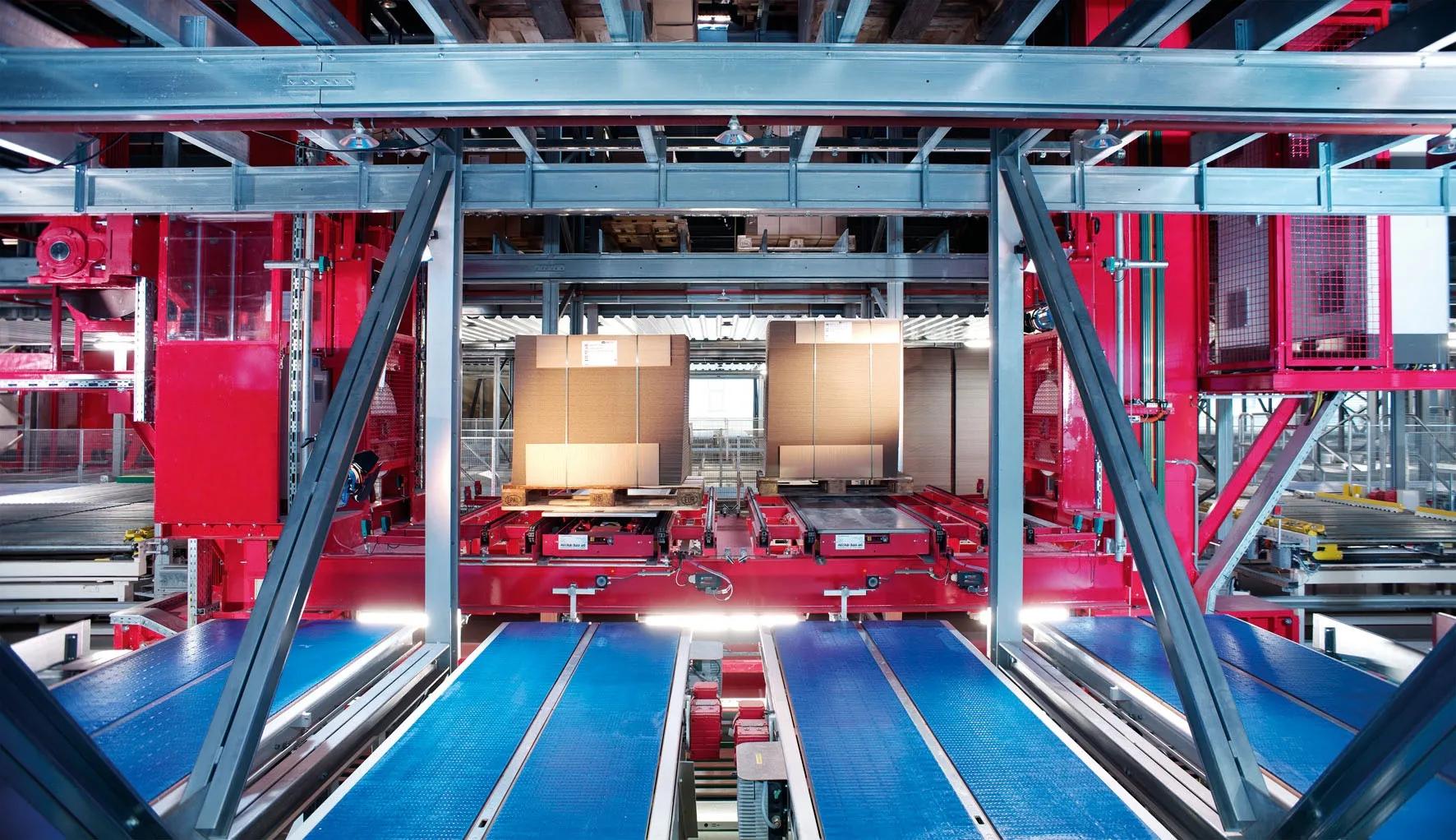
Several automatic high-bay warehouses for corrugated sheetboards at Progroup
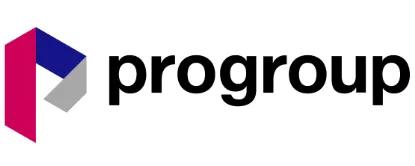
Progroup produces corrugated sheetboards in its core business with high-tech equipment that is among the fastest in the world. Its own paper production and service companies provide process optimization at 12 locations in Europe. Strongly expanding and highly specialized, Progroup has been working with HÖRMANN Logistik for many years to implement future-oriented intralogistics concepts.
Automated high-bay channel warehouse in Schüttorf, Germany
In Schüttorf/Lower Saxony, Progroup built the largest and most modern corrugated sheet feeder plant in Europe with a corrugator of 3.30 m working width, a speed of up to 400 m/min and a production volume of 140,000 t/a. Between the CIM-controlled corrugated board production (Computer Integrated Manufacturing System) and the shipping department, HÖRMANN Logistik installed a high-bay warehouse with buffer function.
The stacked corrugated board produced on the corrugator is immediately transported away, placed on up to three sub-pallets depending on the order and format, secured against loading and temporarily stored in the high-bay warehouse. Before storage, the load units are measured, centered and aligned. Depending on the specified retrieval date and order assignment, HiLIS decides where the load is to be stored.
Highlights
- 3-aisle high-bay channel storage system with 13 levels and 13,000 storage locations
- 3 highly dynamic stacker cranes in single-mast design with a lifting speed of up to 2 m/s and variable acceleration values
- Automatic handling of almost all stack dimensions (max. dimension of 2.5 x 1.8 x 2.2 m, with max. 3 lower pallets or palletless)
- Special channel vehicles for lengthwise or crosswise storage of corrugated board stacks
- Intelligent pairing strategies with the HiLIS Warehouse Management System
- Logical quadrant management of the warehouse for performance optimization
- Millimeter-precise management and positioning of stacks in the channels for optimal volume utilization
- Shortest provisioning times and flexible loading of approx. 100 trucks per day
- Storage/retrieval capacity of 120 / 150 units per hr.
- Operating time of 24 hrs/day and 7 days/week
Automated high-bay channel storage system in Offenbach, Germany
At the Progroup site in Offenbach, a state-of-the-art corrugated sheet feeder plant for the production of heavy-duty corrugated board was built in a new record-breaking construction time of only nine months. In order to ensure the greatest possible flexibility with regard to machine utilization and waste-optimized production, a three-aisle high-bay warehouse with channel technology was also chosen here.
Highlights
- 3-aisle high-bay channel storage system: 60 x 41 x 34.5 m (L x W x H)
- Highly dynamic stacker cranes with 2 channel trucks for large formats with a lifting speed of up to 2.0 m/s
- Camera-based fine positioning system with teach-in function
- Millimeter-precise management and positioning of piles in the channels for optimal volume utilization
- Storage of formats from 1.2 x 0.8 m to 4.2 x 2.5 m
- Large format stacks are placed on up to 9 lower pallets
Automated high-bay channel storage system in Strykow, Poland
At Progroup in Strykow, HÖRMANN Logistik built a high-bay warehouse using channel technology as a buffer between corrugated board production and shipping. This enables highly waste-optimized production and just-in-time delivery to customers.
Highlights
- 3-aisle high-bay channel storage system with 13,000 storage locations
- 3 highly dynamic storage and retrieval machines
- Special channel truck for transport with up to three sub-pallets or palletless
- Millimeter-accurate, camera-based compartment fine positioning with teach-in function
- Handling and storage of different formats with and without lower pallet
- Storage/retrieval capacity 120 / 150 units per hour
- Average storage time less than 24 hours
- Direct loading of stacks from conveyor into trucks
Automated high-bay warehouse in Ellesmere Port, Great Britain
A special feature of the intralogistics concept at Progroup in Ellesmere Port is the combination of strapped corrugated board formats on pallets and non-strapped corrugated board formats without a lower pallet. Different compartment types in the high-bay warehouse allow fully flexible and volume-optimized loading with packing units in a wide variety of combinations.
Highlights
- 4-aisle high-bay warehouse: 96.7 x 48.2 x 33 m (L x W x H)
- 4 stacker cranes in 2-mast design
- 2 stacker cranes with 1 load handling device - pair factor 100%
- 2 RBG with 2 load handling devices - packing units in triples
- storage capacity approx. 14,436 pallets
- Transport and storage of different formats with and without lower pallet
- Camera-based compartment fine positioning
Automated high-bay warehouse in Eisfeld / Thuringia, Germany
Highlights
- 3-aisle high-bay warehouse: 89.9 x 37.1 x 35 m (L x W x H)
- 2 stacker cranes with 6 telescopic forks
- 1 stacker crane with 3 telescopic forks
- Storage capacity approx. 10,563 pallets
- Transport and storage of different formats with and without bottom pallet
- Intelligent, volume-optimized storage strategies with HiLIS
- Camera-based compartment fine positioning
"Together with HÖRMANN Logistik, we have implemented a fully automatic high-bay warehouse with direct online connection to the corrugator for the first time in the corrugated board industry. This resulted in a groundbreaking, fully automated intralogistics concept from corrugated board production to intermediate buffering in the high-bay warehouse and truck loading."

Jürgen Heindl
President of the board
Progroup AG