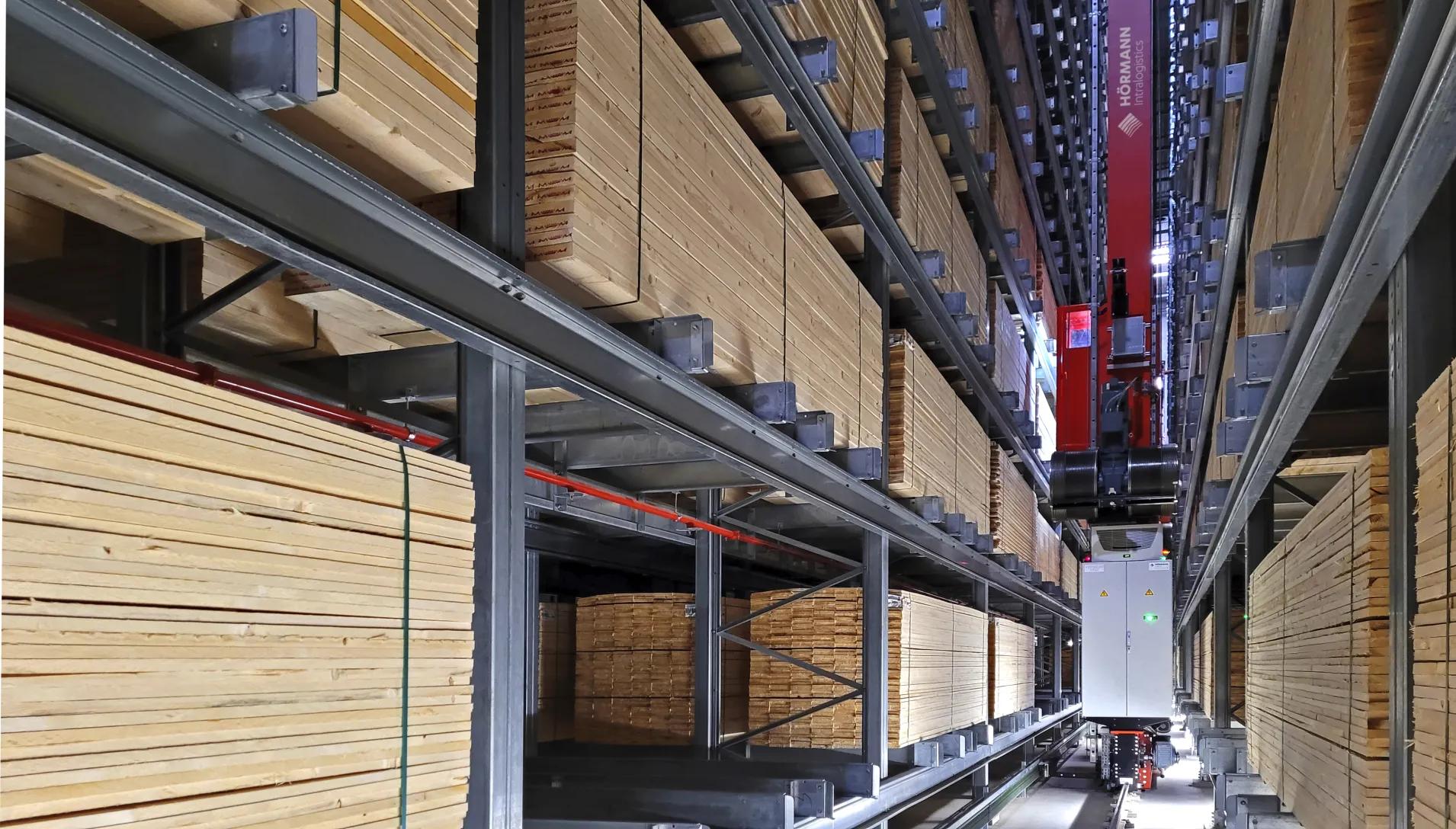
New standard for timber logistics
Successful handover: Automated high-bay warehouse for Mayr-Melnhof Holz in Leoben
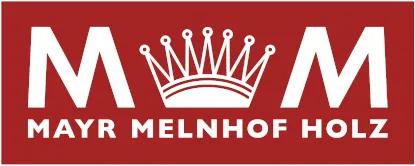
HÖRMANN Intralogistics is pleased to announce the successful completion of the state-of-the-art high-bay warehouse for the Mayr-Melnhof Holz Group in Leoben. The major project sets a new standard for timber logistics with a high degree of automation including truck loading.
Mayr-Melnhof Holz Holding AG, headquartered in Leoben, was founded in 1850 and is one of Europe's leading companies in the sawn timber and wood processing sectors. Around 1,630 people are employed at nine locations. As a driving force in the timber industry, market leader in the glulam segment and a driving force in the advance in the production of cross-laminated timber, the building and construction material of the future, the long-established company relies on advanced, efficient plant solutions for the expansion and modernization of its plants.
A modern, future-oriented intralogistics solution has been created at the sawmill site in Leoben, which is also home to the group's headquarters, with an automated, 3-aisle high-bay warehouse and the connecting conveyor technology for order-related sequencing, packaging, stacking and tour-oriented provision with subsequent truck loading in the loading hall, which is being implemented in a pioneering, semi-automated process for the first time. Based on the functional specifications of logistics planner Xvise from Lauterbach (Austria), HÖRMANN Intralogistics developed a convincing concept for Mayr-Melnhof Holz and was awarded the general contractor contract for the implementation of this special intralogistics solution.
Facts
In this pioneering showcase project for Mayr-Melnhof Holz, HÖRMANN Intralogistics' scope of delivery included the steel racking construction, the roof and wall cladding, storage and retrieval machines, special conveyor technology from HÖRMANN Klatt Conveyors, fire protection doors, high-speed doors, gantry robots for placing squared timber underneath or in between, parcel stackers, strapping machines, automatic saws incl. Chipper, labeller, inkjet labelling, loading crane and the HiLIS WMS, as well as the PLC system control including system visualization.
Pallet- High-bay warehouse |
Conveyor technology & packaging |
---|---|
|
|
Stephan Dorn, Project Manager Realization at HÖRMANN Intralogistics, comments:
"This project was an exciting challenge, which we accepted with enthusiasm but also a great deal of respect. The close collaboration with Mayr-Melnhof Holz enabled us to develop a tailor-made solution that is both efficient and forward-looking. We are proud of the result and the sustainable improvements it brings for our customer."
The concept
The high-bay warehouse (HRL) and the logistics and loading hall were built on an existing site next to the existing production halls of the sawmill and directly adjacent to the newly constructed high-performance resorting and planing plant and the new high-tech cross-laminated timber plant. The conveyor system transports the timber packages from the sorting and planing mill to the high-bay warehouse. In the 3-aisle high-bay warehouse, the timber packages are temporarily stored and, depending on the order, either loaded onto trucks for internal and external customers or transferred to the cross-laminated timber plant for further processing. For truck loading, the sawn timber packages are put together in the correct sequence and route, packed and stacked if required. A distribution wagon then transports the heavy-duty packages to the respective staging lane next to trailers in the loading hall.
Stefan Hierzenberger, Head of Group Logistics at Mayr-Melnhof Holz, adds:
"The all-in-one concept from HÖRMANN Intralogistics has enabled us to revolutionize our logistics processes. The designed software control, sensor technology, innovative conveyor technology and seamless integration into our existing processes increase our efficiency and competitiveness. We are excited about the possibilities offered by this new system."
Flexible and gentle material flow with innovative modular belt conveyor technology
The load units are bundled packages of sawn timber measuring up to 5.2 m long, 1.27 m wide and 1.30 m high and weighing up to 3,200 kg. HÖRMANN Intralogistics uses innovative modular belt conveyor technology made of high-quality, lubricant-free plastic with integrated transport rollers to transport the packages safely and gently on the conveyor system. The packages can be transported on these with or without squared timber. All packages undergo a weight and contour check when they are transferred from the sorting and planing mill.
On arrival from the sorting and planing mill, the timber packages are automatically picked up, checked and transported to the pre-zone of the high-bay warehouse. At the storage infeed, packages up to 4.2 m / 2.7 t are positioned centrally to the storage and retrieval machine (SRM) according to their lengths and transferred by the SRM to 3-deep rack storage locations.
Order-related sequencing and gantry robot station for stacks of 3 and 4 parcels
The timber packages are then retrieved in exact sequence and to the exact route. During this process step, there are further sorting options directly on the conveyor system. For the most part, the packages are wrapped fully automatically at the customer's request, underlaid with squared timber by a robot and strapped. After automatic labeling, the parcels are stacked.
This takes place in the hall pre-zone, where up to four parcels can be put together by a straddle stacker to form a lift for truck loading. Two parcels next to each other and two parcels on top of each other form this lift.
In the high-bay warehouse's storage and retrieval zone, retrieval slots have also been included in every aisle. Packages of sawn timber are retrieved here and fed to the cross-laminated timber plant via a distribution trolley.
Intelligent intralogistics strategies with the warehouse management system HiLIS
Warehouse management, system control and system visualization are carried out with the tried-and-tested HÖRMANN Intralogistics Warehouse Management System HiLIS, which communicates with the customer system via an interface. With 24/7 operating times, HiLIS continuously receives retrieval and putaway orders for the items to be loaded via an interface from the on-site HOST.
Eberhard Keppler, Sales Project Manager at HÖRMANN Intralogistics summarizes:
"Our task was to bring the material flows planned by Xvise to life with precise detail work and innovative technology. The realization of this project shows the incredible automation possibilities even for heavy load packages with high throughput. We would like to thank Mayr-Melnhof Holz for their trust and excellent cooperation. Together, we have set a new standard and look forward to future projects."
Installation started in October 2021, commissioning in 2023 and handover in 2024.