Newsmeldungen 2022
2022
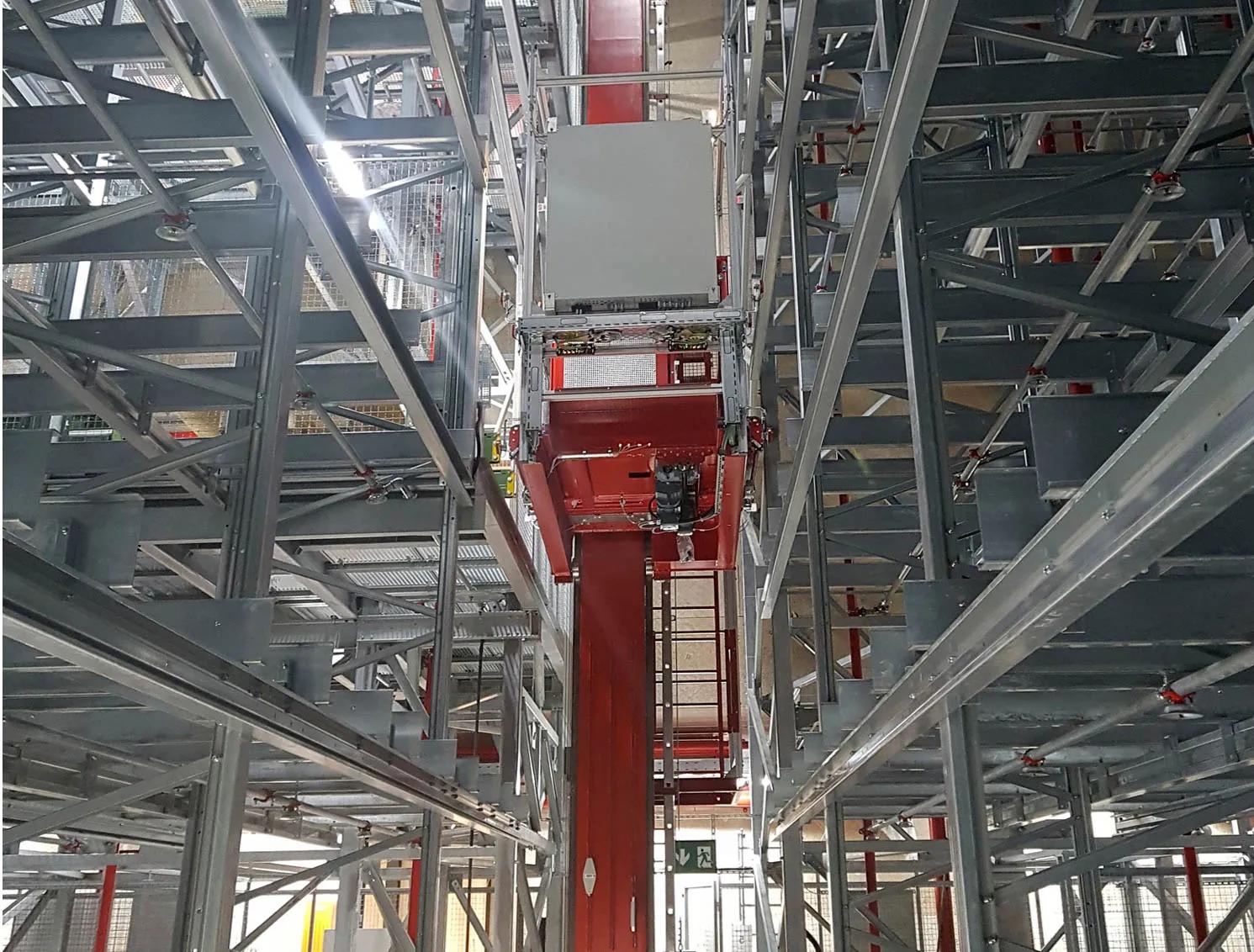
Referenz rondo
Neubau 8-gassiges vollautomatisches HRL für die Lagerung von Fertigware aus Wellpappe für Rondo in Frastanz, Österreich
Die Rondo Ganahl Aktiengesellschaft ist ein traditionsreiches österreichisches Familienunternehmen mit 220-jähriger Geschichte. Das Kerngeschäft der international tätigen Wellpappe-Spezialisten ist die Herstellung von Wellpappe-Verpackungen, Wellpappe-Rohpapieren sowie die Sammlung von Papier und Verpackungen. Das Wellpappewerk im österreichischen Frastanz (Vorarlberg) produziert Wellpappe-Rohpapiere auf der Basis von 100% Altpapier und nimmt mit weißen und geflammten Testliner-Sorten eine führende Rolle in den Hauptmärkten Deutschland und Österreich ein. Für die Lagerung von Fertigware hat HÖRMANN Intralogistics ein neues Hochregallager mit automatischer Produktionsanbindung und Versandbereich errichtet, das von der Gutweniger Logistik GmbH geplant wurde.
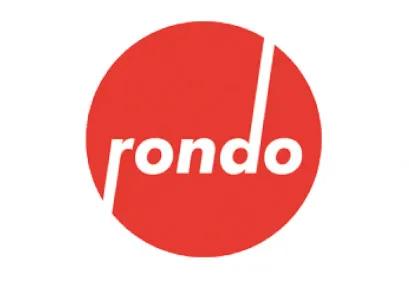
Konzept
In dem neuen 8-gassigen Hochregallager (HRL) werden unterschiedlichste Palettenformate aus Holz oder Kunststoff gelagert. Dabei dient das HRL zur Produktionsentsorgung, zur Andienung und Entsorgung der Kommissionierbereiche, zur Einlagerung von Handelsware und zur Auslagerung von Versandware.
Die Paletten sind artikelrein beladen, wobei in den Gassen 1-7 die kleineren Palettenformate eingelagert werden, die mit je einem Kanalfahrzeug transportiert werden. In Gasse 8 arbeitet ein spezielles Regalbediengerät mit vier Teleskopgabelzinken, das Großformate mit einer Länge von bis zu 3,1 m ein- und auslagern kann. Die Paletten aus der Produktion werden von dort über eine Fördertechnikbrücke Richtung Hochregallager transportiert. Die zur Kommissionierung benötigte Ware wird in Auftrags-Reihenfolge abgearbeitet. Dazu lagern die Regalbediengeräte (RBG) der Gassen 1-7 die Ware im Erdgeschoss aus und dienen sie dann am RBG 8 an, welches die Paletten ins Obergeschoss befördert und dort an die Fördertechnik zu den Kommissionierbereichen übergibt.
Für die Versandbereitstellung wählt das WMS HiLIS die erforderlichen Paletten clever in der richtigen Auslagerreihenfolge und erzielt so eine optimale Lagerleistung. Die Paletten werden von den RBGs ausgelagert und an den acht Verladebahngruppen mit je zwei Spuren bereitgestellt. Jeder Tour (LKW) wird von HiLIS eine Verladebahngruppe zugeordnet. Mittlere und breite Paletten belegen beide Spuren, kleinere Paletten nur eine Spur.
Das Hochregallager arbeitet parallel zu den Betriebszeiten des Wellpappenwerks an 6 Tagen die Woche, rund um die Uhr. Die Anlagenleistung wurde auf die Anforderungen der Produktionsentsorgung, der Kommissionier-versorgung und der Versandleistung ausgelegt. Die Lagerverwaltung und –steuerung erfolgt mit dem bewährten Hörmann intra Logistics System HiLIS, das mit dem Kundensystem über Schnittstelle kommuniziert. Durch das HiLIS ECO-Powermanagementsystem sparen die Regalbediengeräte durch intelligenten Energieausgleich bis zu 25% des Energieverbrauchs.
Highlights
- 8-gassiges Hochregallager 74 x 70 x 29 m (L x B x H)
- 7 Regalbediengeräte mit je einem batteriebetriebenen Kanalfahrzeug
- 1 Regalbediengerät für Großformate mit vier Teleskopgabelzinken
- Stellplatzkapazität ca. 20.000 Paletten
- Max. Einlagerleistung 180 Paletten pro Stunde
- Max. Auslagerleistung 25 Paletten pro Stunde
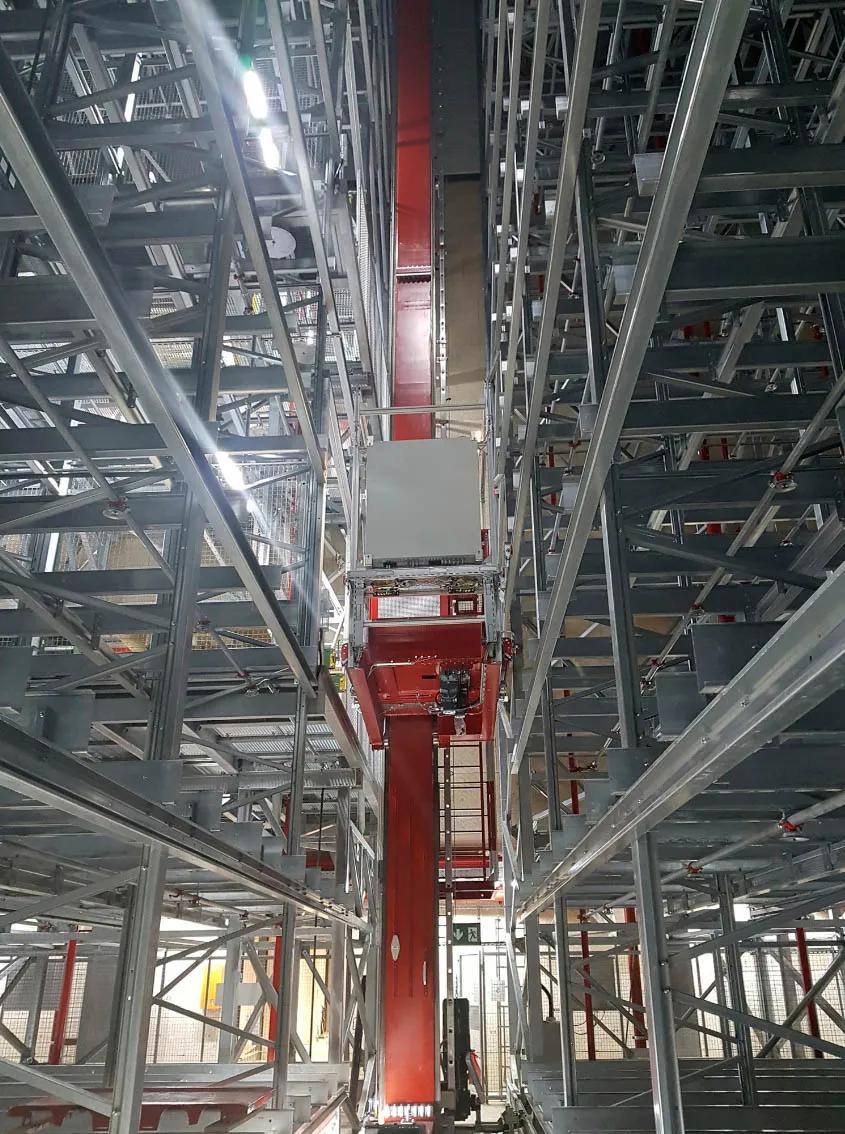
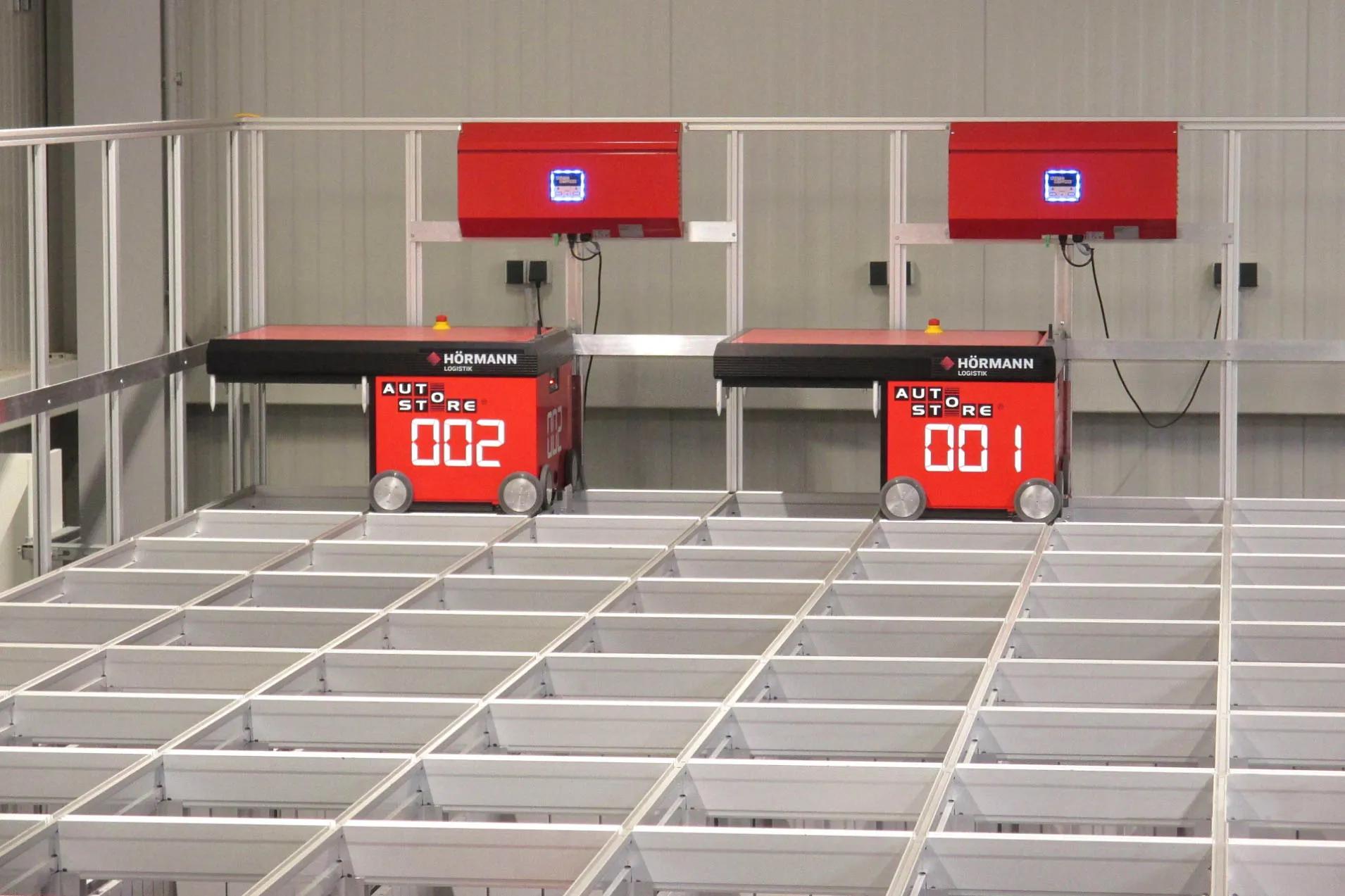
Referenz Theegarten
Maßgeschneidertes AutoStore® Kleinteilelager für Theegarten-Pactec in Dresden
Als einer der weltweit führenden Hersteller auf dem Sektor der Verpackungstechnologie entwickelt die Theegarten-Pactec GmbH & Co. KG qualitativ hochwertige und intelligente Verpackungsmaschinen. Mit Innovationskraft und Premiumqualität hat sich Theegarten-Pactec auf kleinstückige Artikel in der Food- und Nonfoodbranche spezialisiert. Am Firmensitz in Dresden sollte ein leistungsfähiges automatisches Kleinteilelager zur Versorgung der Montage von Verpackungsmaschinen entstehen. HÖRMANN Intralogistics hat für die speziellen räumlichen Gegebenheiten und die Materialflussanforderungen eine AutoStore®-Lösung realisiert.
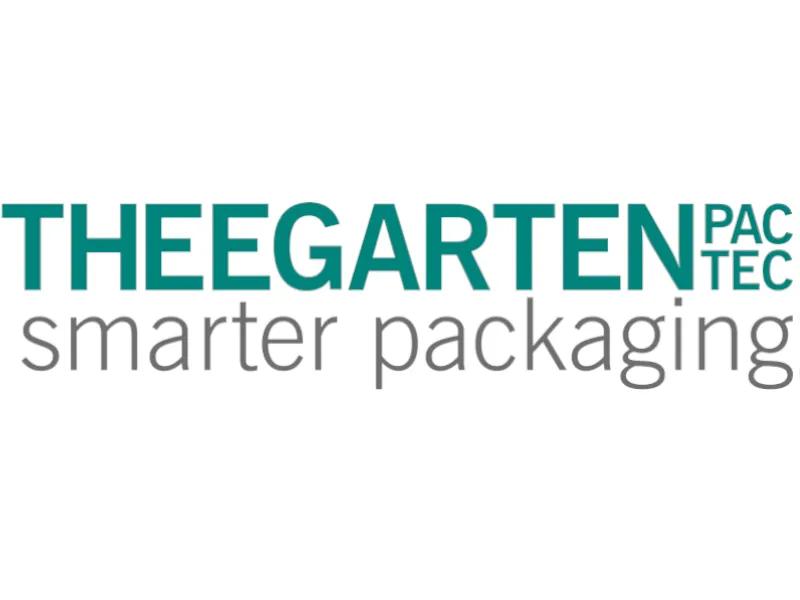
Konzept
Am Wareneingang erfolgen die Kontrolle und die Erfassung der angelieferten Ware. Die Mengen für die AutoStore®-Lagerung werden an den AutoStore®-Kommissionierplätzen bereitgestellt. Sobald in einem AutoStore®-Behälter ein Platz frei wird, lagert der Kommissioniermitarbeiter einen Artikel ein und bucht diesen in den am Kommissionierplatz bereitstehenden, offenen AutoStore®-Behälter.
So werden bis zu 60 Artikel pro Stunde eingelagert und ein kontinuierlich hoher Behälterfüllgrad garantiert. Gleichzeitig bleibt so die Anzahl der Behälterbewegungen minimal. Bei Bedarf können für eine Einlagerung auch passende AutoStore®-Behälter aktiv angefordert werden. Dabei wird vom LVS-System der AutoStore®-Behälter ausgewählt, der das entsprechende Volumen frei hat, das Zulagergewicht aufnehmen kann und am schnellsten abrufbar ist.
Intelligente Algorithmen optimieren die Warenbewegungen
Insgesamt umfasst das AutoStore®-Lager von Theegarten-Pactec gut 14.000 Behälter, 6 Roboter und 3 Einlager-/Kommissionierarbeitsplätze. Alle Warenbewegungen innerhalb des AutoStore®-Systems finden in einem selbstoptimierenden Prozess statt. Mit Hilfe eines intelligenten Algorithmus beginnen die Umschichtungen innerhalb eines Stapels rechtzeitig vor dem Transport des betreffenden Behälters zur Kommissionierung. Gleichzeitig sinken Behälter mit weniger häufig benötigten Artikeln stetig weiter nach unten, während Artikel mit häufigen Zugriffen permanent oben stehen bleiben. So können die Kommissioniermodule optimal und ohne Wartezeiten für ca. 90 Vorgänge pro Stunde mit Behältern versorgt werden.