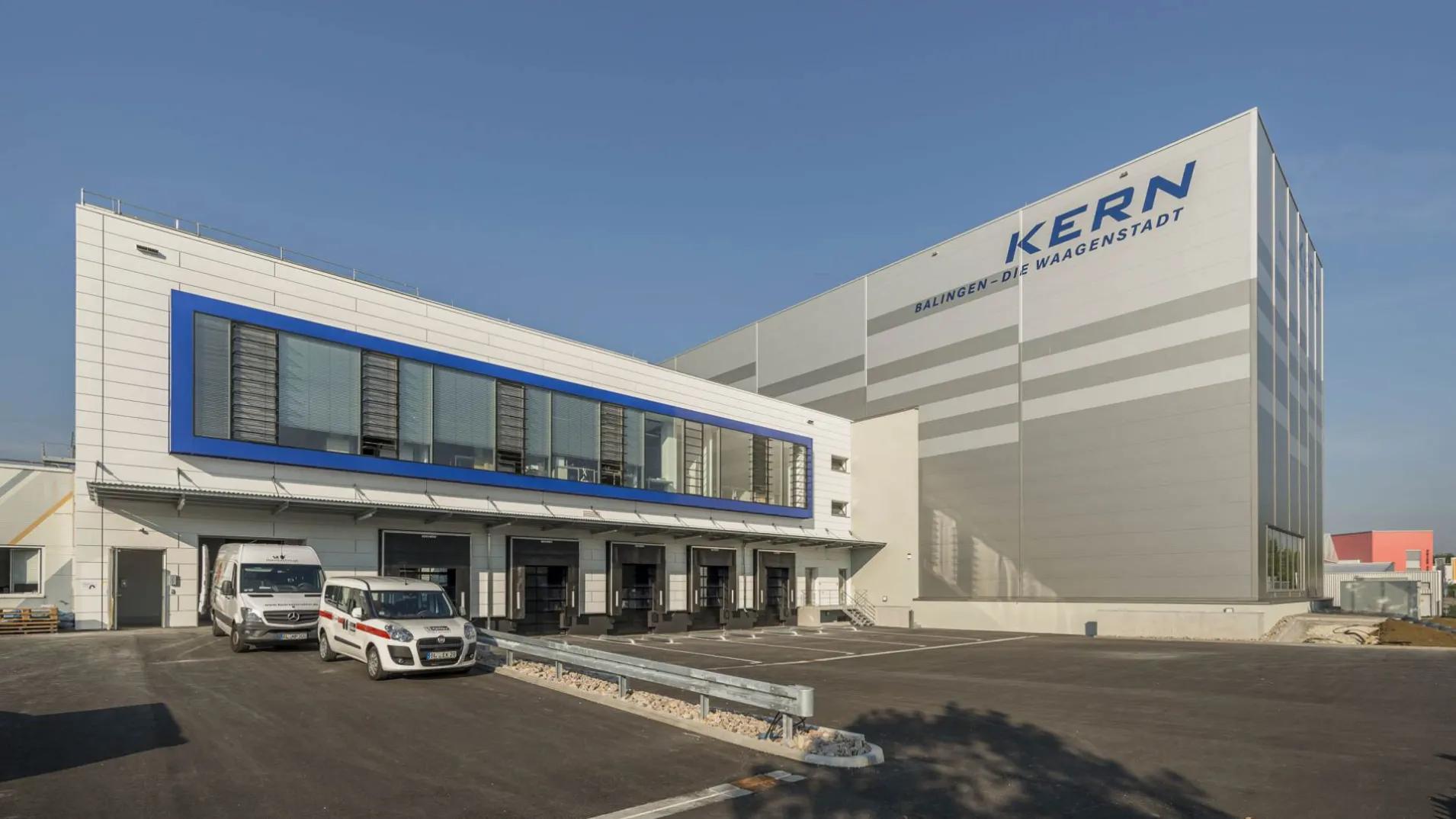
Reference iDM Energiesysteme GmbH
Multi-solution project comprising an automated high-bay warehouse and AutoStore System® for the new logistics center at iDM Energiesysteme GmbH in Matrei
Kern & Sohn GmbH is one of the largest suppliers of professional scales in Germany and is internationally known under the KERN brand. The product portfolio covers the entire spectrum of weighing technology, including integrated weighing solutions in conveyor and plant technology. In order to secure further growth and optimize material flow processes, PROTEMA Unternehmensberatung GmbH developed a new overall concept, which includes a new logistics and assembly concept as well as the construction of a new factory and logistics building. The automatic pallet high-bay warehouse and the automatic small parts warehouse with picking stations supplied HÖRMANN Logistik as general contractor.
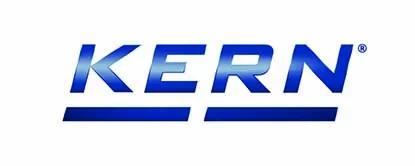
Concept
A special feature is the innovative concept in which cartons and small load carriers (KLT) of various sizes can be stored. This automated small parts warehouse (AS/RS) is integrated into the silo structure of the pallet high-bay warehouse and has the same height of 25 meters. This is made possible by the use of special storage and retrieval machines (SRM) in which only one drive drives both the chassis and the mast head via a toothed rack. With sophisticated gripping technology, the various cartons can be stored up to four deep.
Uniform large compartments are filled with up to 24 cartons in a volume-optimized manner. To prevent fire, both the single-aisle pallet high-bay warehouse and the double-aisle carton high-bay warehouse (AKL) are operated with an oxygen-reduced atmosphere. Cartons, KLTs and pallets are placed on the conveyor system at the goods receiving area. At the I-points, the WMS identifies the load units via barcode labels. The contours of cartons and KLTs are recorded on the conveyor system using a camera-based system. At this point, the WMS already decides how the load units are stored in the miniload.
The load units are immediately turned into the volume-optimized position. At several buffer lanes in front of the miniload, cartons of the same size classes are collected and stored as pairs or quadruples. The quadruple transport significantly reduces the number of AS/RS trips.
Customized warehouse management through HiLIS
HiLIS receives the delivery orders from the host computer. By passing them on early, HiLIS can couple orders of the same width class and thus also collect up to four cartons via the SRM and make them available at the delivery stub. They then pass through the airlock to the pick & pack stations. To enable the operator to work ergonomically, a scissor lift table lowers the pallets to working level. The operator removes the articles indicated by the terminal. Remaining quantities are put back into storage.
Warehouse management is handled by the HÖRMANN intra logistics system HiLIS, which communicates directly with the HOST. The three stacker cranes operate with the HiLIS Eco-Power Management System, which saves up to 25% of energy consumption through intelligent energy balancing. The HiLIS plant visualization system makes it possible to track and control all plant movements in real time and, if necessary, to change them by manual intervention.
Balingen is located in the Zollernalbkreis district, which is prone to earthquakes. To safeguard against this, an earthquake package was integrated into the system, which detects the possible shifting of cartons in the rack by sensor after an earthquake and realigns them.
Highlights
- Volume and throughput optimized warehouse strategies
- Direct connection of production & order picking
- Integration of seismic packages
- Fire prevention concept
- 1-aisle high-bay pallet warehouse
- 90.0 x 8.6 x 25.4 m (L x W x H)
- Storage capacity: 3,480
- Double-deep storage
- 1 automatic stacker crane with built-up telescopic fork
- Conveyor connection
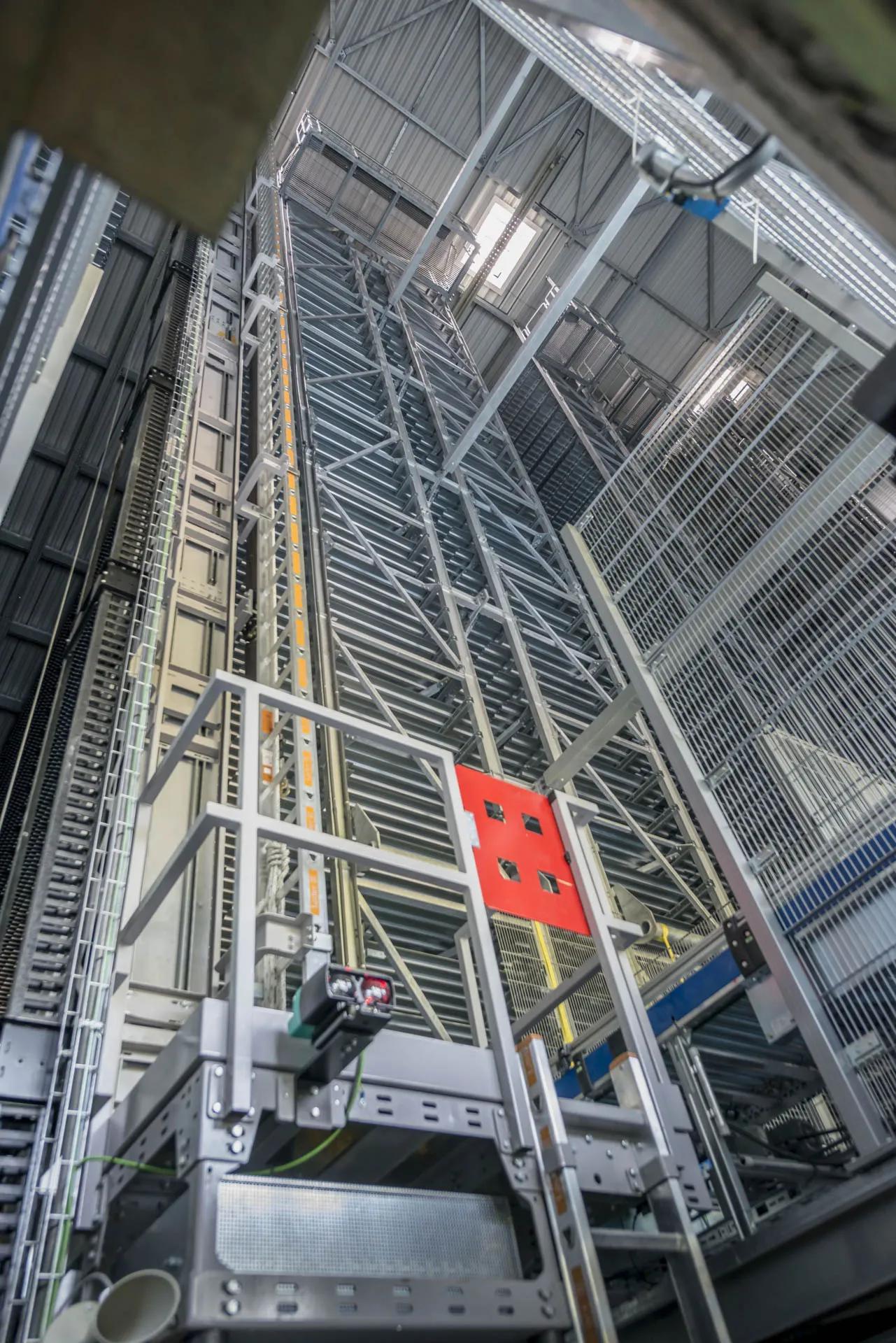
1-aisle pallet high bay warehouse
- 90.0 x 8.6 x 25.4 m (L x W x H)
- Storage capacity: 3,480
- Double-deep storage
- 1 automatic stacker crane with built-up telescopic fork
- Conveyor connection
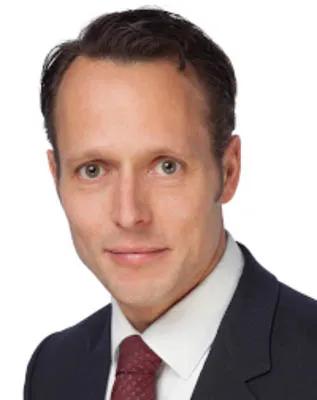
The new material flow concept ensures the greatest possible flexibility for our company, future growth as well as secure and transparent processes. During the implementation of this challenging project, we were able to rely on HÖRMANN Logistik as a professional and on-time partner at all times.
Albert Sauter
Managing Director, Kern & Sohn GmbH
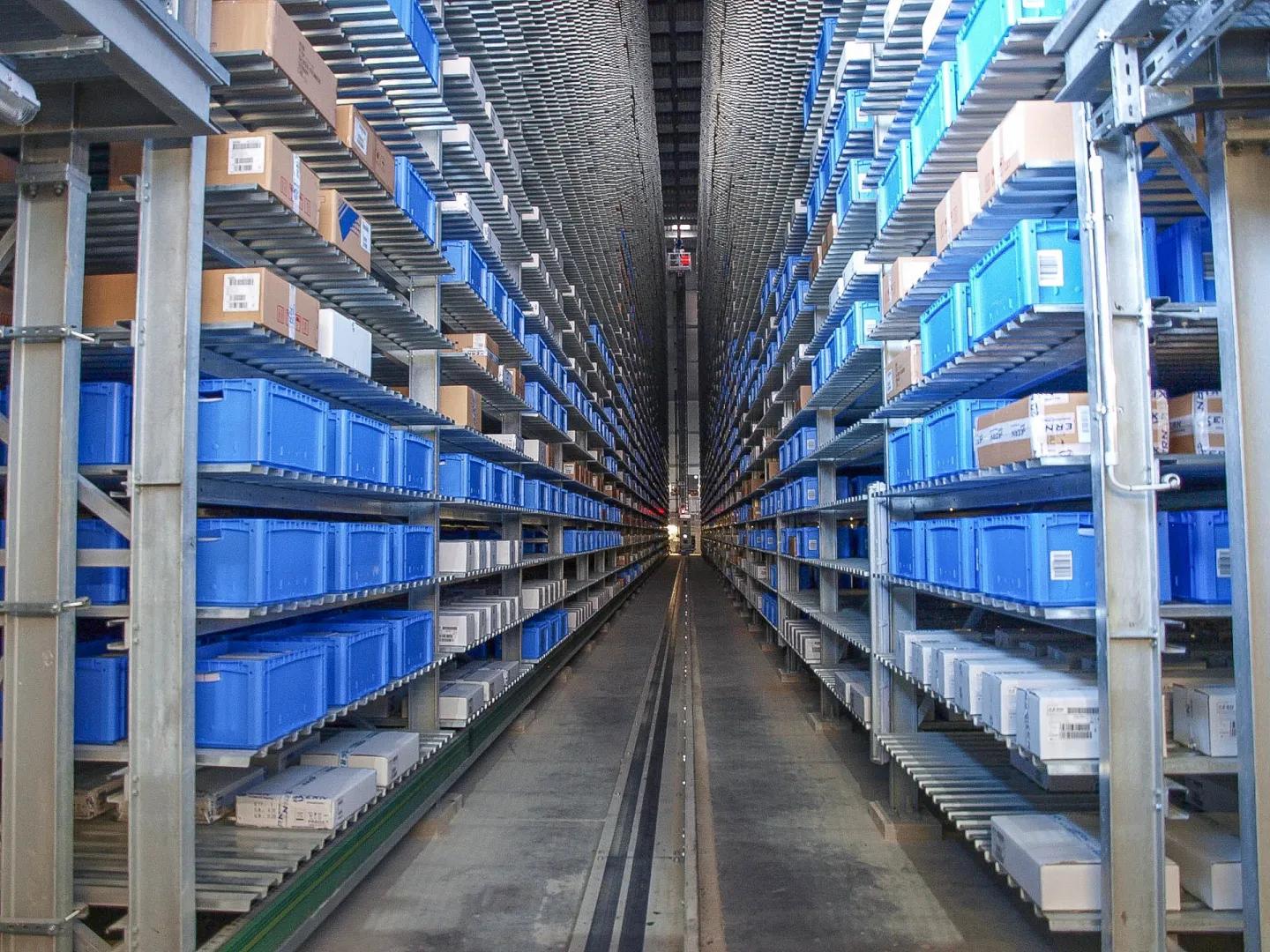
2-aisle AKL carton high bay warehouse
- 90.0 x 8.6 x 25.4 m (L x W x H)
- Storage capacity: up to 75,000 cartons and KLTs
- Storage 2 to 4 deep
- Storage of a wide range of carton sizes
- 2 automatic stacker cranes, each with a puller to hold up to 4 cartons
- Extensive conveyor technology
- HiLIS WMS