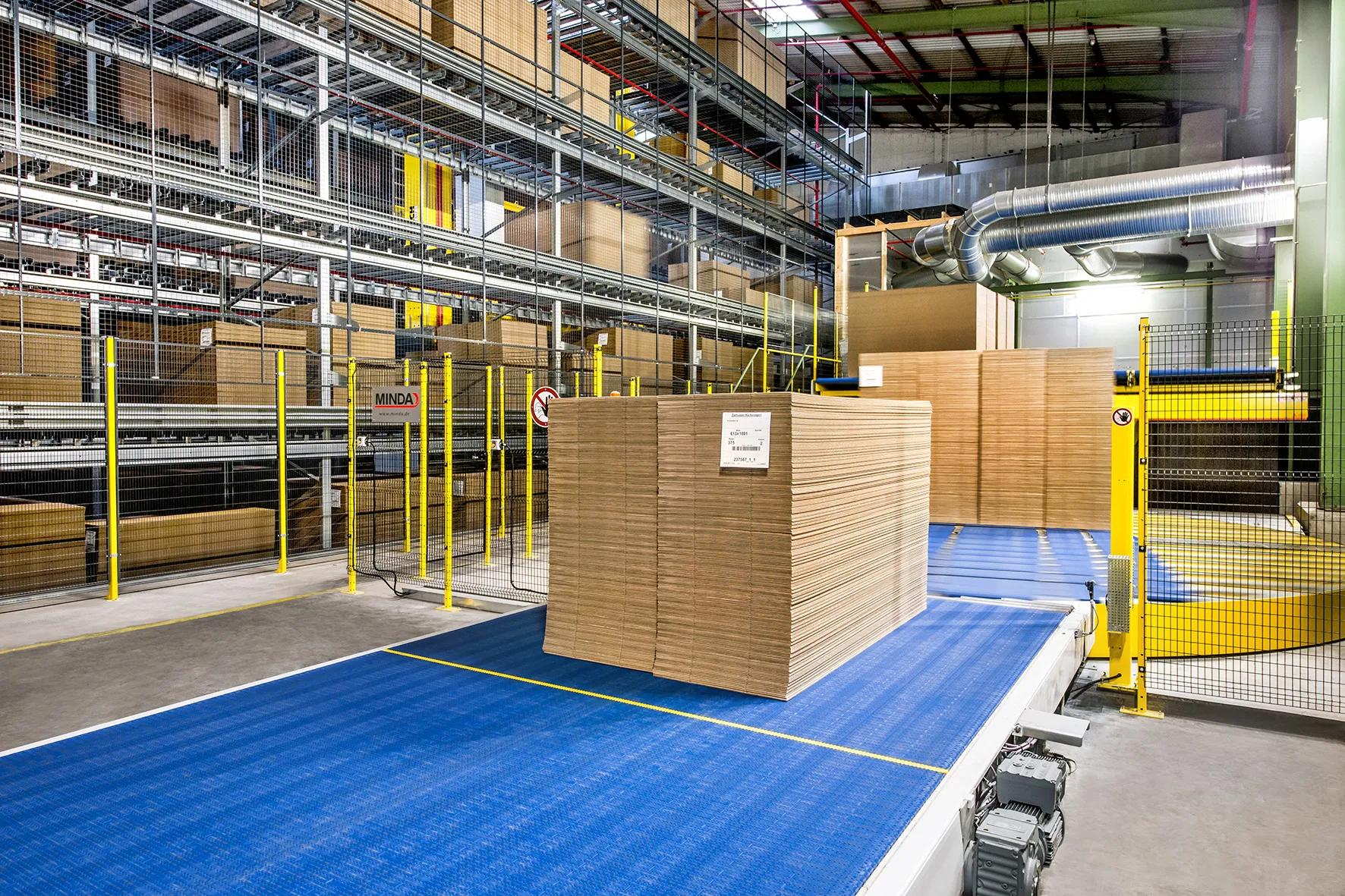
Highly flexible warehouse concept with finished goods and format goods high-bay warehouse at Zerhusen
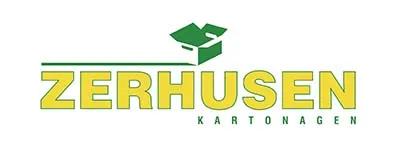
Zerhusen Kartonagen GmbH specializes in the production of corrugated board packaging as well as customer-specific special packaging. At the Damme site, approximately 440 employees process around 200 million square meters of corrugated board per year, which are manufactured from 100,000 tons of paper on the company's own corrugator. Folding boxes, erecting boxes, blanks or multi-component packaging are produced. The strong growth in production at Zerhusen made it necessary to increase storage capacity. HÖRMANN Logistik developed a highly flexible logistics concept and, as general contractor, implemented the three-aisle high-bay warehouse (HRL 1), its extension and expansion (HRL 2), a two-aisle format goods warehouse, and in each case the connecting conveyor technology.
Concept
All components at Zerhusen are based on the HÖRMANN logistics warehouse concept, which was specially developed for the specific properties of corrugated board. This is tailor-made for the low weight and high volume of corrugated board. The relatively low weight allows the simultaneous transport of several load units during storage and retrieval. With one storage or retrieval cycle of a storage and retrieval machine (SRM), up to three identical pallets can be stored or retrieved. The number of load units transported simultaneously depends on the size of the packages. For this purpose, each load unit is measured to the millimeter after the contour check at the end of production.
Innovative sorter concept
The largest packages are stored and retrieved individually, medium sizes as pairs and small load units as triples. An innovative sorter almost merges the same pallet types into pairs or triples to enable highly efficient use of the line capacity. The load units are buffered in several buffer lanes of the sorter until the pair or triple can be completed. At the storage spur of the high-bay warehouse, the load units are precisely aligned using a sophisticated technique and then transferred to the SRMs. These control the storage compartment with pinpoint accuracy by means of compartment fine positioning. Depending on their size, the pallets are stored 1 to 3 deep. All SRMs operate with the HiLIS Eco power management system, which saves up to 25% of energy consumption through intelligent energy balancing.
Highlights
Construction and extension of three-aisle high-bay warehouse HRL 1 for the storage of finished goods
- First construction phase of three-aisle high-bay warehouse: 125 m x 30 m x 38 m (L x W x H)
- 15,435 pallet spaces
- High-bay warehouse after extension: 155 m x 30 m x 38 m (L x W x H)
- 20,600 pallet spaces
- 3 stacker cranes in single-mast design with telescopic forks and chain conveyors
- Pallet storage 1 to 3 deep
- Single, pair or triple pallet transportation
- Flexible load unit size up to 3.1 x 1.7 x 1.95 m (L x W x H)
- Direct connection to production and shipping
- Expansion without interfering with day-to-day operations
Doubling of the three-aisle high-bay warehouse for the storage of finished goods HRL 2
The new high-bay warehouse 2 is connected to the north of the existing three-aisle high-bay warehouse 1 and is linked to production in terms of conveyor technology. A second distribution car enables the increased material flow in the direction of dispatch. The WMS HiLIS was also reconfigured.
- Three-aisle high-bay warehouse: 155 x 31 x 38 m (L x W x H)
- 22,000 pallet spaces
- 3 stacker cranes in single-mast design with telescopic forks and chain conveyors
- Pallet storage 1 to 3 deep
- Single, pair or triple pallet transport
- Gentle handling
- Flexible load unit size as in HRL 1
- Direct connection to production and shipping
Two-aisle format goods warehouse - transport and storage without bottom pallet
The two-aisle format warehouse was built in an existing hall to temporarily store format stacks with a wide range of dimensions until they are needed in processing. The stacks are transported and stored without load securing and without a bottom pallet.
- Two-aisle format warehouse: 59.5 x 18 x 10.8 m (L x W x H)
- Up to 752 stacking locations
- 2 two-mast stacker cranes with 11-tine telescopic forks
- 1 - 4 stacks per compartment, single-deep
- Maximum stacking weight: 3,000 kg
- Flexible handling of various dimensions, max. 3.73 x 2.62 x 1.85 m (L x W x H)
- Just-in-time supply of processing
"I was particularly impressed by the short start-up phase of the new HRL. After less than 6 weeks, the system was already running at full load in 3-shift operation. The assumed calculated storage and retrieval values were even exceeded. Detailed planning and a trouble-free construction phase were decisive for this. I am happy that we decided in favor of HÖRMANN Logistik."
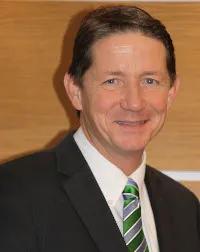
Roland Zerhusen
Managing Director
Zerhusen Kartonagen GmbH