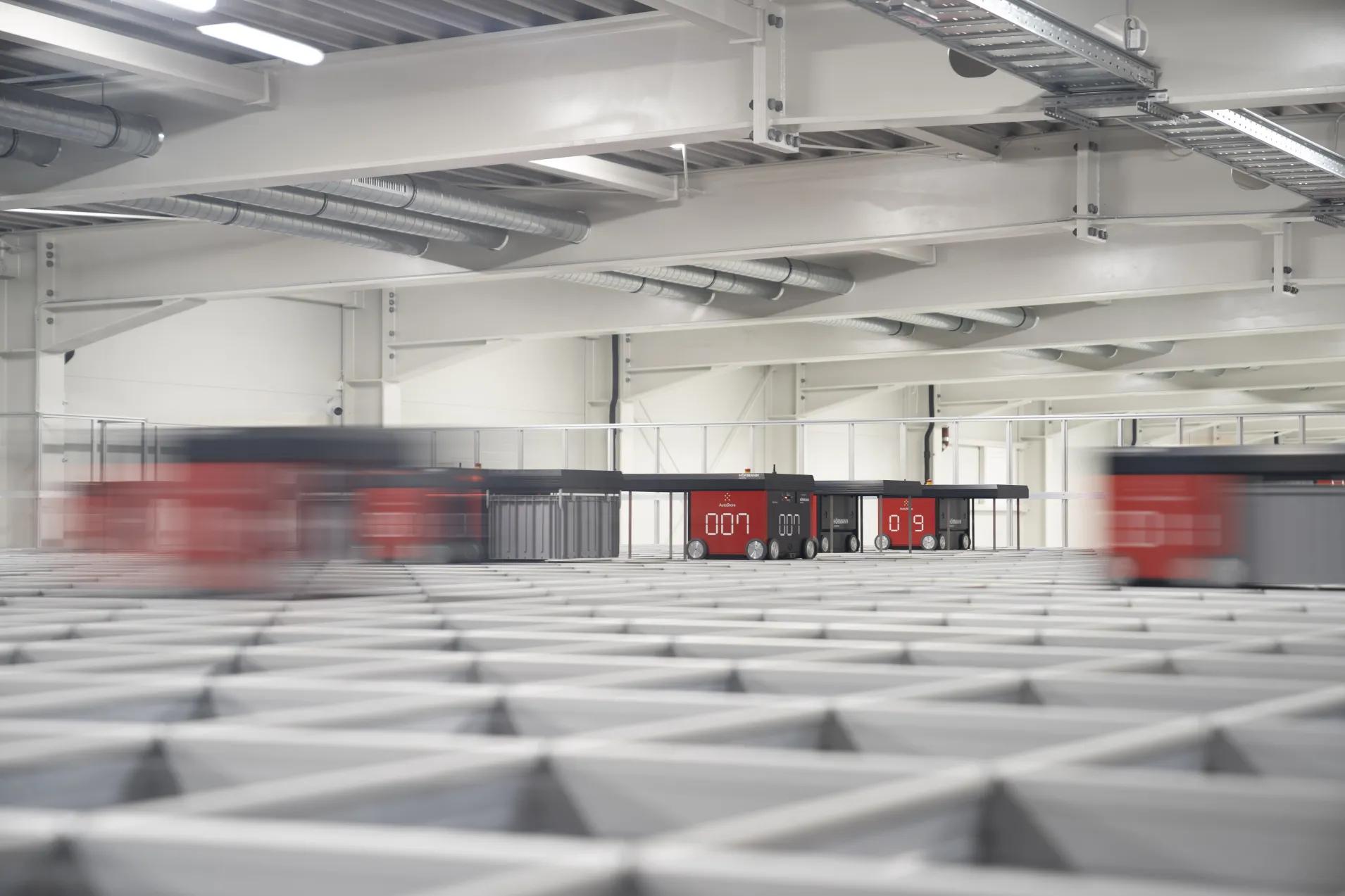
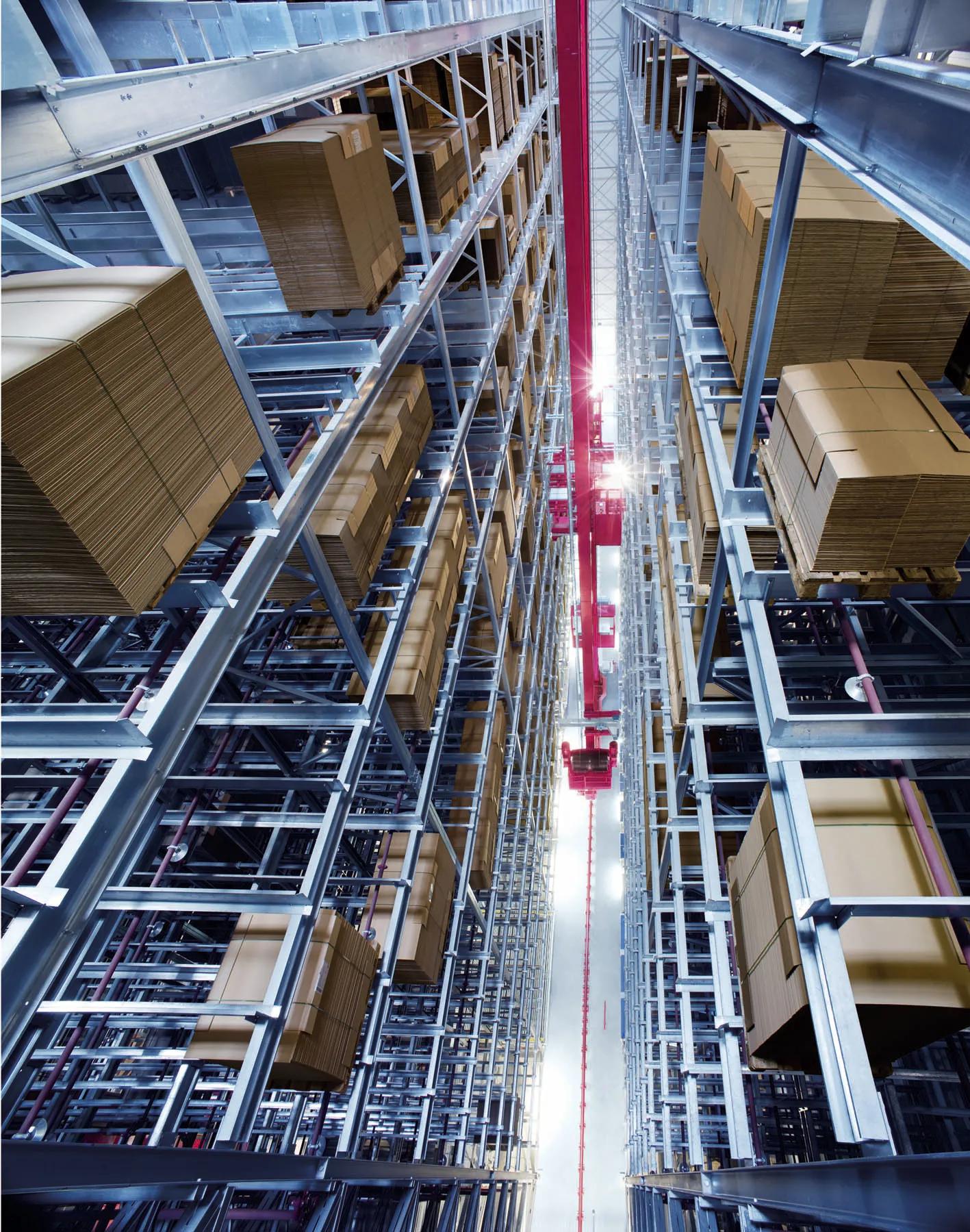
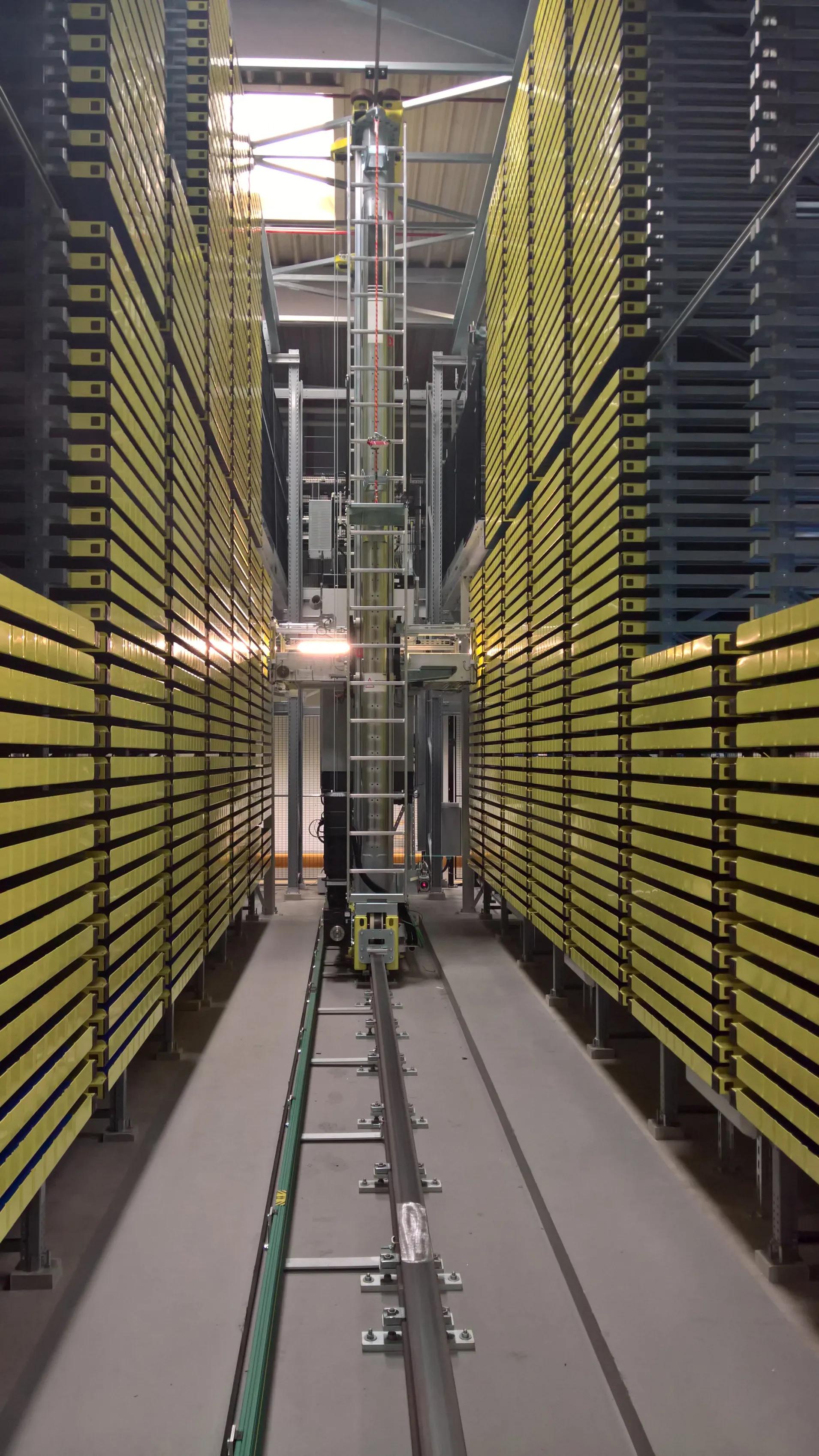
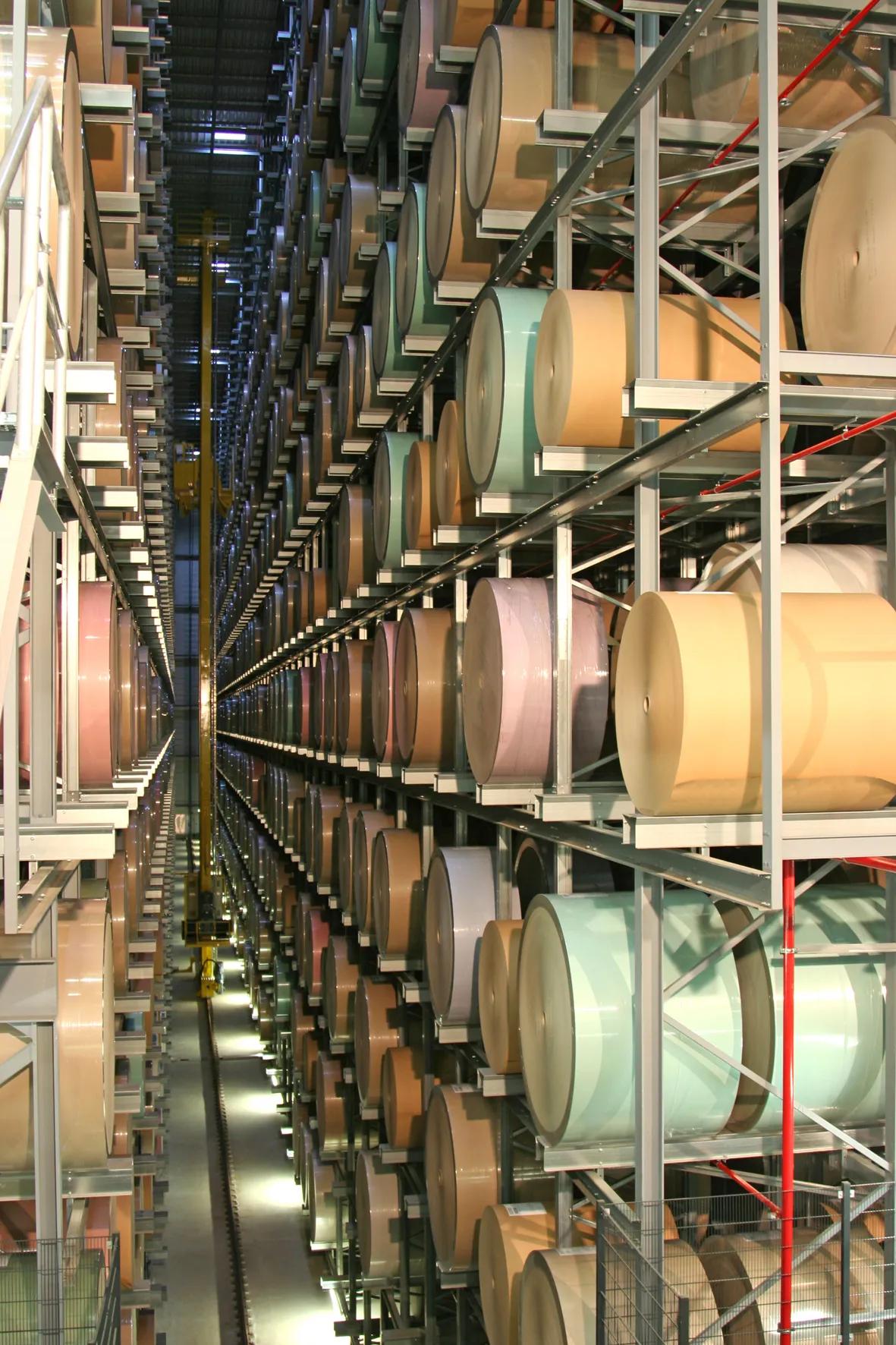
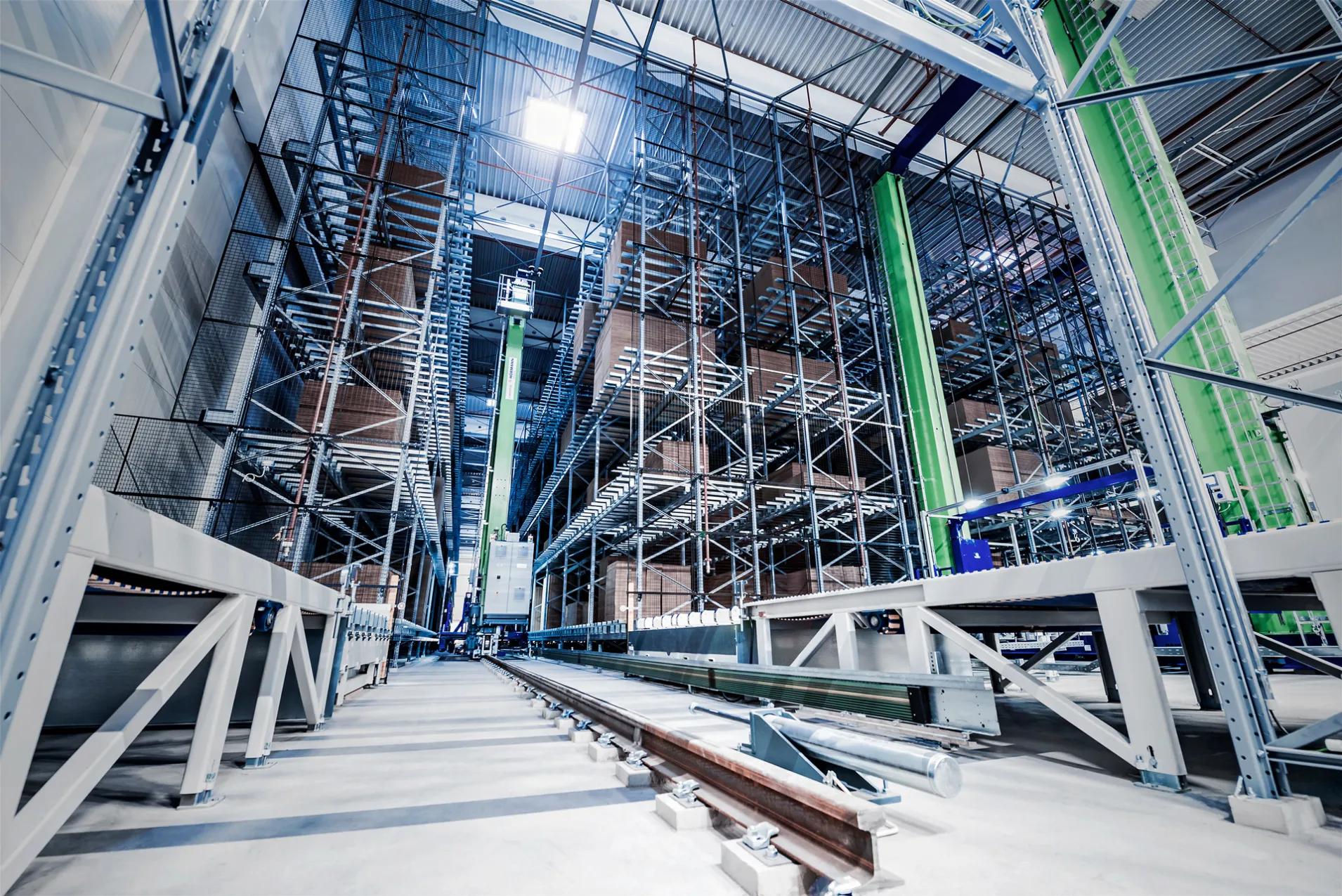
Intralogistics Solutions
Ihr Partner für hochdynamische Intralogistik, Automatisierung und Service
Als Partner renommierter nationaler und internationaler Kunden setzen wir innovative Impulse und neue Maßstäbe in der Intralogistik hinsichtlich Dynamik, Wirtschaftlichkeit und Innovation.
HÖRMANN Intralogistics bietet jahrzehntelang entwickelte Kernkompetenz in Automatisierung, IT und Industrieservice sowie die branchenübergreifende Erfahrung bei der Planung und Errichtung von schlüsselfertigen, automatisierten und datenoptimierten Lagerlösungen. Patentierte Fördertechnik- und preisgekrönte Robotik-Lösungen garantieren unseren Kunden das effizienteste Materialfluss-System aus einer Hand.
Wir sind ein Teil der starken HÖRMANN Gruppe und die Leidenschaft für Logistik treibt unsere über 300 Mitarbeiter täglich zu Höchstleistungen. Alles für den nachhaltigen Erfolg unserer Kunden!
Robotic Solutions
Hohe, fehlerfreie Produktivität, geringe Betriebskosten und unkomplizierte Inbetriebnahme – gemeinsam mit leistungsfähigen Partnern verwirklichen wir innovative Robotik-Lösungen, die unabhängig oder gemeinsam mit anderen Lager- und Kommissioniersystemen implementiert werden können. Bedarfsgerechte Skalierbarkeit, schnelle Erweiterung und höchste Dynamik machen unsere Robotik-Anwendungen zur idealen Lösung für Wachstumsmärkte.
Products
Kundenspezifische, kreative und patentierte Fördertechnik-Systeme sowie ein hochperformantes, modulares Warehouse-Management-System sorgen für permanent optimierte und reibungslose Intralogistik-Prozesse vom Wareneingang bis zum Warenausgang.
Services
Unser Service-Angebot ist auf den Lebenszyklus automatisierter Fertigungs- und Produktionseinrichtungen ausgerichtet. Von der Konzeption, Realisierung, Montage und Inbetriebnahme von Maschinen- und Anlagen bis hin zur Verlagerung oder Modernisierung vorhandener Produktionsanlagen sowie der Optimierung und Instandhaltung durch begleitende Wartung:
Renommierte nationale und internationale Kunden vertrauen auf HÖRMANN Intralogistics - ein Auszug aus unserer Referenzliste
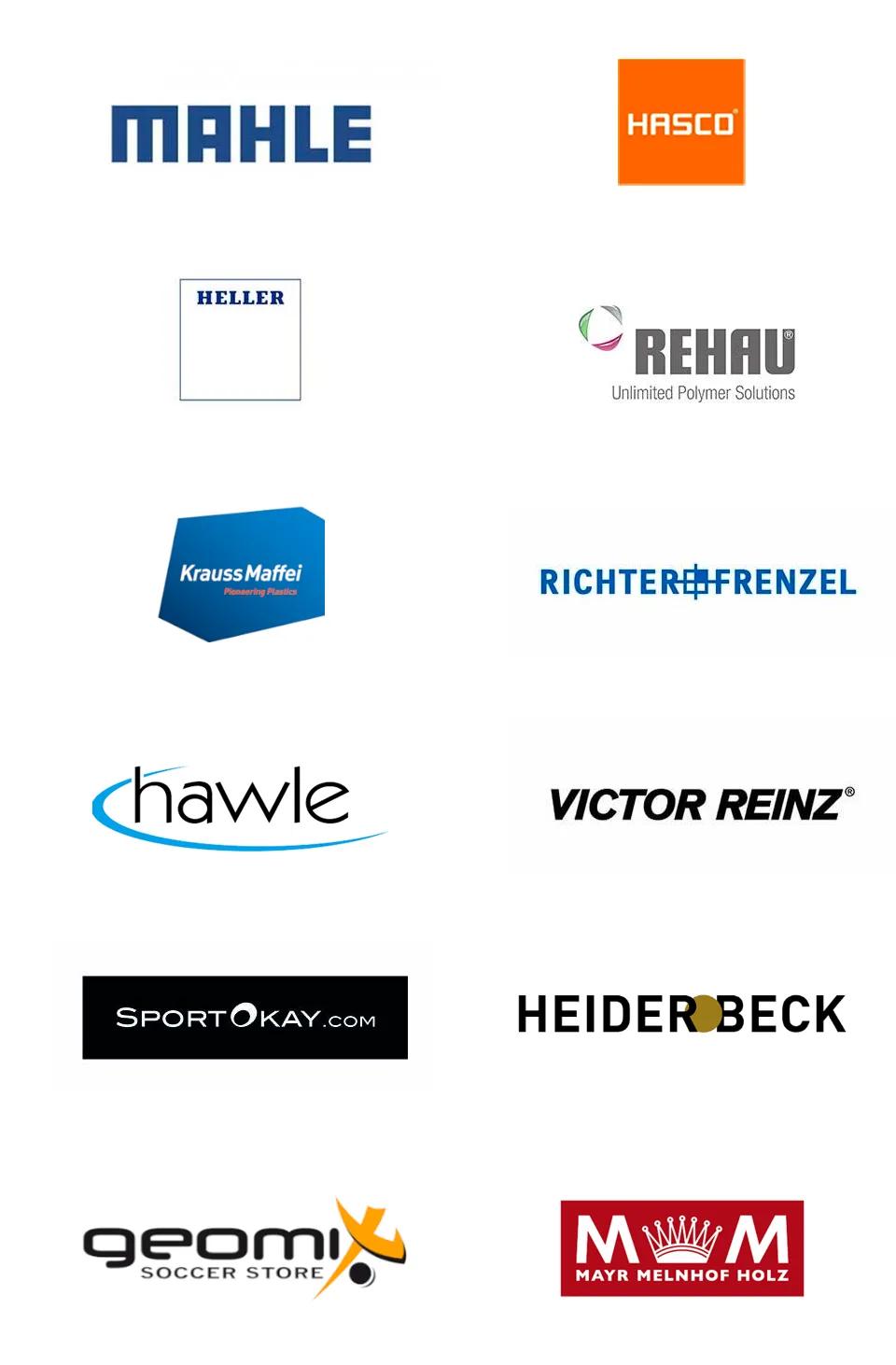
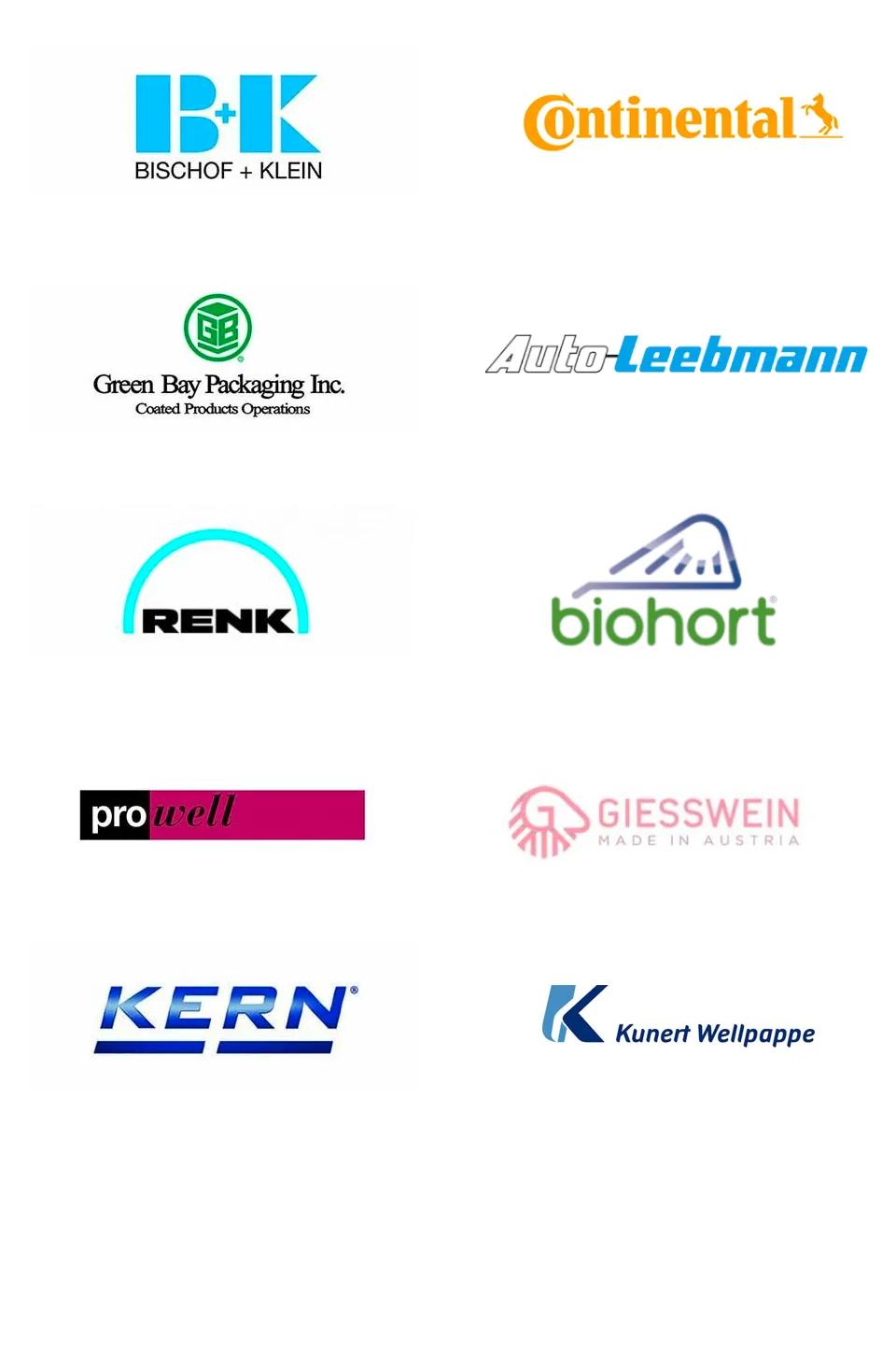
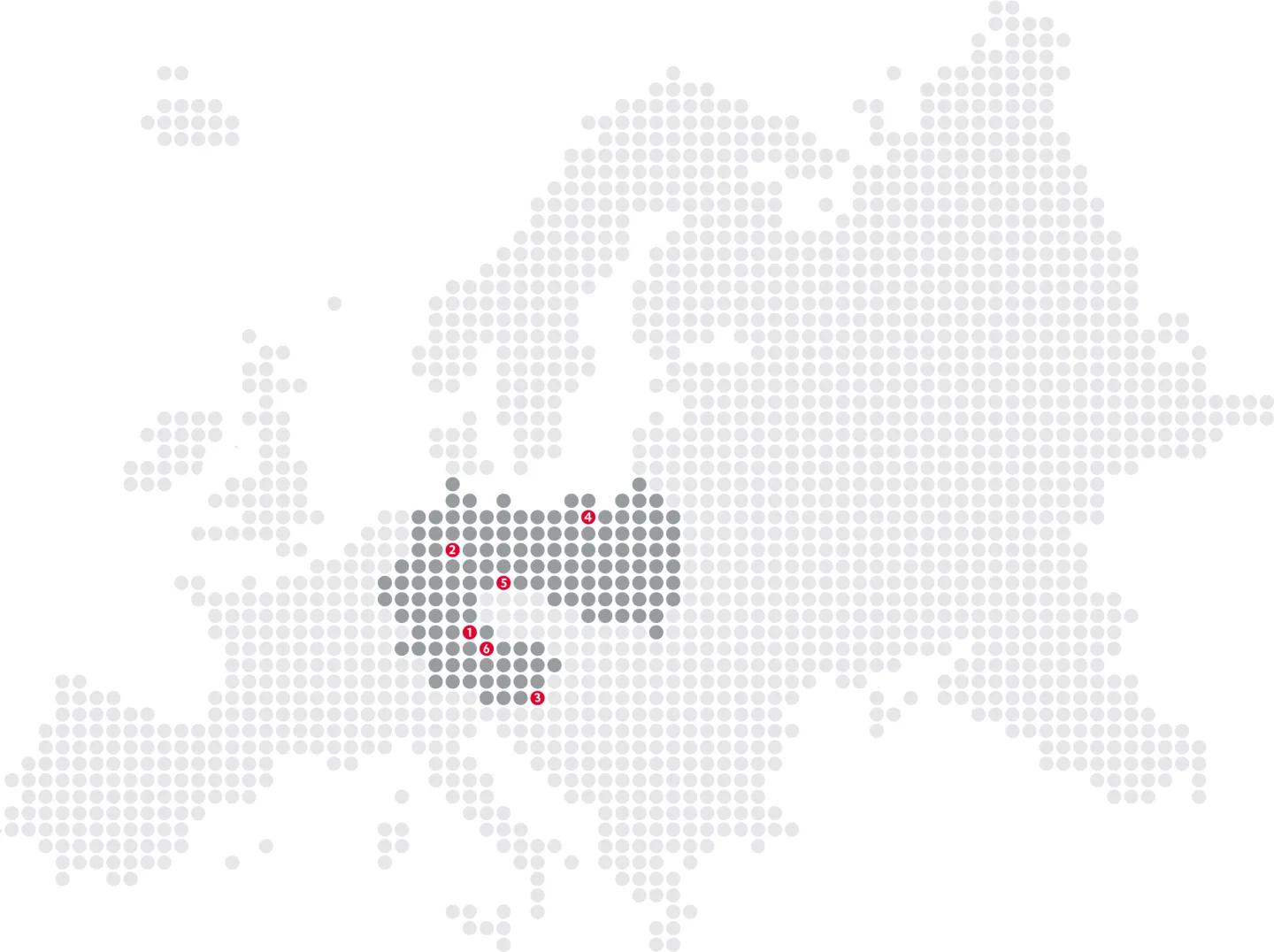
Bereit für die Anforderungen von morgen
Wir sind an 6 Standorten europaweit aktiv und mit unseren Service-Teams flächendeckend für unsere Kunden im Einsatz.
- München
- Salzgitter/Wolfburg/Wolfenbüttel
- Graz
- Danzig
- Chemnitz
- Neumarkt am Wallersee
Kontakt
Solutions
HÖRMANN Moving Racks
Micro-Fullfilment as an efficient problem solution
Micro-Fullfilment E-Food
System Grocery Retail animation
Reference projects AutoStore®
Reference project: Giesswein Brixlegg
Reference project: SportOkay
AutoStore®
The innovative small parts storage solution
The e-commerce solution
Stop Airhousing - Start Warehousing
Space Redefined
Red Line
Conveyor Port
Carousel Port
Cube Storage Pioneers
Reference projects
Timber-Intralogistics at Mayr-Melnhof Holz in Leoben | EN
iDM Energiesysteme GmbH | Matrei, Tirol | EN
Reference project: Kern & Sohn
Reference project: Fripa
Reference project: Prowell GmbH
Reference project: Herma GmbH
Reference project: Weig Logistik GmbH
Reference project: Modine Wackersdorf GmbH
Reference project: Mondi Business Paper Austria AG
Reference project: Sata Farbspritztechnik
HÖRMANN Logistik GmbH
Imagefilm | 2020 in 70s
Innovation Champion "Top Innovator 2020"! | german
We deliver security in times of Corona | german
Imagefilm 2015
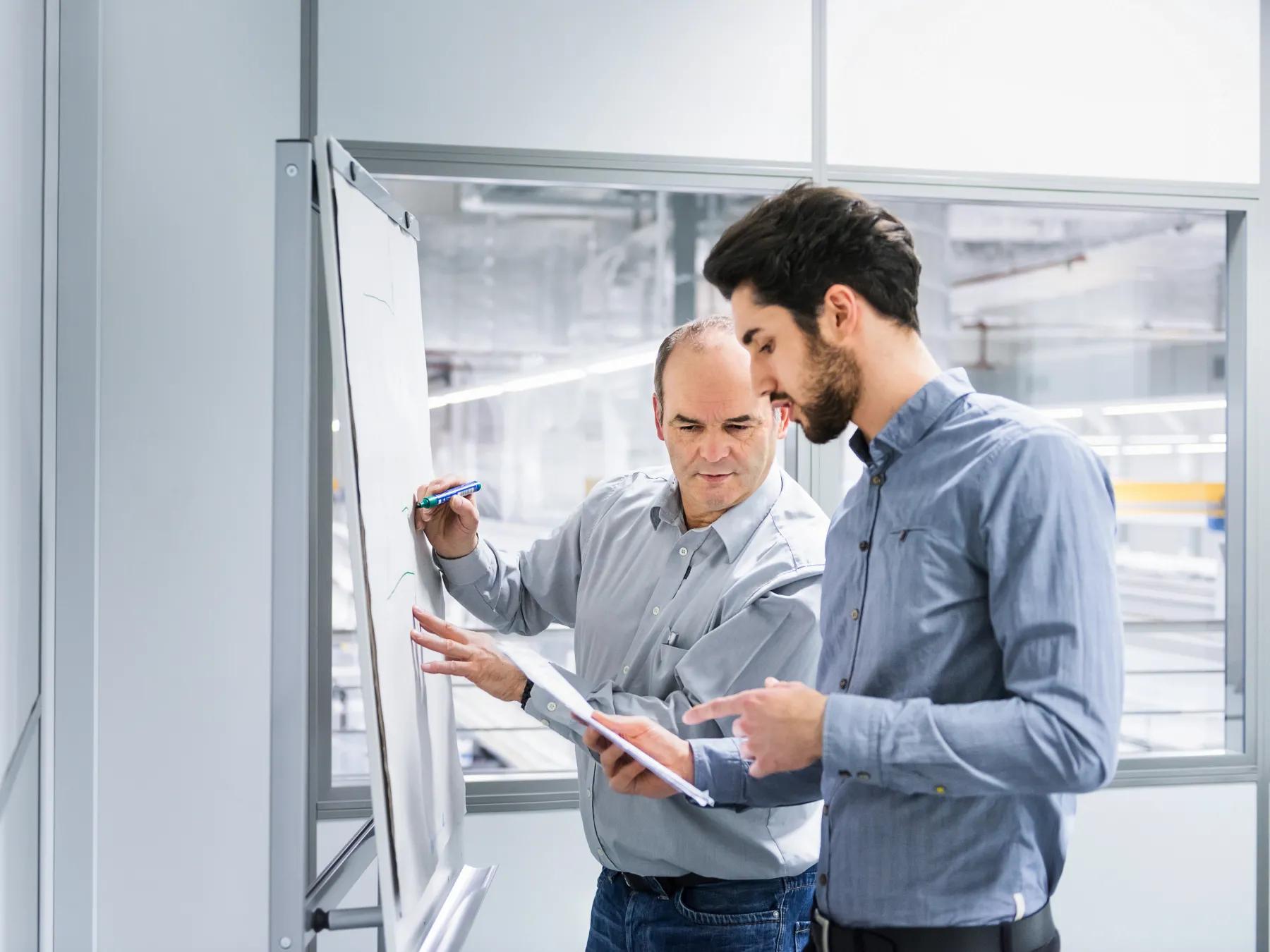
Competences
In increasingly dynamic markets, order-based and batch-size-optimised production and goods distribution require customised just-in-time and just-in-sequence processes.
Whether setting up a new facility or modernising and optimising existing systems - we offer a single point of contact from finding the solution to turnkey handover.
As a general contractor, we design and implement individual intralogistics systems for distribution and production logistics.
The HÖRMANN logistics customer service is available for you on the hotline around the clock, 365 days a year.
Our offer
- We offer you conception, realisation, training and service from a single source.
- You have only one contact partner until turnkey handover
- We ensure an optimal flow of goods and transparent information, shortened throughput times and inventory reductions.
- You receive the most economical solution with transparent costs
- State-of-the-art, future-proof technology guarantees you optimum functionality