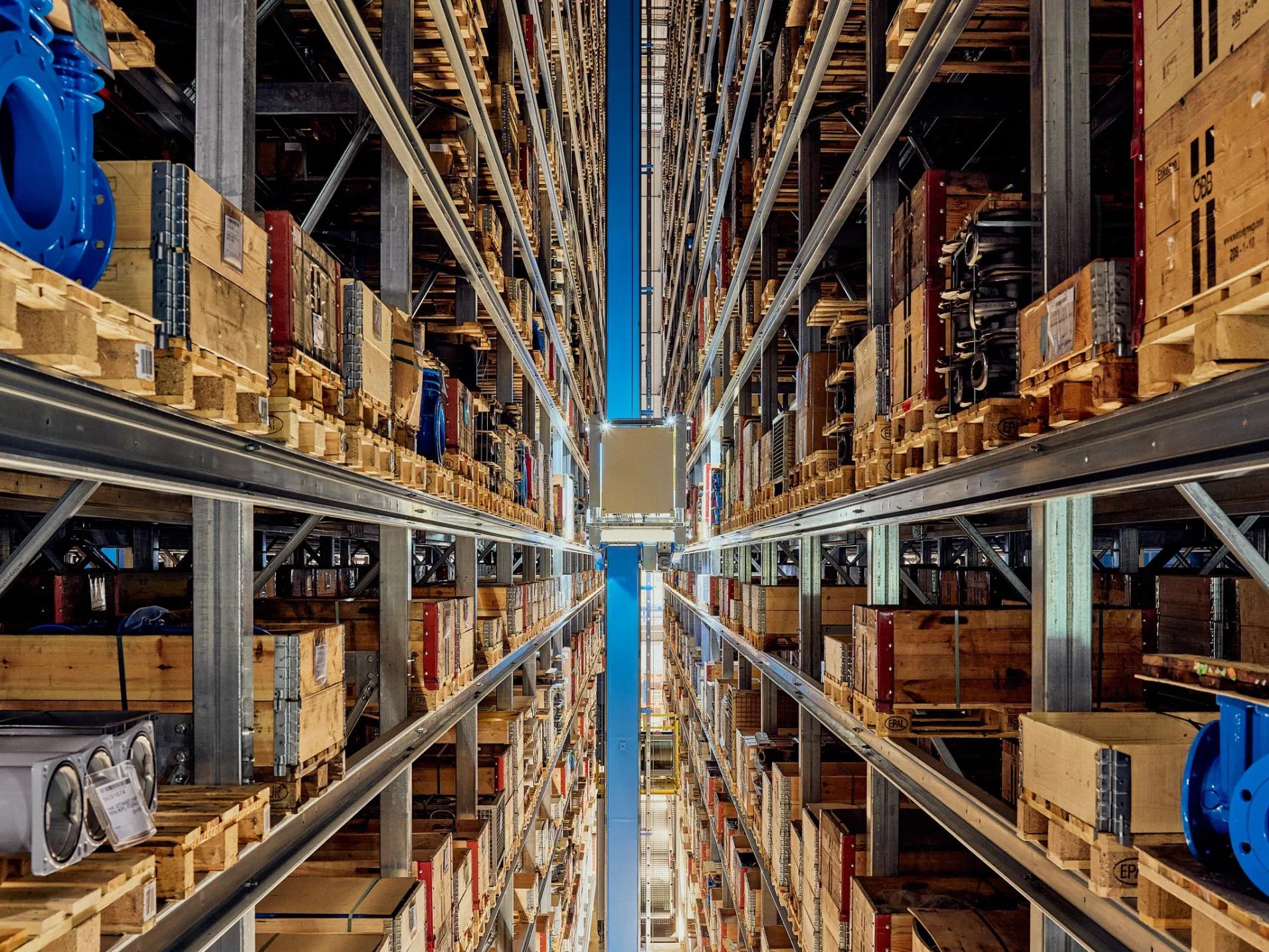
Automated high-bay warehouse for supply and storage of production at E. Hawle Armaturenwerke in Austria
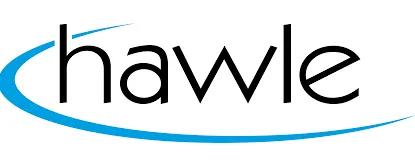
Automated high-bay warehouse for supply and storage of production at E. Hawle Armaturenwerke in Austria
The Hawle Austria Group produces and distributes heavy-duty valves worldwide. The products, which are designed for generations, are used in residential water management from the source to the house connection. The Hawle Austria Group includes 12 subsidiaries in Austria, the Czech Republic, Poland, Slovakia, Russia, Turkey, Italy, Great Britain and India.
A new logistics warehouse is built at the E. Hawle Armaturenwerke GmbH production site in Frankenmarkt, Upper Austria, reducing the previously rented external warehouse capacity as far as possible. Hörmann Logistik, as general contractor, is responsible for the delivery of the 5-aisle high-bay warehouse and the connecting conveyor technology.
Concept
In order to reduce the numerous rented external warehouses, minimize the resulting transport costs and create additional capacity in production, Hörmann Logistik was awarded to build an automatic high-bay warehouse. Unfinished and semi-finished parts are temporarily stored for production or for shipping dispatch.
The production connection is made directly from production the production area via a new, double-level conveyor system for pallets. In addition, a loading and unloading station is planned in the outer wall of the new logistics hall, which can be reached from the yard with
forklifts.
The 5-aisle high-bay warehouse is equipped with five aisle-bound storage and retrieval machines (SRM). These have telescopic forks for double-deep storage. Three-slot side-by-side storage is provided per rack compartment. The storage and retrieval conveyor sections of the
high-bay warehouse are connected to a loop conveyor line, extending into the logistics hall to pick up or drop off goods. All stacker cranes are equipped with a compartment fine positioning system that detects both the front and rear z-positions.
Goods receipt and shipping for different load carriers
At the goods receiving area, normal load units are fed onto three conveyor sections with weight and dimension control. Box pallets are only loaded on the middle conveyor section. There, the loading station is automatically fed with a wooden lower pallet onto which the pallet cage is placed.
The empty pallets required are kept in stacks at a buffer station and, if necessary, transported individually to the placement station.
Highlights
- 5-aisle high-bay warehouse 70 x 40 x 29 m (L x W x H)
- 5 aisle-bound S/R machines in single mast design with telescopic forks for double-deep storage
- 32 pallets per hour in and out of storage per S/R machine
- Connecting pallet conveyor system
- Powercaps energy storage
- Return of stacker crane energy into the cycle
- Consumption with 5 S/R machines approx. 230,000 KWh/year - reduction with Powercap app. 40%.
- Mains pre-fuse with 35A (6mm²) instead of >100A (35mm²)
- Fire protection and high-speed doors
- Controls technology with HOST interface
- Plant visualization