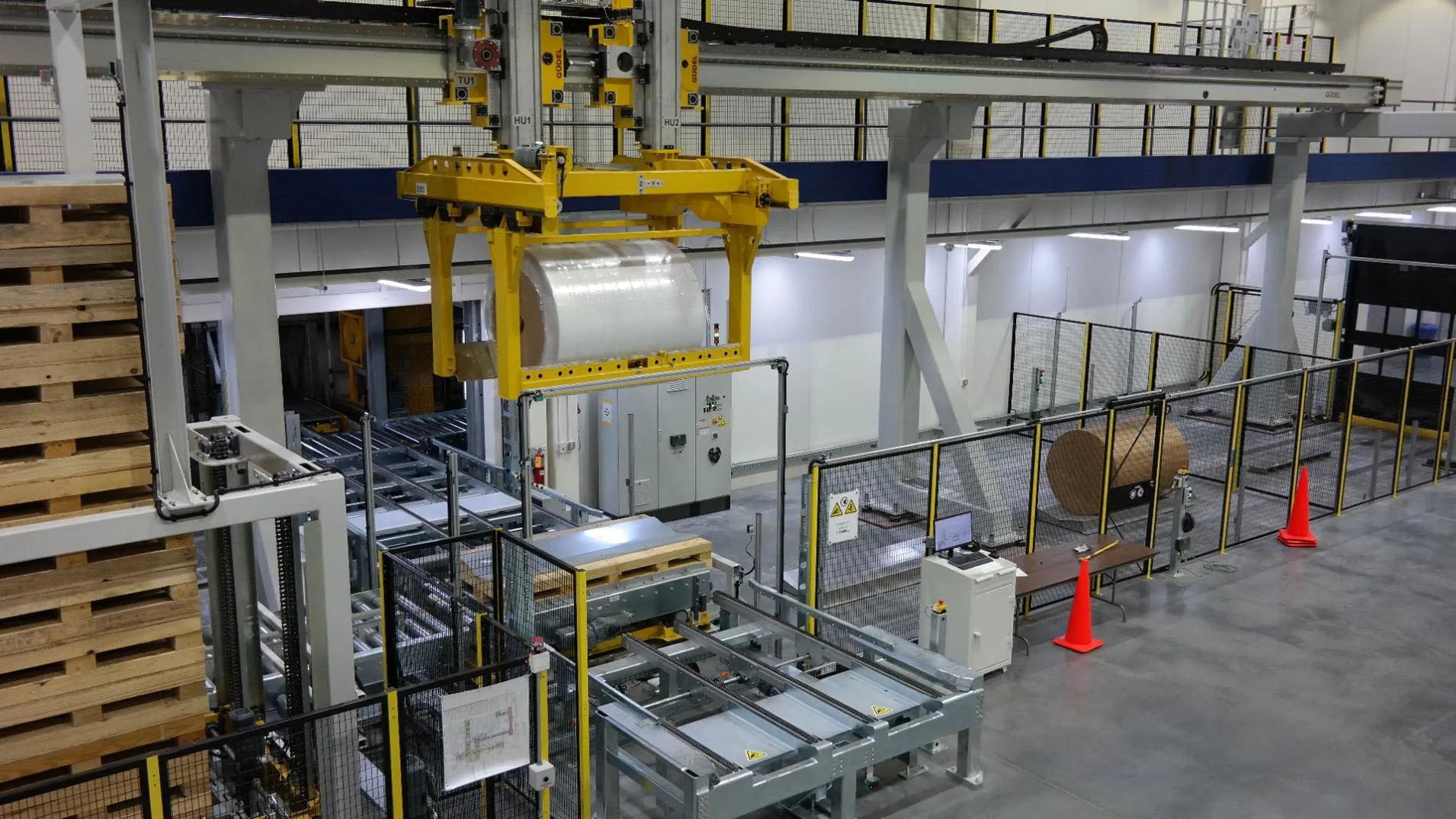
Reference DS Smith
Automated high-bay warehouse for corrugated board at DS Smith in France
Green Bay Packaging Inc. specializes in custom corrugated packaging, folding cartons and self-adhesive labels. With its philosophy of producing creative solutions tailored to customer requirements, the Green Bay Wisconsin company is a premium supplier in the USA. More than 3,000 employees work at locations in 15 U.S. states as well as Mexico. As part of a plant expansion at Green Bay's Labelstock Division in Wisconsin, a new high-bay warehouse for paper rolls and shippable palletized goods was built. It is directly connected to the existing coating and cutting lines as well as to the newly created production areas by means of automated guided vehicles (AGV). HÖRMANN Logistik realized the new, imposing high-bay warehouse including the connecting conveyor and handling technology and two different AGV systems as a general contractor.
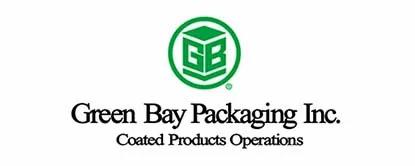
Concept
The special challenges of the two-aisle channel warehouse were the transport and handling of a wide variety of load units with weights of up to 5 tons. With several innovative developments, such as the different roller manipulators, slave board lowering devices, special AGVs with mandrel pick-up and cross-distribution wagons with powercap technology, HÖRMANN Logistik met all project requirements. This also includes the fully flexible storage and retrieval strategies with three stacker cranes. Paper rolls as well as different types of pallets with finished goods can be stored in each storage channel. In this context, one aisle of the high-bay warehouse (HRL) is equipped with two storage and retrieval machines (SRMs) on one track and one aisle with one SRM.
The stacker cranes are each equipped with two channel trucks that can extend individually (for smaller pallets) or together (for system pallets for heavy rolls). The middle rack unit can be served from both aisles, ensuring a redundant supply of rolls to production. The shelving slices are 2-deep, 4-deep or 6-deep in order to respond flexibly to different article quantities. The widths
of the storage channels vary between 1,000 mm and 2,200 mm for better space utilization. All storage and retrieval machines are equipped with self-learning fine compartment positioning, which allows the channels to be approached with millimeter precision.
In goods receiving, the raw material rolls are placed on the system pallet with a line gantry. In the process, the roll is measured, matched with the notified data, transported to the HRL and stored. When production needs raw material, it requests a selection of rolls via the HÖRMANN intra Logistics System HiLIS, from which HiLIS determines the one that is most easily and quickly accessible for the SRMs. In this way, stock transfers can be avoided. After the SRM has retrieved the roll specified by HiLIS, it is taken to another portal via conveyor technology.
This removes it from the system pallet and sets the roll down for an Automated Guided Vehicle (AGV). The AGV then transports the roll directly to the skate of the unwinder in production. The return journey of the finished coated rolls to the warehouse takes place in reverse order. The HiLIS WMS manages and controls all material flow processes and communicates via interface with the Green Bay HOST. The HiLIS visualization ensures permanent transparency and fast fault diagnosis in the event of a malfunction.
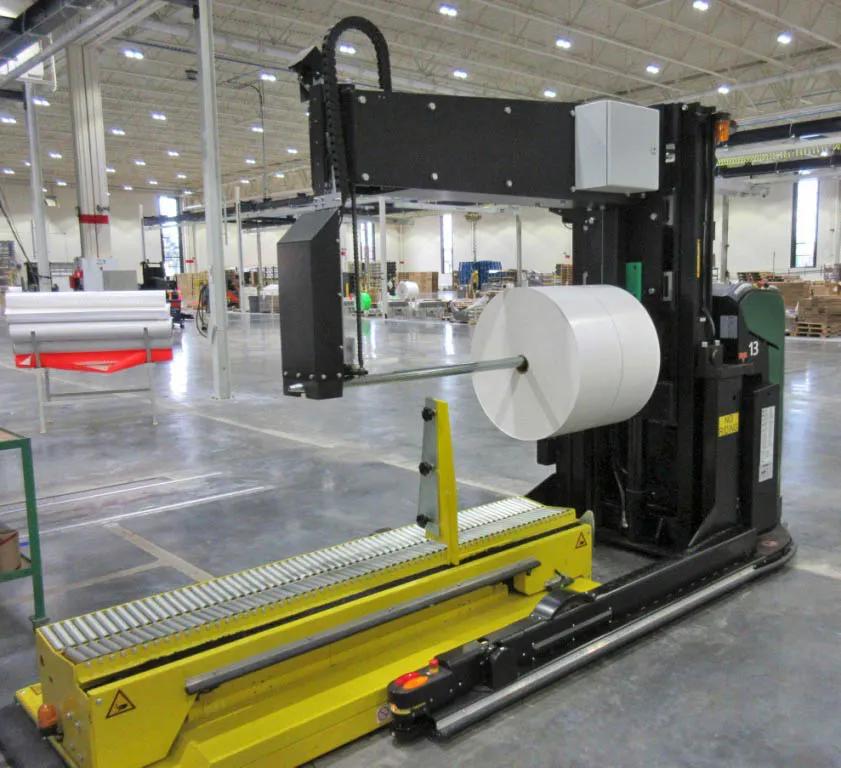
Flexible interfaces and innovative techniques
The HiLIS warehouse management system not only coordinates material movements between the warehouse and production. A special interface between HiLIS, AGV, production machines and conveyor technology allows roll and other production data to be carried along in parallel with physical transport.
Since the load handling device required for automatic transport was not available on the market, HÖRMANN Logistik developed a special solution in cooperation with the manufacturer. This innovative mandrel AGV is able to pick up a set of cut rolls of 1,400 mm roll width and 2 tons weight directly from the slitter rewinder and deliver them fully automatically to many different pick-up points in the packaging. In this way, slitting and packaging are decoupled in terms of time without multiple handling.
When connecting the packing area to the warehouse, the floor-level transport crosses a main traffic route. The specially designed distribution carts are controlled via WLAN data link and receive electrical energy from PowerCaps (capacitors). Since the PowerCaps only need a few seconds for a charge, they can be loaded when the pallet is handed over without any waiting time. In addition, the capacitor blocks are maintenance-free and have a long service life.
Highlights
- 2-aisle high-bay warehouse in silo design: 176 x 26 x 25 m (L x W x H)
- Storage double deep to 6 deep
- Mixed storage of paper rolls and finished goods on pallets
- Storage capacity: 12,800 pallets or 6,370 rolls
- 3 automatic stacker cranes (aisle-bound) with two channel trucks each
- 3 automatic roll handling gantries, two each fully redundant
- 4 AGVs for horizontal roll handling
- 3 AGVs with special pick-up (mandrel) for cut customer rolls
- Distribution truck for crossing forklift traffic routes with powercap technology
- HiLIS WMS
- Just-in-time supply of production
In order to remain a viable option in our marketplace, we looked for means to increase speed and throughput, handle greater roll weights, maximize quality and minimize waste. HÖRMANN Logistik provided the internal expertise and a network of capable suppliers to enable us to realize a highly customized and efficient system.
Green Bay
Project Team