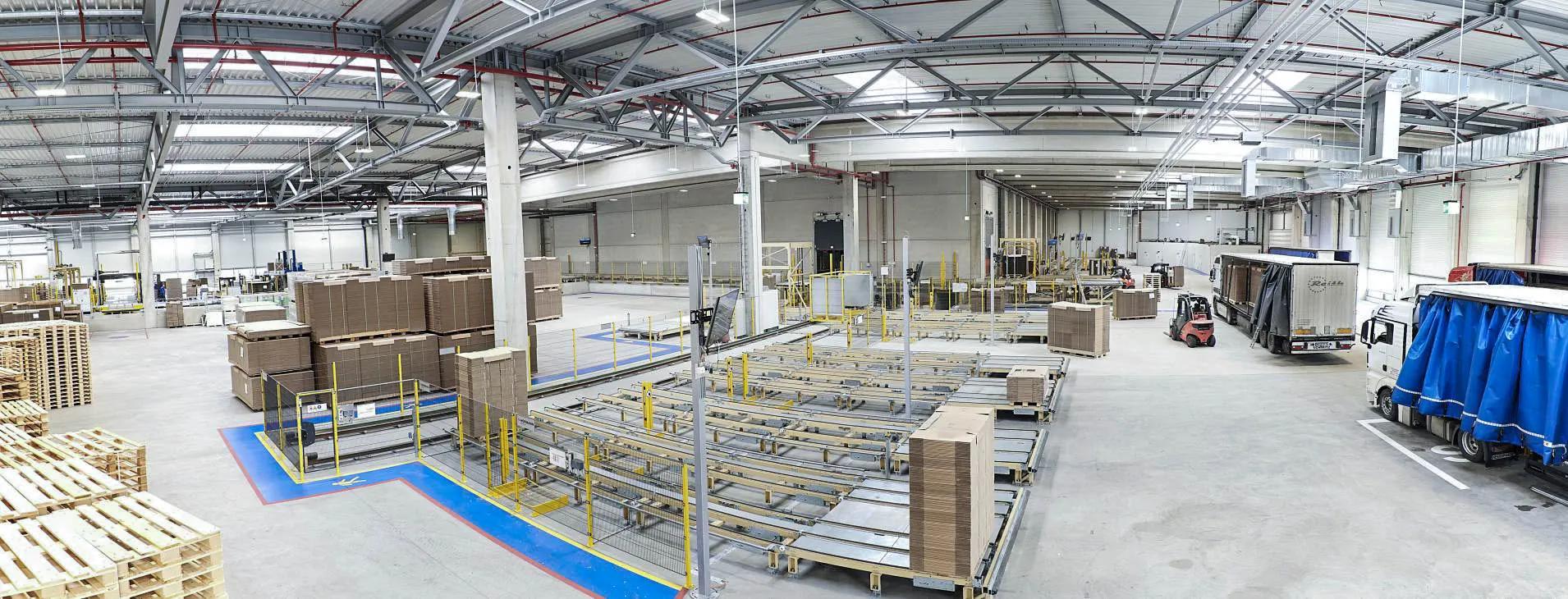
Odnośnik Kunert Tektura falista
Automatyczny magazyn kanałowy dla palet mało- i wielkoformatowych w Kunert Wellpappe
Kunert Wellpappe Bad Neustadt GmbH & Co.KG jest częścią rodzinnej grupy Kunert. Dziś Grupa Kunert zatrudnia 1900 osób w 16 zakładach w Europie i Azji. Rocznie Grupa Kunert produkuje 300.000 ton rdzeni tektury falistej, ochraniaczy krawędzi i opakowań, a także ponad 225.000 ton rdzeni tektury falistej. W zakładzie w Bad Neustadt wybudowano nowy zautomatyzowany magazyn wysokiego składowania, aby stworzyć przestrzeń dla rozszerzenia produkcji i sprostać zmieniającym się wymaganiom klientów w zakresie mniejszych ilości zamówień, krótszych cykli dostaw i efektywnego zarządzania zapasami. Dzięki innowacyjnej koncepcji firma HÖRMANN Logistik przejęła realizację nowego magazynu z techniką przenośników łączących. Cechą szczególną czteronawowego magazynu kanałowego jest wielokrotne składowanie krzyżowe różnorodnych formatów wyrobów gotowych na różnych typach palet, jak również na kilku subpaletach.
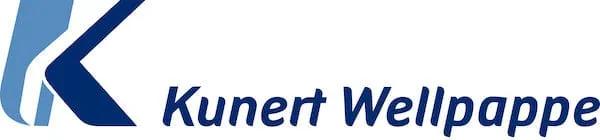
Koncepcja
Jednostki opakowaniowe są transportowane z produkcji za pomocą wózka dystrybucyjnego w celu przeniesienia na nowy system przenośników. Już na produkcji zwraca się uwagę na to, aby w miarę możliwości zawsze transportować dwie identyczne jednostki opakowaniowe jedna za drugą, które następnie mogą być przenoszone jako pary w obszarze magazynu wysokiego składowania i pobierania. To znacznie zwiększa przepustowość magazynu. Jednostka opakowaniowa może mieć do sześciu podpalet. Jednostki opakowaniowe są wyśrodkowane i sprawdzane pod względem długości, szerokości, wysokości, szerokości palety, długości palety i wagi za pomocą systemu kontroli konturów.
System przenośników przenosi następnie jednostki opakowaniowe do strefy wstępnej magazynu wysokiego składowania, gdzie obwód paletowy ze specjalnymi przenośnikami łańcuchowymi i rolkowymi stołami podnoszącymi łączy strefę produkcji, magazynu wysokiego składowania i przygotowania do wysyłki. W przypadku składowania w nowym magazynie kanałowym, jednostki opakowaniowe są precyzyjnie pozycjonowane na bocznicy magazynowej za pomocą siatki świetlnej. Dwumasztowe maszyny do składowania i pobierania (SRM) są wyposażone w przenośniki łańcuchowe i wózki kanałowe. W dwóch korytarzach magazynu SRM-y pracują z jednym wózkiem kanałowym każdy, natomiast w pozostałych dwóch korytarzach pracują z dwoma wózkami kanałowymi każdy, aby obsłużyć transport dużych palet.
Wózki kanałowe są zasilane bateriami i są ładowane na bieżąco w AS/RS. Układnica podnosi jednostkę opakowaniową w poprzek i składa ją na wielu głębokościach w kanałach magazynowych przy pomocy wózków kanałowych. Podczas pobierania towarów, system zarządzania i kontroli magazynu HiLIS otrzymuje zlecenie pobrania poprzez interfejs z lokalnego HOSTu. Towary są pobierane przez układnice i transportowane za pomocą przenośników do strefy wysyłki. Istnieją różne strefy załadunku dla tylnego i bocznego załadunku ciężarówek.
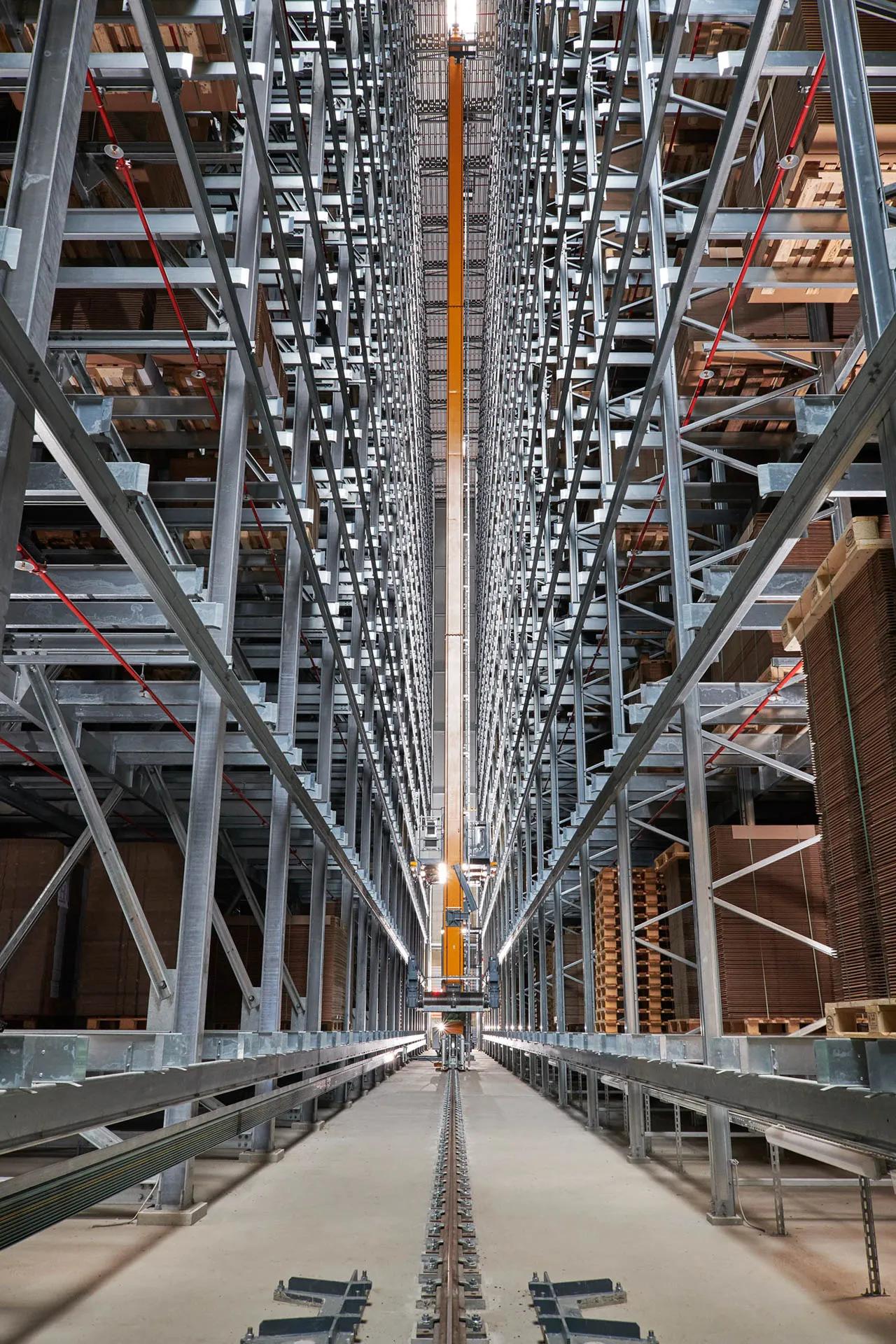
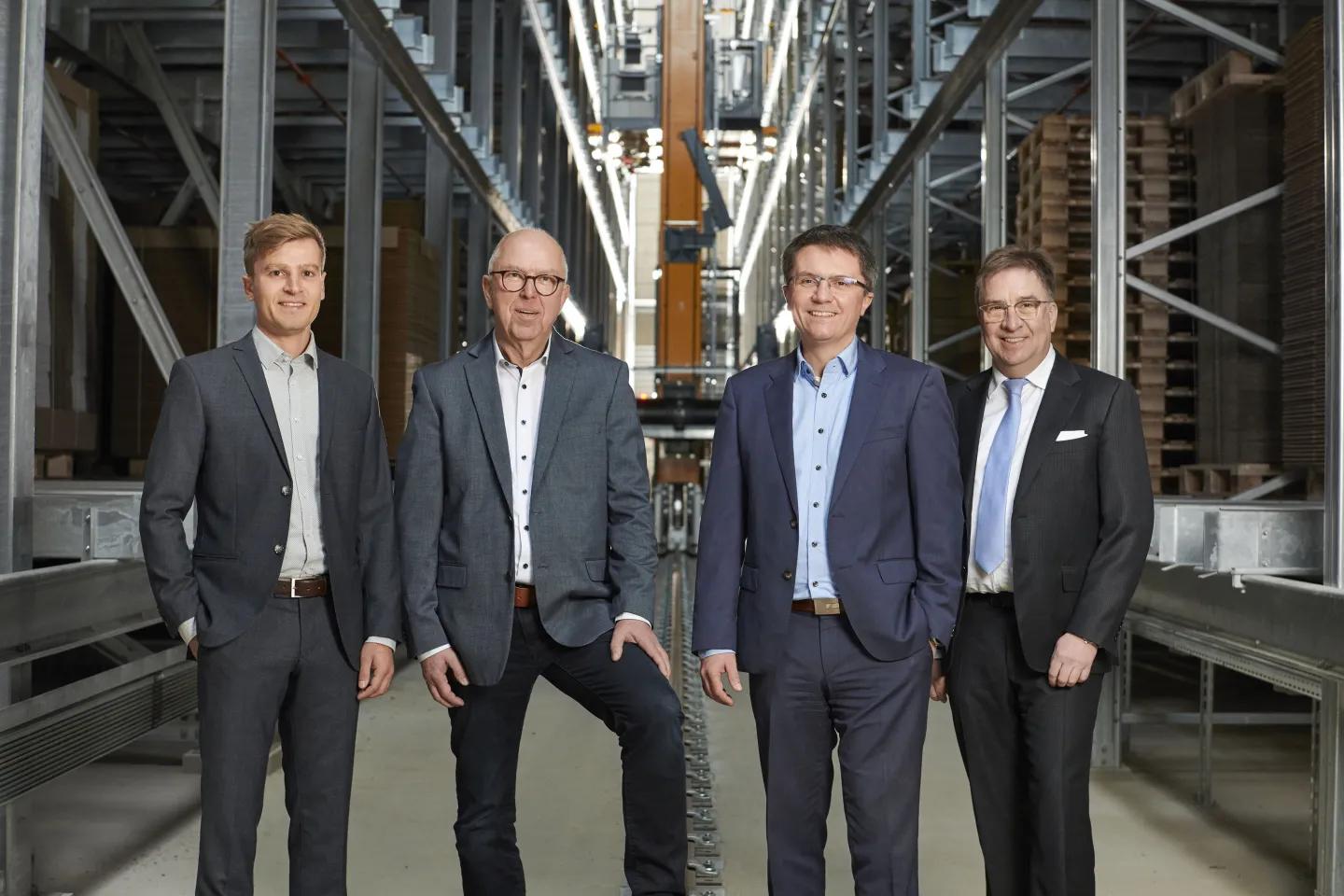
Wyszukane strategie przechowywania i transportu różnorodnych jednostek opakowaniowych
Highlights
- 4-nawowy magazyn wysokiego składowania w konstrukcji silosowej z możliwością wielokrotnego składowania
- Wymiary: 84 x 46 x 42 m (dł. x szer. x wys.)
- 19 000 miejsc paletowych
- 2 korytarze dla maksymalnych wymiarów ładunku 2.300 x 2.600 x 2.200 mm (dł. x szer. x wys.)
- 2 korytarze dla dużych formatów z maksymalnie 6 europaletami 3.000 x 2.600 x 2.200 mm (dł. x szer. x wys.)
- Wysoka dynamika dzięki sterowaniu krzywą przesuwu antykolizyjnego i pozycjonowaniu kamery
- Wydajność wejściowa: 160 palet/h
- Wydajność wyjściowa: 190 palet/h
- System zarządzania magazynem HiLIS
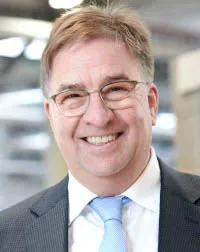
Dostosowany do naszych indywidualnych wymagań system zarządzania magazynem HiLIS firmy HÖRMANN Logistik gwarantuje maksymalną elastyczność i przejrzystość.
Mathias Kunert
Partner i Dyrektor Zarządzający, Kunert Wellpappe Bad Neustadt GmbH
AutoStore®
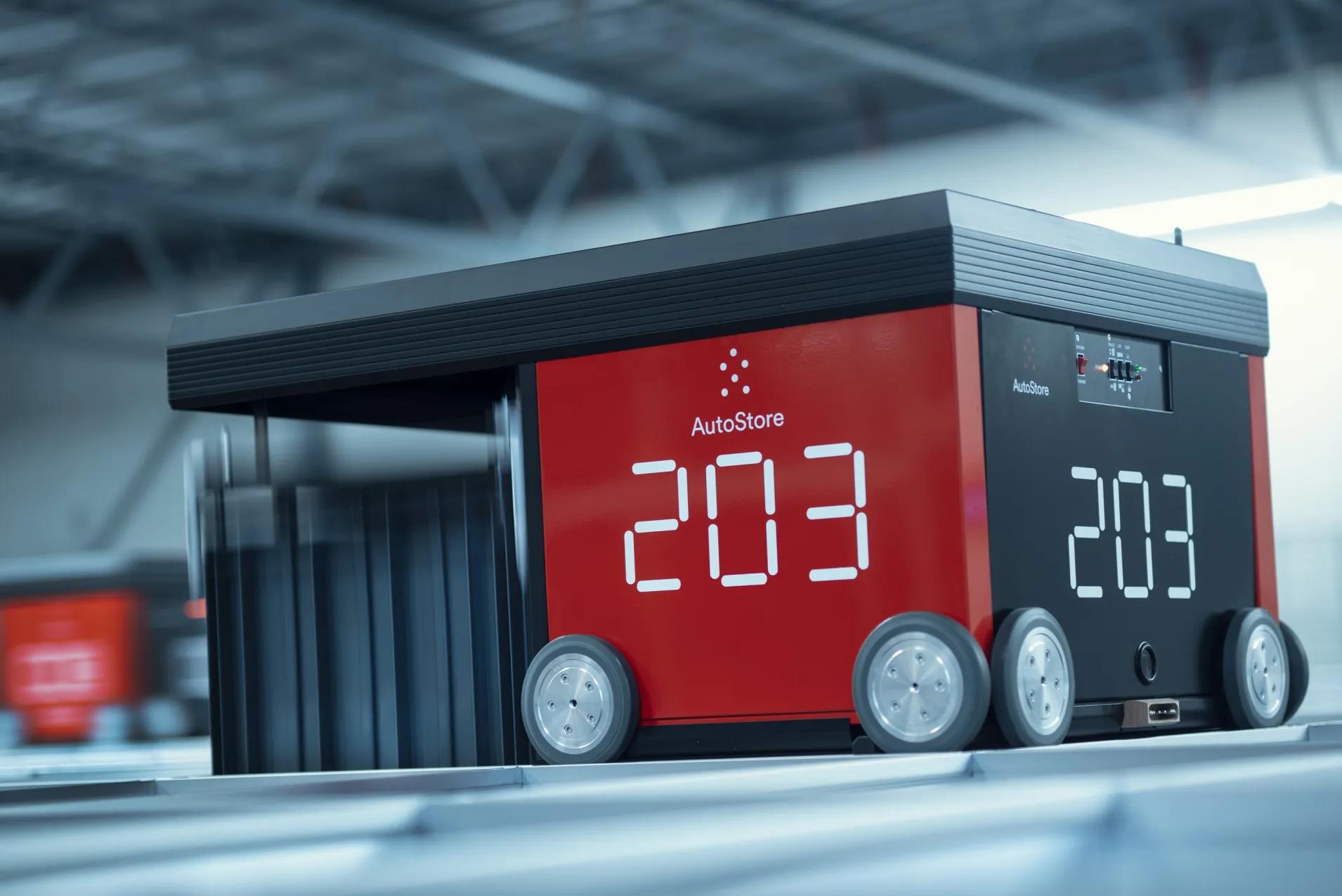
AutoStore® small parts warehouse for Pati-Versand.de in Herzlake
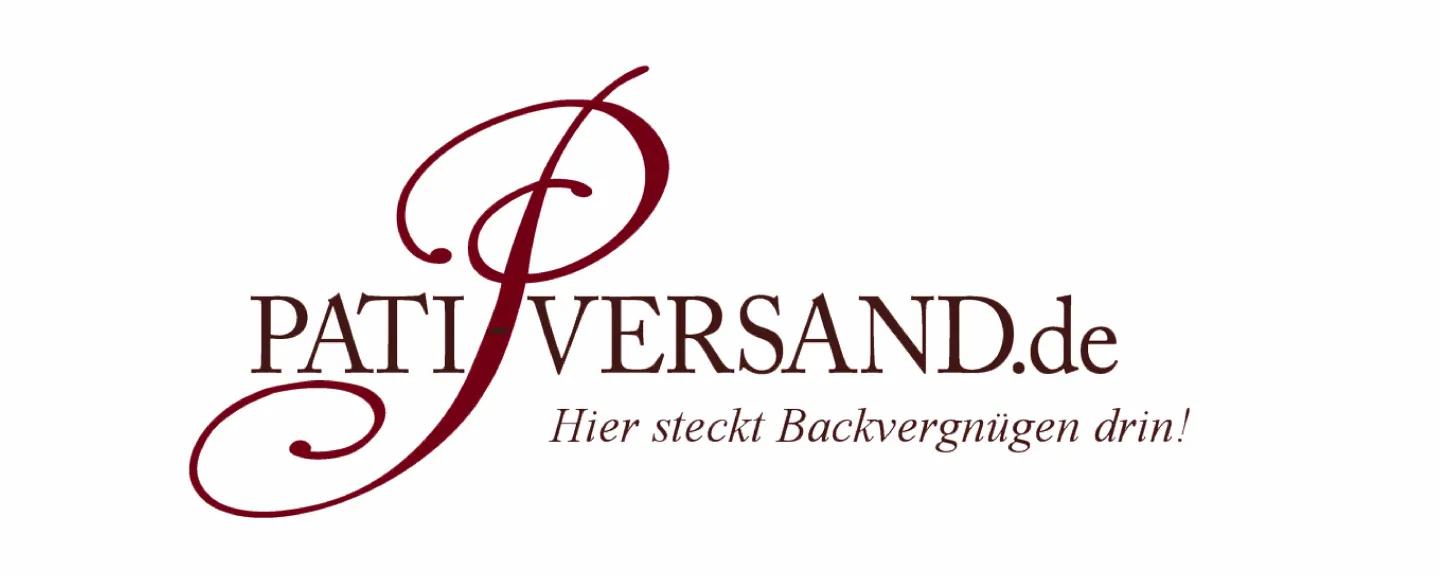
The Pati-Versand has specialised in patisserie supplies, confectionery and baking ingredients and accessories since 2007. The extensive product range, which is expanded annually with the latest trend articles, is also available in the tailor-made online shop. Today, www.pati-versand.de is the largest provider of cake, praline and baking ingredients for private customers in the German-speaking world. At the Herzlake location, an automated small parts warehouse for the storage of baking accessories is built in a new warehouse. Hörmann Logistik convinced with its AutoStore® concept and received the order to realise the system including the HiLIS AS warehouse management system.
Concept
The AutoStore® warehouse is built in the new building with a clearance height of 5,500 mm. Goods receipts and picking can be carried out at all workstations at any time.
For the individually tailored design of the AutoStore® system for Pati dispatch, Hörmann Logistik carried out several system simulations with original data in real time during the planning phase. The net operating time is 8 hours daily, 5 days a week.
The customer parameters together with the simulation results led to a system configuration with 12 levels, 25,000 containers, 6 carousel workstations and 2 conveyor workstation modules. This enables the required 110 goods storage and 1,040 goods retrieval operations, including the approximately 10 "fast orders" per hour, to be implemented. For a possible extension, 3 or 2 additional frames for carousel or conveyor workstations are already planned.
The AutoStore® system consists of an aluminium grid system with the overall dimensions of 24.5 m x 33.3 m x 4.1 m (L x W x H) including the service platform and a cladding of MDF boards coated on one side on three sides. In the grid system, stacks of 12 containers each are placed directly on the hall floor. Above the stacks of containers is the rail system (grid) on which the 32 battery-powered, autonomous robots move. The robots cooperatively pick up containers, re-sort them and are responsible for the supply and disposal of the carousel and conveyor workstations. The maximum total weight of the 649 mm x 449 mm x 330 mm (L x W x H) containers is 35 kg with a net load of around 30 kg. To ensure the maximum weight is maintained, an overweight check is carried out during storage. The containers can be flexibly subdivided by separating inserts for the use of several articles.
The system is controlled by the HiLIS AS warehouse management and control system, which was specially designed for AutoStore®. AutoStore® "only" knows the container number in the system, but not the contents. The higher-level WMS HiLIS AS knows the content of each container, takes over the higher-level management and control of the AutoStore® system and implements the logistical processes including the interfaces to the ERP system. The easy-to-understand graphical user interface of HiLIS AS provides clear work and picking instructions via touch screen. In addition, HiLIS AS supports permanent inventory processes, empty container insertion, status dialogues, special access to the containers and much more.
The AutoStore® small parts warehouse at Pati-Versand.de in Herzlake went into operation in early 2019.
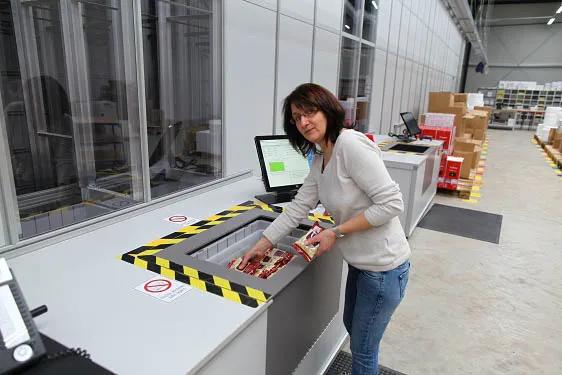
Das AutoStore®-System besteht aus einem Aluminium-Rastersystem mit den Gesamtabmessungen von 24,5 m x 33,3 m x 4,1 m (L x B x H) inkl. der Service-Bühne und einer Verkleidung aus einseitig beschichteten MDF-Platten an drei Seiten. In dem Rastersystem stehen Stapel mit jeweils 12 Behältern direkt auf dem Hallenboden. Über den Behälterstapeln ist das Fahrschienensystem (Grid) montiert, auf dem sich die 32 batteriebetriebenen, autonomen Roboter bewegen.
Die Roboter nehmen kooperativ Behälter auf, sortieren sie um und sind für die Ver- und Entsorgung der Carousel- und Conveyor-Arbeitsplätze zuständig. Das maximale Gesamtgewicht der 649 mm x 449 mm x 330 mm (L x B x H) großen Behälter beträgt 35 kg bei einer Netto-Zuladung von rund 30 kg. Zur Absicherung des Maximalgewichts findet bei der Einlagerung eine Übergewichtsprüfung statt. Die Behälter können durch Trenneinlagen flexibel für die Nutzung mehrerer Artikel unterteilt werden.
Die Steuerung der Anlage übernimmt das von HÖRMANN Intralogistics speziell für AutoStore® konzipierte Lagerverwaltungs- und –steuerungssystem HiLIS AS. AutoStore® kennt „nur“ die Behälternummer im System, nicht aber den Inhalt. Das übergeordnete LVS HiLIS AS kennt den Inhalt jedes Behälters, übernimmt die übergeordnete Verwaltung und Steuerung des AutoStore®-Systems und setzt die logistischen Prozesse inklusive der Schnittstellen zum ERP-System um. Die einfach verständliche, grafische Benutzeroberfläche von HiLIS AS stellt via Touch-Screen klare Arbeits- und Kommissionieranweisungen zur Verfügung. Zusätzlich unterstützt HiLIS AS permanente Inventurprozesse, Leerbehälter-Einbringung, Status-Dialoge, Sonderzugriff auf die Behälter und vieles mehr.
Das AutoStore®-Kleinteilelager bei Pati-Versand.de in Herzlake ging Anfang 2019 in Betrieb.
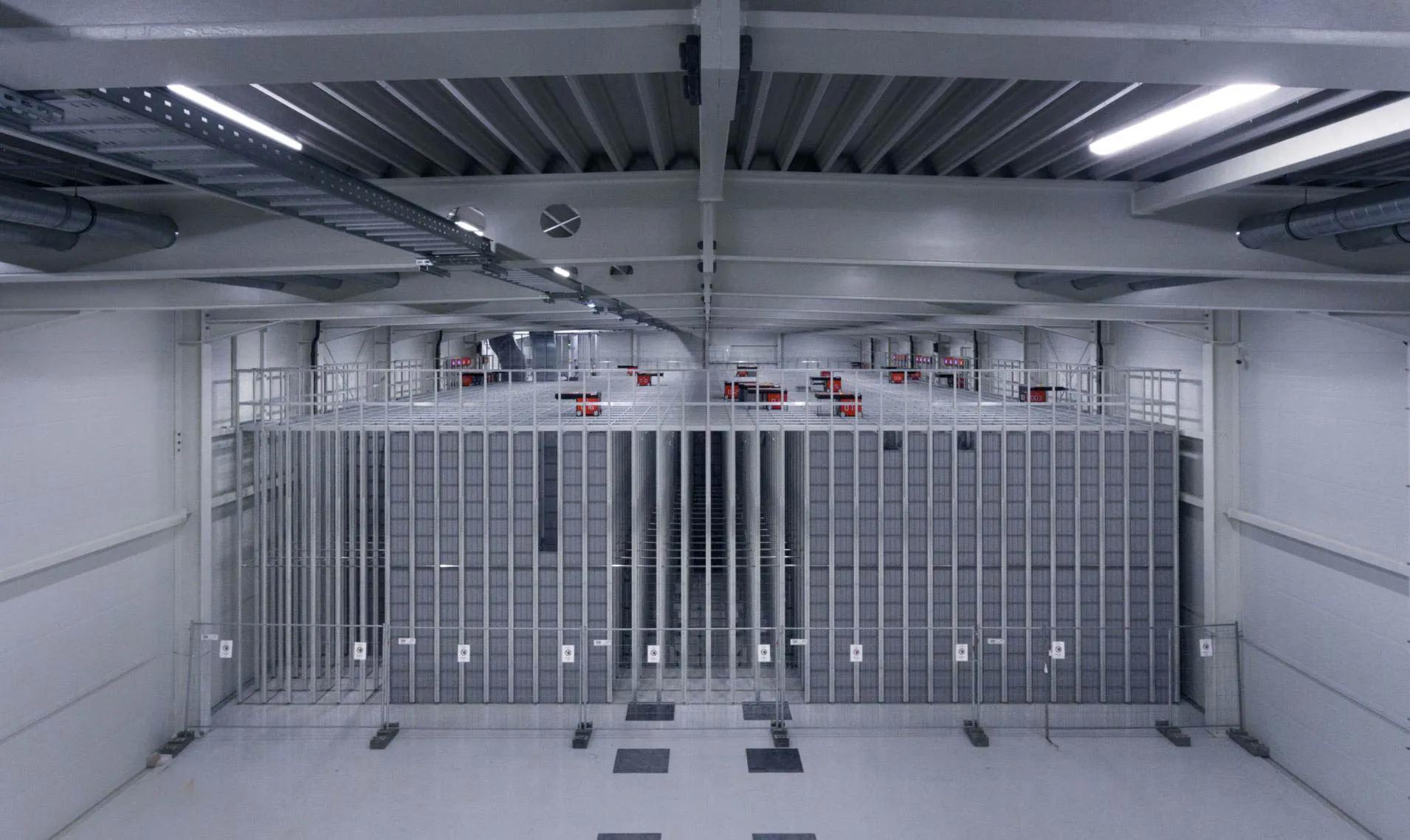
Referencje SportOkay
Mały magazyn części AutoStore® dla SportOkay.com w Innsbrucku
Jako specjalista w dziedzinie odzieży alpejskiej i sprzętu sportowego, firma e-commerce Sport Okay GmbH oferuje ponad 200 najlepszych marek w swoim sklepie internetowym www.sportokay.com. Unikalny na skalę światową jest widok 3D, za pomocą którego można przeglądać i sprawdzać artykuły w sklepie internetowym! Dziesiątki tysięcy zadowolonych klientów w Niemczech, Austrii, Włoszech i 15 innych krajach jest zaopatrywanych przez specjalistów sportowych w sercu Alp. Ze względu na bardzo pozytywny rozwój sklepu internetowego, SportOkay.com zainwestuje w budowę nowego centrum logistycznego w Innsbrucku, w którym w pełni zautomatyzowany system magazynowania małych części będzie wykorzystywany jako centralny system kompletacji. HÖRMANN Intralogistics zachwycił swoją koncepcją AutoStore® i otrzymał kontrakt na realizację systemu.
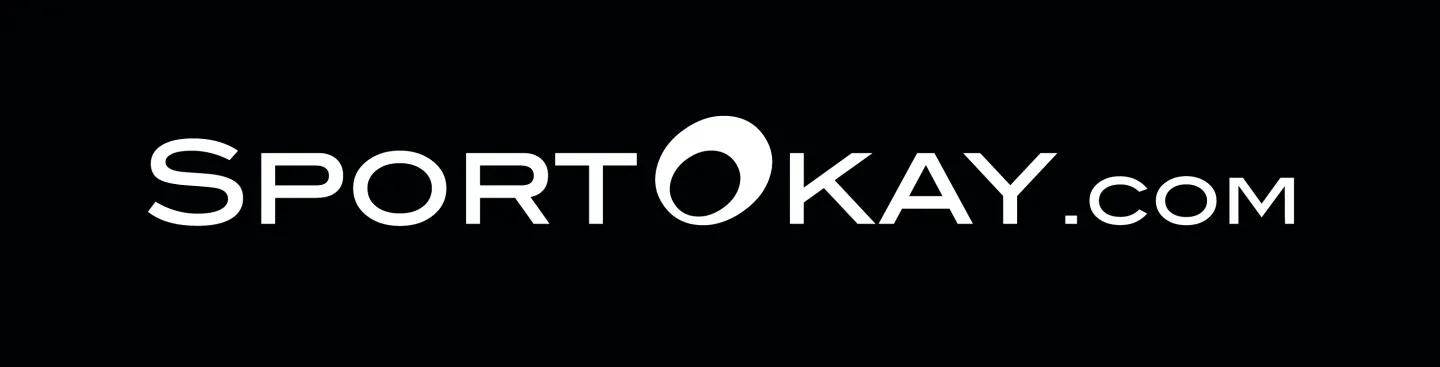
Koncepcja
Magazyn AutoStore® powstaje na pierwszym piętrze nowego budynku. Stanowiska pracy do przyjmowania towarów i kompletacji zamówień będą zlokalizowane na parterze.
W przypadku indywidualnego projektu systemu AutoStore dla SportOkay.com, Hörmann Logistik przeprowadził kilka symulacji systemu z oryginalnymi danymi w czasie rzeczywistym w fazie planowania.
Wymagania klienta, wraz z wynikami symulacji, doprowadziły do konfiguracji systemu w dwóch etapach budowy. W pierwszej fazie budowy 22 roboty z 26 500 pojemnikami na 16 poziomach i 6 powiązanych stacji roboczych z portami wahadłowymi umożliwią około 168 magazynów i zwrotów, a także 4000 pobrań dziennie i 400 pobrań na godzinę. W drugim, ostatnim etapie rozbudowy, szerokość siatki AutoStore® zostanie w przybliżeniu podwojona, dzięki czemu 44 roboty z około 55 000 pojemników i 12 stacji roboczych z portami wahadłowymi zapewnią około 336 odstawień i zwrotów, a także 8 000 kompletacji dziennie i 800 kompletacji na godzinę.
Dzięki nowemu, rozszerzalnemu magazynowi drobnych części AutoStore, centrum logistyczne SportOkay.com jest doskonale wyposażone na przyszłość dzięki osobistemu i dedykowanemu wsparciu zapewnianemu przez HÖRMANN Intralogistics.
Konrad Plankensteiner
Dyrektor zarządzający
System AutoStore składa się z aluminiowego systemu kratowego o wymiarach całkowitych 18,4 m x 36,9 m (79,2 m) x 5,4 m (dł. x szer. x wys.). W systemie siatkowym stosy 16 pojemników są umieszczane bezpośrednio na podłodze hali. System szynowy (siatka), po którym poruszają się 22 (44) autonomiczne roboty zasilane bateryjnie, jest zamontowany nad stosami kontenerów. Roboty współpracują przy odbieraniu i sortowaniu pojemników oraz są odpowiedzialne za dostarczanie i usuwanie odpadów ze stacji roboczych Swing-Port na parterze. Maksymalna masa całkowita pojemników o wymiarach 649 mm x 449 mm x 330 mm (dł. x szer. x wys.) wynosi 35 kg, a obciążenie netto około 30 kg. W portach przeprowadzany jest test nadwagi, aby upewnić się, że maksymalna waga nie zostanie przekroczona. Pojemniki można elastycznie dzielić za pomocą przegródek w celu wykorzystania wielu przedmiotów.
Stanowiska robocze do przechowywania, pobierania i kompletacji towarów w SportOkay.com znajdują się pod systemem AutoStore® na parterze. Artykuły są przywożone do stacji roboczych towarów przychodzących na paletach lub w pudełkach, rozpakowywane tam i przechowywane w systemie. Towar przeznaczony do kompletacji dostarczany jest przez system AutoStore® na jedno ze stanowisk towarów wychodzących, pracownik wyjmuje towar i umieszcza go w kartonie wysyłkowym.
Magazyn drobnych części AutoStore® w SportOkay.com w Innsbrucku został uruchomiony późnym latem 2018 roku.
Konfiguracja systemu składowania regałowego z wózkami SAFELOG AGV
W piwnicy na regałach składowane są duże przedmioty, takie jak narty, deski snowboardowe, kijki itp. Półki mają przypisane stałe miejsca przechowywania i są kodowane za pomocą tagów RFID na podłodze. W ten sposób powstaje obszar półek ze zdefiniowanymi ścieżkami przejazdu dla pojazdów AGV. W zależności od kolejności kompletacji, mobilne roboty transportowe SAFELOG AGV L1 pobierają regały z wymaganymi produktami z obszaru przechowywania. Podnośnik konsoli przenosi pojazd AGV z półką bezpośrednio do strefy kompletacji i właściwego stanowiska pracy. Regały mogą być wyposażone w ramiona wspornikowe lub regulowane półki. Po zakończeniu kompletacji regały są zwracane do miejsca składowania przez pojazd AGV.
Kompletowane zamówienia są również transportowane ze stacji kompletacji AutoStore bezpośrednio do maszyny pakującej przez specjalnie skonfigurowane pojazdy AGV SAFELOG typu S2.
Zasada "towar do człowieka" umożliwiła efektywne wykorzystanie przestrzeni magazynowej i skrócenie czasu podróży pracowników podczas czynności kompletacyjnych o około 80%. Znacząco zwiększa to wskaźnik kompletacji.
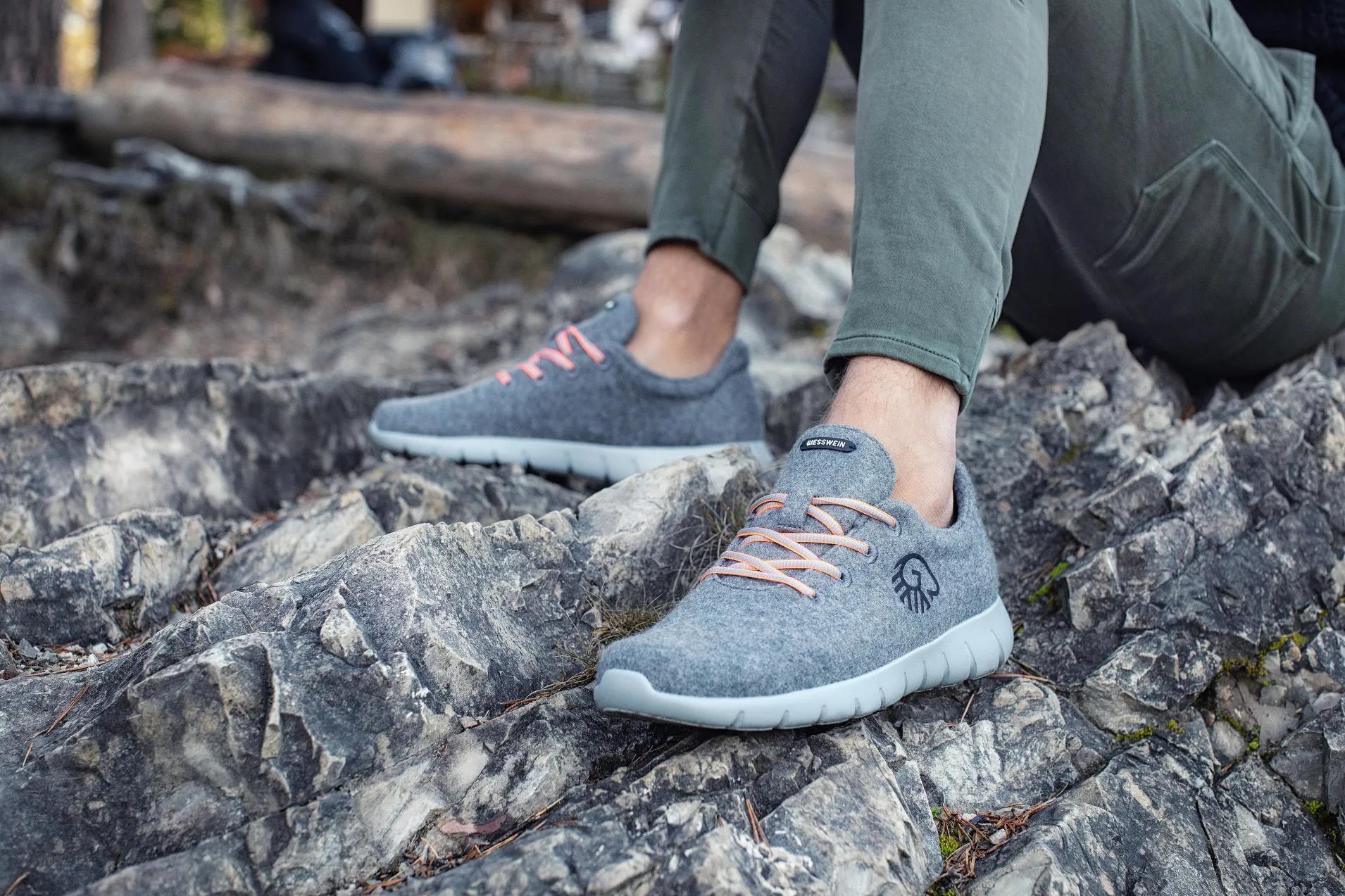
Modern AutoStore® warehouse for original Giesswein mill products in Austria
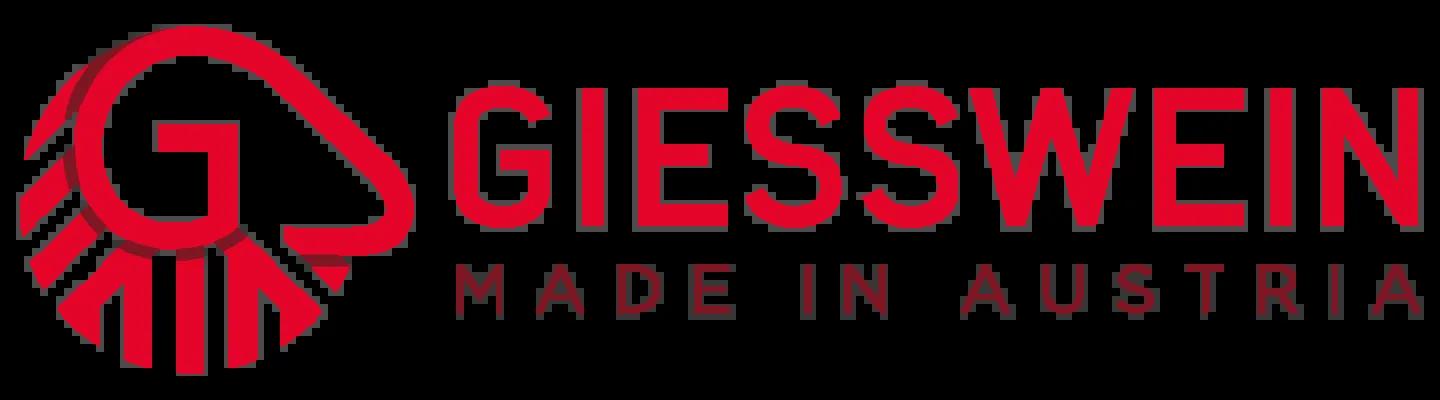
Giesswein Walkwaren AG is a Tyrolean family business in its third generation. From hand-picked wool in traditional quality, modern, sustainable and functional clothing and shoes are produced in our own production facilities. With special know-how and a holistic approach, the company has developed into Europe's leading manufacturer of clothing made of 100% new wool. At the Brixlegg site, a finished goods warehouse was built in an existing warehouse to support the constantly growing online shop business and stationary trade. The tailor-made concept with the modern, versatile AutoStore® system was developed by Hörmann Logistik.
Concept
Joint planning discussions and several system simulations with real data led to the individual AutoStore® system configuration with 31 robots and 17,500 containers on nine levels. The height of the AutoStore® grid was determined by the 4.6-metre high existing hall.
In order to guarantee the performance specifications of 140 storage and 900 retrieval operations per hour, 5 carousel and 3 conveyor workstation modules were initially provided. A further carousel workstation module has already been preconfigured. The single-double grid with the overall dimensions of 26.1 x 30.4 x 3.1 m (L x W x H) is clad on two sides.
The 17,500 containers in the standard format 649 mm x 449 mm x 330 mm (L x W x H) each allow a load capacity of approx. 30 kg.
31 robots supply the Carousel workstations 8 hours a day. This requires a charging process per robot of approx. 4 hours per day, for which a total of 24 charging stations are provided at the edge of the grid.
Maximum flexibility and efficiency
In principle, all workstations are equipped so that goods receipts or picking can be carried out there at any time. The incoming goods are delivered to the workstation by the warehouse staff.
In the grid system, stacks of 9 containers each are placed directly on the hall floor. A single-double-grid rail system is mounted above the stacks of containers, on which the battery-powered, autonomous robots travel. They pick up containers cooperatively, re-sort them as required and serve them at the carousel ports. The containers can be flexibly subdivided by means of separating inserts for the use of several articles.
The AutoStore® system at Giesswein Walkwaren in Brixlegg was put into operation in July 2020.
"The new AutoStore system makes our picking processes much more effective and makes our employees' work easier. A benefit for the whole team."
Markus Giesswein
Owner
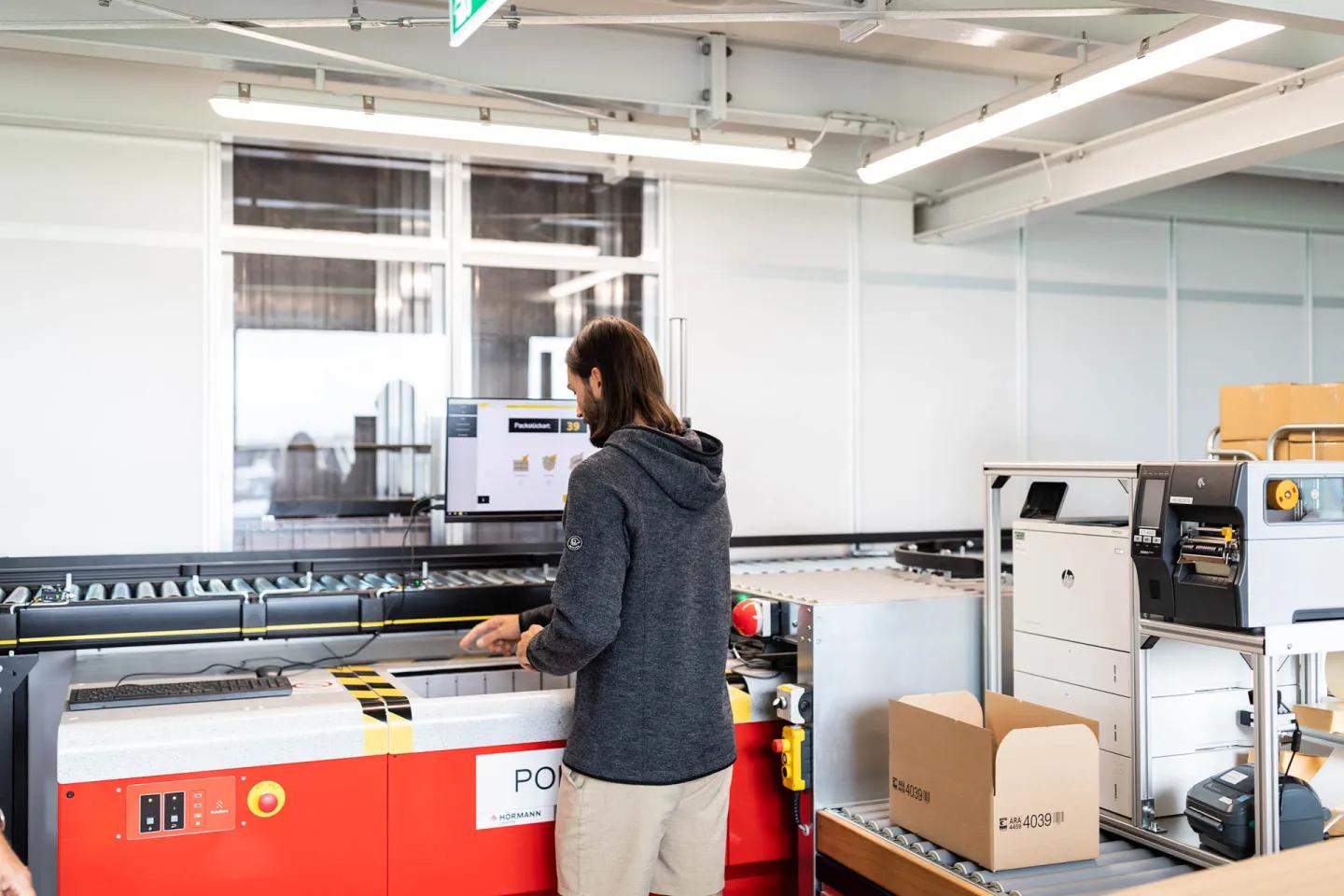
Maximale Flexibilität und Effizienz
Prinzipiell sind alle Arbeitsplätze so ausgestattet, dass dort jederzeit Wareneingänge oder auch Kommissionierungen durchgeführt werden können. Die Andienung der Eingangswaren am Arbeitsplatz erfolgt durch die Lagermitarbeiter.
In dem Rastersystem stehen Stapel mit jeweils 9 Behältern direkt auf dem Hallenboden. Über den Behälterstapeln ist ein Single-Double-Grid Fahrschienensystem montiert, auf dem die batteriebetriebenen, autonomen Roboter fahren. Sie nehmen kooperativ Behälter auf, sortieren sie bei Bedarf um und dienen diese an den Carousel-Ports an. Die Behälter können durch Trenneinlagen flexibel für die Nutzung mehrerer Artikel unterteilt werden.
Das AutoStore® System bei Giesswein Walkwaren in Brixlegg wurde im Juli 2020 in Betrieb genommen.
AutoStore Giesswein Brixlegg
Die neue AutoStore Anlage macht unsere Kommissionierungsprozesse wesentlich effektiver und erleichtert unseren Mitarbeitern die Arbeit. Ein Gewinn für das ganze Team.
Markus Giesswein
Inhaber