High degree of automation
Hörmann Intralogistics receives order for AutoStore system with innovative robot cell

Hörmann Intralogistics has received an order from Siemens AG in Rastatt to implement an AutoStore system with an integrated robot cell. This combination enables fully automated incoming goods of small load carriers into an AutoStore grid for the first time. The project sets new standards in the automation of intralogistics processes and offers a well thought-out concept for high speed.
Efficient combination of AutoStore and robotics The project comprises the planning and realization of a modern AutoStore system with the following key data:
- Single double grid with a capacity of approx. 23.000 containers
- 8 "Red Line" robots with 8 charging stations
- 6 conveyor ports for order picking and goods receipt
- 10 kN supports and aerosol capsules
- Goods issue capacity for production: 100 retrievals per hour at two workstations
- Outgoing goods capacity for customer order picking: 60 retrievals per hour at two workstations
To fully automate incoming goods, a specially developed robot system with "bin-in-bin, bin-out-bin" technology is used. A Kuka robot, equipped with a special gripper and integrated vision technology, takes over the storage and retrieval into the AutoStore Conveyer Port
The robot system takes filled containers from pallets or trollies, which were brought into stations fully automatically using AGVs (provided by Siemens). Barcode readers and weight monitoring check whether they may be stored, i.o containers are brought into the conveyor port, n.i.o containers are discharged via an n.i.o space. Access is secured via two airlocks with light grids, radar sensors and roller shutters. Control of the system and synchronization of the processes with SAP EWM enable a seamless process.
The facts of the innovative bin-in-bin, bin-out-bin robot cell:
- A robotic arm accepts the small load carriers (SLCs), which are also delivered fully automatically by AGILOX ONE and ODM, and automatically feeds them into the AutoStore grid.
- 55 storage units per hour at one workstation
- Empty small load carriers are automatically removed from the AutoStore containers.
- With the help of modern 3D vision technology, the robot cell can recognize and handle four different KLT types.
- The safety areas are monitored using INXPECT radar technology.
- The entire solution is integrated into the existing SAP EWM system
Comments on the project
Jonas Wilhelm, Project Manager Logistics at Siemens about the project: "With the new combined solution, we are creating end-to-end automation in our warehouse logistics, which not only speeds up processes, but also lays the foundation for a future-oriented material flow strategy. We are looking forward to working with Hörmann Intralogistics."
"The combination of AutoStore with a robot cell for fully automated incoming goods is incredibly exciting for us," explains Sebastian Behrens, Project Manager New Technologies at Hörmann Intralogistics. "The KLT gripping concept and the integration of the robot into the overall system were particularly challenging. We are delighted to be able to implement the pioneering concept together with the Siemens project team and ensure even more efficient processes."
The implementation phase will begin in early 2025 with completion planned for August 2025.
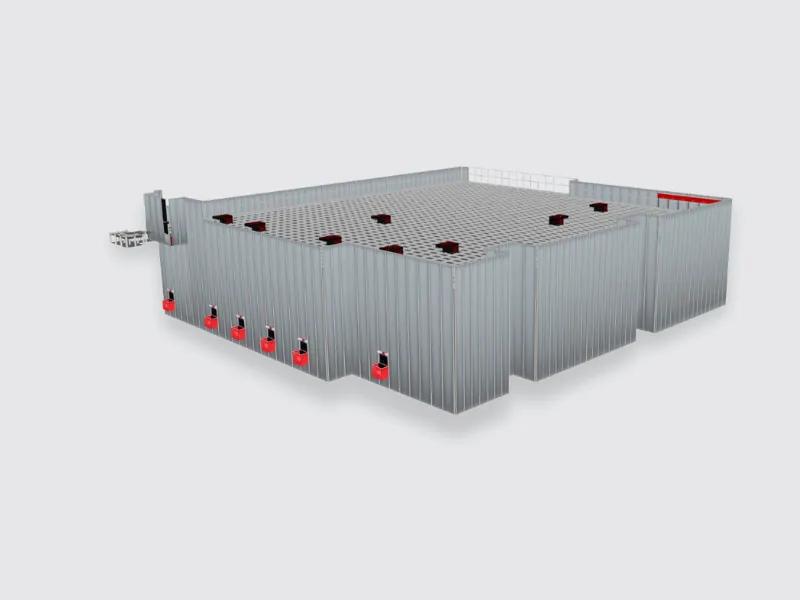
