Fairs 2019
2019
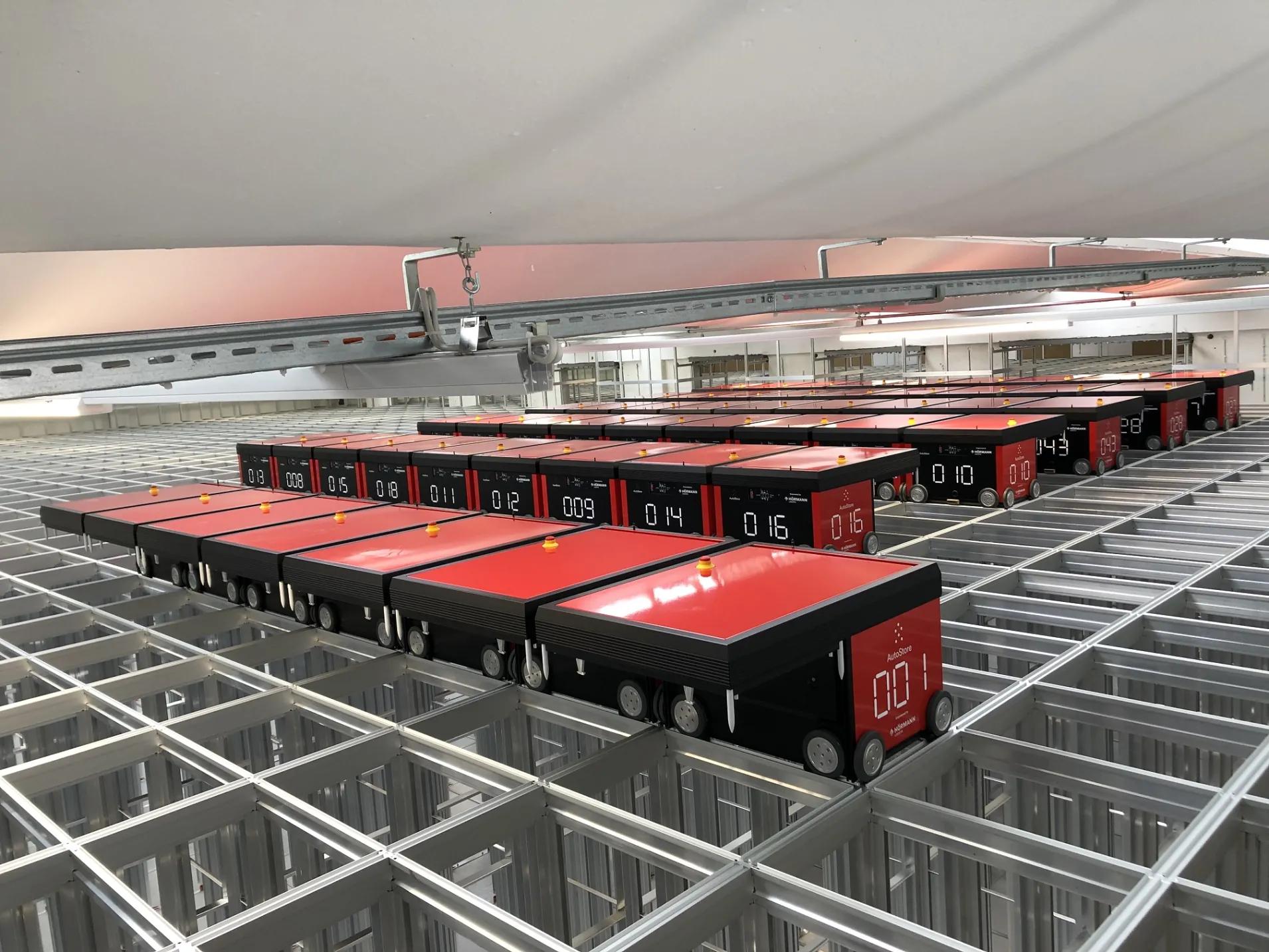
Innovative multi-solution material flow solutions
Smart integrated warehousing
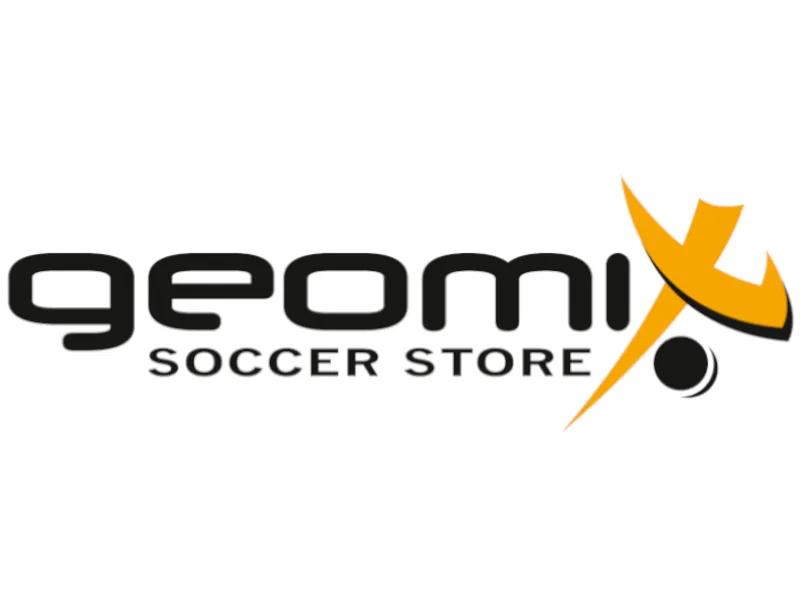
The online store of Geomix GmbH, official partner of the Austrian Football Association and the Austrian Football League, offers clothing and shoes for soccer, leisure, running and training. In addition, you can find original jerseys of the most important international football clubs in their extensive fan store. In Liezen, Styria, an AutoStore® system was installed in an existing warehouse to optimize e-commerce processes. Hörmann Logistik planned the special requirements for dynamics and pick rate in detail and realized the project.
The concept
Based on eight operating hours on five days, available space and several system simulations with real data, Hörmann Logistik designed the individual AutoStore® system with 52 robots and 23,500 containers on nine levels. The existing hall determines the height of the AutoStore® grid.
Nine carousel ports guarantee the high pick rate of 1,500 retrievals per hour. 2 carousel ports will cover about 100 storages per hour in the first phase, three more carousel workstations are preconfigured for a second phase. The Single-Double-Grid with the overall dimensions of 31 x 40 x 4.2 m (L x W x H) is encased on three sides.
The 23,500 standard containers (649 mm L x 449 mm W x 330 mm H) allow a maximum payload of 30 kg each.
52 red-line robots supply and discharge the 11 carousel workstations. Each robot needs about 5 hours charging time per day. For this purpose, 41 charging stations are available at the edge of the grid.
Maximum dynamics with 1,500 picks per hour
All workstations are equipped for both goods receipt and picking. The warehouse employees deliver the incoming goods to the two storage ports.
1,500 presumed retrieval picks per hour result in a cycle time of approximately 19 seconds per pick.
The stacks, each with 9 containers, stand directly on the hall floor. The single-double-grid rail system is located above the container stacks. There the battery-powered robots move autonomously. The robots jointly pick up containers, re-sort them as required and make them available at the carousel ports. Dividers allow for flexible partitioning of containers for simultaneous handling of different articles.
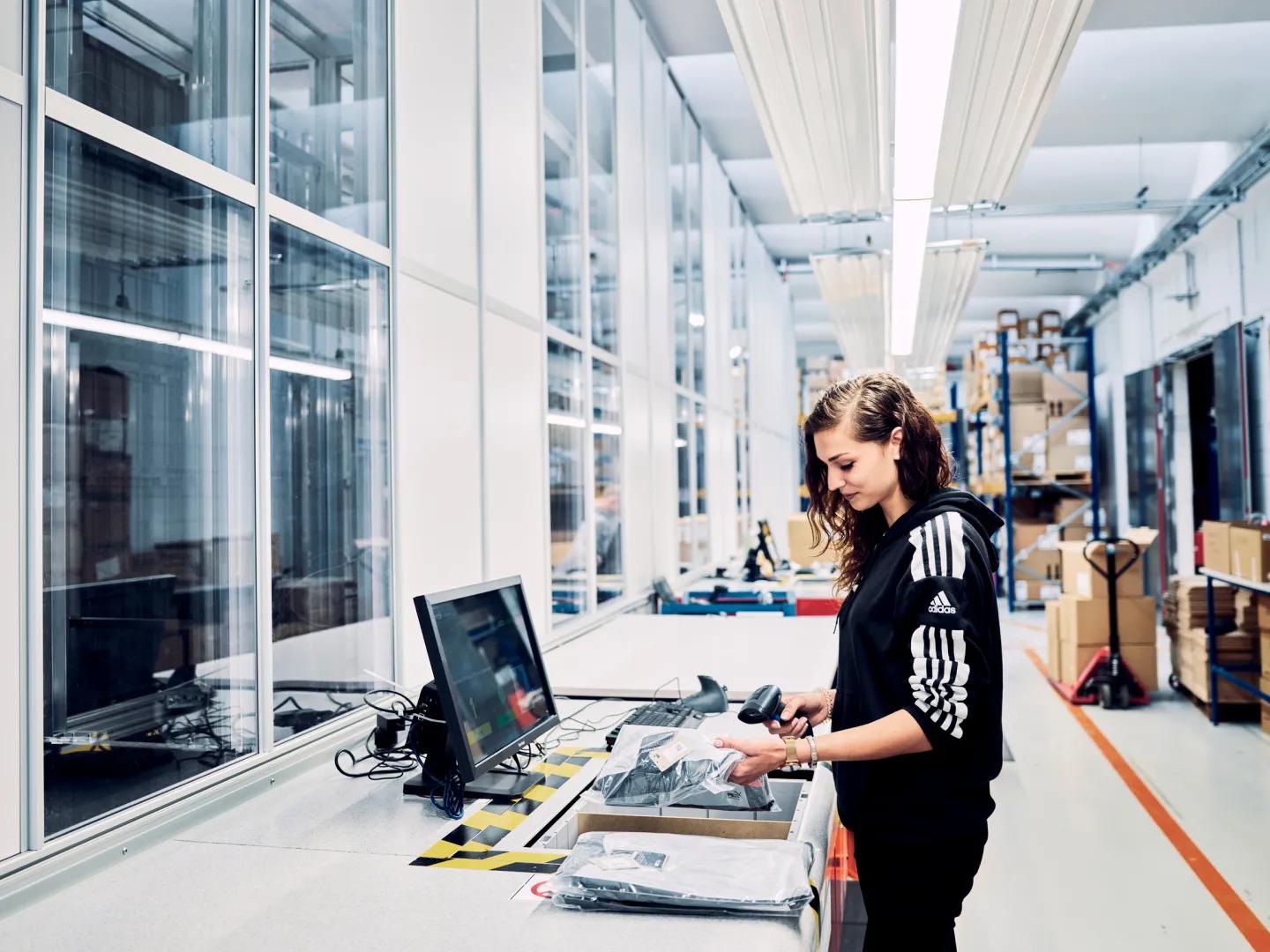
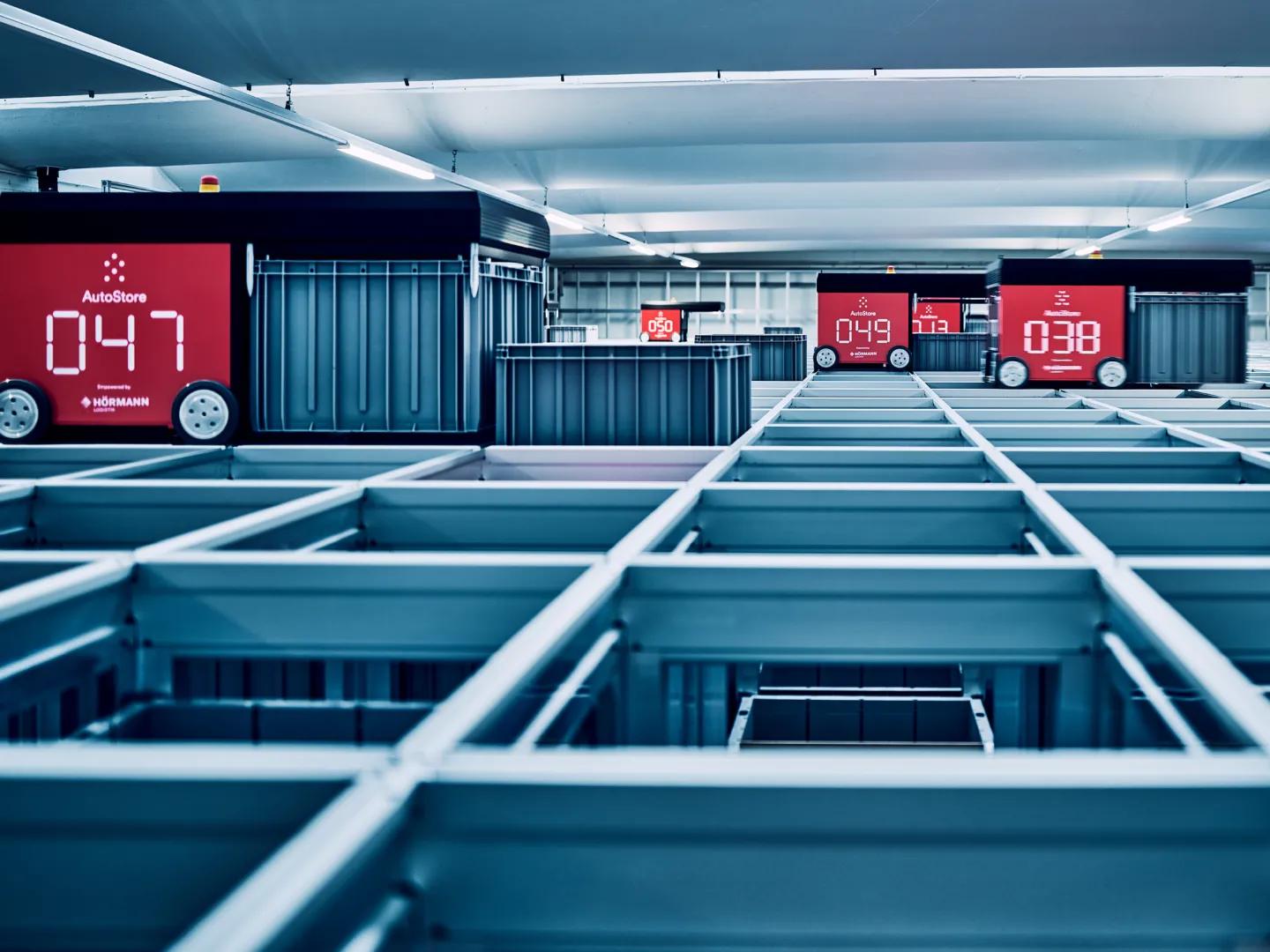
"As official partner of various soccer leagues we offer clothing and footwear for soccer, leisure, running and exercising in our online-store. The AutoStore® system meets our particularly high requirements for dynamic and fast pick rates within the e-commerce processes."
KARL ZETTLER | BOARD MEMBER GEOMIX
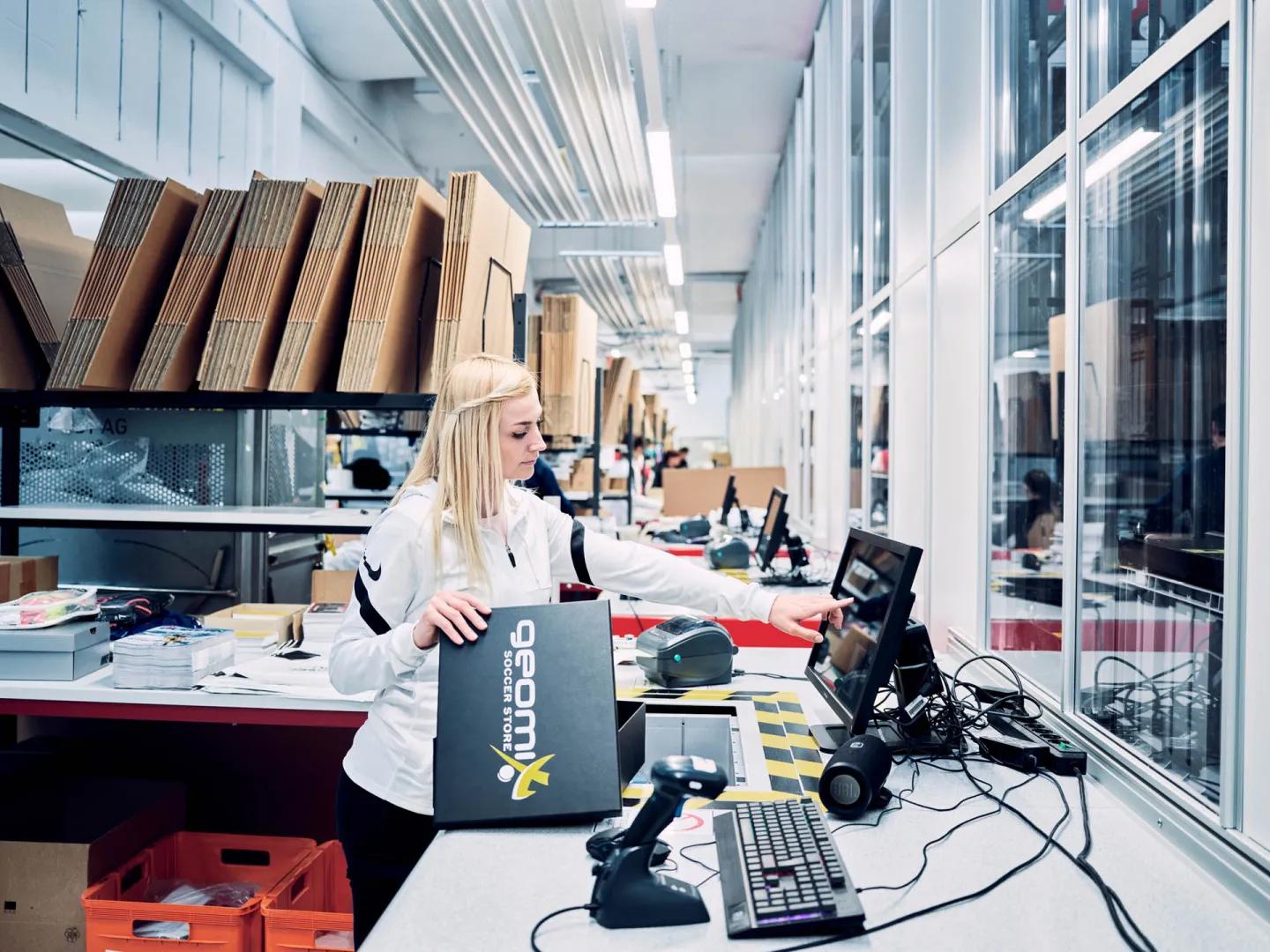
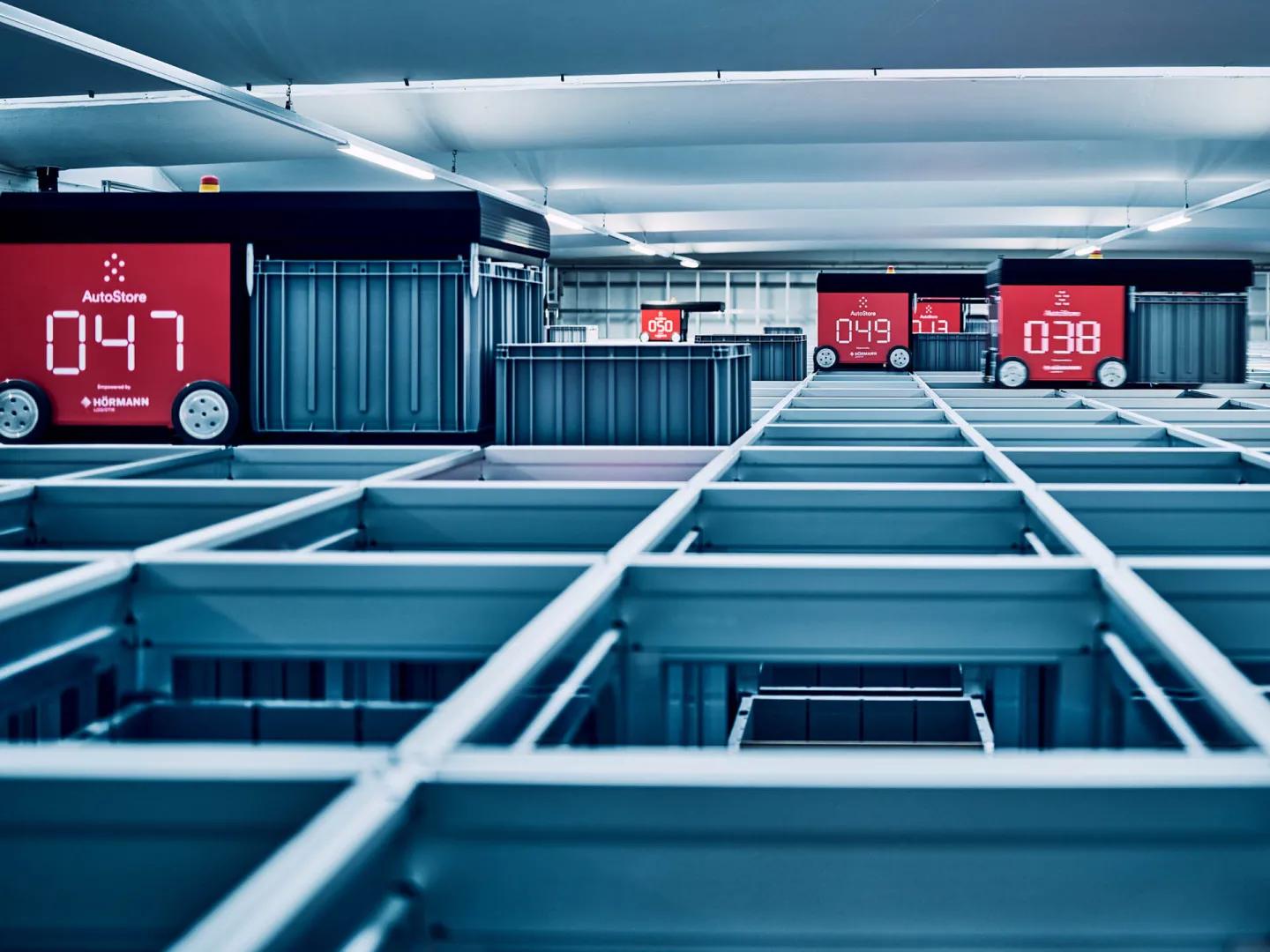
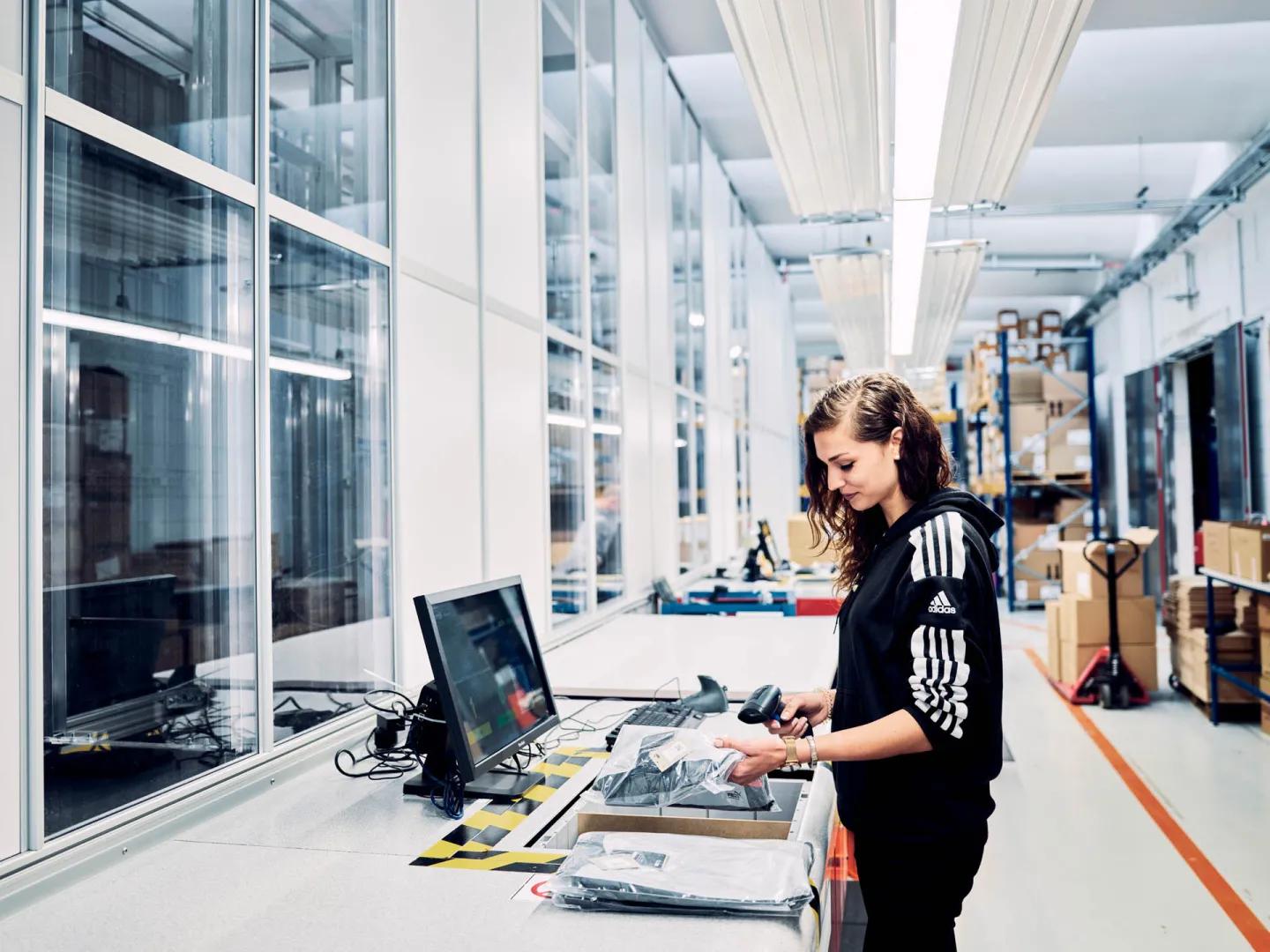
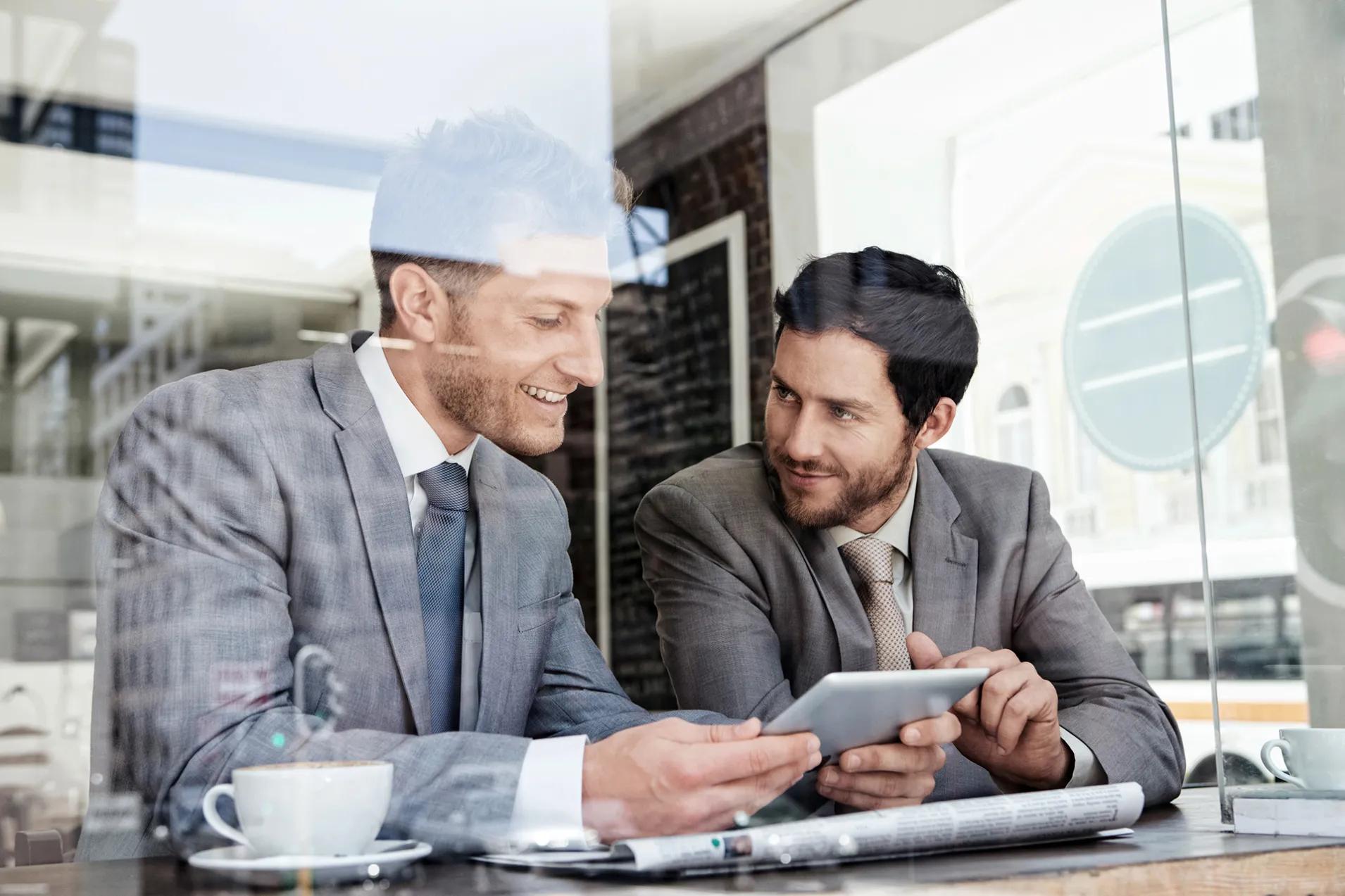
Press and Media Contact
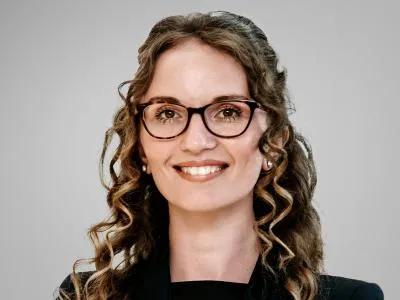
Head of Marketing Communication – Press and Media Contact for HÖRMANN Gruppe
Celina Begolli
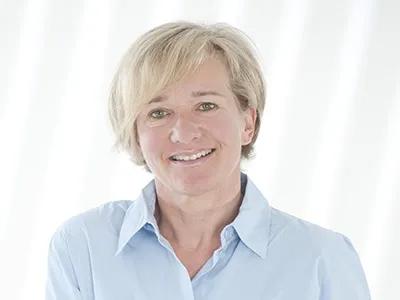
PRESS AND MEDIA CONTACT for HÖRMANN Intralogistics
Annett Sachs
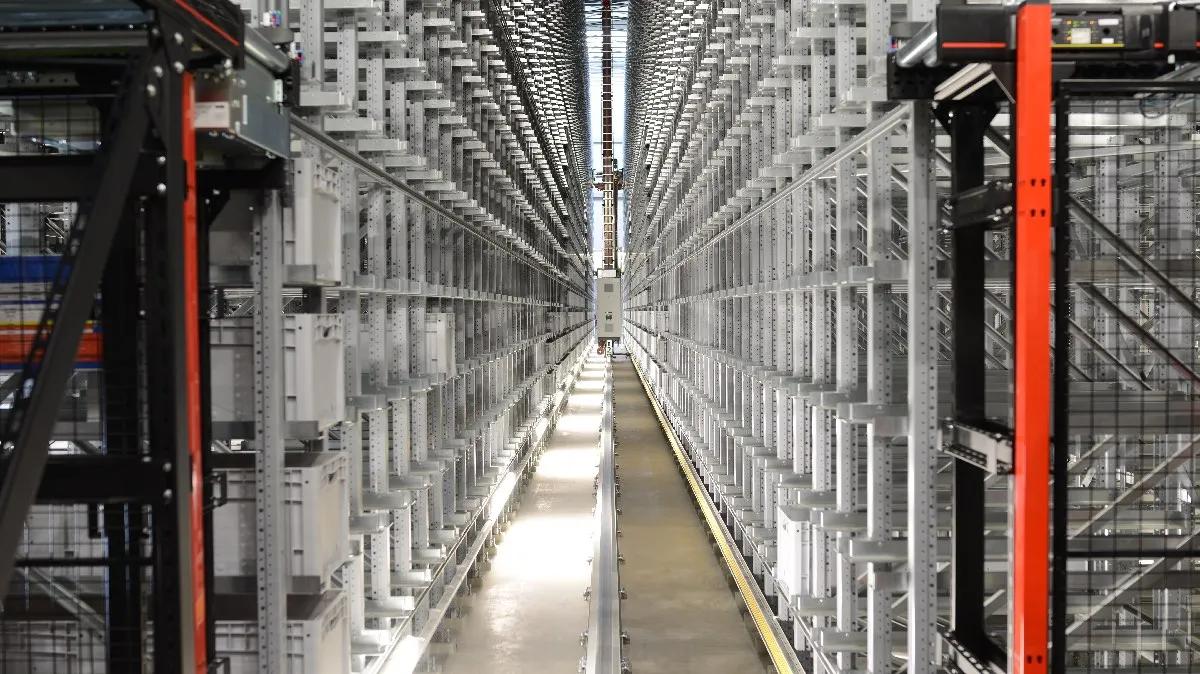
Automatic small parts warehouse for Codico in Perchtoldsdorf, Austria
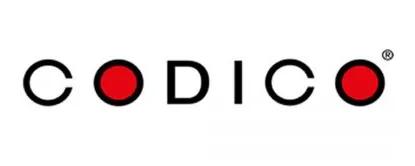
Codico Holding GmbH specializes in the distribution of high-quality electronic components in the areas of active and passive components as well as connection technology. Founded in 1977, the company operates in twelve countries with 191 employees.
At the Austrian headquarters in Perchtoldsdorf in the south of Vienna, a new automated small parts warehouse (AS/RS) with container conveyor technology is being built for the storage and picking of electronic components. Hörmann Logistik implemented the project as general contractor.
Concept
The new mini-load warehouse is designed with three aisles, but for the time being only two aisles have been equipped with stacker cranes. The racking steel structure is a built-in warehouse in which the totes are stored double-deep lengthwise. The storage and retrieval machines (SRM) are equipped with a telescopic belt conveyor as load handling device. This allows them to pick up two totes at a time and store and retrieve them in parallel. In order to optimally control the storage compartment, the SRMs are equipped with a camera for fine compartment positioning.
The items are stored by type in the totes, which measure 600 x 400 x 320 mm (L x W x H) and have a maximum weight of 50 kg. An automatically scannable, unique barcode marries the containers to their contents.
A tote circuit connects the miniload with the deconsolidation workstations, as well as with picking and packing. The empty container conveyor system runs above the full container conveyor system and supplies the picking and deconsolidation areas with empty containers.
Material flow with the customized warehouse management system HiLIS.
In deconsolidation, delivered goods are filled into empty containers by employees, the barcode of the container is read and thus the goods are booked into the warehouse management system. Once the entry is complete, the container is automatically transported via the conveyor system and a vertical conveyor towards the miniload. In order picking, the employee marries an empty tote that has been delivered via conveyor technology to the current order by scanning the barcode. He then removes the order-related items from the requested storage totes and places them in the order tote.
The storage totes are then returned to the miniload, while the order totes are either conveyed directly to the packer after picking is complete or, in exceptional cases where the order has not yet been released for packing, temporarily stored in the miniload. The order totes are already conveyed to the packing station in the correct sequence from the point of view of packing strategy. There, the employee removes the goods, packs and labels them, and finally places them on a shipping pallet. The empty containers are returned to the empty container cycle.
Warehouse management, control and visualization are carried out with the proven Hörmann intra Logistics system HiLIS, which communicates with the ERP customer system via interface. A particular challenge was the integration of manual warehouses and complex manual processes in the packaging and shipping areas. In the manual areas, the HiLIS work dialogs are displayed on mobile devices (PDAs).
Highlights
- 3-aisle
- 2 stacker cranes with telescopic belt conveyors
- dimensions miniload: 65 x 12 x 12 m (L x W x H)
- Storage: 100 totes per hour
- Retrieval: 170 totes per hour
- Number of totes: 38,550
The scope of supply from Hörmann Logistik included steel racking as built-in storage, tote conveyor technology, stacker cranes, fire doors, Warehouse Management System HiLIS incl. system visualization. The commissioning at Codico took place in summer 2020.
Materialfluss mit dem maßgeschneiderten Warehouse Management System HiLIS
In der Dekonsolidierung wird angelieferte Ware von Mitarbeitern in Leerbehälter gefüllt, der Barcode des Behälters gelesen und so die Ware im Lagerverwaltungssystem eingebucht. Nach Abschluss der Erfassung wird der Behälter automatisch über die Fördertechnik und einen Vertikalförderer in Richtung AKL transportiert. In der Kommissionierung verheiratet der Mitarbeiter einen über Fördertechnik angedienten Leerbehälter durch Barcodescannung mit dem aktuellen Auftrag. Er entnimmt dann aus den angeforderten Lagerbehältern die auftragsbezogenen Artikel und legt diese in den Auftragsbehälter.
Die Lagerbehälter werden dann ins AKL rückgeführt, während die Auftragsbehälter nach Abschluss der Kommissionierung entweder direkt zur Verpackung gefördert oder in Ausnahmen, falls der Auftrag noch nicht zur Verpackung freigegeben ist, im AKL zwischengelagert. Die Auftragsbehälter werden bereits in der packstrategisch richtigen Reihenfolge zum Packplatz gefördert. Dort entnimmt der Mitarbeiter die Ware, verpackt und etikettiert sie und legt sie abschließend auf eine Versandpalette. Die Leerbehälter werden wieder dem Leerbehälterkreislauf zugeführt.
Die Lagerverwaltung, –steuerung und -visualisierung erfolgt mit dem bewährten Hörmann intra Logistics System HiLIS, das mit dem ERP-Kundensystem über Schnittstelle kommuniziert. Eine besondere Herausforderung dabei waren die Integration manueller Läger und komplexe manuelle Prozesse im Verpackungs- und Versandbereich. In den manuellen Bereichen werden die HiLIS-Arbeitsdialoge auf mobilen Endgeräten (PDAs) dargestellt.
Highlights
- 3-gassig
- 2 Regalbediengeräte mit Teleskop-Riemenförderer
- Abmessungen AKL: 65 x 12 x 12 m (L x B x H)
- Einlagerungen: 100 Behälter pro Stunde
- Auslagerungen: 170 Behälter pro Stunde
- Anzahl Behälter: 38.550
Der Lieferumfang von HÖRMANN Intralogistics umfasste Regalstahlbau als Einbaulager, Behälterfördertechnik, Regalbediengeräte, Brandschutztore, Warehouse Management System HiLIS inkl. Anlagenvisualisierung. Die Inbetriebnahme bei Codico erfolgte im Sommer 2020.
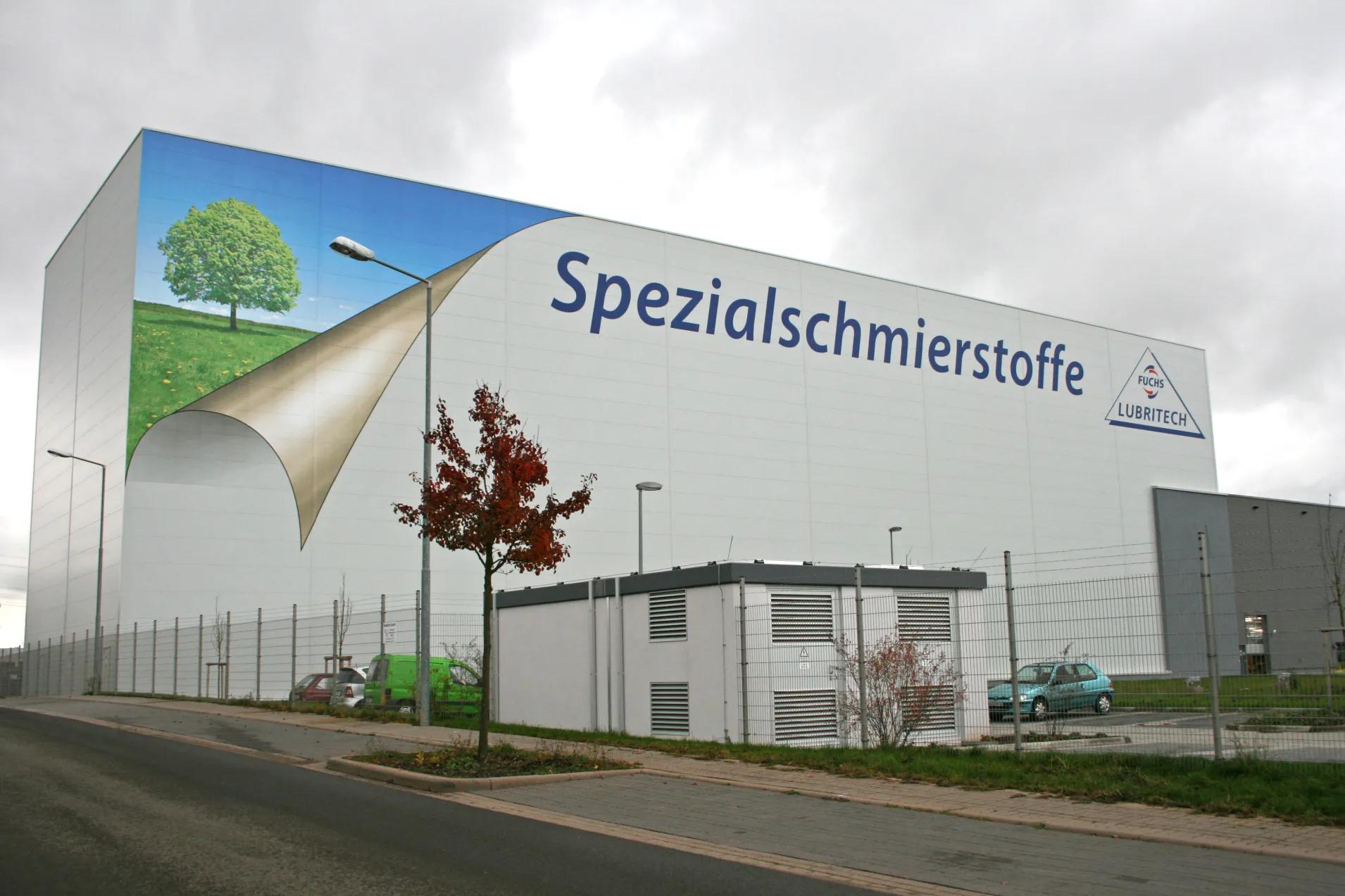
High-bay warehouse with explosion protection zone for a wide variety of stored goods at Fuchs Lubritech in Kaiserslautern, Germany
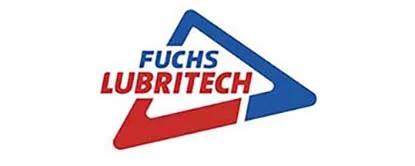
Fuchs Lubritech GmbH is one of the world's leading producers of specialty lubricants and release agents for all industrial applications such as the automotive industry, mechanical engineering, construction and agriculture. The product range comprises more than 1,000 special products tailored to the respective application. At the headquarters in Kaiserslautern, a new laboratory, administration and production center was built with a high-bay warehouse linked to production. It serves as a raw material warehouse, for production supply as well as a finished goods warehouse with connected order picking zone. As general contractor, HÖRMANN Logistik realized the complete new high-bay warehouse and the three-aisle extension with connected conveyor technology and WMS.
Concept
The storage of highly flammable and highly combustible products required a special fire protection concept. A system of fire prevention is used by reducing the oxygen content in the entire high-bay warehouse. This prevents a flame from developing in the first place. By injecting nitrogen, this inerting system creates a low-oxygen atmosphere in the warehouse, similar to that on a mountain peak at an altitude of 4,500 meters. For stored goods with a very low flash point and for highly flammable products, a special zone has also been set up in the high-bay warehouse that can be flooded with CO2. A detection system permanently monitors this zone and issues warnings in the event of an emergency. In the explosion protection area of the warehouse, mechanical and control sparking must be avoided under all circumstances. This applies primarily to the storage and retrieval machines, which are equipped with special explosion-proof drives and explosion-proof sensors. Essential electrical components are installed outside the explosion-proof area. Special mechanical components in the chassis area and on the telescopic fork were designed with materials that prevent sparking. The control system of the transfer cars calculates the optimum travel curve by means of an integrated travel curve control system, thus enabling jerk-free acceleration and deceleration, which is an important safety factor, especially when containers and drums are filled with liquids. The same applies to the storage and retrieval machines, whose self-learning compartment fine-positioning control system permanently updates the coordinates
and thus considerably reduces positioning movements.
Sophisticated conveyor technology
A pallet circuit is the central element linking the different material flow areas. It serves both to provide goods for production supply, to connect to the picking stations, and to connect to the six-meter higher level of high-bay storage and retrieval via the vertical conveyors. Before entering the storage area, the pallets pass through an airlock with high-speed doors to maintain the oxygen-reduced environment of the warehouse. In the high-bay warehouse, a distribution truck transports the pallets to the storage spur assigned by HiLIS. The HÖRMANN intra Logistics System HiLIS, which has an interface to the on-site HOST system, ensures smooth processes of the conveyor and storage technology as well as optimized warehouse management.
Highlights
- 3+3-aisle high-bay warehouse: 76.9 x 45 x 25.4 m (L x W x H)
- Electrical and mechanical equipment according to ATEX 94/9/EG Zone 2
- Fire protection concept with low oxygen atmosphere and CO2 zone
- Double-deep storage
- Storage of a wide variety of load carriers such as Euro pallets, chemical pallets, drum pallets and a wide variety of materials
- Common storage of packaging, raw materials and finished products
- 6 automatic stacker cranes in single mast design (aisle-bound) with telescopic fork pair in explosion-proof design
- Connecting conveyor system with distribution trolley and vertical conveyor
- Fire protection lock with high-speed doors
- 20,000 pallet spaces
- Individual solution for picking palletized goods and drums
- HiLIS WMS
"Together with the HÖRMANN Logistik team, we implemented a customized and secure storage solution for our diverse and highly sensitive goods. From planning to turnkey handover of the high-bay warehouse, HÖRMANN Logistik was always a reliable partner for us."
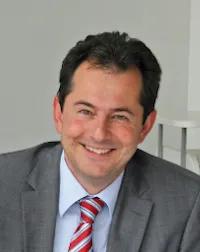
Markus Heck
Managing Director
Fuchs Lubritech GmbH
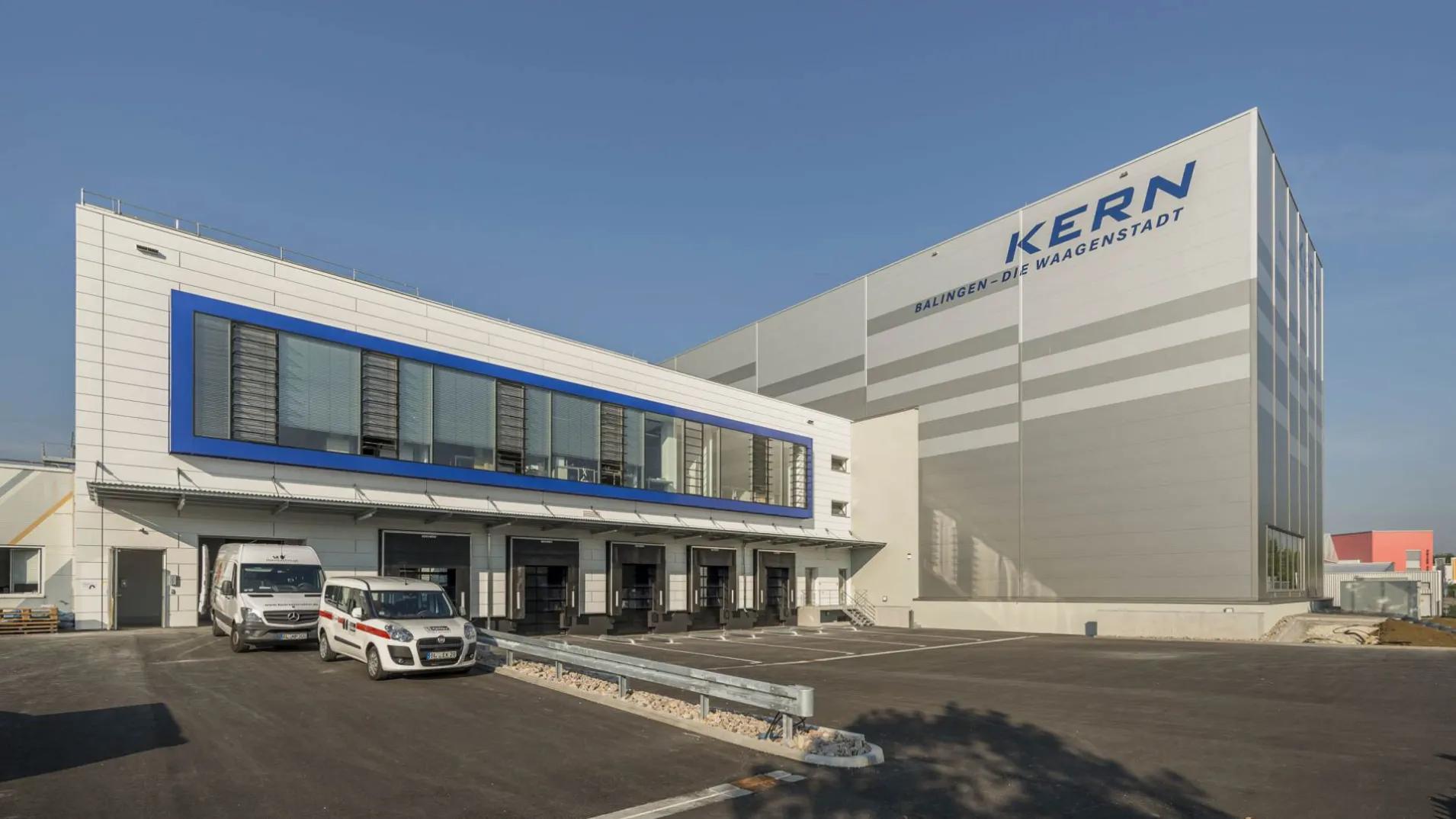
Reference iDM Energiesysteme GmbH
Multi-solution project comprising an automated high-bay warehouse and AutoStore System® for the new logistics center at iDM Energiesysteme GmbH in Matrei
Kern & Sohn GmbH is one of the largest suppliers of professional scales in Germany and is internationally known under the KERN brand. The product portfolio covers the entire spectrum of weighing technology, including integrated weighing solutions in conveyor and plant technology. In order to secure further growth and optimize material flow processes, PROTEMA Unternehmensberatung GmbH developed a new overall concept, which includes a new logistics and assembly concept as well as the construction of a new factory and logistics building. The automatic pallet high-bay warehouse and the automatic small parts warehouse with picking stations supplied HÖRMANN Logistik as general contractor.
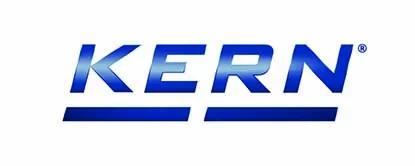
Concept
A special feature is the innovative concept in which cartons and small load carriers (KLT) of various sizes can be stored. This automated small parts warehouse (AS/RS) is integrated into the silo structure of the pallet high-bay warehouse and has the same height of 25 meters. This is made possible by the use of special storage and retrieval machines (SRM) in which only one drive drives both the chassis and the mast head via a toothed rack. With sophisticated gripping technology, the various cartons can be stored up to four deep.
Uniform large compartments are filled with up to 24 cartons in a volume-optimized manner. To prevent fire, both the single-aisle pallet high-bay warehouse and the double-aisle carton high-bay warehouse (AKL) are operated with an oxygen-reduced atmosphere. Cartons, KLTs and pallets are placed on the conveyor system at the goods receiving area. At the I-points, the WMS identifies the load units via barcode labels. The contours of cartons and KLTs are recorded on the conveyor system using a camera-based system. At this point, the WMS already decides how the load units are stored in the miniload.
The load units are immediately turned into the volume-optimized position. At several buffer lanes in front of the miniload, cartons of the same size classes are collected and stored as pairs or quadruples. The quadruple transport significantly reduces the number of AS/RS trips.
Customized warehouse management through HiLIS
HiLIS receives the delivery orders from the host computer. By passing them on early, HiLIS can couple orders of the same width class and thus also collect up to four cartons via the SRM and make them available at the delivery stub. They then pass through the airlock to the pick & pack stations. To enable the operator to work ergonomically, a scissor lift table lowers the pallets to working level. The operator removes the articles indicated by the terminal. Remaining quantities are put back into storage.
Warehouse management is handled by the HÖRMANN intra logistics system HiLIS, which communicates directly with the HOST. The three stacker cranes operate with the HiLIS Eco-Power Management System, which saves up to 25% of energy consumption through intelligent energy balancing. The HiLIS plant visualization system makes it possible to track and control all plant movements in real time and, if necessary, to change them by manual intervention.
Balingen is located in the Zollernalbkreis district, which is prone to earthquakes. To safeguard against this, an earthquake package was integrated into the system, which detects the possible shifting of cartons in the rack by sensor after an earthquake and realigns them.
Highlights
- Volume and throughput optimized warehouse strategies
- Direct connection of production & order picking
- Integration of seismic packages
- Fire prevention concept
- 1-aisle high-bay pallet warehouse
- 90.0 x 8.6 x 25.4 m (L x W x H)
- Storage capacity: 3,480
- Double-deep storage
- 1 automatic stacker crane with built-up telescopic fork
- Conveyor connection
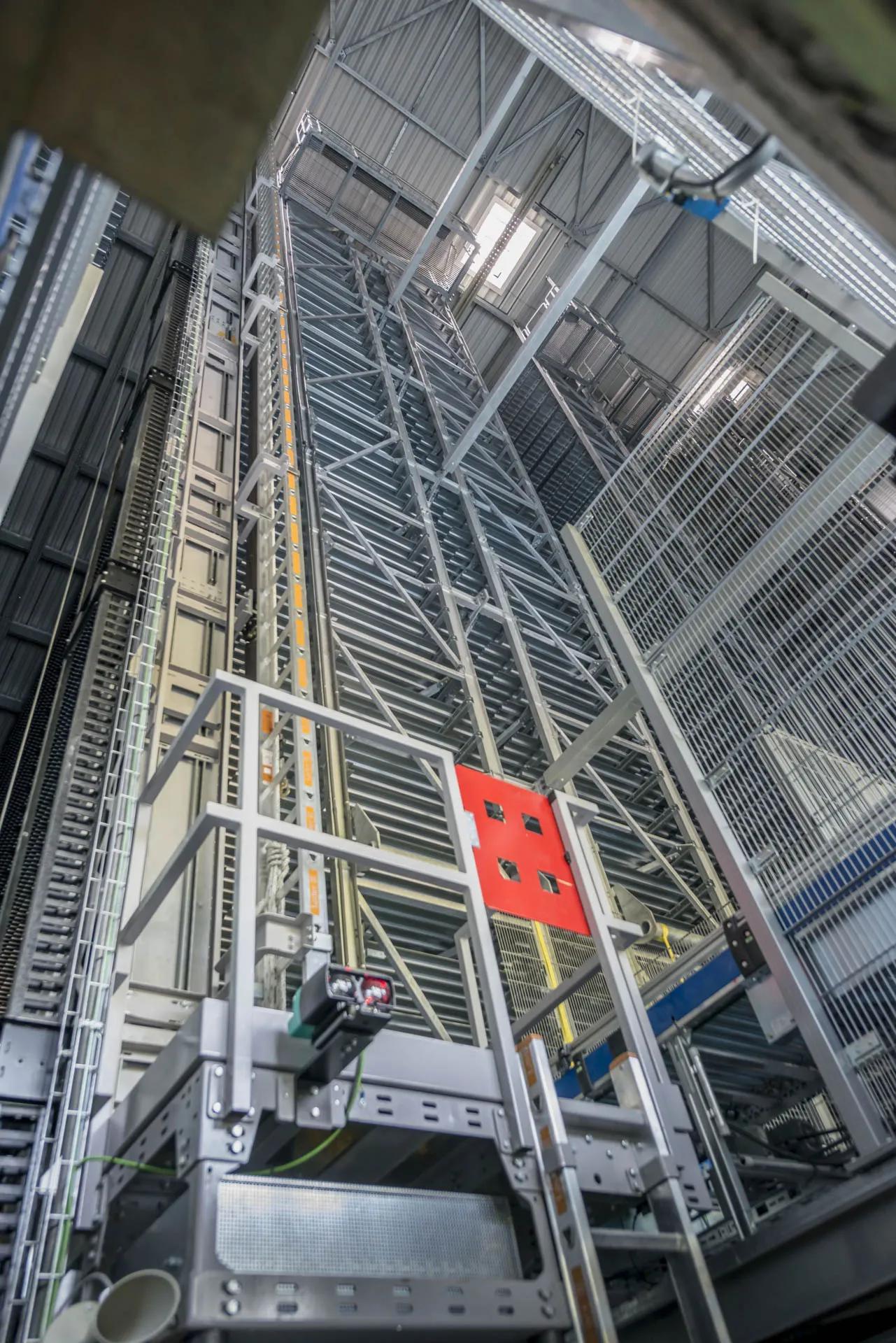
1-aisle pallet high bay warehouse
- 90.0 x 8.6 x 25.4 m (L x W x H)
- Storage capacity: 3,480
- Double-deep storage
- 1 automatic stacker crane with built-up telescopic fork
- Conveyor connection
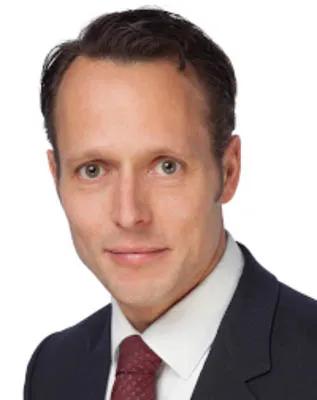
The new material flow concept ensures the greatest possible flexibility for our company, future growth as well as secure and transparent processes. During the implementation of this challenging project, we were able to rely on HÖRMANN Logistik as a professional and on-time partner at all times.
Albert Sauter
Managing Director, Kern & Sohn GmbH
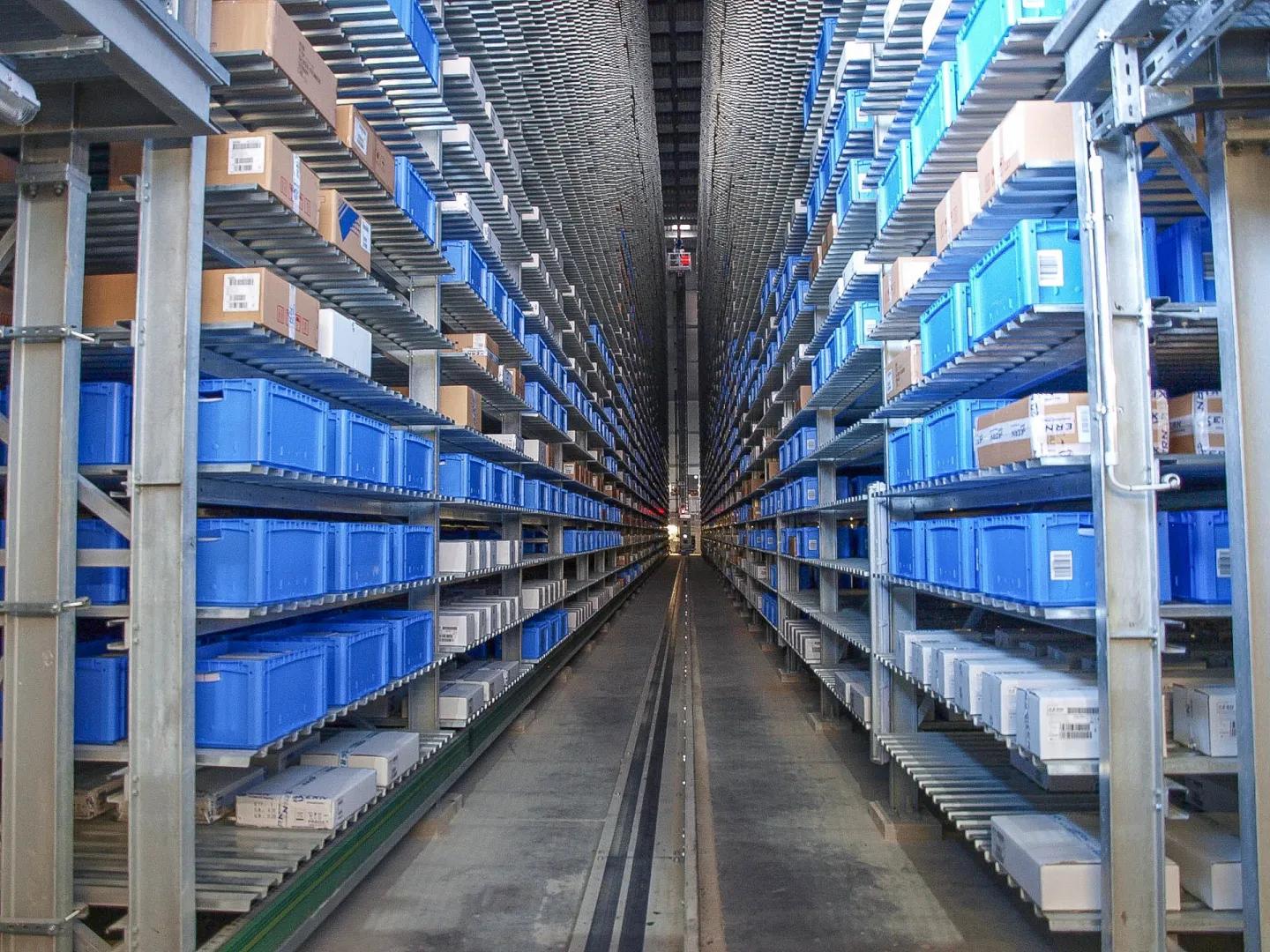
2-aisle AKL carton high bay warehouse
- 90.0 x 8.6 x 25.4 m (L x W x H)
- Storage capacity: up to 75,000 cartons and KLTs
- Storage 2 to 4 deep
- Storage of a wide range of carton sizes
- 2 automatic stacker cranes, each with a puller to hold up to 4 cartons
- Extensive conveyor technology
- HiLIS WMS
Referenfilm Kern & Sohn: HRL & AKL für Industriewaagen
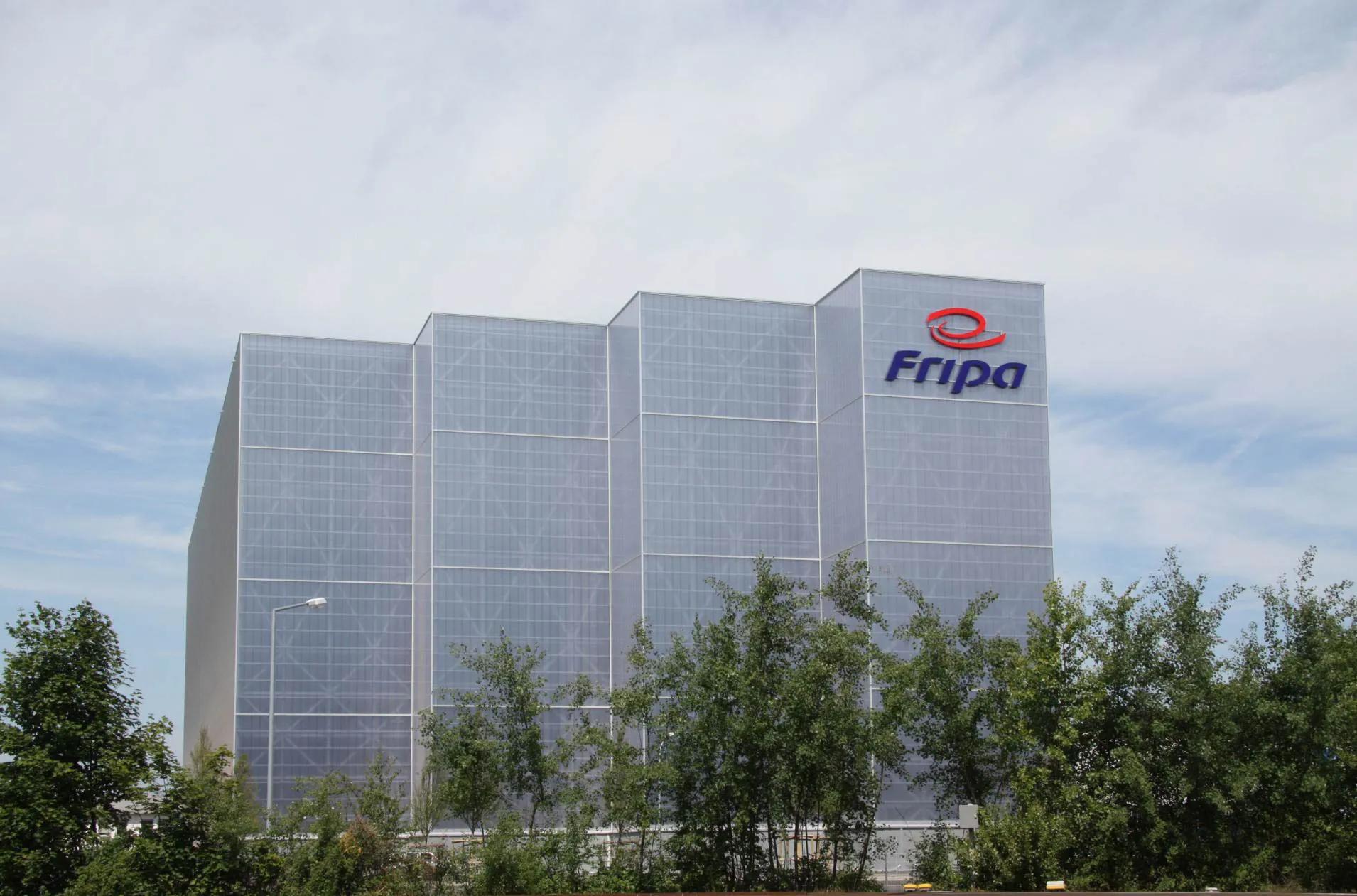
Reference Versandmanufaktur
Caja Robotics revolutionizes the fulfillment of Versandmanufaktur GmbH
The Fripa Papierfabrik Albert Friedrich KG is an internationally sought-after supplier of high-quality hygiene papers. The Miltenberg production site, with approximately 370 employees and several converting lines, is the company's state-of-the-art performance center. The steadily growing sales volumes required a new concept of warehouse logistics, in which the existing three-aisle high-bay warehouse and the block warehouse should be integrated.
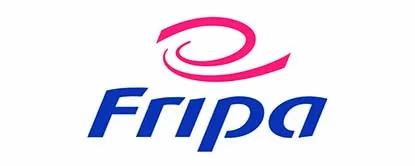
Based on Fripa's requirements, the specialist planning company Luy & Partner GbR developed an overall logistics concept in which the new warehouse management software to be implemented plays a decisive role. In competition with other suppliers, HÖRMANN Logistik was able to prevail as general contractor for the overall project. The warehouse management system HiLIS fulfills all specifications for a continuous IT and control concept from the production connection to the new high-bay warehouse 2 to be built, the integration of the existing warehouses to the new dispatch.
Concept
The new construction of the four-aisle fully automated high-bay warehouse is designed for four-deep pallet storage of finished goods on Euro pallets. For the most efficient storage and retrieval performance, the storage and retrieval machines (SRMs) were equipped with a special telescopic fork that can pick up to two pallets at a time. The pairing of similar items takes place directly at the infeed points of the new high-bay warehouse. The conveyor connection takes place on two conveyor levels. In the preliminary zone of the HRL 2, a highly dynamic electric monorail takes over the pallet transport.
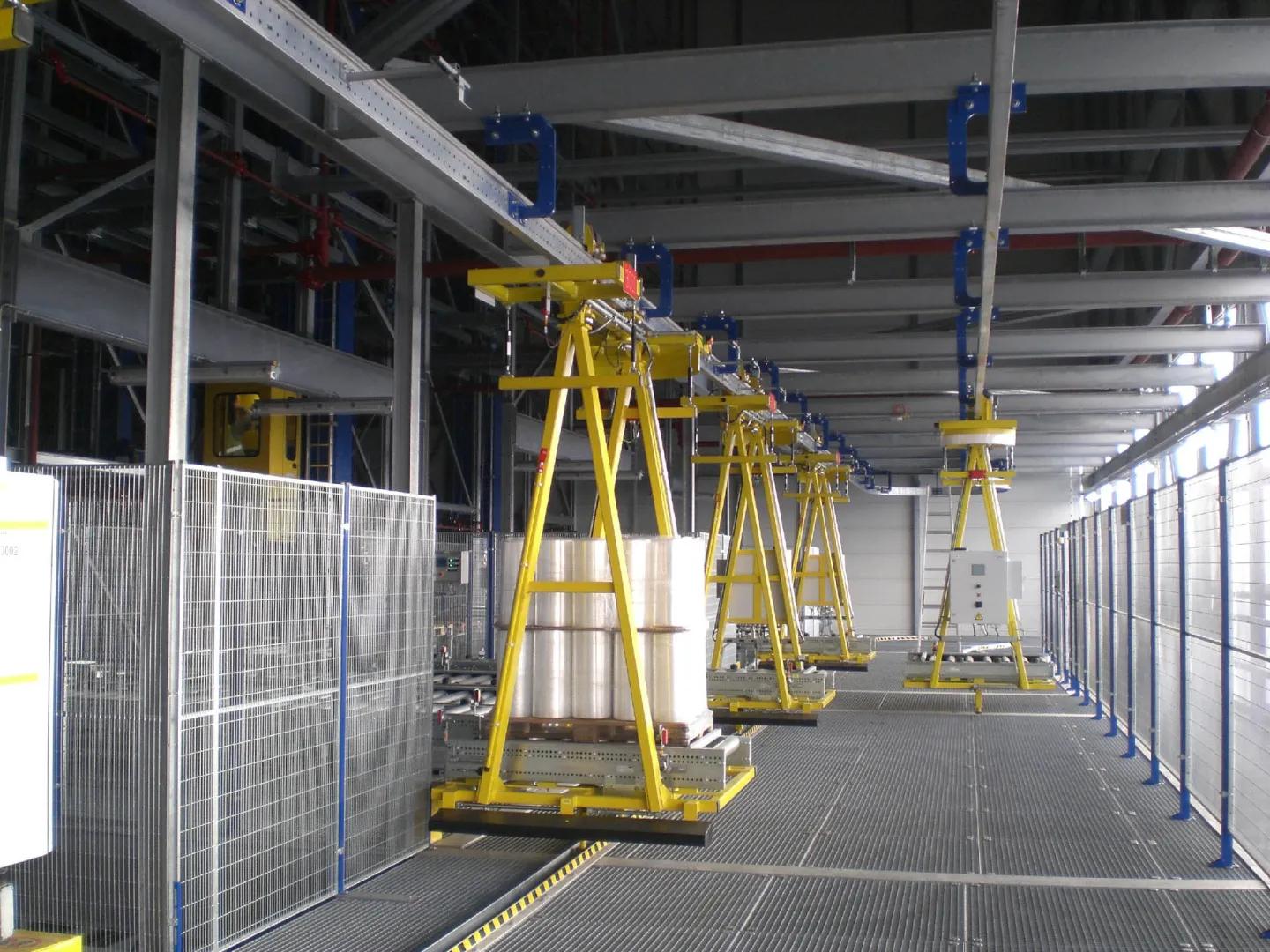
Transport to shipping takes place via vertical conveyors, continuous conveyors and distribution carriages until transfer to one of the 24 gravity roller conveyors. Three gravity roller conveyors are assigned to each loading gate. Shipping displays, which are controlled by HiLIS, show the shipper the required loading information. As a special feature, a photo is automatically taken of each truck load and stored in the warehouse management system. The two-mast design stacker cranes are equipped with the HiLIS Eco-Power Management System, which saves up to 25% of energy consumption through intelligent energy balancing.
After commissioning the new high-bay warehouse, HÖRMANN Logistik subjected the existing high-bay warehouse to a complete retrofit. In addition to mechanical adjustments to the existing storage and retrieval machines and conveyor technology, these were equipped with new control technology and integrated into the HiLIS WMS. The existing high-bay warehouse is connected to the new building via a conveyor technology bridge.
Highlights
- Four-aisle high-bay warehouse
- 4 stacker cranes in two-mast design with special telescopic forks
- Four-aisle deep storage
- Pair transport
- 210 / 200 pallets/h storage or retrieval capacity
- 21,500 pallet locations
- Retrofit three-aisle high-bay channel warehouse with 3 stacker cranes
- 6,500 storage locations
- Implementation HiLIS WMS
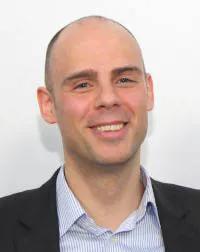
With the best references and a convincing and consistent IT concept, HÖRMANN Logistik was able to convince us in the selection of suppliers for our demanding project. The high expectations for the new high-bay warehouse construction, the modernization and the integration of the existing high-bay warehouse were excellently met by HÖRMANN Logistik as general contractor.
Jochen Giegerich
Purchasing Manager Technology, Fripa Papierfabrik
Albert Friedrich KG
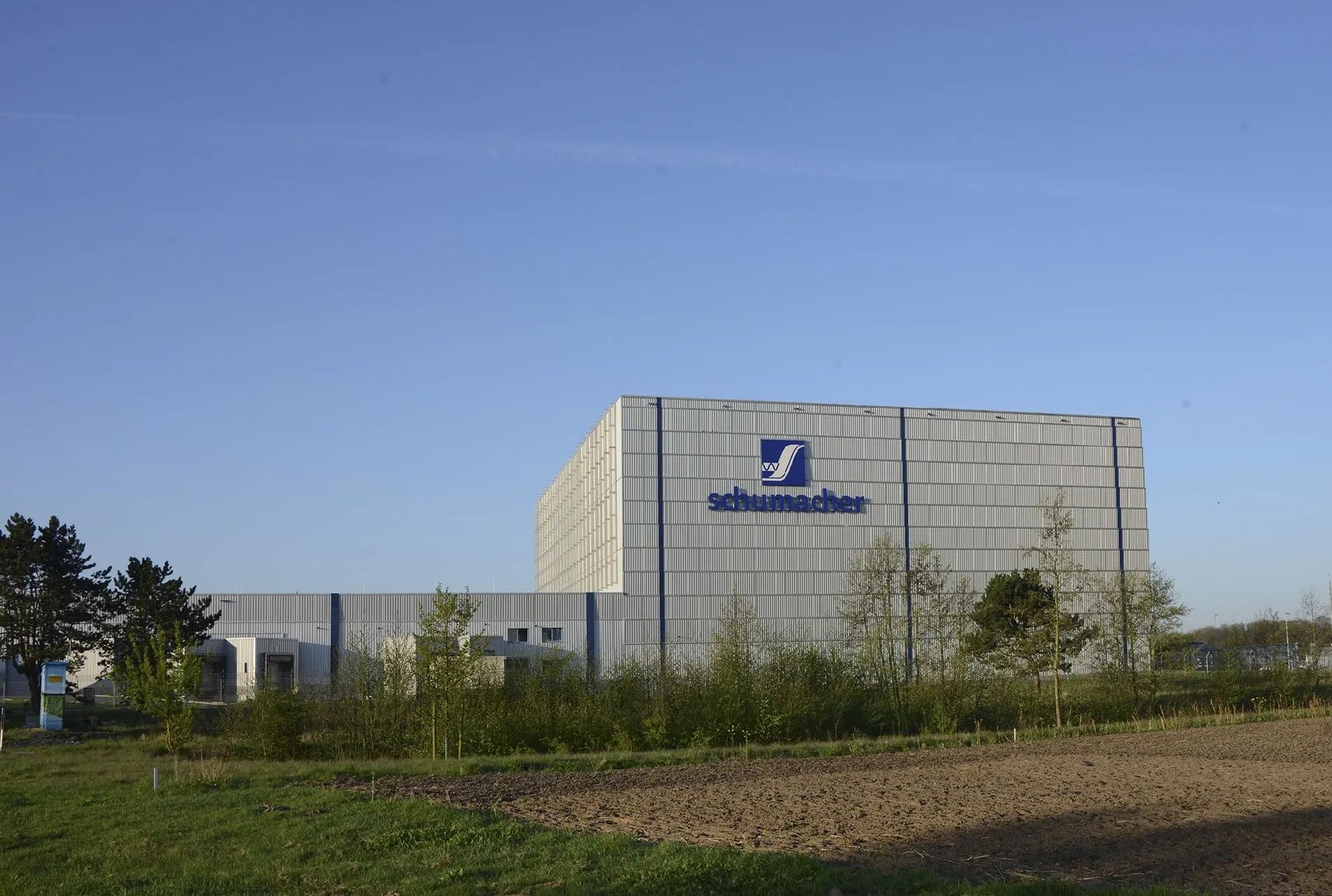
High-bay warehouse extension at Schumacher Packaging in Greven
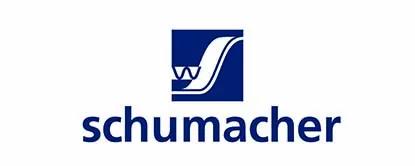
As an owner-managed, Europe-wide specialist for packaging made of corrugated and solid board, Schumacher Packaging offers an extremely wide range of sizes, printing techniques and finishes. Through newly established production facilities and the acquisition of existing plants, Schumacher Packaging has grown continuously in recent years. At the plant at AirportPark FMO in Greven, North Rhine-Westphalia, which only opened in 2014, the packaging specialist is now doubling its production and storage capacities. HÖRMANN Logistik has now expanded the existing high-bay warehouse with a two-aisle channel warehouse.
Concept
With the expansion of the automated high-bay warehouse, the existing storage capacity of the existing two-aisle channel warehouse has been more than doubled. In addition, the storage and retrieval capacity was massively increased. The two high-bay warehouses are used both to dispose of the production, which is operated around the clock, and to prepare the goods for dispatch. For high storage and retrieval performance, the stacker cranes can accommodate two pallets simultaneously for storage and retrieval. To ensure perfectly coordinated operation of the two high-bay warehouses and to improve serviceability, the warehouse management software and AS/RS controls installed by the previous supplier were replaced by the HÖRMANN Logistik Warehouse Management System HiLIS.
In addition to the high-bay warehouse, HÖRMANN Logistik supplied the entire conveyor technology for connecting the new high-bay warehouse and for the new shipping provision. The expansion was carried out in several construction stages during ongoing operations and without any interruptions to operations.
Highlights
The scope of supply of HÖRMANN Logistik includes steel racking construction, stacker cranes, conveyor technology, control technology as well as the WMS HiLIS.
- Two-aisle high-bay warehouse
- Dimensions 64.48 m x 35.55 m x 32.76 m (L x W x H)
- Storage capacity: 13,056
- Depending on pallet size, pallet storage up to 10 deep
- Two 1-mast stacker cranes with wireless channel trucks
- Conveyor system with connection to production and with dispatch provisioning
- Conveyor technology platforms