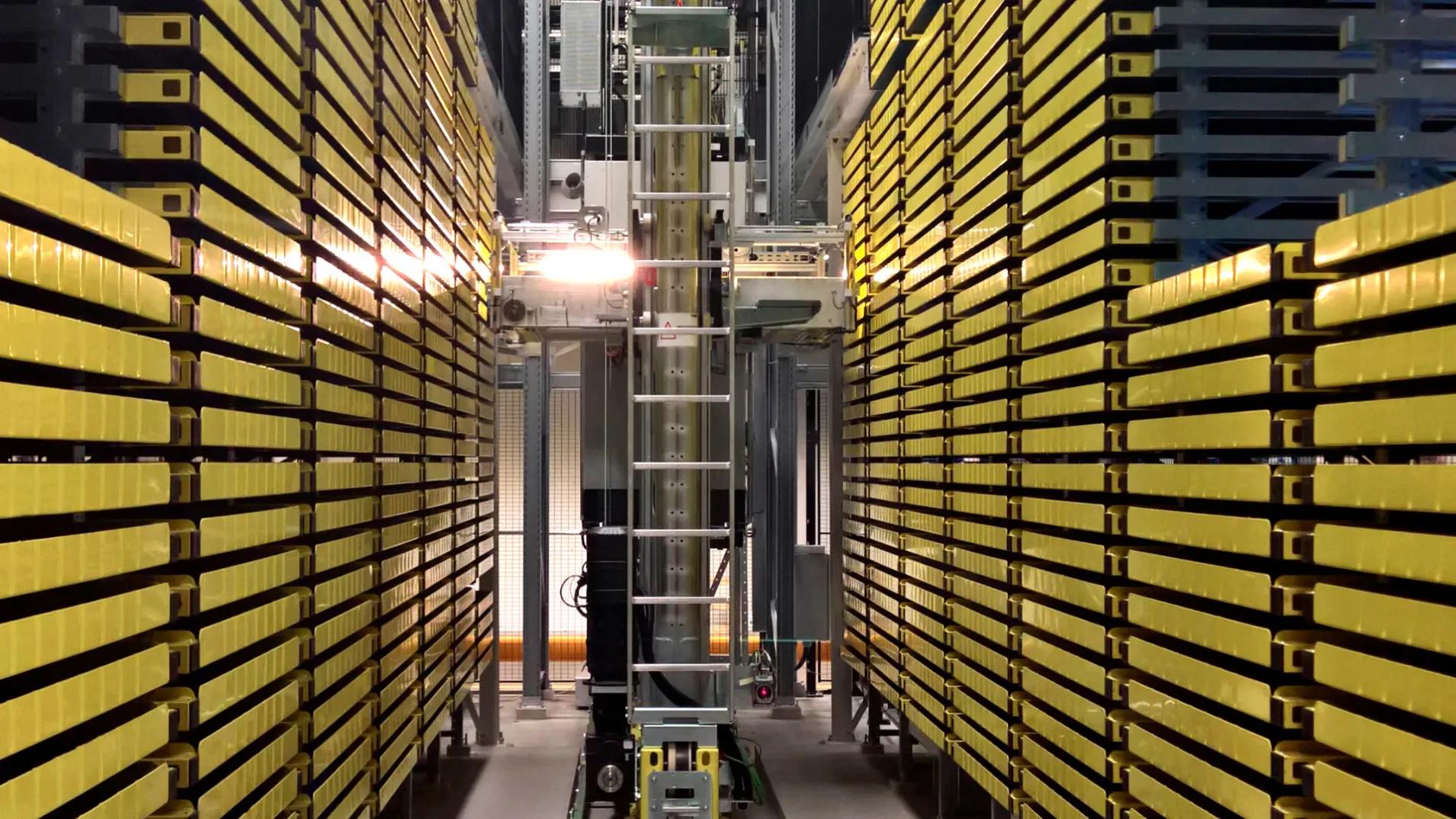
Reference Rehau
Automatic tray bearing with extraordinary tray dimensions for REHAU
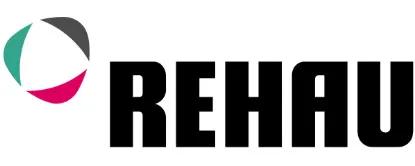
As an innovative system manufacturer and creative development partner, REHAU supports the automotive industry in its efforts to purposefully optimize design, comfort and safety around the automobile. At the Feuchtwangen site, a new automated tray warehouse is to be built in an existing hall as a buffer between the injection molding plant and packaging. HÖRMANN Intralogistics has realized this as a general contractor.
The concept
A special challenge for the conception and technical implementation of the new warehouse are the large-sized steel trays in a medium weight class. The trays can be loaded in 3 different height classes.
The tray warehouse is connected to the injection molding area and packaging via conveyor technology. Empty trays are transported either directly from the packaging or also from the tray storage to the injection molding area. At the injection molding machines, robots loosely insert the finished injection molded parts into the empty trays in a variant-clean manner. A conveyor system transports the filled large trays to the infeed stacks of the automatic 2-aisle tray warehouse with as little vibration as possible so that the load does not slip. The storage and retrieval machines (SRM) take over the trays and store them dynamically according to a sophisticated strategy to achieve optimum warehouse utilization with maximum variability of tray loading (loading height). If necessary, the packaging requests the required goods via HOST interface, which is retrieved by the RBG and served via the conveyor system at the packaging area. The warehouse control and management is carried out by the Warehouse Management System HiLIS, which communicates via interface with the REHAU HOST system. The HiLIS plant visualization supports the operation and control of the entire system with simple, ergonomically designed masks in real time.
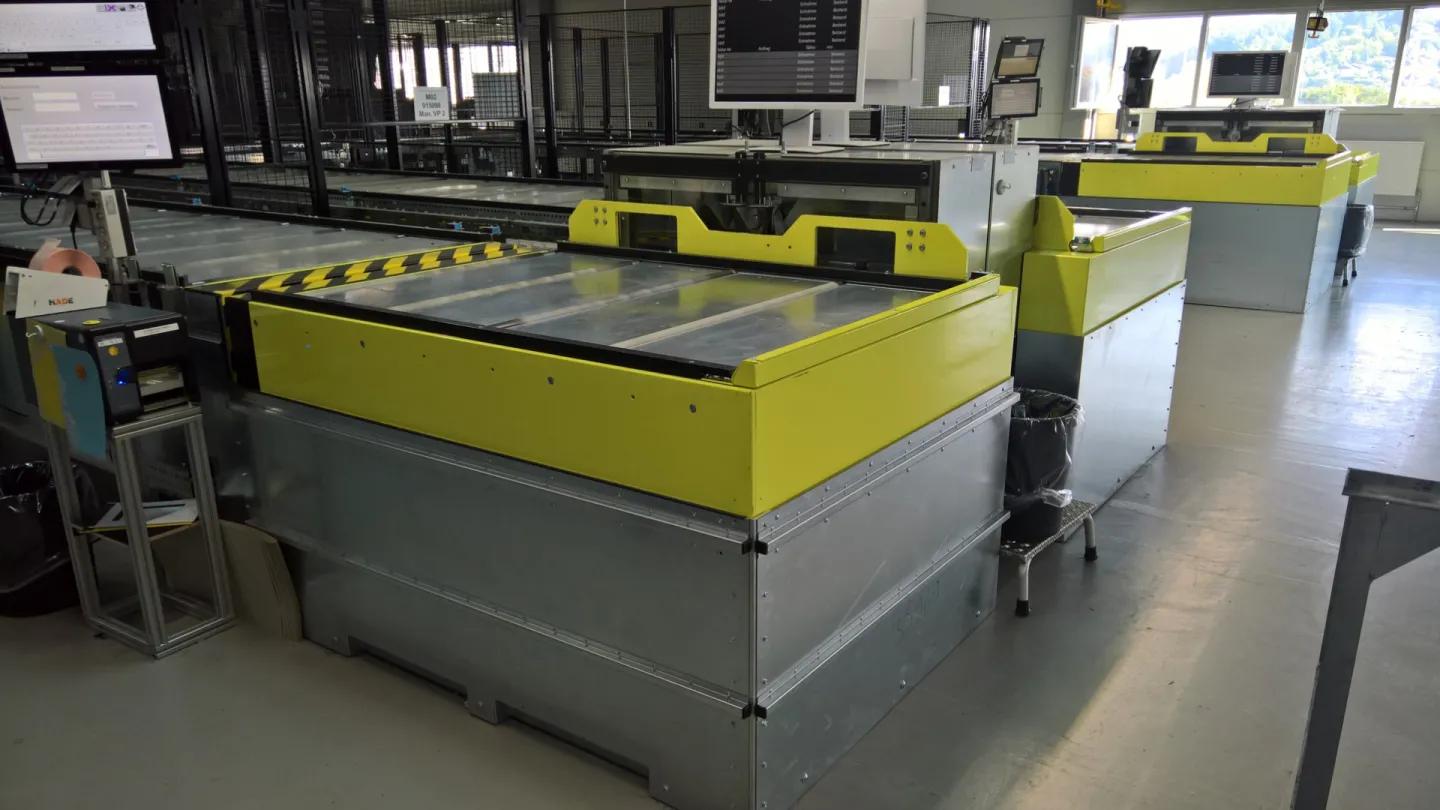
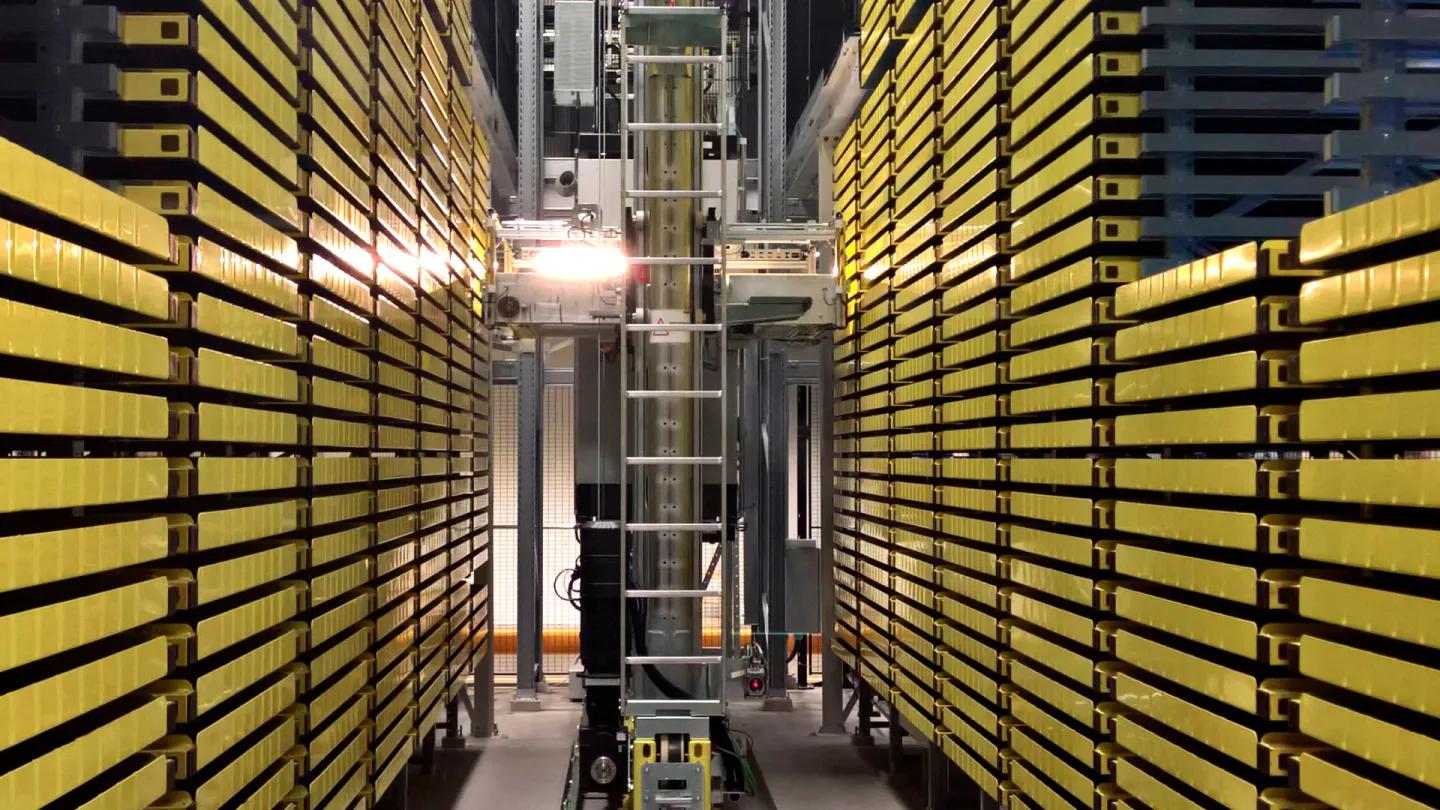
Facts tray storage
The scope of supply of HÖRMANN Intralogistics includes shelf steel construction, platform construction, tray conveyor technology with connection to the injection molding plant, tray storage and packaging, stacker cranes, control technology for stacker cranes and conveyor technology as well as the warehouse management and control system HiLIS with plant visualization.
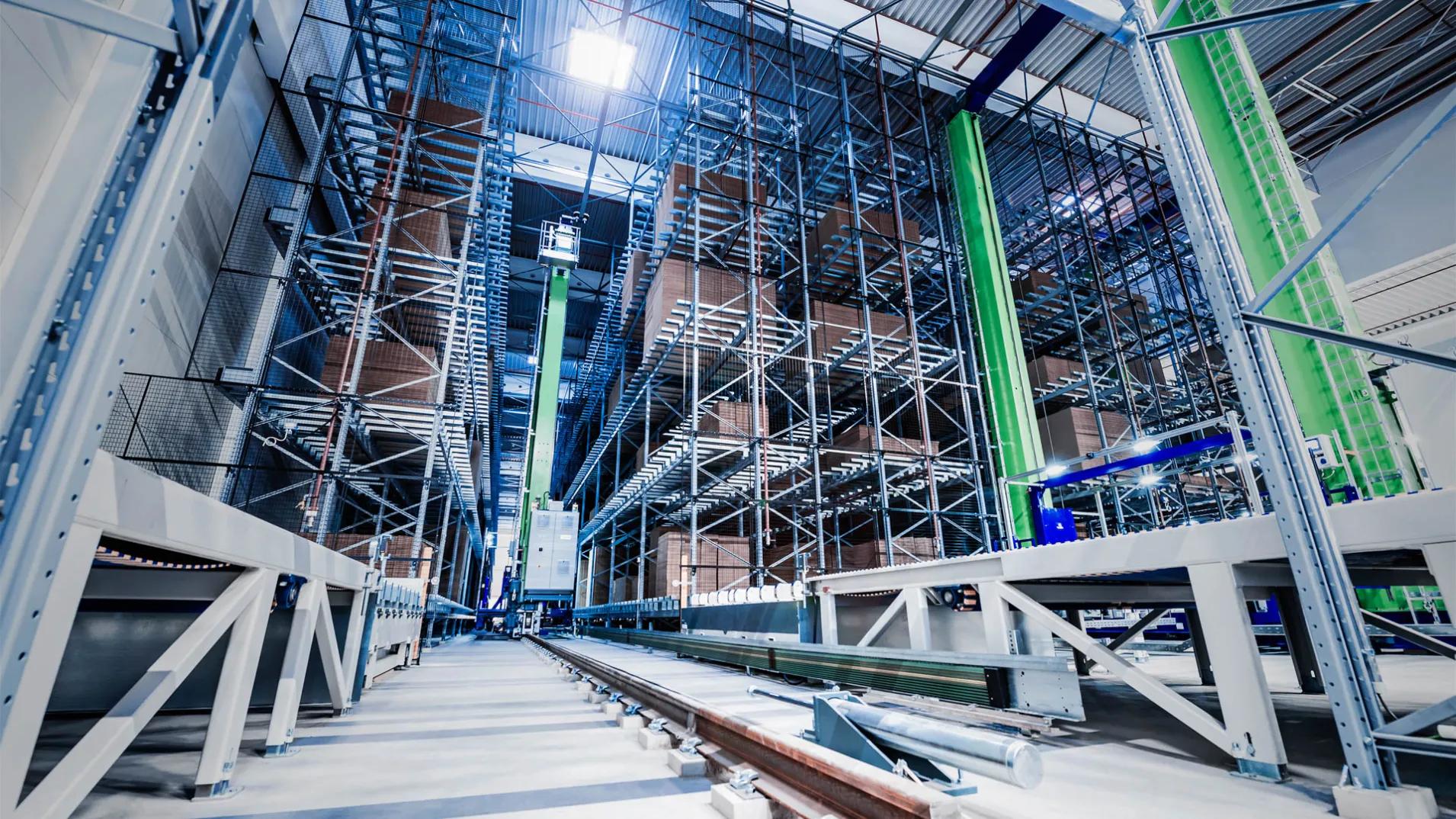
404 – Unfortunately, this page doesn't exist
This link leads to a subpage that does not exist (anymore). Maybe you just made a typo? Then please try again.
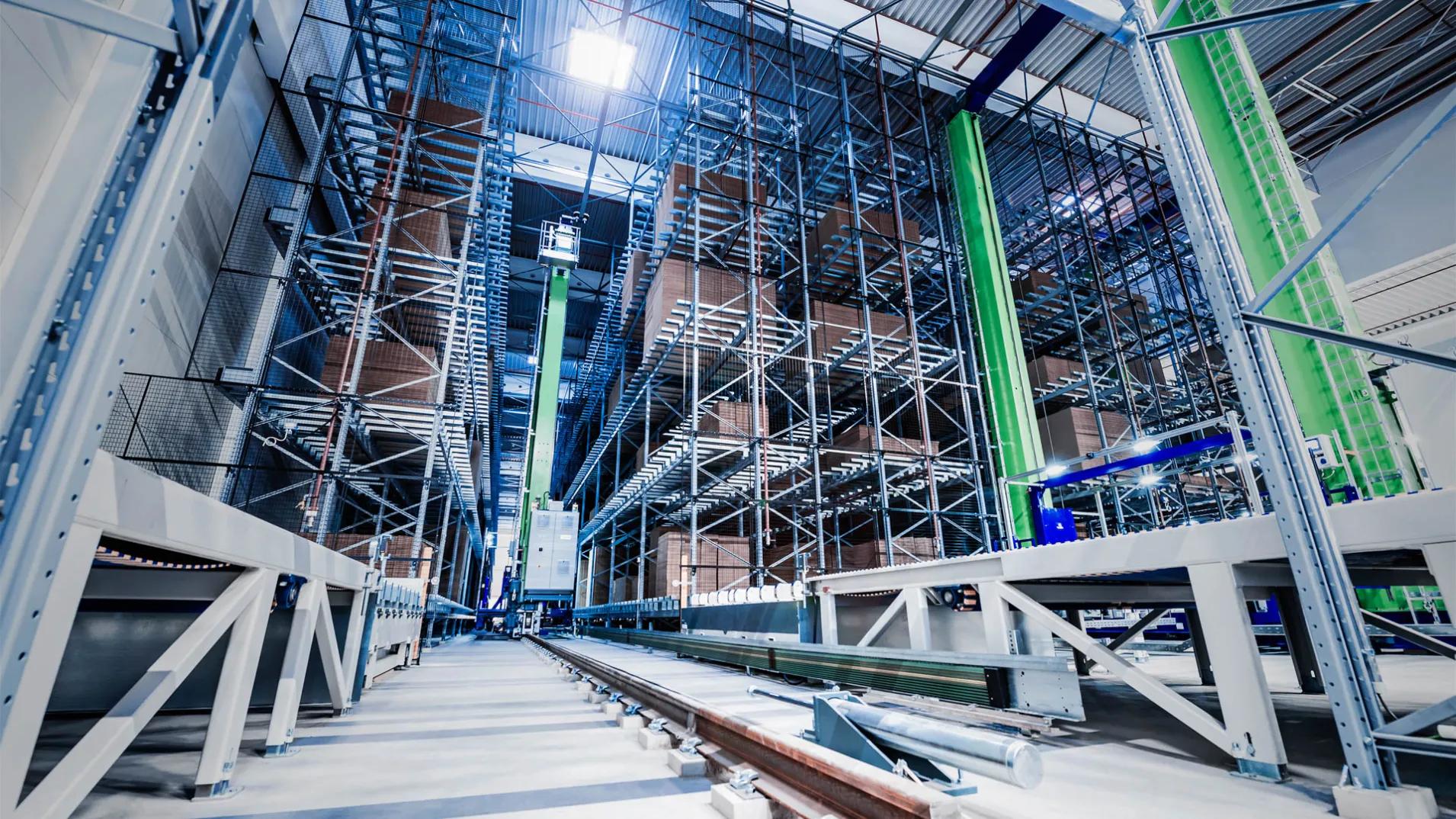
Soon you will find the english translation here
We are still working on this content at HÖRMANN Intralogistics. But soon there will be fresh content to see here.
Are you interested in comprehensive intralogistics solutions from a single source? Do you need comprehensive services for your machinery or would you simply like to optimize the cycle times in your processes? Or anything else … We are your partner. Feel free to browse the German language version of our Site get in contact directly:
Search Test 1 EN
EN: Blabla ist das Wort was ich suchen möchte