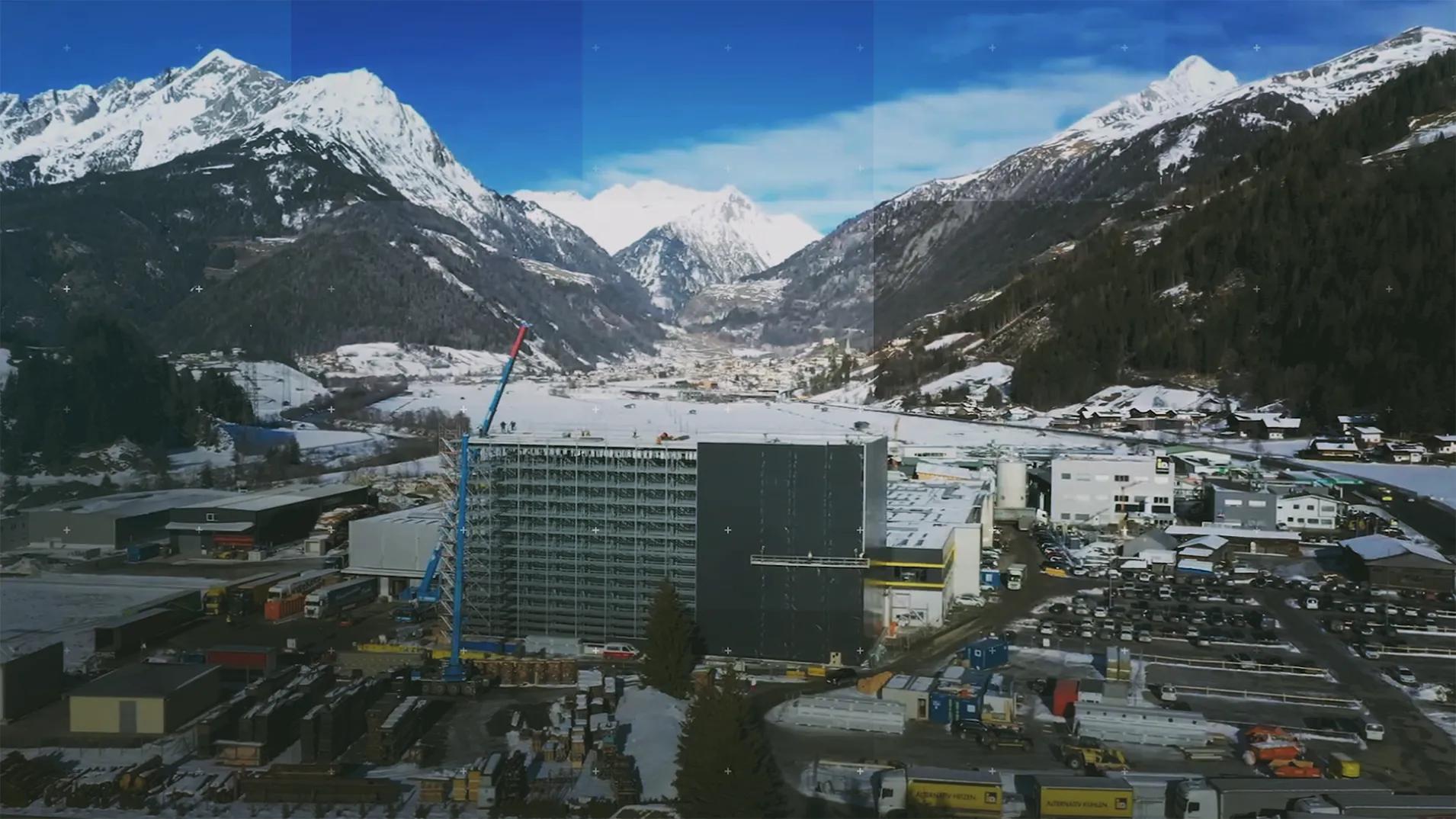
Reference iDM Energiesysteme GmbH
Multi-solution project comprising an automated high-bay warehouse and AutoStore System® for the new logistics center at iDM Energiesysteme GmbH in Matrei
The iDM Group is Austria's largest manufacturer of heating heat pumps. Over 400 employees develop, produce and distribute more than 20,000 heat pumps for heating, cooling and hot water every year. in 2019, logistics was a bottleneck in meeting the booming demand.
This is how the success story of the collaboration between Hörmann Intralogistics, iDM-Energiesysteme in Matrei, East Tyrol and the planning office iBH Schepper began. An innovative multi-solution storage system was created and has revolutionized the Austrian heat pump manufacturer's warehouse in many respects - from output and occupational safety to employee satisfaction.
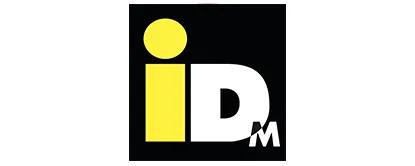
Concept
Automatic high-bay warehouse for the storage of semi-finished and finished goods
The new three-aisle high-bay warehouse (HBW), measuring 57.5 x 22.5 x 31 m (L x W x H), is connected to the incoming goods area via pallet conveyor technology. A contour and weight check is carried out at the infeed point. The Euro pallets, industrial pallets or pallet cages on Euro pallets are then transported to the pallet circuit in the pre-zone of the high-bay warehouse. Each of the three high-bay aisles has a separate storage and retrieval point. This is where the storage and retrieval machines (SRMs) pick up the pallets. The SRMs move to the assigned storage location using camera-based compartment fine positioning. The double-deep telescopic forks of the stacker cranes can extend to the second z-position and thus set the pallets down double-deep with pinpoint accuracy. The three storage and retrieval machines work with the HiLIS ECO power management system, which saves up to 25% of energy consumption through intelligent energy balancing. The HBW has space for 9,324 pallets and achieves a storage capacity of 93 pallets/h and a retrieval capacity of 85 pallets/h.
Dynamic AutoStore® small parts warehouse for 16,000 containers
In order to optimally adapt the AutoStore® small parts warehouse to iDM's requirements, HÖRMANN Intralogistics carried out a comprehensive system simulation with real data. This resulted in a configuration with a carousel port on the west side of the AutoStore® warehouse, which is primarily intended for storage. Four conveyor ports are aligned to the central picking stations. The 16,000 bins measuring 649 x 449 x 330 mm (L x W x H) are stored and handled on seven levels. Each container has a net load capacity of approx. 30.5 kg.
The single-double grid with overall dimensions of 29.8 m x 35.3 m x 3.5 m (L x W x H) is installed above the container stacks. On the grid, 9 Red-Line robots move in two directions thanks to their four pairs of wheels arranged around the corners, enabling them to reach any position in the grid. They communicate via WLAN with the AutoStore® controller, which assigns the transport orders to the individual robots. If the order load is low or the battery capacity is too low, the robots move independently to one of the 10 charging stations at the edge of the grid. The AutoStore® system is connected to the electrical department on the upper floor via two transfer cells, a lifter and container conveyor technology
Central picking for high-bay warehouse and AutoStore® small parts warehouse
Four picking stations are connected directly to the high-bay warehouse via conveyor technology and distribution trolleys. One conveyor port of the AutoStore® system is also responsible for supplying each picking station. This means that both palletized goods and goods from AutoStore® can be picked at each workstation. Supply from the high-bay warehouse takes place via two distribution trolleys on one rail, which can work partially redundantly. In addition, a gripper lifting aid supports each picking station when removing heavy items.
Maximum performance and availability with the WMS HiLIS and HiLIS AS
Warehouse management, system control and system visualization of the two automatic and manual storage areas are carried out with the tried-and-tested HÖRMANN Intralogistics Warehouse Management System HiLIS and the integrated, tailor-made AutoStore® WMS HiLIS AS, which communicate with the customer system via an interface.
Goals and challenges of the project:
- Increase in performance - from 3,000 to 30,000 units per year
- Inventory security - complete transparency of stock levels
- Efficient material flow - digitalisation and just-in-time delivery
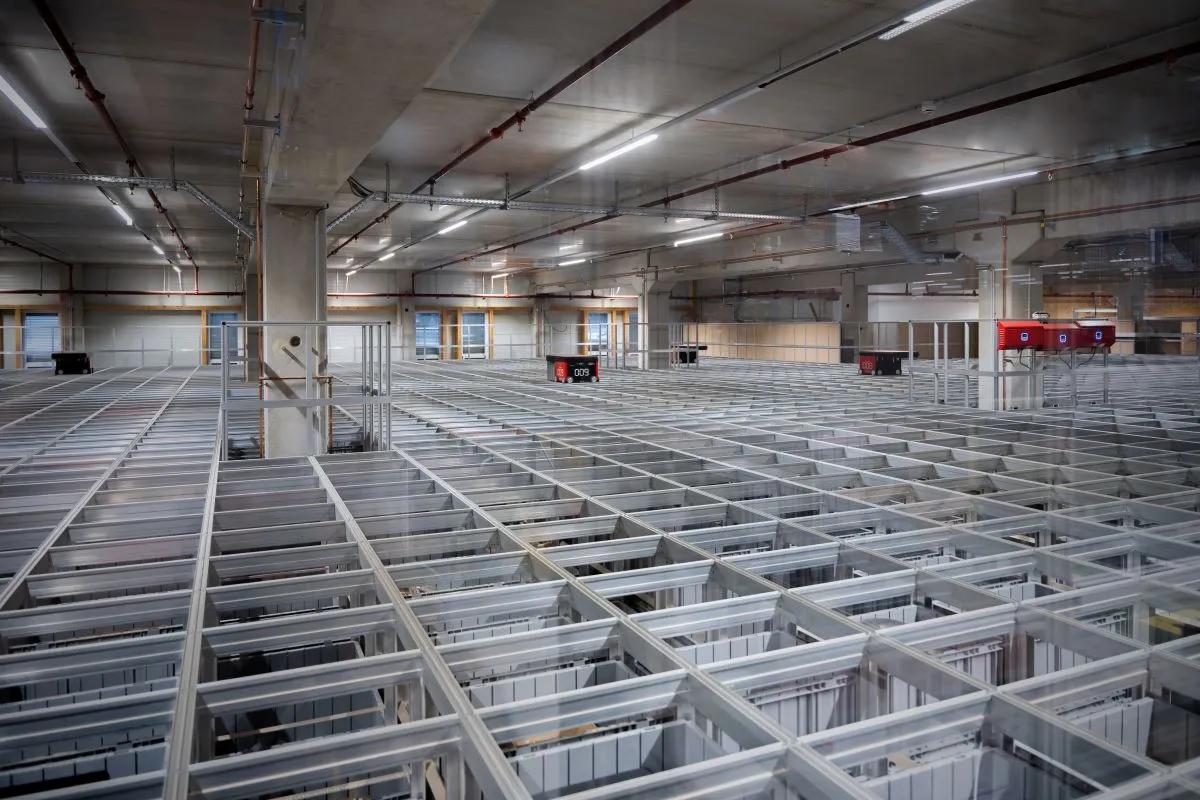
Facts & figures
AutoStore® warehouse | High-bay warehouse |
---|---|
|
|
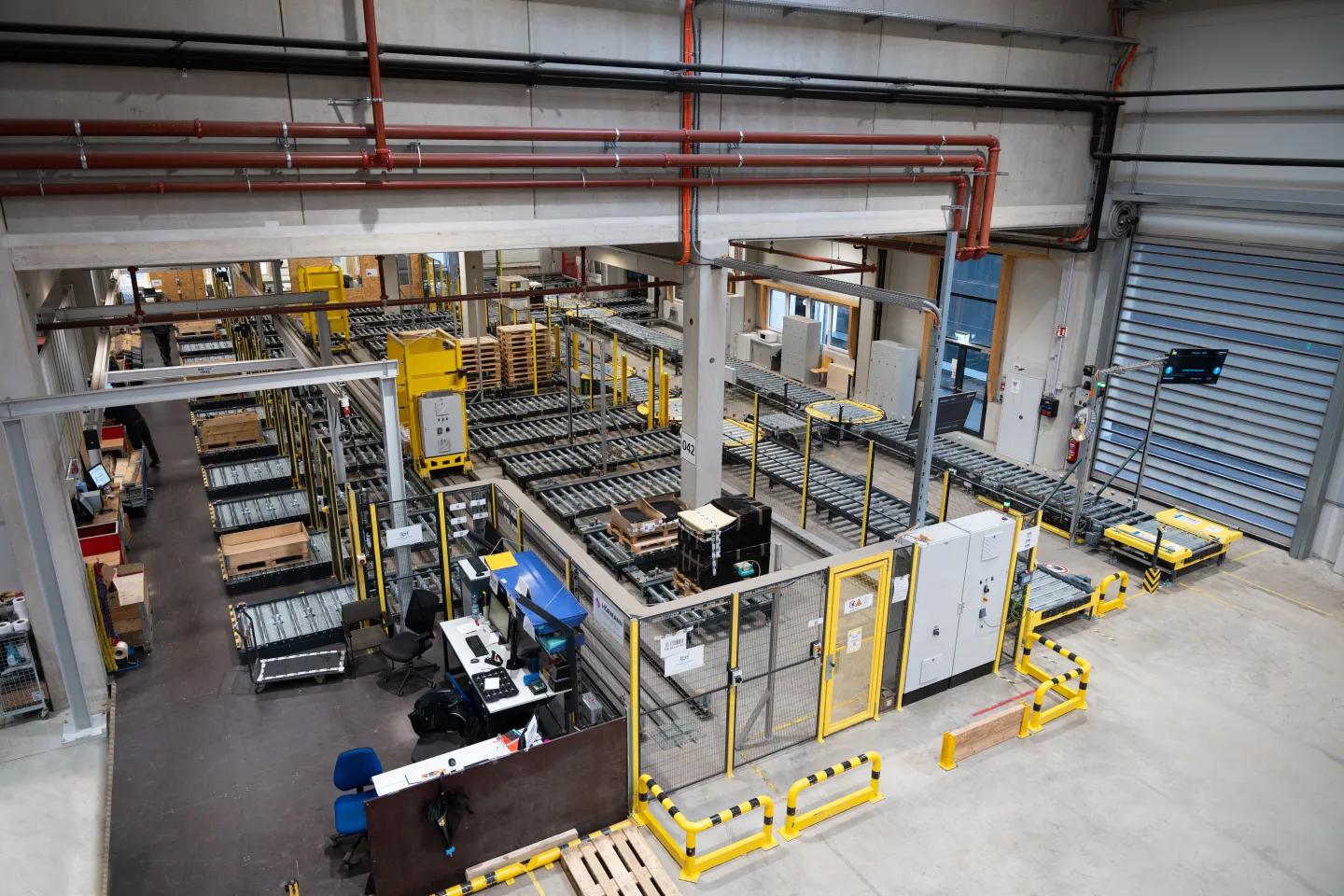
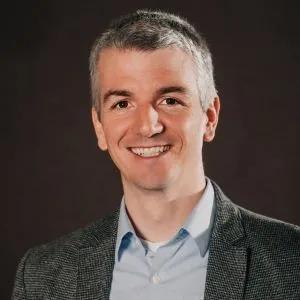
"The project was a complete success - we are already planning another plant with the multi-solution system from HÖRMANN Intralogistics"
Christoph Bacher
Managing Director, iDM Energiesysteme GmbH