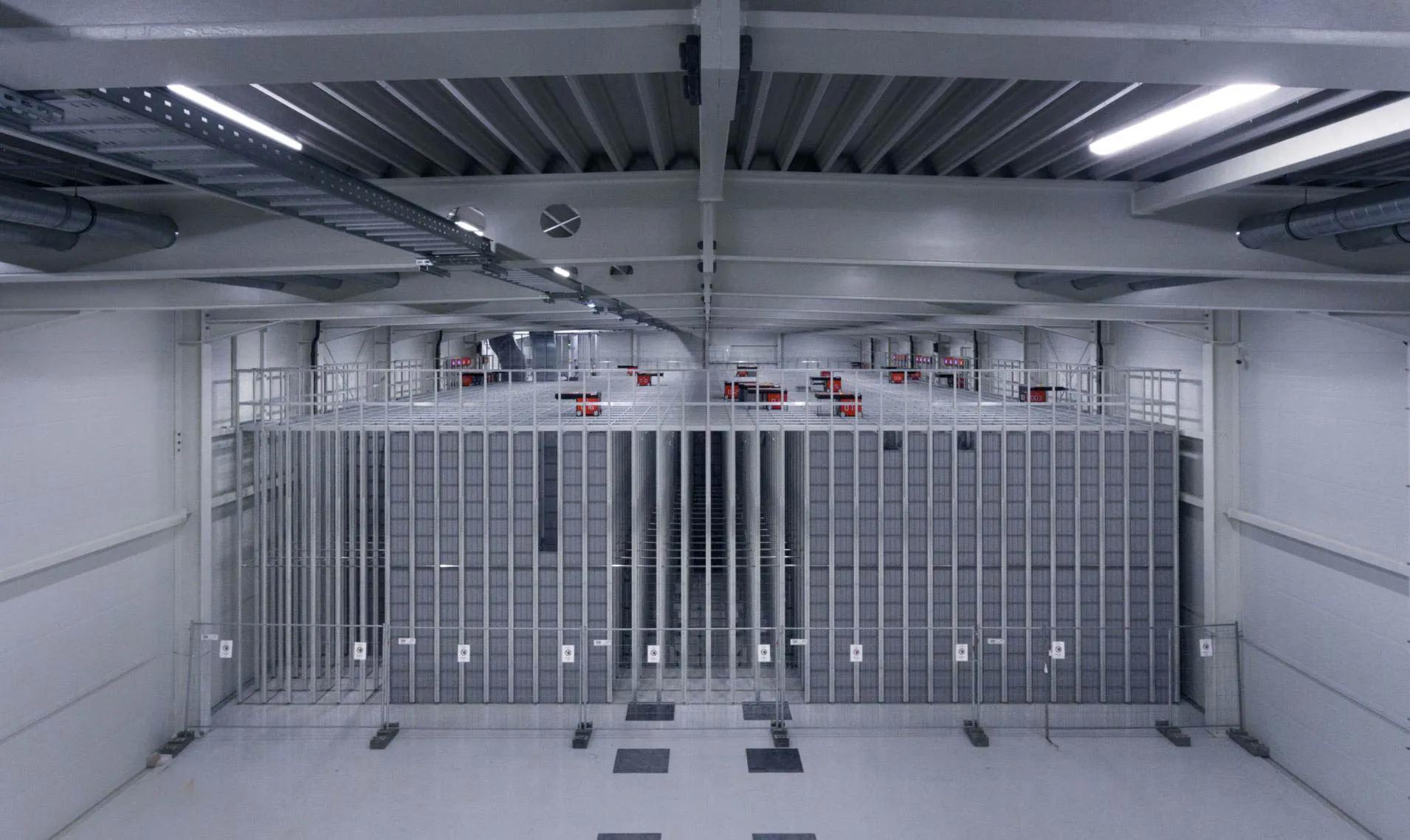
Reference SportOkay
AutoStore® small parts warehouse for SportOkay.com in Innsbruck
The e-commerce company Sport Okay GmbH, as a specialist for alpine clothing and sports equipment, offers more than 200 top brands in its online store www.sportokay.com. Unique worldwide is the 3D view, with which you can look at and examine your article in the online store! Tens of thousands of satisfied customers in Germany, Austria, Italy and another 15 countries are supplied by the sports specialists in the heart of the Alps. Due to the very positive development of the online store, SportOkay.com will invest in the construction of a new logistics center in Innsbruck, where a fully automated small parts storage system will be used as the central order picking system. With its AutoStore® concept Hörmann Logistik has convinced and received the order for the realization of the plant.
.
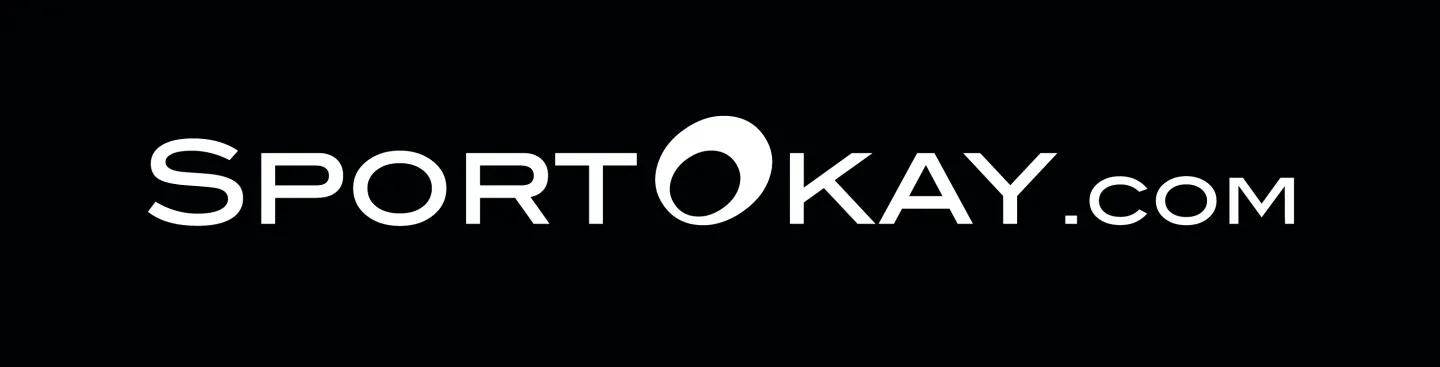
Concept
The new AutoStore® warehouse will be built on the second floor of a new building. On the first floor, workstations for incoming goods and order picking are provided.
For the customized design of the AutoStore system for SportOkay.com, Hörmann Logistik's planning included several plant simulations with original data in real time.
The customer requirements together with the simulation results led to a system configuration in two construction stages. In the first construction phase, 22 robots with 26,500 totes on 16 levels and associated 6 workstations with swing ports will enable around 168 putaways and returns as well as 4,000 picks per day and 400 picks per hour. In the second, final stage of expansion, the AutoStore® grid will be enlarged to approximately twice the width, so that 44 robots with approximately 55,000 bins and 12 workstations with swing ports will provide for approximately 336 putaways and returns as well as 8,000 picks per day and 800 picks per hour.
.
With the new, expandable AutoStore small parts warehouse, SportOkay.com's logistics center is perfectly equipped for the future, thanks in part to the personal and dedicated support of Hörmann Logistik.
Konrad Plankensteiner
Managing Director
The AutoStore system consists of an aluminum grid system with overall dimensions of 18.4 m x 36.9 m (79.2 m) x 5.4 m (L x W x H). In the grid system, stacks of 16 bins each stand directly on the hall floor. Mounted above the tote stacks is the track system (grid) on which the 22 (44) battery-powered autonomous robots move. The robots cooperatively pick up and re-sort bins and are responsible for the supply and disposal of the swing port workstations on the first floor. The maximum total weight of the 649 mm x 449 mm x 330 mm (L x W x H) bins is 35 kg with a net payload of around 30 kg. To safeguard the maximum weight, an overweight check takes place at the ports. The containers can be flexibly divided by dividers for the use of several items.
.
The workstations for storage, retrieval and picking of goods at SportOkay.com are located below the AutoStore® system on the first floor. The articles are brought to the goods receipt workstations on pallets or in cartons, unpacked there and stored in the system. Goods intended for picking are tendered to one of the outgoing goods workstations by the AutoStore® system, the employee removes the goods and places them in the shipping carton.
.
The AutoStore® small parts warehouse at SportOkay.com in Innsbruck went into operation in late summer 2018 .
.
Connection of the rack storage by SAFELOG AGVs
.
In the basement, large parts, such as skis, snowboards, poles, etc. are kept in shelves. Fixed storage spaces are assigned to the shelves and coded via RFID tags on the floor. This results in a shelf area with defined routes for the AGVs. Depending on the picking order, the mobile transport robots of the type SAFELOG AGV L1 pick up the shelves with the required items from the storage area. Via a console lifter, the AGV with the racking arrives directly in the picking zone and at the correct workstation. The racks are variably equipped with cantilever arms or adjustable shelves. After picking, the racks are brought back to their place by the AGV.
.
Even ready-picked orders are transported from the AutoStore picking stations by specially configured SAFELOG AGVs type S2 directly to the packaging machine.
.
Through this goods-to-person principle, the warehouse space could be used efficiently and the travel times of the employees could be reduced by approx. 80% during the picking activity. This significantly increases the picking rate.
.