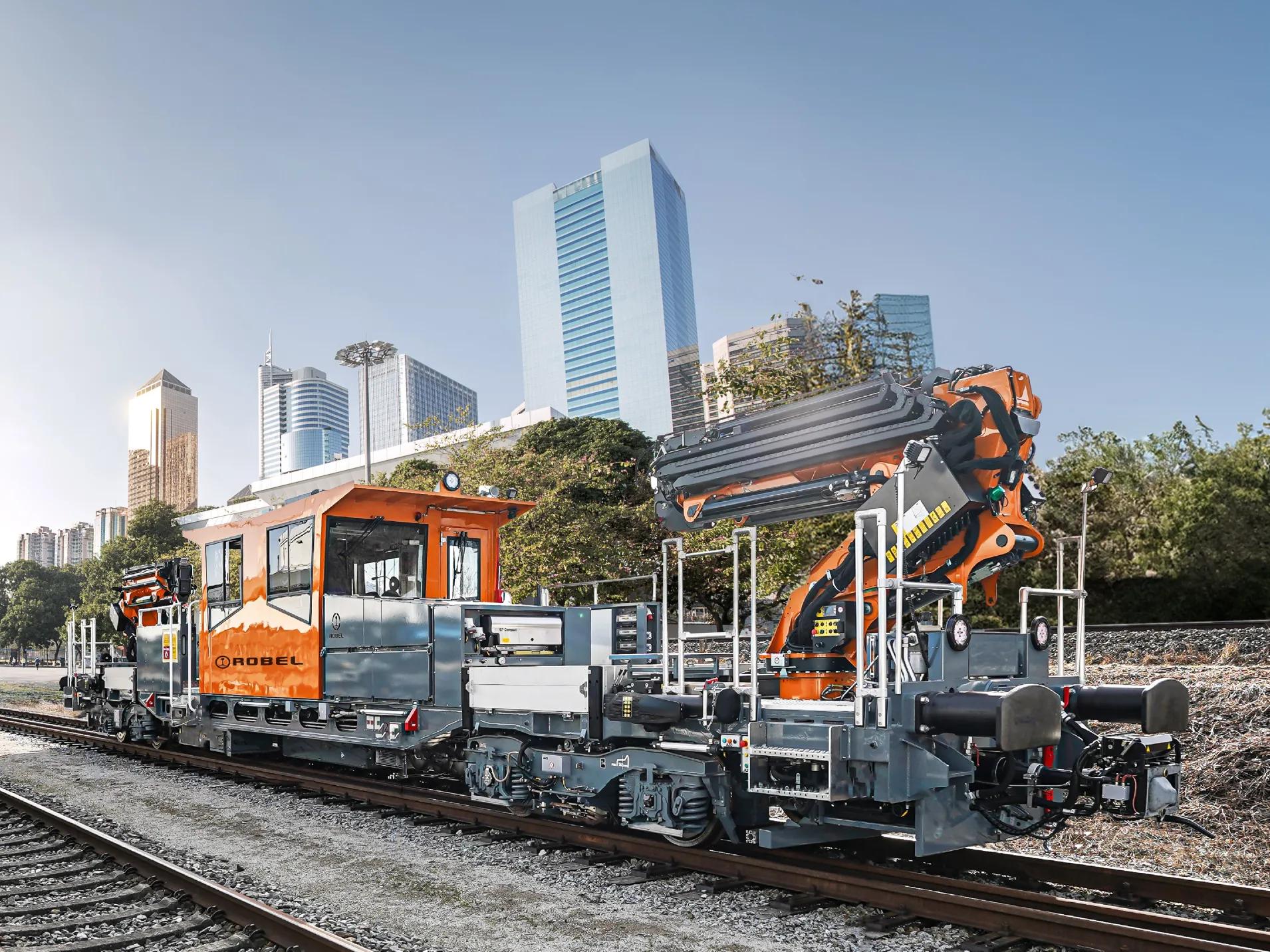
Digitization of the inventory storage system
AutoStore® system and centralized, cross-warehouse WMS at ROBEL Bahnbaumaschinen
AutoStore® system and cross-warehouse, central WMS at ROBEL Bahnbaumaschinen
ROBEL Bahnbaumaschinen GmbH in Freilassing has been developing, producing and supplying track-laying machines since 1901. Around 670 employees at the site provide modern, safe and economical machines, systems and services for all aspects of track construction.
In order to expand production capacities and the level of automation in Freilassing, the construction of a new logistics building and a centrally controlled, new material flow concept are planned. The heartbeat of the future-oriented intralogistics solution is a comprehensive warehouse management system that ensures optimal logistics operations and the digitalization of internal processes.
HÖRMANN Intralogistics came out on top with its overall concept comprising the AutoStore® system and WMS HiLIS and was awarded the implementation contract. With the proven, modular HiLIS warehouse management system, ROBEL's complex requirements can be mapped from the management and control of all warehouse areas, to goods receipt and quality assurance, through to production integration and shipping.
"With the new intralogistics concept, we will digitalize our warehouse and transport processes at the Freilassing site, integrate all heterogeneous warehouse areas and centrally control the connection to production via tugger train and forklift," says Christoph Bräuer, Head of Procurement & Logistics at ROBEL Bahnbaumaschinen GmbH, summarizing the project.
The structure of the new material flow processes and the new AutoStore® system
The plan includes a new logistics building in which, in addition to the AutoStore® small parts warehouse, a narrow-aisle warehouse will also be built and where incoming goods, quality control, consolidation, production supply, packaging and shipping will be handled. Small components are stored and picked in the AutoStore® system, which is directly linked to incoming goods and dispatch and is positioned on the first floor of the new warehouse building. Ten Red Line robots handle a total of 20,000 containers on the single-double grid, on which loading stations are installed at the side. The AutoStore® robots bring the required items just-in-time to one of the four bin lifts with swing ports on the first floor. Two further bin lifts are already planned. The new building also includes a narrow-aisle warehouse and a cantilever warehouse.
Consistent, digitalized and transparent warehouse and logistics processes thanks to HiLIS
In addition to standardizing and systemically supporting processes, the overarching goal of introducing a new WMS is to increase the level of automation, achieve significant optimizations through improved inventory transparency and increase efficiency through tailored logistics processes.
The HÖRMANN Intralogistics Warehouse Management System HiLIS will manage and control all material flow processes in future: From incoming goods to quality control, a total of six storage areas (including AutoStore®), consolidation - where goods from the storage areas are brought together on an order-related basis and made available for transportation synchronously -, production or service supply, packaging and shipping.
Andreas Wimmer, Head of IT Sales at HÖRMANN Intralogistics, confirms the WMS HiLIS as the heart of the new intralogistics solution: "HiLIS implements all asynchronous, existing and new manual and automated warehouse areas, including the AutoStore® system, and ensures that the requested goods arrive synchronously at the consolidation point."
The new intralogistics concept at ROBEL will go live at the end of 2024.
www.hoermann-intralogistics.com, May 2024
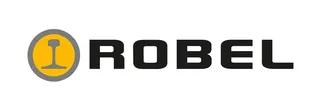