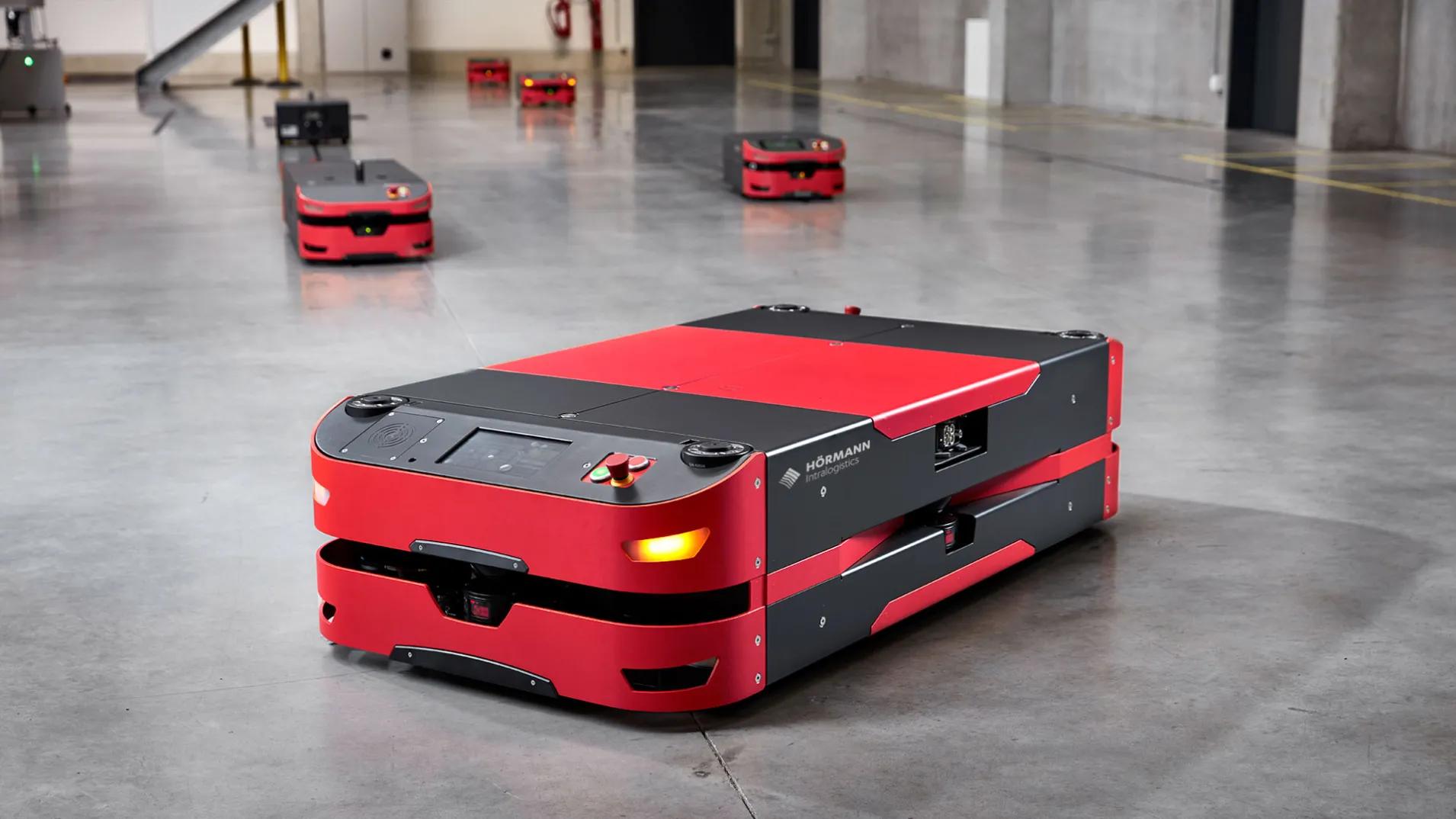
Robotics
Moving Racks solution - goods-to-person (logistics) with robots and racks
Constantly increasing item volumes, along with ever increasing demands for fast and efficient order picking, pose new challenges for classic warehouse logistics. Working with SAFELOG, HÖRMANN Intralogistics has developed an innovative moving racks system for picking process automation, even for bulky goods, based on the goods-to-person principle.
Mobile transport robots (AGVs) transport the goods in modular racks, sequentially and just-in-time from the storage areas to the picking stations. HÖRMANN Intralogistics’ smart HILIS Warehouse Management System controls and monitors all picking processes to guarantee maximum performance.
The advantages at a glance
- Reduced staff and walking distances
- Flexible and modular expansion at any time with more AGVs or racks
- Picking areas can be supplemented by support systems, e.g. pick-by-light
- In multi-order picking configuration, the HiLIS WMS offers additional possibilities for increasing picking efficiency with intelligent batch formation.
What are Moving Racks?
Moving Racks replace or supplement traditional picking areas (man-to-goods) with high staffing levels and long walking distances, with an efficient, flexible system of modular shelving (racks) that are presented in a timely and sequential manner to the picking staff.
Rack transport from the storage areas to the picking workstations is carried out by mobile transport robots. This means that all system picking processes are intelligently contolled and monitored by software to ensure maximum performance and timely delivery.

Our Partner
The ever-increasing volume of items, added to the ever-increasing demand for fast and efficient order picking pose new challenges for classic warehouse logistics. With a range of robotic solution it’s possible to achieve significant cost savings and increase resource efficiency.
In the ideal case, this would involve combining several systems, such as a automated CubeStorage system by AutoStore for storage and retrieval and an AGV shuttle system for the subsequent connection to the packaging line. For these, as well as for stand-alone scenarios, we work closely with our partner Safelog, which manufactures autonomous shelf-lifting robots.
The solution in detail
Storage Area
In the HÖRMANN Intralogistics Moving Racks system, the storage area for all goods consists of the individual racks on their storage spaces. Different types of standardised racks can be combined with various interiors (e.g. EURO pallet, shelf or grid) or configured as individual racks.
All standard racks have the same 1280 mm x 900 mm footprint and a height of up to 2500 mm. The moving racks are placed in a grid layout with travel paths in between in the storage areas. The grid layout can be flexibly adapted to different local conditions, around obstacles or in separated areas.
In addition, areas close to the pick zones can be reserved for fast-moving items.
Maintenance and loading area
Battery charging stations for mobile robots are built-in to the Storage Area, and can be distributed and placed according to the available connection options. This way, mobile robots on charge are available for transport operations without an additional approach route. The robots manage their charge status independently, and always approach the charging stations in good time.
Picking Area
The Picking Area consists of one or more picking workstations and associated buffer locations. Each picking area is connected to the storage area by defined travel paths. The workstations themselves can be individually designed.
In the standard configuration, a workstation comprises two rack storage locations. This means the rack that follows can already be staged during a pick process. The staging areas are separated from the MA work area only by stop bars on the floor, to permit optimal accessibility of the moving racks.
In addition to the rack staging areas, the workstation includes a work table with a flat-screen display showing the HiLIS picking interface and target locations for the picked items. Destination locations can be floor carts, conveyor elements or pallet locations for example.
HÖRMANN Intralogistics - Moving Racks
The control system allows omnidirectional travel, so that a robot can move in any direction at any time. This increases the operational flexibility of the vehicles, as they can be maneuvered in very confined spaces. It also makes it possible to turn racks on the spot.
Mobile AGV robots by SAFELOG
SAFELOG mobile transport robots are used to transport the racks. With a height of just 340 mm, these driverless transport vehicles are equally suitable for driving under the racks as they are for transporting pallets or wire mesh boxes. The weight of the Topload can be up to 1,500 kg.
SAFELOG has developed an agent-based control system for the mobile robots, through which the individual vehicles communicate with each other and with the surrounding production and logistics facilities. This ‘swarm’ intelligence of the transport vehicles controls both route coordination and task distribution between the devices. This means they do not require a higher-level control station for their operation. The software configuration is customer-specific to the respective requirements and linked to the HiLIS WMS for order control.
To achieve the highest possible technical availability of the overall system, various navigation types are available, and can also be used in combination. Depending on the application conditions, magnetic track, RFID tags, virtual track and contour navigation are used individually or together as a hybrid navigation system.
Contact us now
Bring your company into the advancing world of innovative logistics solutions. With our moving racks and mobile robots, you can significantly increase the efficiency and flexibility of all picking operations