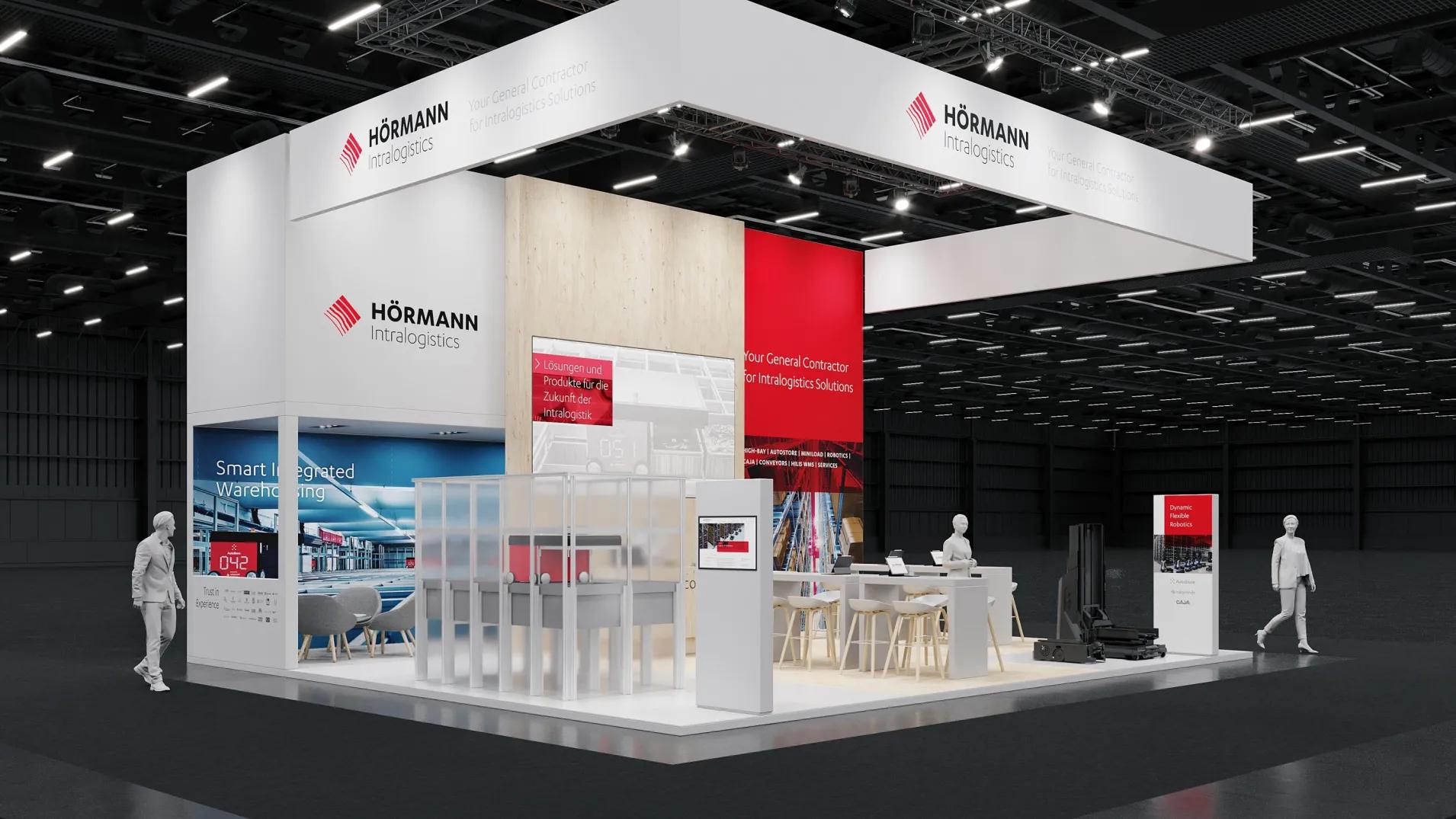
Smart Integrated Warehousing
HÖRMANN Intralogistics @LogiMAT 2024
Dear business partners,
not long now until the industry's big annual meet-up from 19.-21. March in Stuttgart!
Have you blocked your calendars and picked your LogiMAT activities yet? Make sure to stop by Hörmann Intralogistics booth in hall 1, J47.
We look forward to discussing the latest trends, projects and ideas and show our portfolio for smart integrated warehousing 🤗, together with our partners AutoStore and Caja Robotics.
Get your free ticket and meeting slot now!
Best regards
Your HÖRMANN Intralogistics Team
This year´s experience
Smart Integrated Warehousing Fluent, dynamic, multi-solution concepts for fully automated intralogistics with
|
HÖRMANN Robotics Lounge
|
LogiMAT 2024 Presseportal
Referenzen integrierte Groß- und Kleinteillager
Referenzen Hochregallager und Kleinteillager