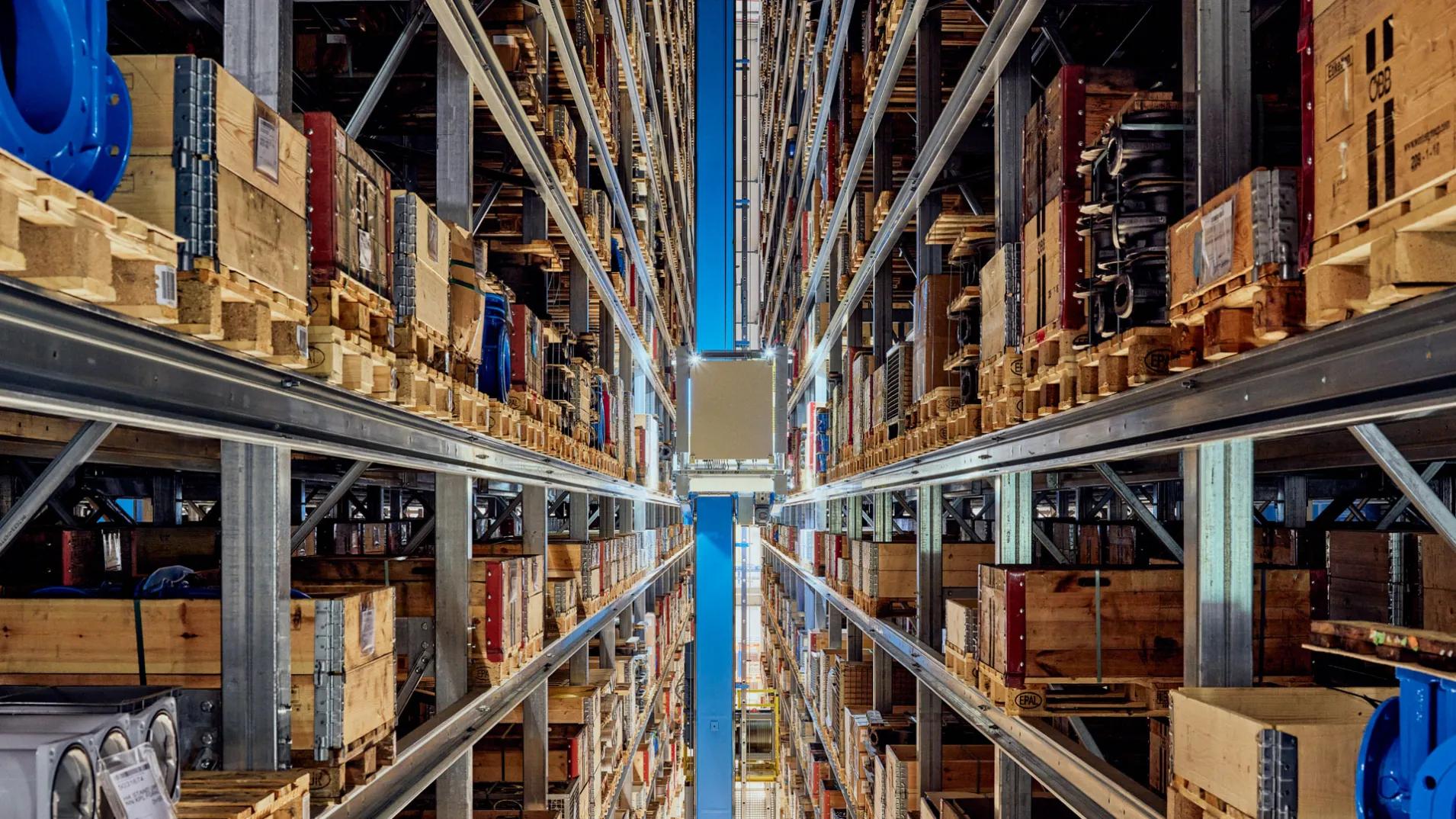
Services
Sustainable intralogistics - Eco power management with power caps
Optimising energy consumption is an absolute must for intralogistics solutions, reducing CO₂ emissions from power generation as well as reducing operating costs.
When building a new high-bay warehouse or modernising an existing one, our intelligent HiLIS Eco power management system can reduce the energy consumption of the stacker cranes by approx. 25%.
Using innovative Powercap technology for storage and retrieval machines, power consumption can be reduced by approx. 40% and connected load by approx. 65%.
- Optimal use of generator power generated from one axis for the other
- Reduction of energy demand through optimised weight management
- Storage of generator-generated energy directly on the RBG
- Up to 40% reduction of electricity consumption
- Saving CO₂
What is cap memory?
The word "caps" comes from "capacitors", referring to electrochemical capacitors. These devices have high power density and can be charged and discharged very rapidly.

Our partner for energy optimisation with photovoltaic solutions
With years of experience, we design system solutions for regenerative energy generation and use. From planning to maintenance, our team of electrical, installation and technology specialists is actively at your side. With quality 100% Made in Germany technology, we can help you on your way to a sustainable energy future.
The importance of renewable energy is increasing day by day. Photovoltaic systems generate electricity from sunlight and so make a significant contribution to protecting the environment. As general contractor, we offer complete infrastructure solutions for high-bay warehouses, industrial systems, house and home.
More Information (in german)
HiLIS Eco-Power management
Since a stacker crane consumes energy during travel and lifting, but releases energy during braking and lowering, it is a challenge to make dissipated energy immediately available to the system again. For this purpose, HÖRMANN Intralogistics uses DC link technology as standard in the stacker crane control system, which establishes an energy balancing connection between the trolley and hoist controllers. The trolley and hoist unit thus share the energy released. The HiLIS WMS issues the specifications for optimised travel and lifting movements while complying with start-up times.
Optimisation is achieved on the basis of two fundamental parameters:
- Matching of the axle movements of the trolley and hoist - for example, the released energy of the downward movement of the hoist is used to accelerate the trolley. In turn, the hoist is then started when energy is available again due to the deceleration of the trolley.
- Matching of speeds - here, for example, the speed of the trolley is reduced if the trolley has to travel upwards and the lifting time is longer than the travel time. If the trolley has to run downwards, its speed is reduced so that the travel time of the trolley matches the acceleration and travel.
Through these energy management measures, the resulting energy is cost-effectively provided directly to the next consumer at the RBG.
HiLIS Eco-Power management enables electricity across the RBG, resulting in cost savings. As soon as the HiLIS has issued the order for an AS/RS movement, the corresponding storage and retrieval machine calculates the power requirement for this as a percentage depending on the maximum power consumption available, and reports this to the HiLIS in a special telegram.
After the order has been placed, HiLIS calculates the power requirement for it as a percentage depending on the maximum power consumption available and reports it as a special telegram.
Only after HiLIS has sent a release telegram taking into account the maximum current efficiency of all the stacker cranes involved, does the respective stacker crane start its journey. With this measure, the required transformer power can be reduced by approx. 30% in systems with several SRMs, and further costs can be saved.
Reduced connected load through weight management as early as the planning phase
Significant weight management measures can be included in the definition of project requirements to reduce the connected transformer load. If, for example, the proportion of pallets with maximum weight is low, but the system is dimensioned for this weight, the drive power can be significantly reduced if it is possible to run at reduced speed at maximum weight. The HÖRMANN Intralogistics HiLIS WMS enables energy-efficient control of high-bay racking systems for individual customer requirements.
The next generation RBGs with Powercap technology
HÖRMANN Intralogistics Powercaps store the energy generated by the stacker cranes regeneratively, saving power that would otherwise be dissipated. The high starting currents during acceleration are drawn from the powercaps. This dramatically reduces the connected loads from the power grid, requires significantly smaller transformers, and the cross-sections of the cables can be reduced by 75%. This reduces power consumption by approximately 40%, resulting in massive CO₂ savings over the entire service life of the system.
Another advantage is consistency. Powercap technology means that any additional energy required from the power grid can be called up constantly. This argument, which saves the energy provider from having to reserve for power peaks, e.g., when several RBGs start up at the same time, can be used to negotiate the price of the power needed.
Fast payback of powercap costs and maximum energy efficiency
The additional cost of Powercap technology pays for itself in about 3 years on average, due to significant savings in energy costs, in addition to the one-time savings on infrastructure (transformer, feeders, etc.) and federal energy efficiency incentives.