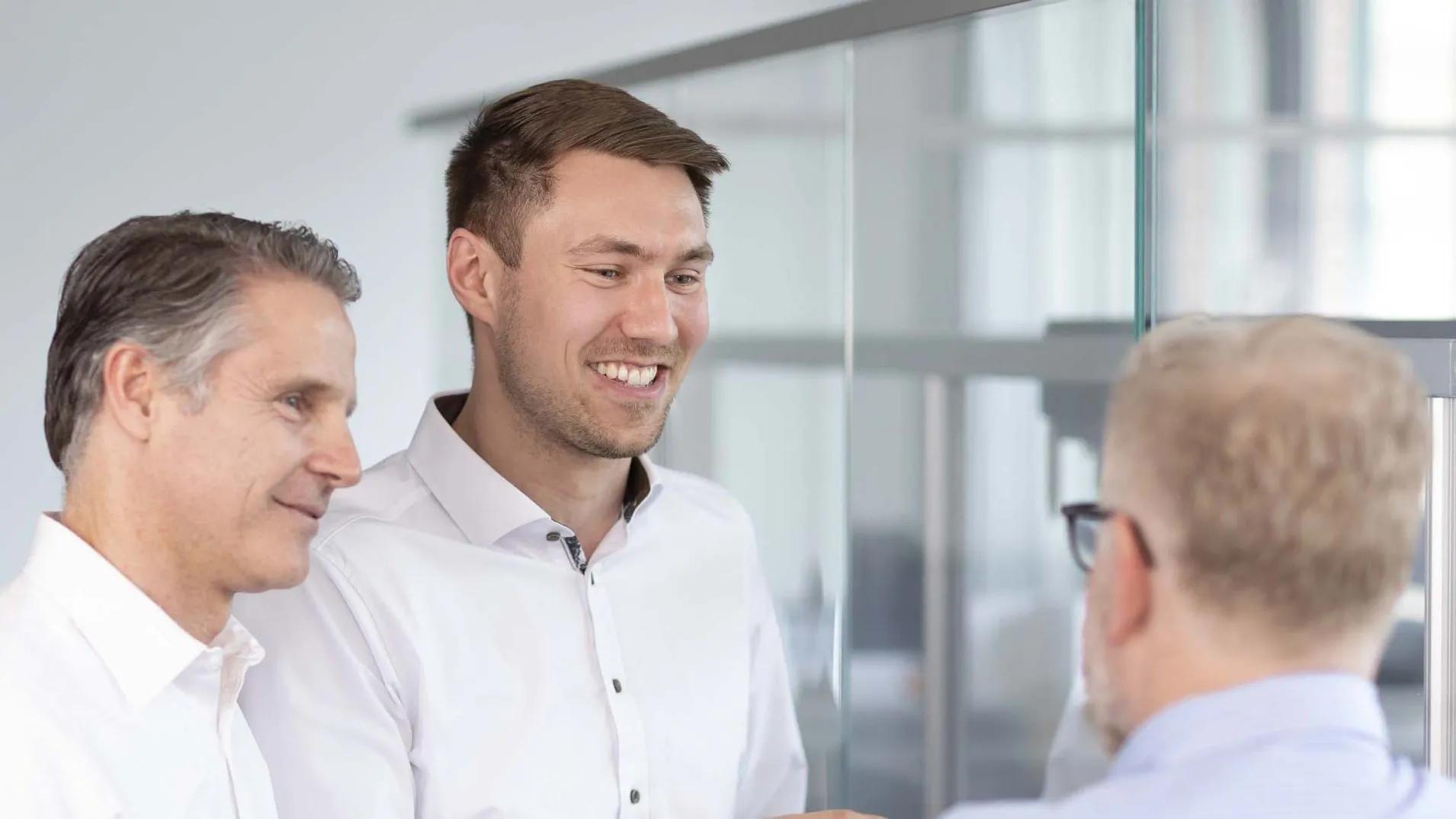
News from HÖRMANN Intralogistics
2025
2024
2023
2022
2021
Press releases
2019 (in german)
Fairs 2016
2016
Fairs 2017
2017
Fairs 2018
2018
News 2016
2016
News 2017
2017
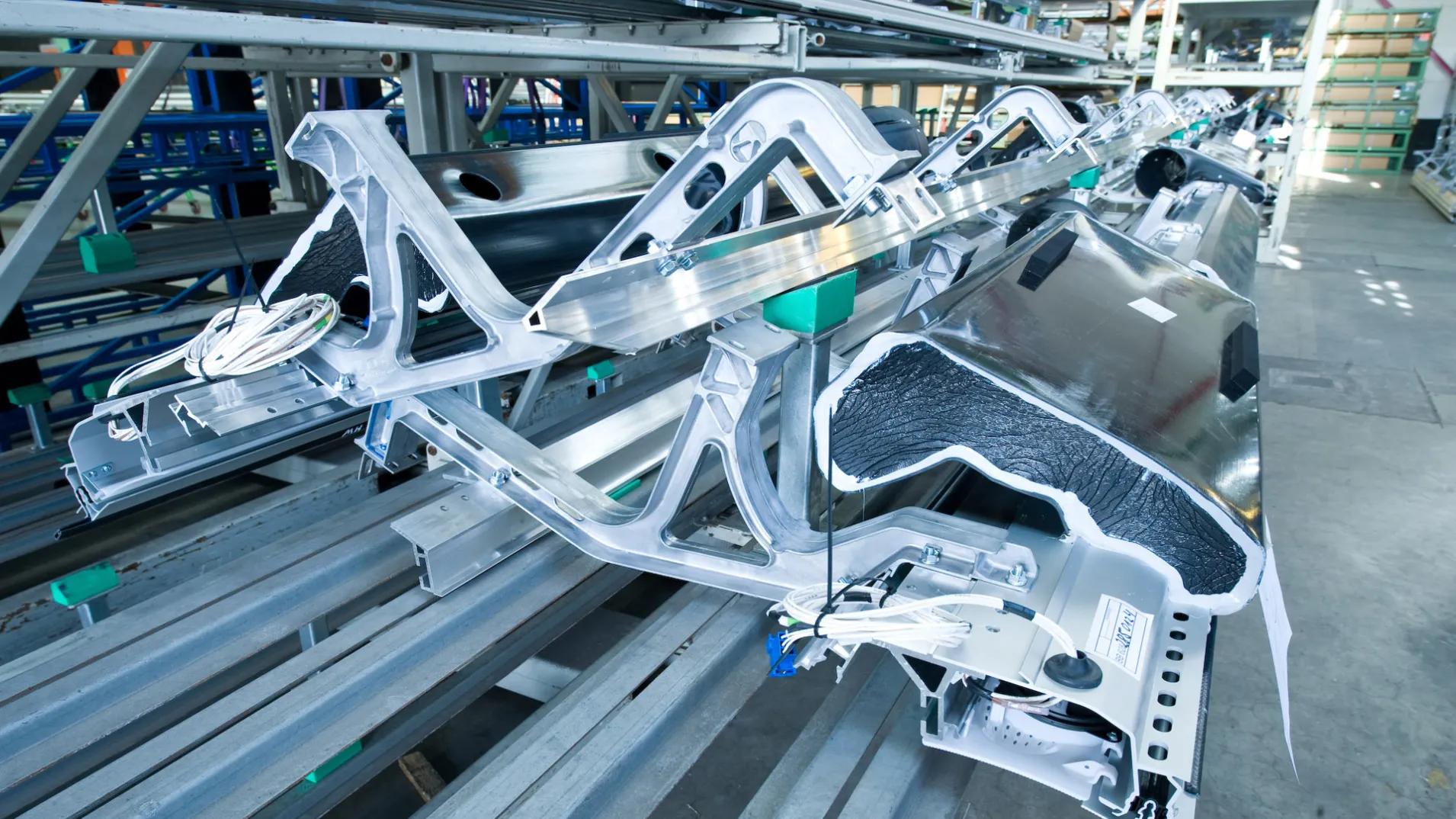
Privacy Policy of HÖRMANN Intralogistics GmbH
The protection of your privacy is a key concern for us at HÖRMANN Intralogistics.
This Privacy Policy provides you with comprehensive information about which personal data we collect when you use our services, apply for open positions, or engage in other business and contractual interactions, how we process this data, and for what purposes. We also explain the rights you have regarding your data.
Part of this Privacy Policy specifically applies to the use of our website. You can generally use our website without providing personal data. However, if you wish to use our services, it may be necessary to process personal data. Furthermore, the information in this Privacy Policy also applies to all other forms of data processing within the scope of our business operations.
We have implemented comprehensive technical and organizational measures to ensure the protection of your personal data. However, data transmissions over the internet can present security vulnerabilities, and as such, complete protection cannot be guaranteed.
This Privacy Policy applies to all companies within the HÖRMANN Intralogistics Group that refer to this Privacy Policy.
Data Controller and Contact Details of the Data Protection Officer
The data controller pursuant to Article 4(7) of the GDPR is:
HÖRMANN Intralogistics Solutions GmbH
Mr. Rainer Baumgartner and Mr. Benito Vigo Nieves
Gneisenaustraße 15
GER-80992 Munich
Phone +49 89 149898-0
E-Mail: datenschutz@hoermann-intralogistics.com
HÖRMANN Intralogistics Solutions Ges.m.b.H.
Mr. Matthis König
Eggenberger Allee 49/1/3
AUS-8020 Graz
Phone +43 31622 8611-510
E-Mail: datenschutz@hoermann-intralogistics.com
HÖRMANN Intralogistics Solutions Sp.Z.O.O.
Mr. Oleg Solovey
Azymutalna 9
POL-80-299 Gdańsk
Phone +48 577 400 145
E-Mail: info@hoermann-logistik.pl
Data Protection Officer
We have appointed a Data Protection Officer who operates for HÖRMANN Intralogistics GmbH and HÖRMANN Intralogistics Solutions GmbH in accordance with Articles 37 et seq. of the GDPR:
Prof. Dr. Thorsten B. Behling
lawyer
c/o
BUSE Rechtsanwälte Steuerberater
Partnerschaftsgesellschaft mbB
Berliner Allee 41
40212 Düsseldorf
T +49 (0) 179 4922302
E-Mail: behling@buse.de
Data Processing on the Website
Purpose of Processing
When visiting the website:
- Ensuring a smooth connection
- Guaranteeing comfortable use
- Evaluating system security and stability
- Administrative purposes
- Using the contact form and email communication
Processing your inquiries
- Fulfillment of contractual or pre-contractual measures
- Download request for the whitepaper
Contacting after the download
- Use of cookies
Improving user experience
- Statistical collection to optimize the website
- Analysis and tracking tools
Design and optimization of the website
- Statistical collection of usage
Legal Bases
When visiting the website:
- Art. 6(1)(f) GDPR (legitimate interest)
Use of contact form and email communication:
- Art. 6(1)(b) GDPR (contractual or pre-contractual measures)
- Art. 6(1)(c) GDPR (legal retention obligations)
- Art. 6(1)(f) GDPR (legitimate interest)
Download request for the whitepaper:
- Art. 6(1)(b) GDPR (contractual or pre-contractual measures)
- Art. 6(1)(c) GDPR (legal retention obligations)
- Art. 6(1)(f) GDPR (legitimate interest)
Use of cookies:
- Art. 6(1)(f) GDPR (legitimate interest)
Analysis and tracking tools:
- Art. 6(1)(f) GDPR (legitimate interest)
Data Recipients
When visiting the website:
- No specific data recipients
Use of contact form and email communication:
- Internal departments responsible for processing
Download request for the whitepaper:
- Internal departments responsible for processing
Use of cookies:
- No specific data recipients; cookies are used internally on the website
Analysis and tracking tools:
- Google Analytics (for web analysis)
- Leadinfo (lead generation service)
Data Transmission
When visiting the website:
- No transmission to third parties
Use of contact form and email communication:
- No transmission to third parties, except when necessary for processing
Download request for the whitepaper:
- No transmission to third parties, except when necessary for processing
Use of cookies:
- No transmission to third parties, except for third-party cookies
Analysis and tracking tools:
- Transmission to Google LLC and Leadinfo B.V. (USA and Netherlands)
Retention Period
When visiting the website:
- Data will be deleted after a maximum of 14 days
Use of contact form and email communication:
- Data will be deleted after processing, unless legal retention periods apply
Download request for the whitepaper:
- Data will be deleted after processing, unless legal retention periods apply
Use of cookies:
- Cookies will be automatically deleted after a defined period (maximum 6 months)
Analysis and tracking tools:
- Google Analytics: Data will be stored for a maximum of 14 months
- Leadinfo: Data will be retained according to Leadinfo’s guidelines
Weitere Informationen
- Google Analytics: Google Privacy Policy
- Leadinfo: Opt-out options at Leadinfo
- YouTube: Google Privacy Policy regarding YouTube
- Google Maps: Google Privacy Policy
Data Processing of Applications
Purpose of Processing
The processing of your personal data within the framework of the application process serves the following purposes:
- Application for a specific job vacancy
- Unsolicited application
- Inclusion in the applicant pool
Legal Bases
- Consent (Art. 6(1)(a) GDPR): If you have given us consent to process your personal data, this serves as the basis for processing. You can withdraw your consent at any time with effect for the future.
- Fulfillment of contractual obligations (Art. 6(1)(b) GDPR): Your personal data will be processed to carry out measures and activities in the context of pre-contractual relationships as well as to execute our contracts.
- Compliance with legal obligations (Art. 6(1)(c) GDPR): We process your data to comply with legal obligations, such as commercial or tax obligations. This includes archiving data according to statutory retention periods as well as gathering evidence in the context of official or judicial actions.
- Legitimate interest (Art. 6(1)(f) GDPR): Your data may be processed based on a balancing of interests to protect legitimate interests of us or third parties. This includes, among other things:
- Communication during the application process and when drafting contracts.
- Consideration of your application for similar or comparable open positions within our company.
Purpose Expansion
If your data are to be processed for further purposes, you will be informed about this and, if necessary, your consent will be obtained in accordance with Art. 6(1)(a) GDPR.
Data Recipients
Your data will be forwarded within our company to the relevant departments responsible for filling the position, typically the HR department and the relevant specialist department.
In addition, your data may be shared with the following entities:
- Processors (Art. 28 GDPR) and service providers, particularly in the area of our application portal (Softgarden: hoermann-logistik.softgarden.io).
- Headhunters and personnel service providers in a consulting role.
- Public authorities and institutions in case of legal or regulatory obligations.
- Other entities based on our legitimate interest or the legitimate interest of third parties (e.g., authorities, credit agencies, debt collection, lawyers, courts).
Data Transmission
Currently, there is no transmission of your data to a third country or an international organization.
Retention Period
- Unsuccessful applications: Your data will be deleted 4 months after the conclusion of the application process.
- Consent for inclusion in the applicant pool: Your data will be stored for 2 years and then deleted.
We will store your personal data only as long as necessary for the conduct of our business relationship or as required by statutory retention periods. Data will be deleted when the purpose of processing no longer applies or statutory retention periods have expired. If necessary, we may store your data longer based on your consent.
Data Processing of Business Partners
Purpose of Processing
We process your personal data for various purposes, which depend on the nature and scope of our contractual relationship. The main purposes of data processing include:
- Conducting the Business Relationship: Handling contracts, orders, and services, including the procurement of goods and services.
- Communication: Collecting and processing contacts, including outreach and communication, as well as handling correspondence such as emails and incoming mail.
- Logistics and Shipping: Sending packages and gifts, as well as preparing and processing invoices for spare parts and services.
- Project Management: Collecting and documenting project-related information, including recording decisions and meetings.
- Customer Service: Assisting with complaints, inquiries, and order confirmations, as well as conducting customer satisfaction surveys.
- Security and Maintenance Planning: Planning maintenance measures, emergency management, and collecting service-specific information.
Legal Bases
The processing of your personal data is based on the following legal grounds:
- Consent (Art. 6(1)(a) GDPR): If you have given us consent to process your data, this serves as the basis for processing the relevant data. You can withdraw your consent at any time with effect for the future.
- Fulfillment of contractual obligations (Art. 6(1)(b) GDPR): We process your data to fulfill our contracts with you, including processing orders and services. This also includes pre-contractual measures.
- Compliance with legal obligations (Art. 6(1)(c) GDPR): Your data will be processed to comply with legal obligations, such as commercial and tax laws. This includes fulfilling tax reporting obligations and archiving data.
- Legitimate interest (Art. 6(1)(f) GDPR): We process your data based on a legitimate interest, for example, for:
- Creating and sending address lists and gifts to maintain the business relationship.
- Gathering information and data exchange with credit agencies.
- Defense in legal disputes.
- Conducting internal and external investigations or security audits.
Data Recipients
Your personal data may be shared with the following entities:
- Processors: IT service providers, logistics companies, external data centers, accounting firms, and other service providers that assist us in fulfilling our contractual and legal obligations.
- Public Authorities: Authorities or other public institutions when legal obligations exist.
- Third Parties: Based on a balancing of interests, data may be shared with authorities, credit agencies, debt collection companies, or lawyers.
Data Transmission
Transmission of your data to countries outside the European Union (EU) or the European Economic Area (EEA) will only occur if necessary or if you have given your consent.
Currently, data may be transferred to the following third countries:
- Switzerland (partner)
- Norway (partner)
If your data are processed in a third country, we ensure an adequate level of data protection through appropriate contracts.
Retention Period
We store your personal data only as long as necessary to conduct our business relationship or as required by statutory retention periods. Data will be deleted when the purpose of processing no longer applies or statutory retention periods have expired. If necessary, we may store your data longer based on your consent.
Data Processing of Suppliers and Service Providers
Purpose of Processing
The processing of your personal data takes place for the following purposes, depending on the agreed or requested service:
- Conducting the Business Relationship: Handling contracts, orders, and services, including the procurement of goods and services, clarification of questions, handling complaints, settling invoices, and preparing quotes.
- Project Management and Documentation: Describing project contents, recording decisions, votes, and relevant meetings.
- IT Management and Documentation: Setting up VPN remote access, logging into the company network (Active Directory account), filing and sorting orders, requests, bookings, and general correspondence, as well as documenting maintenance and deployment planning.
- Logistics and Customer Service: Shipping packages or gifts, preparing invoices for spare parts and billing for services, and conducting satisfaction surveys.
- Compliance and Security Management: Collecting service-specific information (e.g., on-call duty, maintenance, licenses) and implementing the Supply Chain Due Diligence Act (LkSG).
Legal Bases
- Consent (Art. 6(1)(a) GDPR): If you have given us consent to process your personal data, this serves as the legal basis for the respective processing. You can withdraw your consent at any time with future effect.
- Fulfillment of contractual obligations (Art. 6(1)(b) GDPR): We process your personal data to fulfill our contracts, particularly in the context of order processing and service utilization, as well as in the context of pre-contractual measures.
- Fulfillment of legal obligations (Art. 6(1)(c) GDPR): We process your personal data to fulfill legal obligations (e.g., from commercial and tax laws). This includes tax control and reporting obligations, archiving obligations, and evidence collection in the context of official or judicial proceedings.
- Legitimate interests (Art. 6(1)(f) GDPR): Your personal data may be processed based on a balancing of interests to safeguard legitimate interests of us or third parties. This includes, among other things:
- Sending gifts to long-term business partners to promote the business relationship.
- Obtaining information and data exchange with credit agencies to assess economic risks.
- Assertion of legal claims and defense in legal disputes not directly related to the contractual relationship.
- Internal and external investigations or security checks.
- Communication during the execution of the contract and maintaining the business relationship.
Purpose Expansion
If your data is to be processed for further purposes, you will be informed, and your consent will be obtained in accordance with Art. 6(1)(a) GDPR if necessary.
Data Recipients
Your personal data will be shared within our company with the relevant departments that need this data to fulfill contractual and legal obligations or to safeguard our legitimate interests.
In addition, your data may be shared with the following entities:
- Processors (Art. 28 GDPR) and service providers for supporting activities, particularly in the areas of IT services, logistics, printing services, external data centers, maintenance of IT applications, accounting, data destruction, procurement, customer management, and marketing.
- Public authorities and institutions, where there is a legal or regulatory obligation to provide information, report, or disclose data.
- Entities and institutions based on legitimate interests (e.g., authorities, credit agencies, debt collection, lawyers, courts, experts, affiliated companies).
Data Transfer
A transfer of your data to third countries outside the EU/EEA may occur, particularly to:
- United Kingdom (customer)
- USA (customer)
In these cases, we ensure the protection of your rights and freedoms according to EU data protection regulations through appropriate contractual agreements. Detailed information on this is available upon request.
Retention Period
We only store your personal data as long as necessary for the performance of our business relationship or as required by legal retention periods. Data will be deleted when the purpose of processing ceases or legal retention periods have expired. If necessary, we can store your data longer based on your consent.
Data Processing of Visitors
Purpose of Data Processing
We process your data exclusively in connection with your visit and for business purposes related to your presence at our company. This includes, among other things:
- Administration and organization of your visit incl. communication (e.g. registration, appointment scheduling, contacts)
- Fulfillment of legal obligations (e.g. security regulations, access control)
- Ensuring company security, including access controls
- Tracking incidents or security events
- IT and data security during your stay (e.g. Wi-Fi usage)
- Compliance with health and safety regulations (e.g. fire safety, emergency measures)
An automated decision-making, including profiling, does not take place.
If we need to use your data for other purposes, we will inform you in advance.
Legal Basis for Processing and Information on the Obligation to provide Data
- Your consent (Art. 6(1) lit. a GDPR), e.g. if you consent to the processing of certain data as part of your visit.
- Fulfillment of legal obligations (Art. 6(1) lit. c GDPR), e.g. to comply with security regulations and access controls.
- Protection of vital interests (Art. 6(1) lit. d GDPR), e.g. in emergencies or medical incidents.
- Legitimate interests (Art. 6(1) lit. f GDPR), e.g. to ensure company and IT security as well as your security during your visit.
In principle, you are not legally or contractually obliged to provide your personal data. However, if you do not provide us with this data, this may mean that we are unable to welcome you as a visitor to our site
Recipients of Data and Data Transfers
- Authorities, e.g. law enforcement authorities, such as police, in particular when we are legally required to do so.
- Third parties, such as lawyers, in particular if it concerns the enforcement of claims.
- Internal recipients, such as reception, data protection officer, information security officer
Your data will not be transferred to countries outside the EU or to international organizations.
Retention and Storage of Data
We store your data for as long as legally required or necessary for our legitimate purposes. Paper forms (e.g. visitor logs) will as a rule be destroyed after three months. Access to this data is restricted to authorized personnel only.
Newsletter
When the newsletter of our company is subscribed, the data in the respective input mask is transmitted to the data controller responsible for processing. Subscription to our newsletter is done via a so-called double opt-in procedure. This means that after registration, you will receive an email asking you to confirm your subscription. This confirmation is necessary to prevent someone from signing up with someone else's email address. During the registration for the newsletter, the user's IP address, as well as the date and time of registration, are stored. This serves to prevent misuse of the services or the email address of the affected person. Data will not be passed on to third parties. An exception applies when there is a legal obligation to disclose. The data will only be used for sending the newsletter. The subscription to the newsletter can be terminated by the affected person at any time. Similarly, consent to the storage of personal data can be revoked at any time. For this purpose, there is a corresponding link in every newsletter. The legal basis for processing the data after the user subscribes to the newsletter, if the user has given consent, is Art. 6 para. 1 lit. a) GDPR. The legal basis for sending the newsletter as a result of the sale of goods or services is § 7 para. 3 UWG.
Use of rapidmail
Description and Purpose
We use rapidmail for sending newsletters. The provider is rapidmail GmbH, Wentzingerstraße 21, 79106 Freiburg, Germany. rapidmail is used, among other things, to organize and analyze the sending of newsletters. The data you entered for the purpose of receiving the newsletter is stored on rapidmail’s servers in Germany. If you do not want any analysis by rapidmail, you must unsubscribe from the newsletter. For this purpose, we provide a corresponding link in every newsletter message. For analysis purposes, the emails sent via rapidmail contain a so-called tracking pixel that connects to rapidmail's servers when the email is opened. This way, it can be determined whether a newsletter message has been opened. Furthermore, we can determine with the help of rapidmail whether and which links in the newsletter message have been clicked. Optionally, links in the email can be set as tracking links, allowing your clicks to be counted.
Legal Basis
The legal basis for data processing is Art. 6 para. 1 lit. a) GDPR.
Recipient
The recipient of the data is rapidmail GmbH.
Transfer to Third Countries
There is no transfer of data to third countries.
Duration
The data you stored with us for the purpose of the newsletter based on your consent will be kept by us until you unsubscribe from the newsletter, and after unsubscribing, will be deleted from both our servers and rapidmail's servers. Data that has been stored with us for other purposes (e.g., email addresses for the member area) will remain unaffected.
Revocation Possibility
You have the option to revoke your consent to data processing with effect for the future at any time. The lawfulness of data processing operations that have already occurred remains unaffected by the revocation.
Further Privacy Notices
For more details, please refer to the data security notices of rapidmail at: https://www.rapidmail.de/datensicherheit. For more information on the analysis functions of rapidmail, please refer to the following link: https://www.rapidmail.de/wissen-und-hilfe.
Use of Social Media Advertising Services
LinkedIn Ads
We use LinkedIn Ads, an advertising service provided by LinkedIn Ireland Unlimited Company, Wilton Plaza, Wilton Place, Dublin 2, Ireland, to run targeted advertising campaigns. Usage data and cookies are processed to display ads and measure their effectiveness. The legal basis for this processing is our legitimate interest (Article 6(1)(f) GDPR). For more information, please refer to LinkedIn's privacy policy. You can object to the data processing at any time or withdraw your consent.
Your Rights
Right to Information
According to Article 15 of the GDPR, you have the right to request information from us regarding whether and which personal data about you is being processed. Upon request, you will receive an overview of the processing purposes, the categories of processed data, the recipients or categories of recipients, as well as a copy of the stored data.
Right to Rectification, Deletion, and Restriction of Processing
- Rectification: According to Article 16 of the GDPR, you can request the correction of inaccurate or the completion of incomplete personal data.
- Deletion: According to Article 17 of the GDPR, you can request the immediate deletion of your personal data, provided that there is no legal obligation to retain it.
- Restriction: According to Article 18 of the GDPR, you can request the restriction of the processing of your personal data if:
- You contest the accuracy of the data,
- the processing is unlawful and you request restriction of use instead of deletion,
- we no longer need the data, but you require it for the establishment, exercise, or defense of legal claims,
- you have objected to the processing.
Right to Object
You have the right to object at any time to the processing of your personal data if the processing is based on Article 6 (1) lit. e or lit. f of the GDPR. We will then no longer process the data unless we can demonstrate compelling legitimate grounds for the processing that override your interests, rights, and freedoms.
Right of Withdrawal
You can withdraw your consent to the processing of personal data at any time. The withdrawal does not affect the lawfulness of the processing up to the point of withdrawal. In the event of a withdrawal, your application will be removed from the applicant pool and will not be further considered. Your application data will be deleted promptly unless legal retention obligations require longer storage.
Right to Complain
If you believe that the processing of your personal data violates applicable data protection regulations, you have the right to lodge a complaint with the competent supervisory authority. The competent supervisory authority for HÖRMANN Intralogistics GmbH is the Bavarian State Office for Data Protection Supervision.
Downloads
Technical and Organizational Measures of HÖRMANN Intralogistics Solutions GmbH
- For data protection agreements, such as the data processing agreement, please contact: datenschutz@hoermann-intralogistics.com
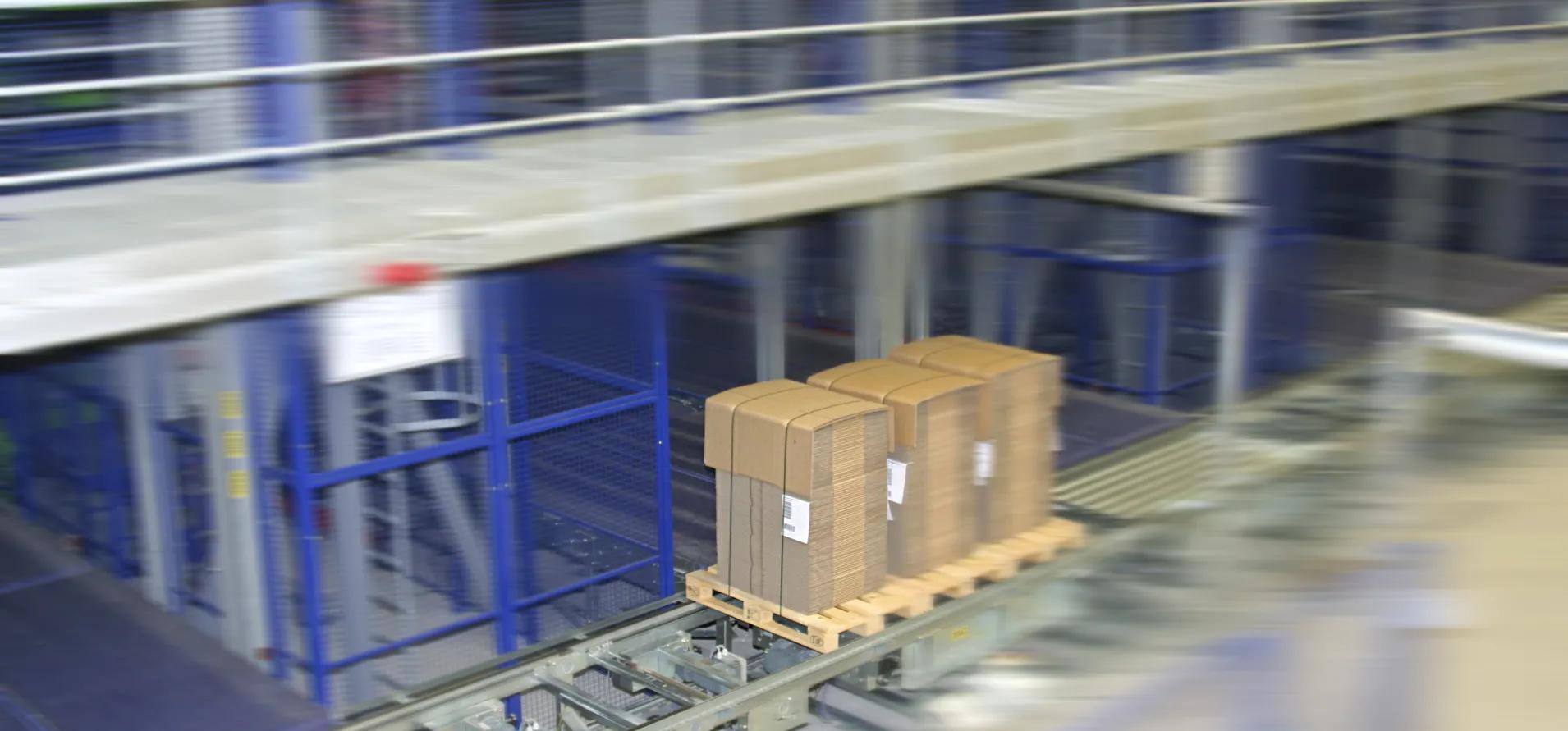
Legal Notice
According to § 5 TMG
HÖRMANN Intralogistics Solutions GmbH
Gneisenaustraße 15
80992 Munich
T +49 89 149898-0
info@hoermann-logistik.de
Represented by management: Rainer Baumgartner, Benito Vigo Nieves
- Company headquarters: Munich
- Registration court: Local court Munich
- Registration number: HRB 81184
- Sales tax identification number: DE 129375619
©Copyright 2025