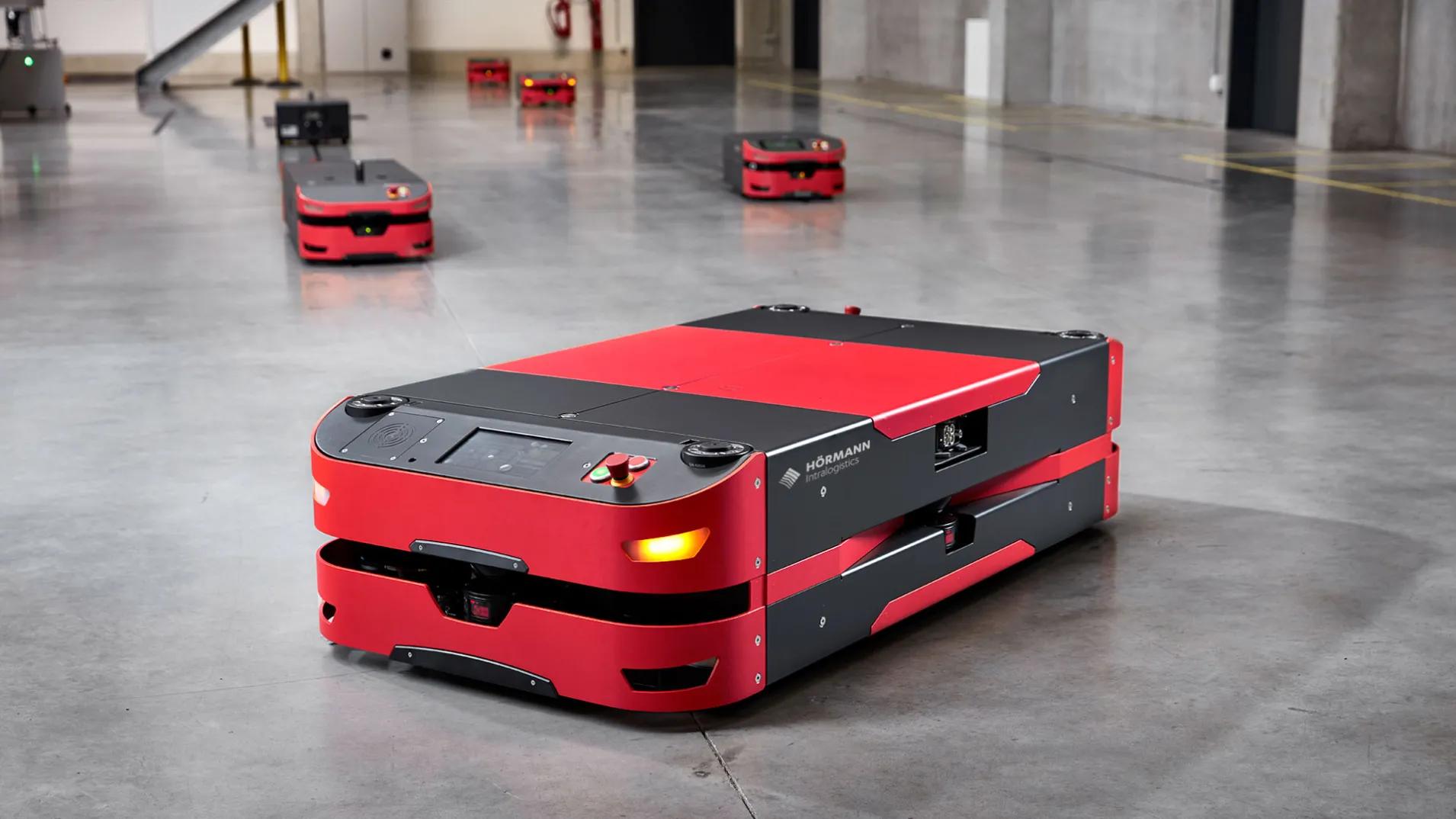
Robotics
Moving Racks solution - goods-to-person (logistics) with robots and racks
Constantly increasing item volumes, along with ever increasing demands for fast and efficient order picking, pose new challenges for classic warehouse logistics. Working with SAFELOG, HÖRMANN Intralogistics has developed an innovative moving racks system for picking process automation, even for bulky goods, based on the goods-to-person principle.
Mobile transport robots (AGVs) transport the goods in modular racks, sequentially and just-in-time from the storage areas to the picking stations. HÖRMANN Intralogistics’ smart HILIS Warehouse Management System controls and monitors all picking processes to guarantee maximum performance.
The advantages at a glance
- Reduced staff and walking distances
- Flexible and modular expansion at any time with more AGVs or racks
- Picking areas can be supplemented by support systems, e.g. pick-by-light
- In multi-order picking configuration, the HiLIS WMS offers additional possibilities for increasing picking efficiency with intelligent batch formation.
What are Moving Racks?
Moving Racks replace or supplement traditional picking areas (man-to-goods) with high staffing levels and long walking distances, with an efficient, flexible system of modular shelving (racks) that are presented in a timely and sequential manner to the picking staff.
Rack transport from the storage areas to the picking workstations is carried out by mobile transport robots. This means that all system picking processes are intelligently contolled and monitored by software to ensure maximum performance and timely delivery.

Our Partner
The ever-increasing volume of items, added to the ever-increasing demand for fast and efficient order picking pose new challenges for classic warehouse logistics. With a range of robotic solution it’s possible to achieve significant cost savings and increase resource efficiency.
In the ideal case, this would involve combining several systems, such as a automated CubeStorage system by AutoStore for storage and retrieval and an AGV shuttle system for the subsequent connection to the packaging line. For these, as well as for stand-alone scenarios, we work closely with our partner Safelog, which manufactures autonomous shelf-lifting robots.
The solution in detail
Storage Area
In the HÖRMANN Intralogistics Moving Racks system, the storage area for all goods consists of the individual racks on their storage spaces. Different types of standardised racks can be combined with various interiors (e.g. EURO pallet, shelf or grid) or configured as individual racks.
All standard racks have the same 1280 mm x 900 mm footprint and a height of up to 2500 mm. The moving racks are placed in a grid layout with travel paths in between in the storage areas. The grid layout can be flexibly adapted to different local conditions, around obstacles or in separated areas.
In addition, areas close to the pick zones can be reserved for fast-moving items.
Maintenance and loading area
Battery charging stations for mobile robots are built-in to the Storage Area, and can be distributed and placed according to the available connection options. This way, mobile robots on charge are available for transport operations without an additional approach route. The robots manage their charge status independently, and always approach the charging stations in good time.
Picking Area
The Picking Area consists of one or more picking workstations and associated buffer locations. Each picking area is connected to the storage area by defined travel paths. The workstations themselves can be individually designed.
In the standard configuration, a workstation comprises two rack storage locations. This means the rack that follows can already be staged during a pick process. The staging areas are separated from the MA work area only by stop bars on the floor, to permit optimal accessibility of the moving racks.
In addition to the rack staging areas, the workstation includes a work table with a flat-screen display showing the HiLIS picking interface and target locations for the picked items. Destination locations can be floor carts, conveyor elements or pallet locations for example.
HÖRMANN Intralogistics - Moving Racks
The control system allows omnidirectional travel, so that a robot can move in any direction at any time. This increases the operational flexibility of the vehicles, as they can be maneuvered in very confined spaces. It also makes it possible to turn racks on the spot.
Mobile AGV robots by SAFELOG
SAFELOG mobile transport robots are used to transport the racks. With a height of just 340 mm, these driverless transport vehicles are equally suitable for driving under the racks as they are for transporting pallets or wire mesh boxes. The weight of the Topload can be up to 1,500 kg.
SAFELOG has developed an agent-based control system for the mobile robots, through which the individual vehicles communicate with each other and with the surrounding production and logistics facilities. This ‘swarm’ intelligence of the transport vehicles controls both route coordination and task distribution between the devices. This means they do not require a higher-level control station for their operation. The software configuration is customer-specific to the respective requirements and linked to the HiLIS WMS for order control.
To achieve the highest possible technical availability of the overall system, various navigation types are available, and can also be used in combination. Depending on the application conditions, magnetic track, RFID tags, virtual track and contour navigation are used individually or together as a hybrid navigation system.
Contact us now
Bring your company into the advancing world of innovative logistics solutions. With our moving racks and mobile robots, you can significantly increase the efficiency and flexibility of all picking operations
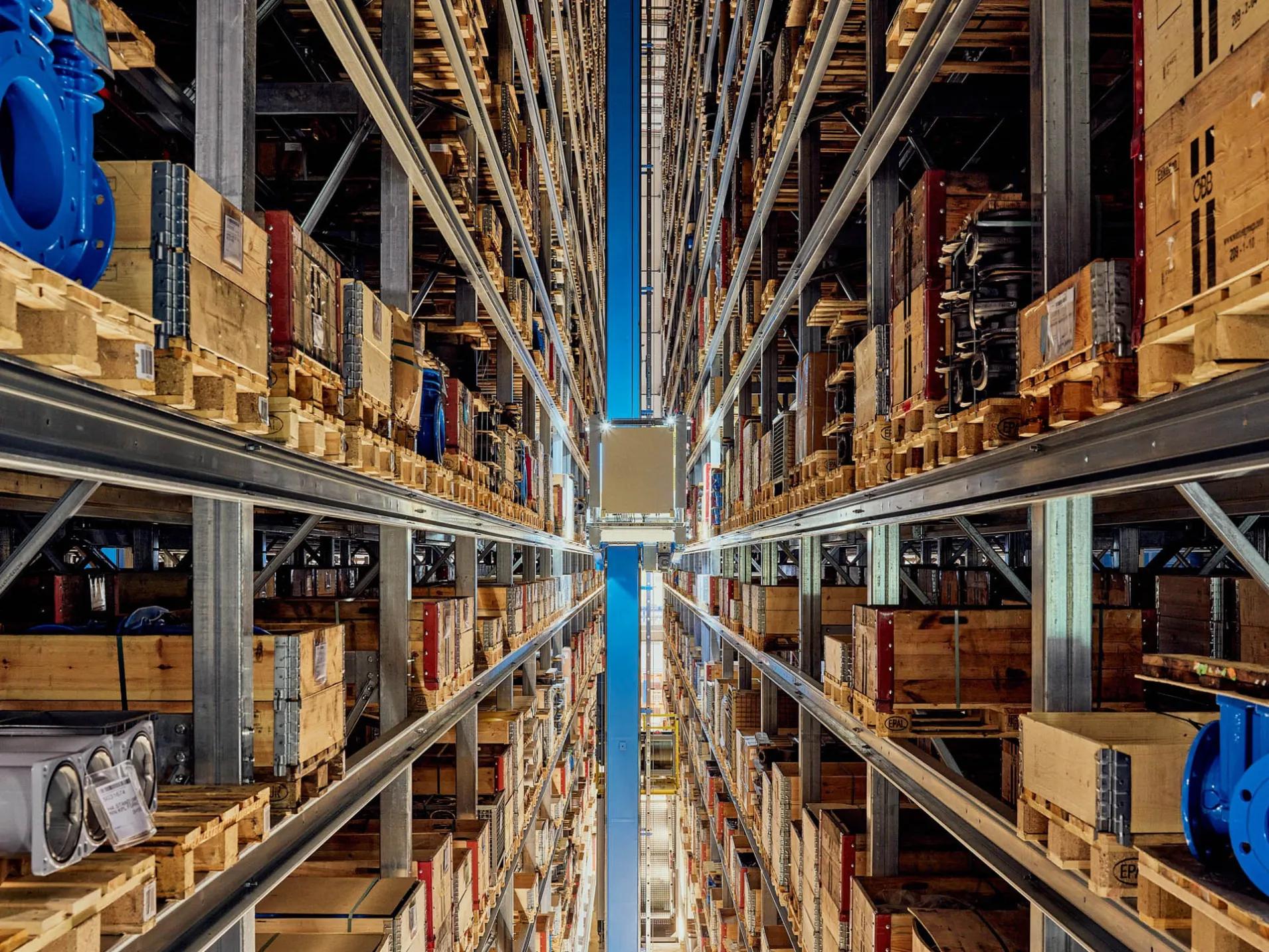
Reference HAWLE
Automated high-bay warehouse for supply and disposal of production at E. Hawle Armaturenwerke in Austria
The Hawle Austria Group produces and distributes heavy-duty valves worldwide. The products, which are designed for generations, are used in residential water management from the source to the house connection. The Hawle Austria Group includes 12 subsidiaries in Austria, the Czech Republic, Poland, Slovakia, Russia, Turkey, Italy, Great Britain and India.
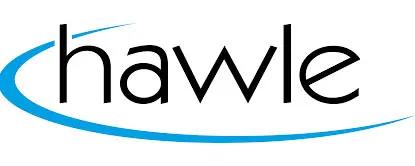
A new logistics warehouse has been built at the E. Hawle Armaturenwerke GmbH production site in Frankenmarkt, Upper Austria, in order to reduce the rented external warehouses as far as possible. The realization of the 5-aisle high-bay warehouse as well as the connecting conveyor technology has been taken over by HÖRMANN Intralogistics as general contractor. IGZ, the SAP engineers from Falkenberg in Bavaria, implemented the entire logistics processes in SAP EWM with direct control of the warehouse technology by SAP MFS.
Concept
In the new high-bay warehouse, raw and semi-finished parts are temporarily stored for production or for staging in shipping. The production connection is made directly from production via a new, double-level conveyor system for pallets. In addition, a loading and unloading station is planned in the outer wall of the new logistics hall, which can be reached from the yard with forklifts and is approached dynamically by SAP EWM in exceptional situations to ensure production supply at all times.
The 5-aisle high-bay warehouse is equipped with five aisle-bound storage and retrieval machines (SRMs). These have telescopic forks for double-deep storage. Three-bay side-by-side storage is provided per rack compartment. The storage and retrieval stacks of the high-bay warehouse are connected to a loop conveyor line that extends into the logistics hall to pick up or drop off goods. All storage and retrieval machines are equipped with a compartment fine positioning system that detects both the front and rear z-positions.
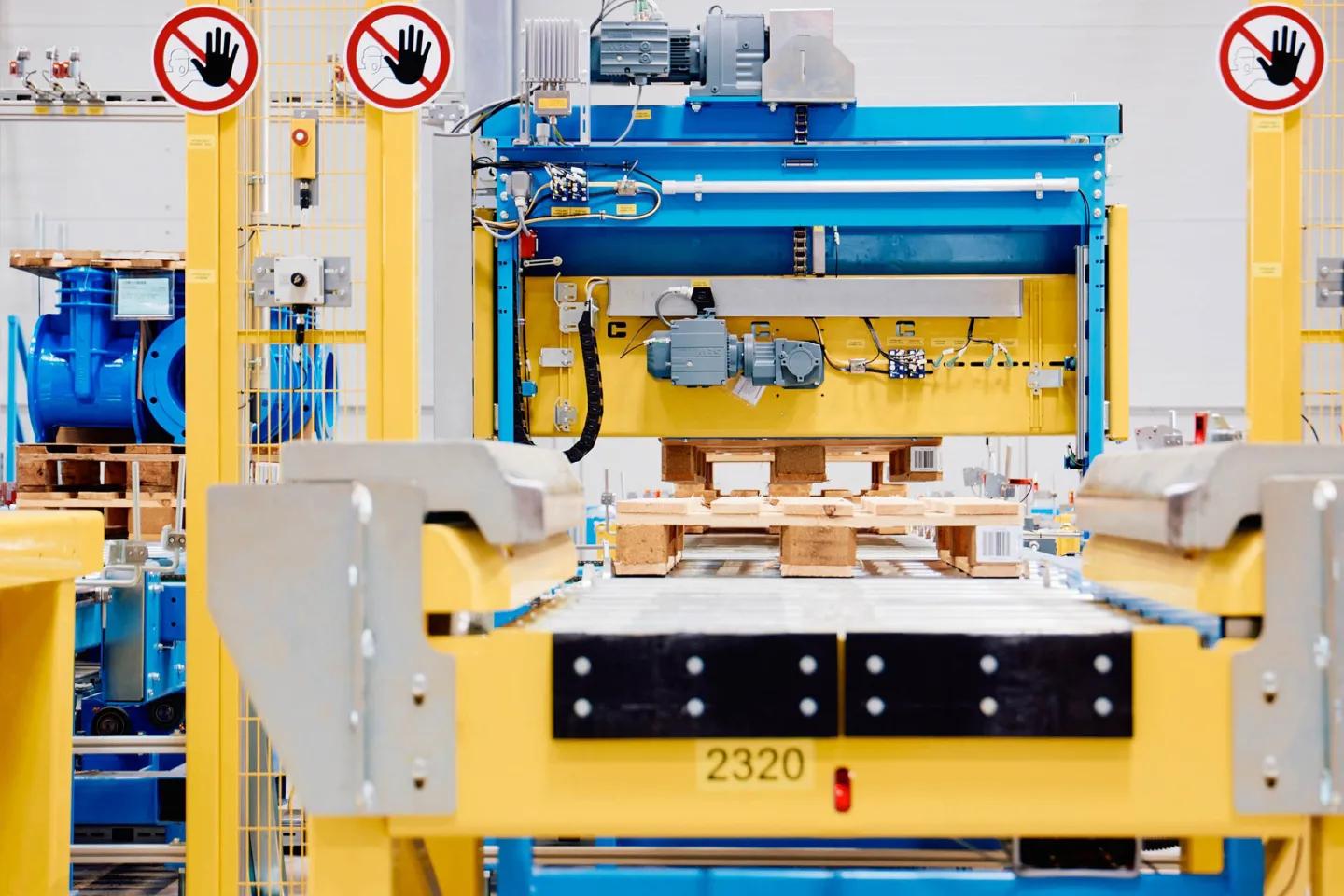
Goods receiving and shipping for different load carriers
At goods receiving, normal load units are fed onto three conveyor sections with weight and contour control. Grid boxes are only fed onto the middle conveyor section. There, the loading station is fully automatically equipped with a wooden lower pallet onto which the wire mesh box is placed
The empty pallets required for this are held in stacks at a buffer station and transported individually towards the set-up station as required.
Highlights
- 5-aisle high-bay warehouse 70 x 40 x 29 m (L x W x H)
- 5 aisle-bound stacker cranes in single-mast design with telescopic forks for double-deep storage
- 32 pallet insertions and removals per hour per stacker crane
- Connecting pallet conveyor system
- Fire protection and high-speed gates
- Control technology with direct connection to SAP EWM / MFS
- Plant visualization
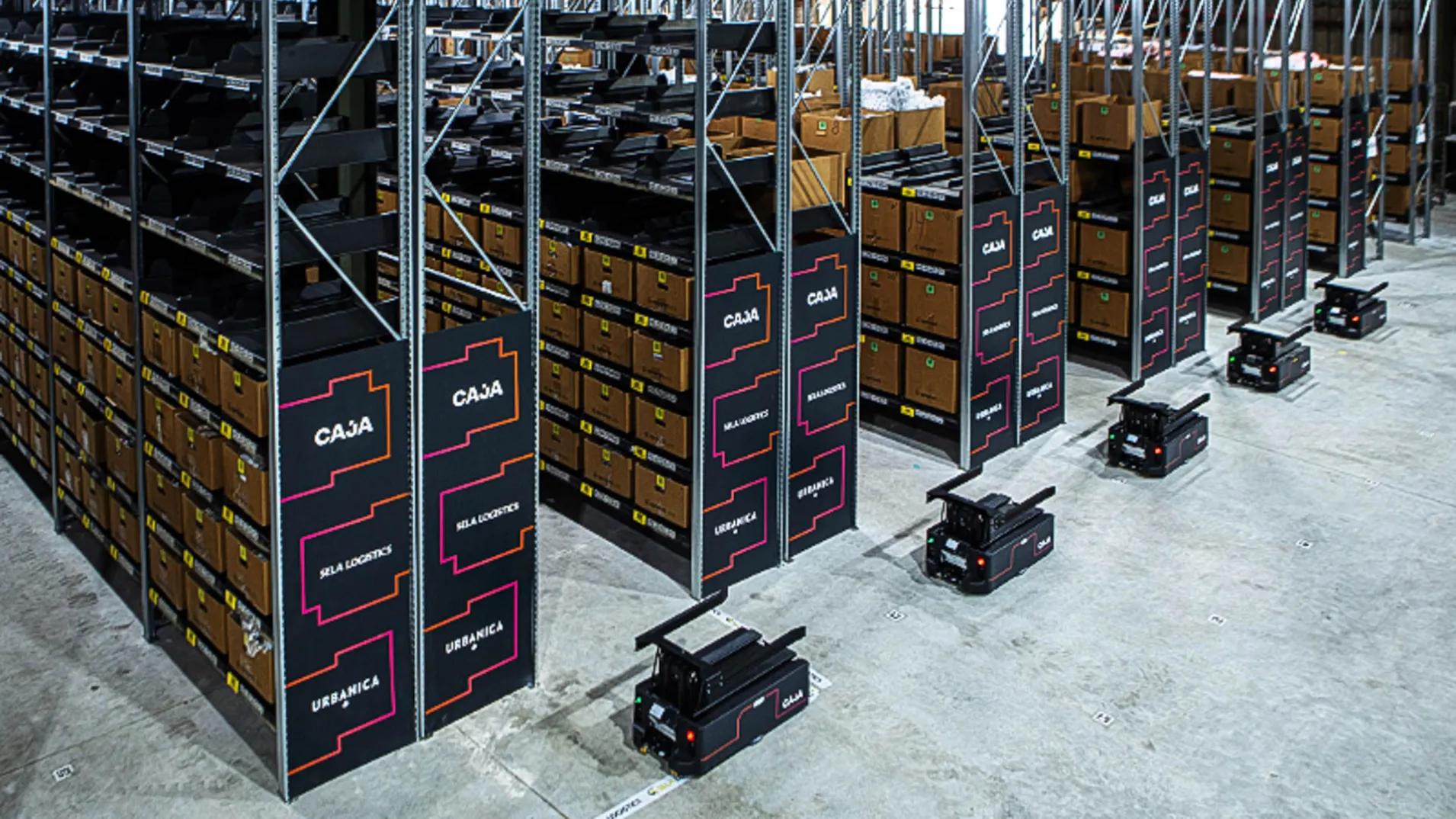
Robotics
Caja Cart & Lift Robotics
When developing automation solutions for fast-moving business areas, it is essential that the systems perfectly adapt to the intralogistics processes and infrastructures. With our partner, CAJA Robotics, we’ve developed an innovative approach using modern software, specifically developed robots that operate according to the goods-to-person principle, user-friendly workstations and solutions for integrating an existing WMS or the in-house HiLIS WMS.
The advantages at a glance
- More efficient order picking
- Reduced order errors and increased inventory security
- Reduced walking distances and manpower
- Robot and cloud software-assisted, AI-based, fully automated order fulfilment
- Scalable, modular architecture which responds lightning fast to order peaks or drops
- Flexibly adaptable shelf structures as new lines of business emerge
- Use of own bins possible
- Simple commissioning
All you need to know about Caja transport and lifting robotics
Brochure - Caja Transport and Lifter Robotics
What is Caja?
Caja's transport and lifting robots handle goods-to-person logistics. In this configuration items from a picking warehouse are delivered with bins or pallets on software-controlled, intelligent robots. After the items have been removed from the storage location, the bins or pallets, either empty or filled with remaining items, are transported back to the warehouse and sorted there.
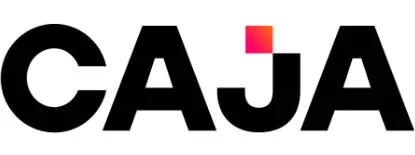
Our Partner
The partnership between the two companies, which began on the German, Austrian and Swiss markets, focuses on the closest possible cooperation to offer and implement smart warehouse solutions. With Caja Robotics’ innovative and intelligent warehouse technology, HÖRMANN Intralogistics continues to expand its portfolio.
Caja Robotics solutions are designed to meet the particular demands of highly dynamic warehouse processes. One particular advantage is that Caja Robotics applications are very flexible and scalable with high goods throughput. They can be easily implemented and adapted to the customers' existing frameworks, and offer immediate benefits coupled with our highly efficient, customised warehouse systems.
The solution in detail
Robots working together
The transport and lifting robots are connected to the backend via radio. Sensors determine their position and detect obstacles or interference. Using software, hardware, and sensors, they interact with their environment to maximise the output of the fulfilment process.
4D navigation
The robots are controlled by cloud-based, decentralised software with multi-layered algorithms. This guarantees the success not only individual isolated tasks, but optimisation of the entire warehouse operation as well . Through artificial intelligence and machine learning, the solution continually adapts to the conditions.
Autonomy
In certain processes, the robots make their own decisions without software commands. Aided by sensors, for example, they can react to events in the queue during order picking.
Temperature
To adapt to different industrial sectors, Caja robots are designed to operate in all temperatures, for example in cold storage for food. In sterile cleanrooms, automated transport robots offer great advantages.
WMS integration
Caja software seamlessly integrates with HiLIS and other existing WMS solutions, enabling accurate and time-optimised flow of goods.
Swarm management
The cloud-, algorithm- and AI-based software ensure continuous order, bin and fleet management of all robots located on the warehouse floor.
Ergonomic workstations
While being extremely automated, Caja Robotics nevertheless still depend on human-machine interaction. The fleet is equipped with user-friendly workstations, for performing tasks like inbound processes, replenishment organisation, returns, or bin consolidation.
Shelf adapter
The system includes Shelf Adapter Units (SAU) that simplify processes, eliminate decanting and extend bin life.
Contact us now
We can accompany you throughout the entire consulting and order process: first, we analyse your warehouse processes based on all the information you can provide, then develop a simulation and custom solution design. Based on this we can calculate costs and possible savings and move on to the quotation phase. Our logistics experts manage every stage of complex automation projects as general contractor.
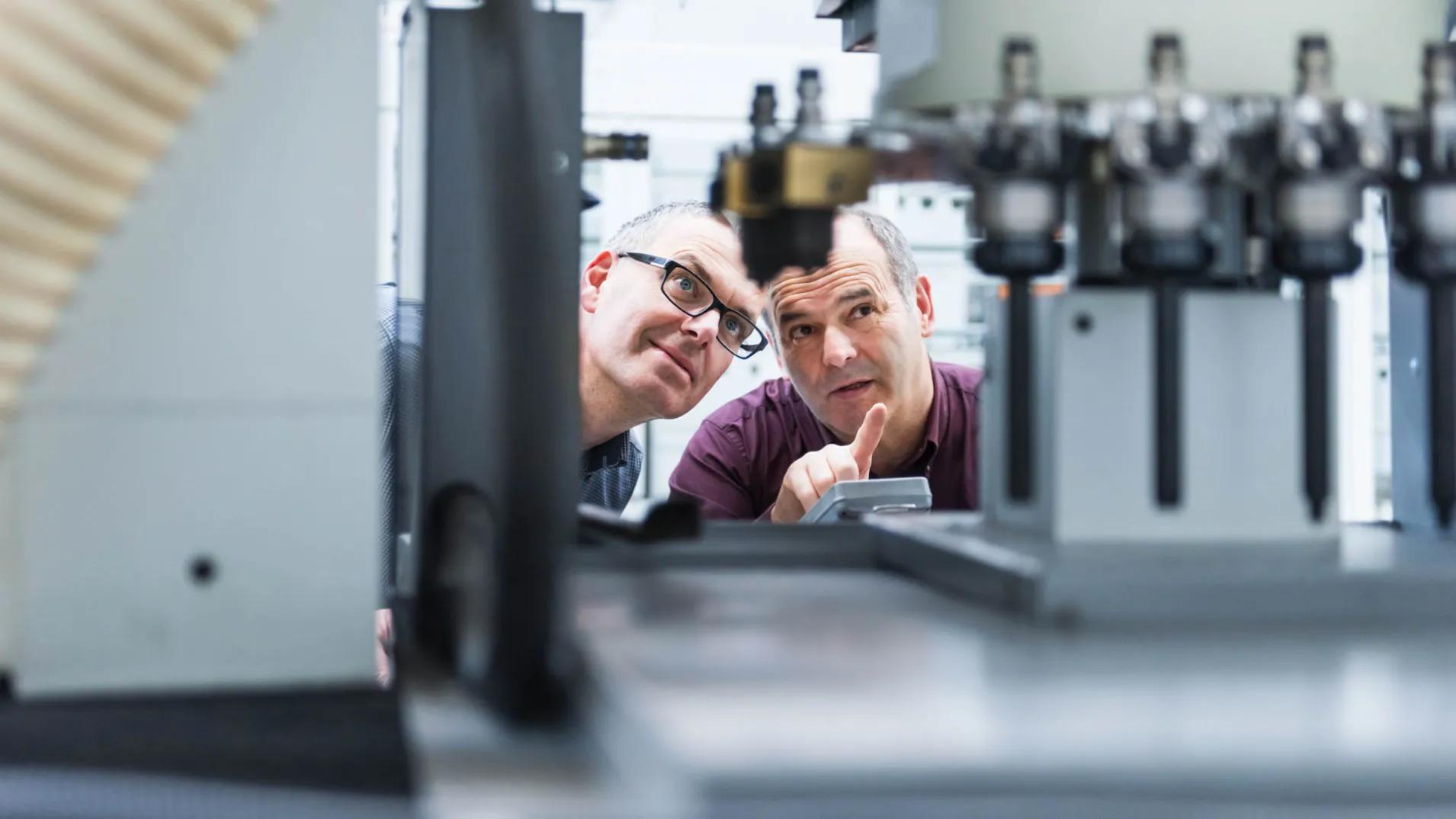
Services
Partner of industry
Our single-source provider industrial services include personalised, competent solutions. Our professional teams with vast experience in planning, production-and assembly know exactly what you need.
As a partner to industry, we provide all-round services geared to the life cycle of automated manufacturing and production equipment. From conception, realisation, assembly and commissioning of machines and systems to the relocation or modernisation of existing production facilities, not to mention optimisation and maintenance.
Our services at a glance
- DGUV examinations
- Maintenance
- Industrial assembly
- Measurement/fixators
- Machine relocations
- Relocation services
Operating equipment and systems safety through competent DGUV inspections
The acronym DGUV stands for the German Social Accident Insurance agency, an organisation of 27 accident insurance funds and nine commercial employers liability insurance associations. DGUV Regulation 3 regulates the testing of electrical equipment and systems used in industry.
On request, we can create a basic inventory of all devices to be tested or check the existing data. Our files include all devices. This way, customers prompt notice from us when the next test cycle is due.
The devices are not only tested, but can be repaired immediately if necessary and according to budget. All documentation, including the legally required protocols, are available at all times - in hard copy format and, depending on the customer requirements, on server / data carrier etc.
This means our customers always work with approved tools and machines and, if necessary, are legally protected in the event of accident, given that all required tests are carried out and documented.
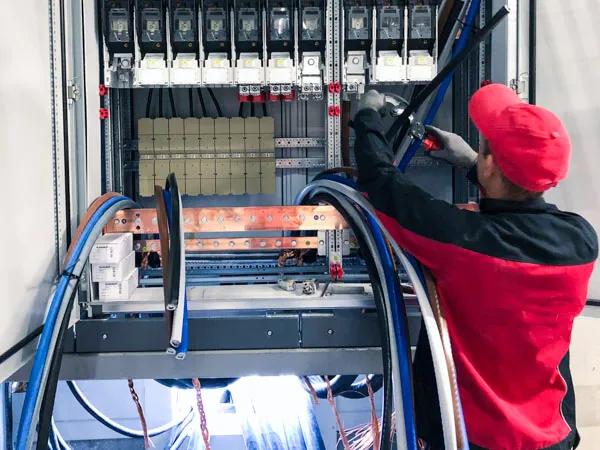
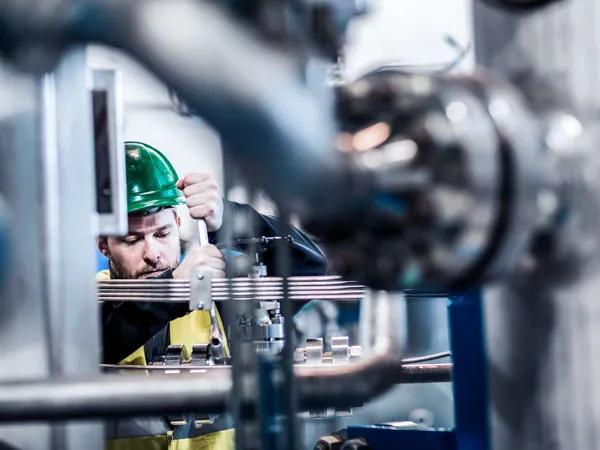
Interruption-free processes and production sequences through continuous maintenance
Regular maintenance and servicing is mandatory for ensuring trouble-free processes and production sequences. It is likewise fundamental for maintaining high production equipment availability, minimising downtime and saving costs.
To sustainably reduce downtime and prevent unscheduled maintenance, we offer preventive maintenance services at the highest level, through our team. We check and document the status of all machines and systems, evaluate them and use this information to identify when maintenance and servicing work needs to be scheduled at the earliest possible stage. This gives customers the advantage of being able to include maintenance and servicing work promptly in their production scheduling.
Of course, the team also takes care of the physical execution of all maintenance and servicing work. From inventory, to determination and calculation of individually coordinated maintenance intervals, to maintenance or repair work.
Industrial assemblies from single machines to production lines
With our specialised staff, we carry out mechanical and electrical industrial assemblies as complete service packages according to customer schedules and design specifications.
We see ourselves as a general contractor, organising all the necessary assembly equipment (including crane, forklift, lifting scaffolding, tools), to ensure professional and timely execution. This also includes utility installations like air and water.
Customers are accompanied by a single contact all the way up to commissioning and, if required, we can provide support through ongoing production assistance. Among others, our reference projects include installations for the automotive and supply-chain industry, materials handling, machine tool and packaging industry. We also offer experienced support for decommissioning services, including the professional disposal of all materials.
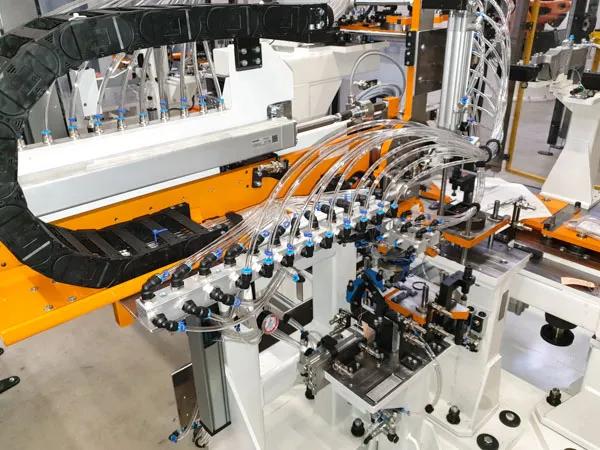
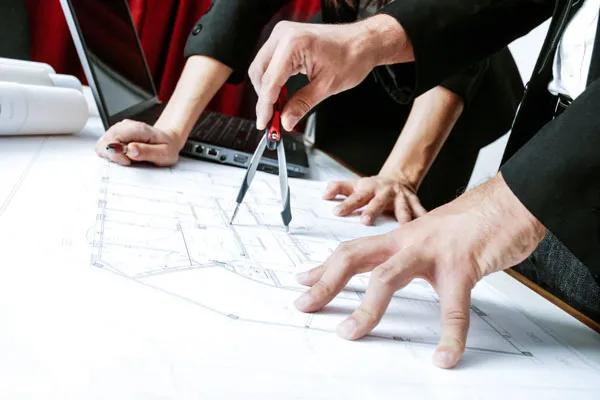
System assembly and machine conversion services
As an important ancillary service in the area of system assembly and machine conversion, we can measure the systems where they are to be installed, marking out the machine axes, contours and adjustable feet, inserting fixators and/or base plates as a fixed and finished service.
Our services at a glance
- System measurement based on dimensioned layouts provided by the manufacturer
- Plotting of machine axes, contours and levelling feet, using in-house laser measurement technology
- Assigning subcontractors for drilling work
- Installation and alignment of fixators and/or base plates
- Assignment of subcontractors for grouting work
HÖRMANN Intralogistics has years of experience and trained personnel for system measurement. We have been providing this type of service to machine manufacturers and equipment suppliers to the automotive industry for many years.
Machine relocation
The relocation of machinery and equipment presents many significant challenges to companies. From planning to logistics and the actual implementation, the necessary human resources and technical equipment are often lacking, meaning that even an in-house machine relocation can quickly become a difficult task to solve. This is where you need a strong partner.
Whether it’s machine relocation in the course of production changeovers, the relocation of complete manufacturing systems and production lines or the relocation of entire systems, we have been offering our customers all services from a single source provider for over 40 years.
Up to re-commissioning at the new location, we offer customers all services in the areas of planning, decommissioning and recommissiong, including loading and transport. This avoids interface losses and guarantees a smooth operations, monitored by our engineers throughout the entire process.
Machine relocation (in-house)
Modularity in the design of machines and systems has increased significantly in recent years. Modern production systems must have a high degree of flexibility in order to respond dynamically to new conditions, such as new manufacturing specifications. This often results in the need to realign the machinery. Machining centres, conveyor technology and packaging systems can be rearranged on the factory floor.
What sounds simple at first glance in reality requires professional planning, just as with an off-site relocation. In addition to the electrical and mechanical dismantling of the machines, the precise preparation of the new positions on the factory floor is crucial for a smooth start-up.
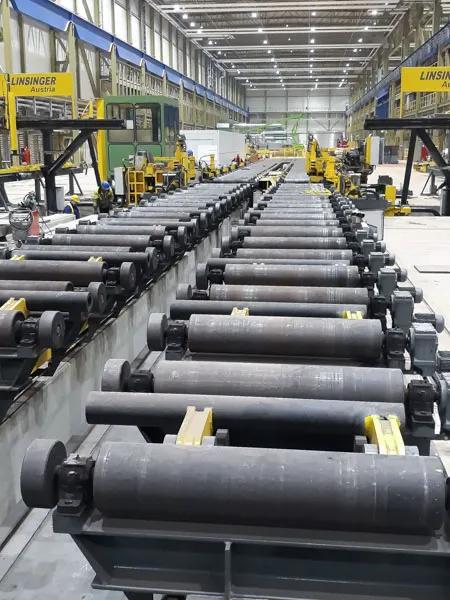
Machine relocation abroad
Above and beyond technical know-how, the relocation of machinery and production facilities abroad demands a high level of organisational services to ensure a smooth operation. Compliance with customs requirements and other international freight transport regulations to name but two.
As an internationally oriented company with more than 40 years of experience in the large-scale industrial sector, we offer customers machine relocations both at home and abroad.
This applies to all services related to your machinery, such as machine assemblies, machine conversions, machine service and much more. Over the years we have successfully provided these services in many different countries (Italy, France, Spain, Scandinavia, Russia, India and China). You too can take advantage of our extensive know-how.
Our services at a glance
- Complete project planning
- Precise surveying
- Backup of control data
- Dismantling of all equipment (electrical and mechanical)
- Loading, securing and transport
- Preparation of the new site
- Remounting incl. positioning and alignment
- Connection and commissioning
- Professional machine acceptance in accordance with the relevant DIN standards
- Creation of safety concepts and CE declarations
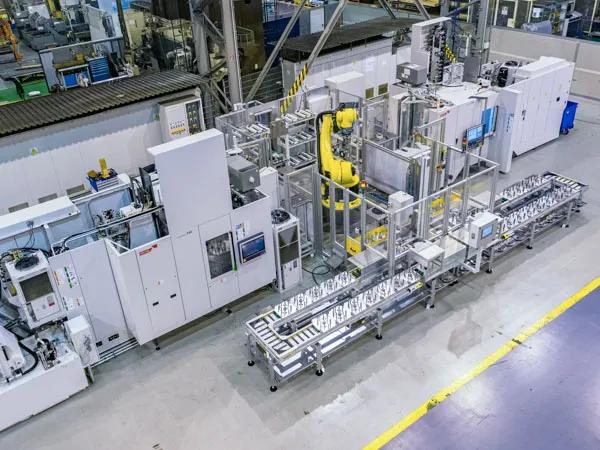
A qualified site team for our customers
On request, we provide customers with a permanent team of specialists directly on site to meet all customer requirements with our portfolio of services. This includes the maintenance and repair of production systems as well as relocations, assemblies and dismantling operations of various kinds. Automation solutions for small projects completes our portfolio of on-site services.
The aim of this on-site service is to support customers as service provider in a close and trusting relationship, so they can focus fully on their core business.
For many years, we have had the privilege of demonstrating our competence and performance at the VW Wolfsburg and VW Salzgitter sites. We have grown thanks to these tasks and put great emphasis on long-term, partnership-based cooperation.
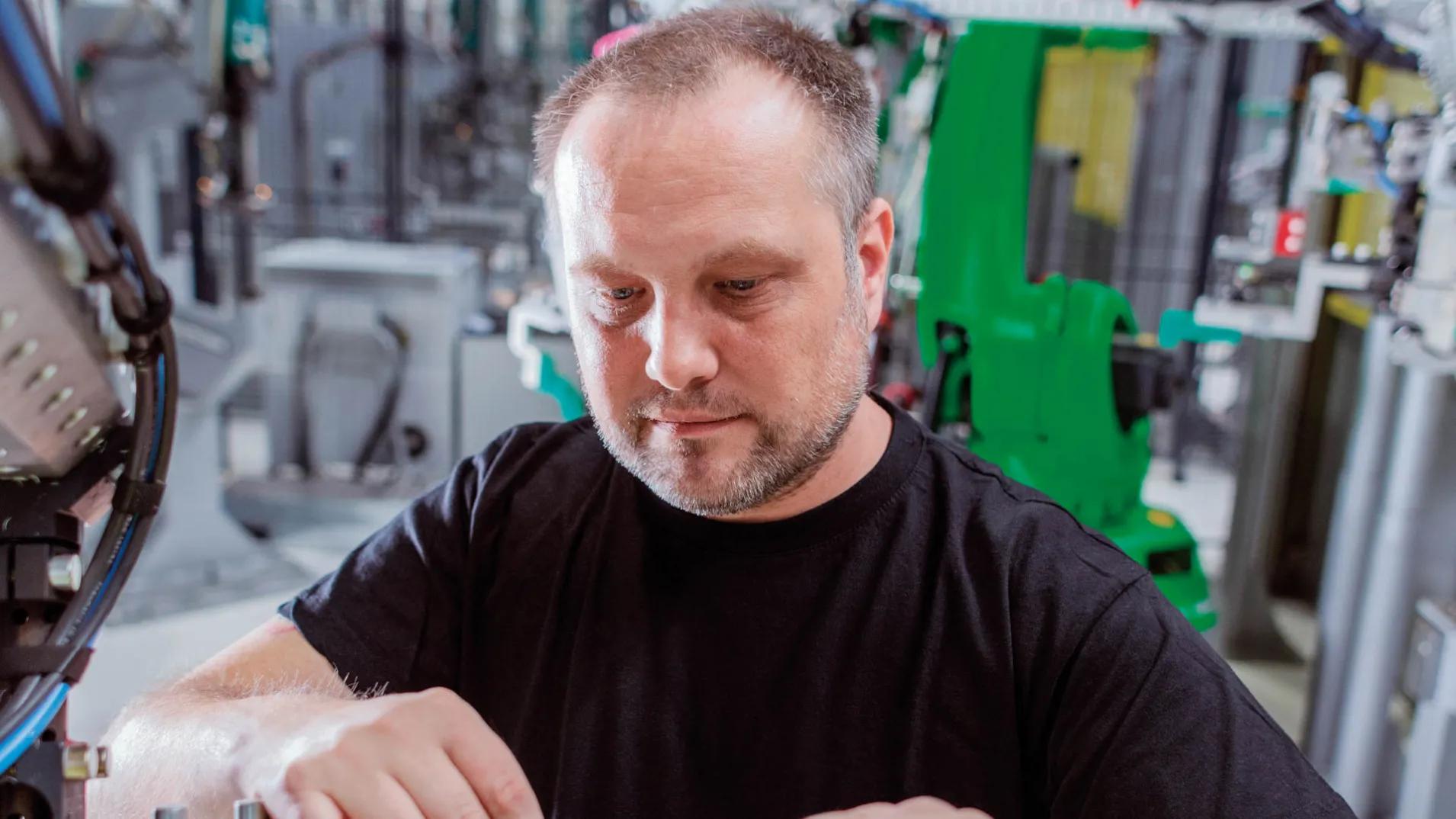
Services
Mechanical Engineering
We cover a wide range of services in the area around your machinery and intralogistics equipment and offer our customers a complete services from a single source provider.
We specialise in processing machines for use in the automotive industry and its supply chain, as well as related industries, and have a well-coordinated service team with many years of experience in the field of machine technology under its belt. In addition to inspection services, we can also provide maintenance and repair services of all kinds. Even for complex intralogistics systems, we can provide full service, from construction to maintenance and modernisation.
Our services at a glance:
- Hydraulic power unit construction and service
- Component and systems assembly
- Hydraulic line and valve assembly
- Pneumatic assemblies
- Trapezoidal and ball screw gearbox repair and overhaul
- Complete machine assemblies
- Machine service, inspection, maintenance and repair
- Machine overhaul (e.g. processing machines
- General overhaul of machinery, equipment and assemblies
- Spindle repair, optimisation and overhaul
- Telescopic cover general overhaul
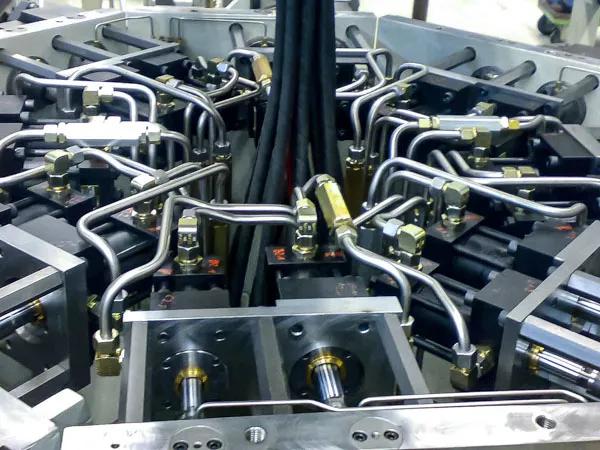
Hydraulic assemblies by the professionals
We lay and assemble hydraulic lines, carry out valve assemblies and are also available to customers for assembling complete systems. Our range of services also includes existing system modernisation. High productivity and efficiency demand ongoing optimisation. We can inspect your ageing hydraulic systems and, if necessary, are happy to modernise them for you.
Through our hydraulic system services, our customers get complete service for their systems from a single source provider. In addition to filter and line servicing, we also offer customers a hydraulic repair service for any kind of fault.
Our services at a glance
- Hydraulic assembly
- Faulty part replacement
- Ageing systems modernisation
- Hydraulic lines service (e.g. replacement of hose lines)
- Filter control
- Filter change service
- Hydraulic fluid change
- Choice of optimal operating medium
- Hydraulic system bleeding
- Hydraulic repairs
You can be sure!
Hydraulic assemblies and services from HÖRMANN Intralogistics:
Pneumatic assemblies
We offer pneumatic assemblies from a single source provider. We can assemble pneumatic lines, valve assemblies as well as the complete pneumatic systems for our customers.
We are equaly happy to provide support in the modernisation of ageing systems. After a professional inspection of your old system, we can provide detailed recommendations about the possible and necessary modernisation works, and an individual quotation.
Using high-quality components from reputable manufacturers & partners, along with constant quality control in accordance with DIN ISO 9001, we guarantee our customers extraordinary levels of quality.
Our services at a glance
- Pneumatic assemblies
- Laying pneumatic lines
- Valve assemblies
- Pneumatic repairs
- Pneumatic system modernisation
- Maintenance and repair
- Pneumatic line service (e.g. replacement of hose assemblies)
- Pneumatic line assembly
You can be sure of our know-how:
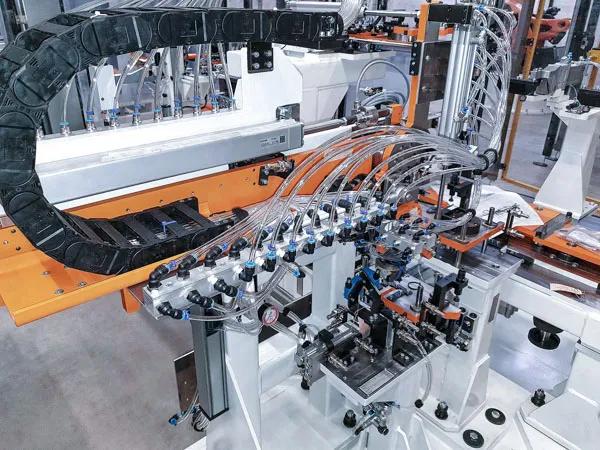
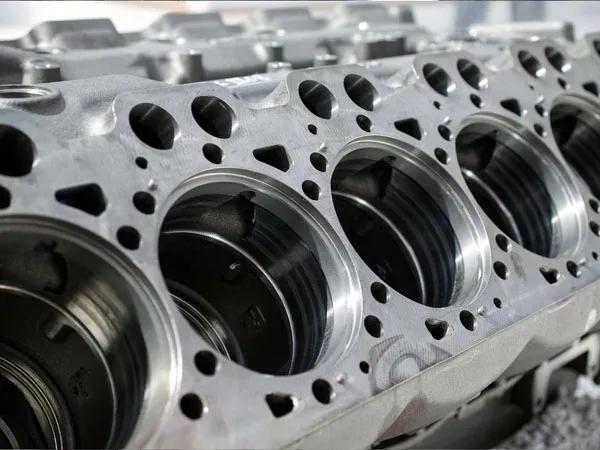
Gearbox Overhaul
Our range of services includes the repair and overhaul of trapezoidal and ball screw gears, lathes, milling and grinding machines.
After an overhaul by our experts, your machine tools will once again be capable of consistently high speeds, combined with an optimal level of precision.
For these services we draw on our many years of experience in the sector.
Thanks to constant quality control in accordance with DIN ISO 9001, we guarantee our customers consistent quality levels and reliability, to your net advantage.
Spindle repair
We can repair, optimise or convert processing machinery motor spindles and external drive spindles. Take advantage of our experience, precision and quality!
Spindle repairs / spindle service
- Belt spindles
- Motor spindles
- Milling and grinding machine main spindles
- Grinding spindles
- Lathe spindles
- Ball screw spindles
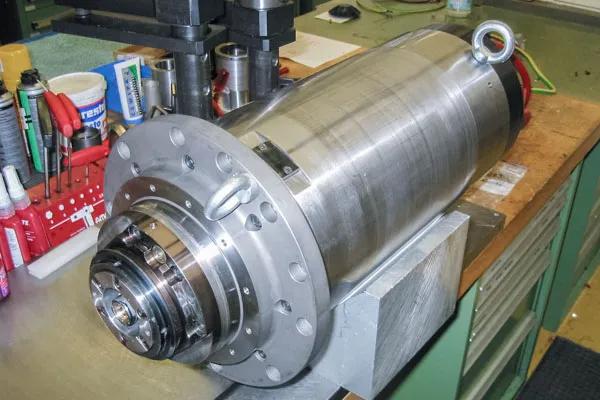
Our repair service includes dismantling and inspection of the spindles, and full test reporting with cost estimates. Once the repair is approved, we replace or rework the faulty parts. Of course, all rotating parts are then finely balanced in accordance with ISO 1940. Following an intensive test run, we provide a test report containing all significant spindle values, such as radial and axial runout, bearing temperatures, motor temperature, vibration values, insulation test result and more.
We can repai spindles made by the following manufacturers - Voumard, Fischer, Weisser, Omlat, GMN, Fortuna, Renaud, Precise, Perske, Jäger, Ibag, Heller, Hauser, Gamfior, Faemat, FAG, Bryant, Colombo, Deuschle, Blohm, SKF, Weiss, Kessler, Junker, UVA, TDM, HSD, StepTec, UKF, DMG, IMT, Jung and others.
As well as the following machine manufacturers - Mazak, Deckel Maho, Mitsubishi, Hermle, Voumard, Jung, Mikron, Vollmer, Huron, Forest, Chiron, Röders, HURCO, Weeke, HOMAG, IMA, Quaser, Bridgeport, Matec and others.
Our services at a glance
- Spindle repairs / spindle service at the highest level
- Maintenance contracts (maintenance contracts)
- Spindle storage (service contracts)
- DIN ISO 1940 balancing of tools, tool holders, fan wheels, spindle shafts, grinding mandrels, rotors, various parts up to 200 kg unit weight, with individual balancing protocol
- On-site service - spindle installation and removal, spindle condition analysis (as part of preventive maintenance), vibration measurement, regrinding of SK/ISO tapers, fine balancing of complete spindles according to ISO 1940 (as part of process optimization)
- Device service - Electrical installation and modification of converters, system cabinets and accessories
Take advantage of our consolidated experience in spindle repair!
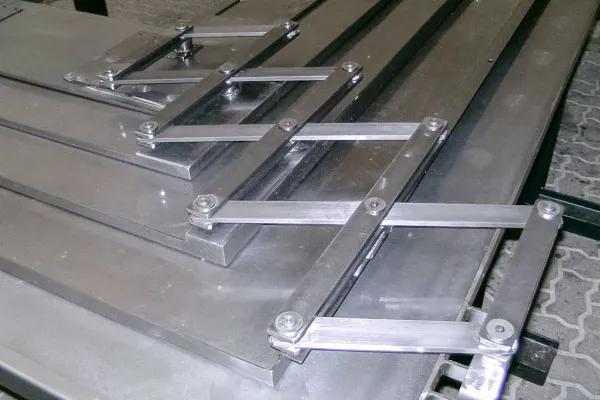
Telescopic cover general overhaul
Ever-increasing precision in industrial manufacturing means it’s essential to protect sensitive machine tools components, especially from dirt and dust. To ensure this, fully functional telescopic covers are needed. Within our group of companies, we offer a wide range of services related to telescopic covers for machine tools.
Telescopic cover general overhaul
Our service team can provide provides proper general overhaul services for the telescopic covers of all kinds of machine - including those made by foreign manufacturers. We can also eliminate design flaws and select the best types of seal and guide strips, to round off our service.
We check the condition and function of all bushings and bolts as part of the plate and shear tong reconditioning service. Defective elements are replaced professionally, to guarantee perfect functionality after overhaul. The segment plates of your telescopic covers are cleaned, degreased as well as ground.
Dent removal and straightening of the segments is also part of our range of services.
General overhaul of telescopic covers by the following manufacturers
Beakbane, GeKaTec, Halltech, HCR, HEMA, Henning, Kabelschlepp, K.H. Thissen, P.E.I. Srl, Raumag Janich, SEMA, Sermeto, WEMA, Willi Fent
Telescopic covers emergency repair
As part of our services, our team is available for emergency repairs to telescopic covers within 24h. Just call us!
Our services at a glance
- General overhaul of telescopic covers
- Telescopic covers repair
- Design defect elimination
- Segmental plates, bushings and bolts overhaul
- Fabrication and replacement of brass conductors and strips
- Sealing lip replacement
- Retaining profiles replacement
- Emergency repairs within 24h
- Individual repair contracts (maintenance contracts)

Services
Future-proof and efficient automation solutions from a single source provider
We develop automation solutions tailored specifically to the needs of our customers: From planning, mechanical and electrical design, manufacturing and assembly to commissioning with PLC and robot programming.
As general contractor, we coordinate all phases of a project, creating maximum transparency and security over the entire course of the works. Our customers can rely on a single contact person, from concept to final acceptance.
All you need to know about automation solutions
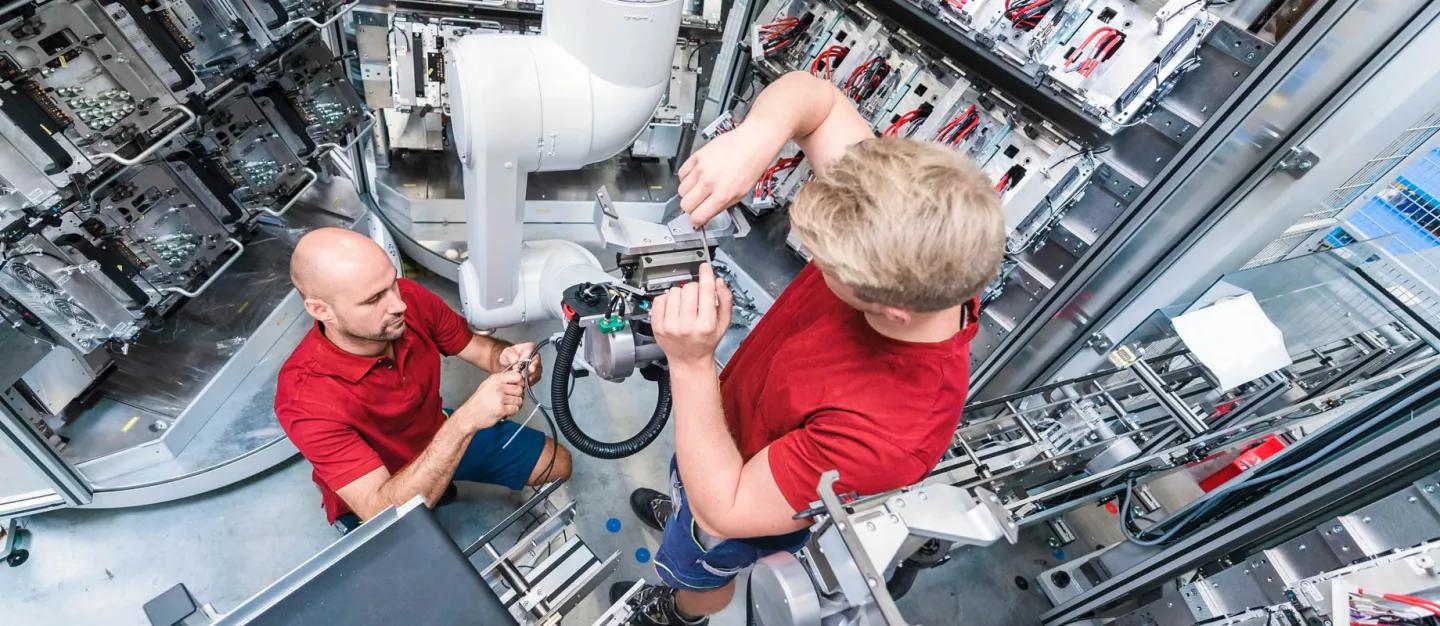
A great deal of experience in all disciplines
Of course, our experienced workforce is proficient in all the necessary areas, from spot welding, MIG/MAG welding and projection welding, to bonding, screwing, punch riveting, clinching, sorting, deburring, cleaning, testing, measurement and transport, all of which we do thanks to the long-standing experience we have in many sectors of industry.
These include the automotive sector and its supply-chain, as well as agricultural and construction machinery. Another field we specialise in is machine tool interlinking with our custom automation solutions.
We always focus on the needs of our customers, meaning we can implement individual automated solutions as well as complex systems with up to 25 robots.
In addition to our general contractor service, we also offer electrical planning, PLC and robot programming serevices as stand-alone operations. We program dynamic and efficient software solutions tailored to the requirements of our customers’ systems.
Our programming is always based on customer specifications and requirements, using controllers from leading robot manufacturers (e.g. KUKA, FANUC). Detailed documentation ensures smooth system operation.
Our services at a glance:
- Robotic systems programming
- Robot system teaching
- Documentation
- Commissioning
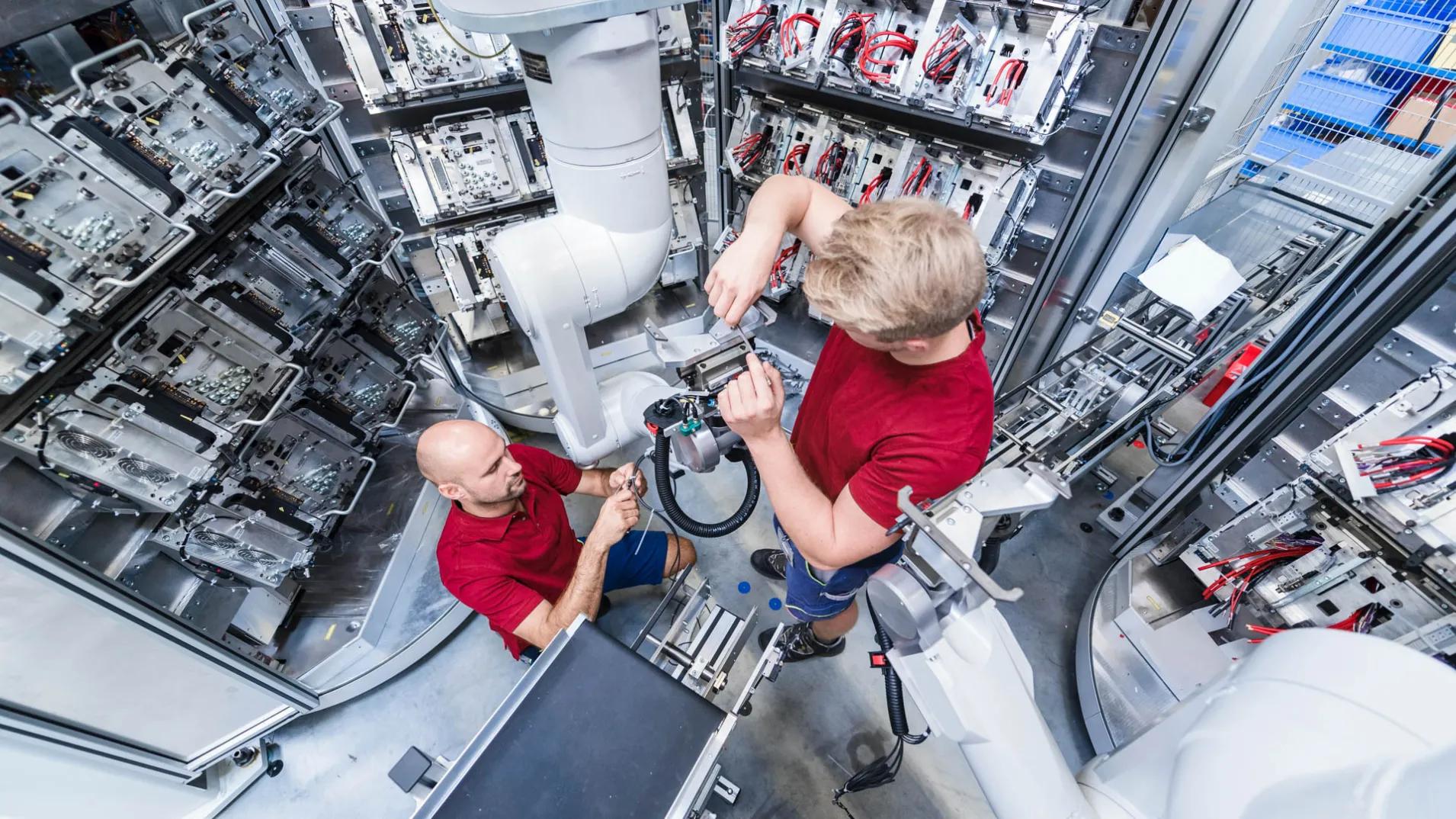
HÖRMANN Intralogistics Services - a strong partner for industry
From the conception to the commissioning, we work around the clock for our renowned customers with our highly qualified, experienced staff, providing full life-cycle support and maintenance, as well as relocation testing services for their automated manufacturing and production facilities.
We ourselves are renowned for our technical competence in the field of electrical and mechanical technology, control systems, robotics, welding, conveyor technology, pneumatic and hydraulic systems, and all the other tools of streamlined industrial engineering.
As a consolidated partner, we support our customers with future-proof and efficient automation solutions, innovative machine technology and versatile industrial services, not to mention future-oriented energy management, customised retrofit measures to increase intralogistics system performance and, of course, 24/7 customer service via our intralogistics hotline.
»The experienced staff at the HÖRMANN Intralogistics Hotline has always managed to provide rapid, solution-oriented support whenever we’ve had any kind of problem.«
RALF GRAMBKE | INSTANDHALTUNG
ZERHUSEN KARTONAGEN GMBH
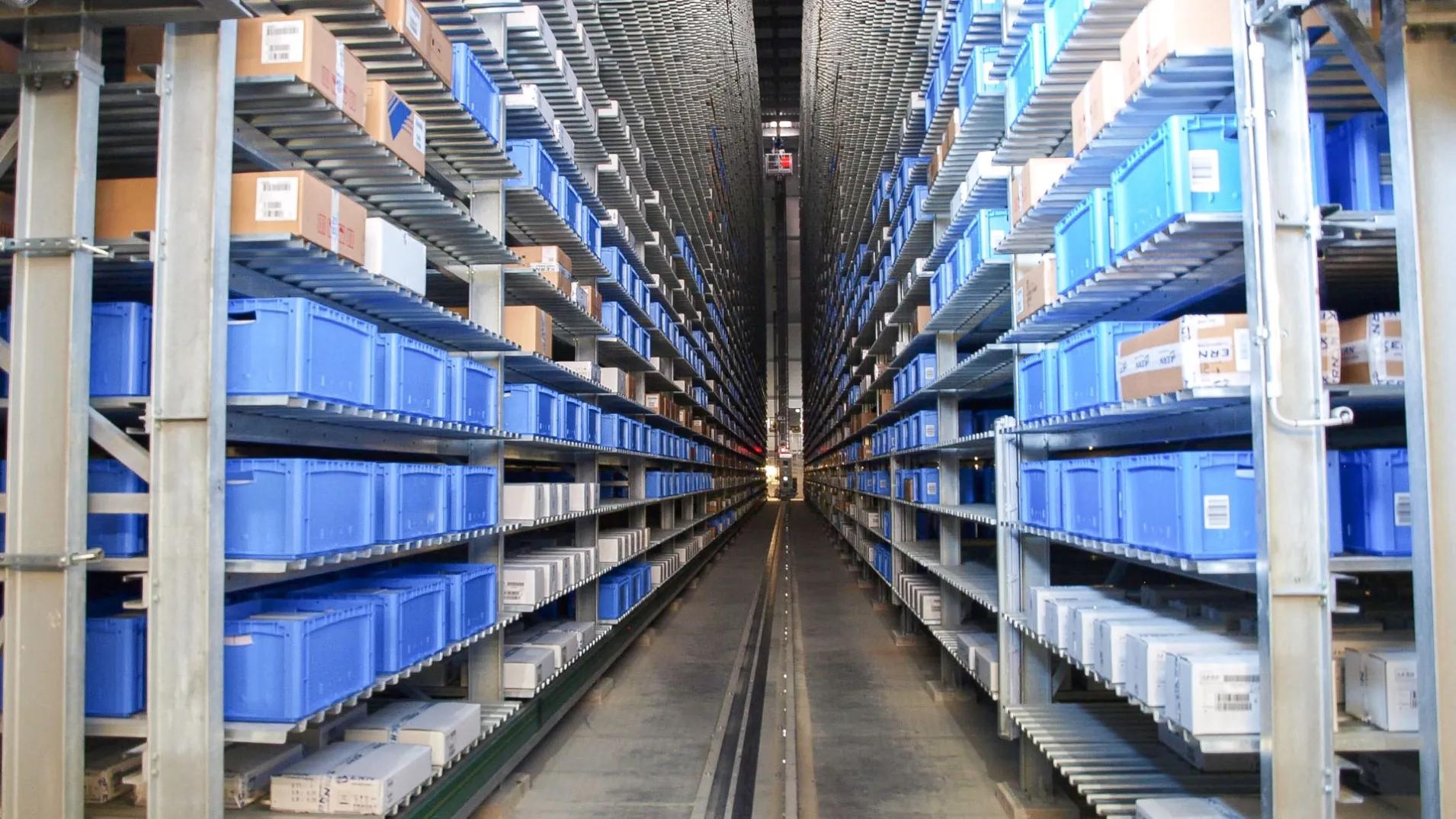
Intralogistics
Rapid access high-density small parts storage systems
We develop custom automated small parts warehouses or shuttle warehouses especially for low weight, high-turnover loads in bins, boxes or trays, ideal for classic warehouse functions as well as for buffer storage, goods service or use as a picking system.
The advantages at a glance
- More room in existing building structures for excellent space utilisation
- Lower construction costs for new warehouse space
- Enormous flexibility and redundancy
- High storage density
- Rapid access to goods (fully automated storage and retrieval)
- Maximum dynamics
- Remarkably high throughput rates
- Remarkable energy-efficient and sustainable through the use of power caps or buffer storage
- Custom solutions, perfectly adapted to your requirements and products
- Holistic support
- Goods-to-person or person-to-goods order picking
All you need to know about shuttle storage systems
Brochure - Intralogistic Solutions
Your contact - Michael Hoffmann
What are shuttle storage systems?
Automated small parts warehouses consist of one or more aisles where stacker cranes or shuttles store and retrieve totes, boxes or trays fully automatically, and serve them to picking stations.
Dynamic small parts storage for optimal space exploitation
The advantages of automated small parts warehouses include high storage density, rapid access to goods (fully automatic storage and retrieval) and optimal stock turnover rates. Shuttle systems in particular also offer maximum dynamics and particularly high throughput rates, enormous flexibility as well as ample redundancy. Using technology like power caps or buffer storage, these shuttle systems are remarkably energy-efficient and sustainable.
Incoming and outgoing storage is handled by shuttles or stacker cranes, and the automated small parts warehouses are linked to picking or other workstations via custom, innovative conveyor technology by HÖRMANN Klatt Conveyors.
Unlimited scalability
Another advantage is the almost unlimited scalability of the systems. Ever-shorter product life cycles, constantly changing product ranges and current market uncertainties make predictable business growth almost impossible. That's why we offer modular solutions that grow with your company and can be expanded as needed without too much effort.
Customised by a single source provider.
We implement your customer-specific system as general contractor. One contact, for everything from planning to commissioning.
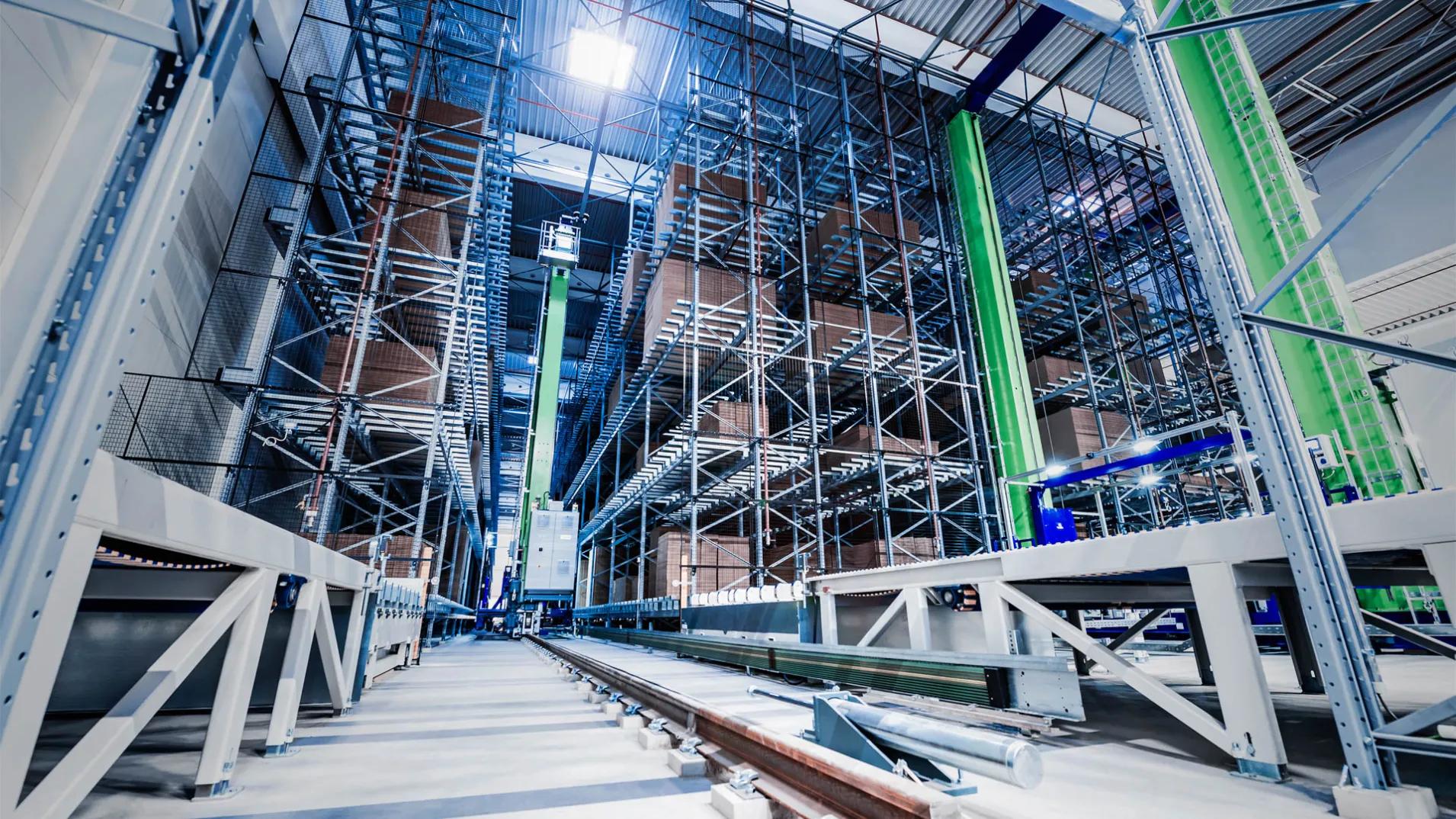
Our intralogistics solutions - individual and future-proof
With creative storage and conveyor technology concepts as well as innovative warehouse logistics techniques, in our more than 35 years of activity we have implemented many custom-made intralogistics solutions in a wide range of industrial sectors.
We design high-bay warehouses as well as tray, miniload and shuttle warehouses specifically for your requirements, to ensure maximum productivity and cost-effectivenes.
As general contractor, we take overall responsibility for implementing new, complex storage systems
and modernising existing systems even during active operations.
The whole system is integrated with our HiLIS warehouse management system. HiLIS manages, controls and monitors all material flow processes on-line, ensuring maximum transparency and system availability in all functional areas.
With our modern, innovative AutoStore® small parts warehouse, dynamic robotics applications, goods-to-person picking systems and micro-fulfilment solutions, we offer flexible, highly dynamic systems especially for e-commerce.
Our customer service is available around the clock, 365 days a year.
What makes our automatic storage systems different?
Dynamic markets demand efficient storage and logistics strategies. Automated storage systems offer maximum availability, better use of space, higher productivity and inventory accuracy, lower operating costs, and sequence-accurate goods picking and shipping.
As general contractor, we can implement your individual, high-performance, scalable and space-optimised automated warehouse solutions.
We’ve been developing our in-house HiLIS smart warehouse management solution for over 30 years, exploiting its flexibly, modularity and scalability for a wide range of industries. It’s designed to operate with all ERP, production and shipping systems.
With HiLIS, all functional areas can be flexibly controlled, monitored, and statistically analysed.
This ensures the greatest possible transparency of your logistics processes, as well as maximum warehouse performance and availability.
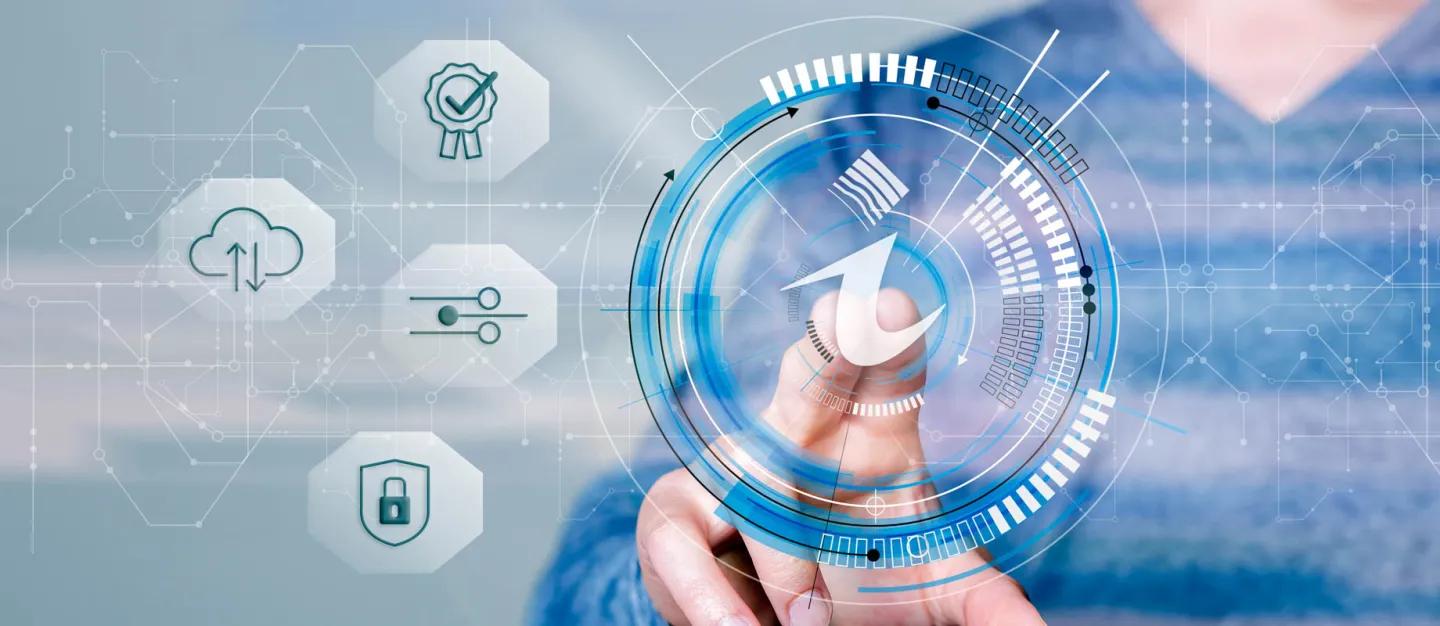
Our HiLIS WMS is the core of the automatic or manual intralogistics procress control system in the solutions we develop for customers, in our role as full-service provider of custom intralogistics solutions.
Contact us now
Thank you for your Message
We will contact you shortly.
Vielen Dank für Ihre Nachricht.
Wir melden uns zeitnah bei Ihnen zurück. Ihr Team von HÖRMANN Intralogistics.